Exploring the Intricacies of CNC Machines: An In-Depth Guide
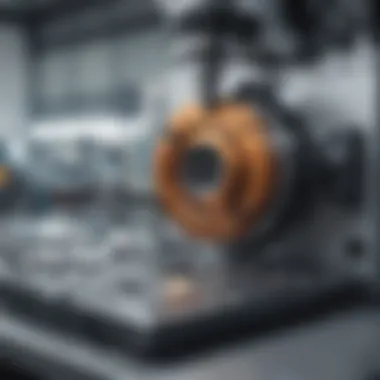
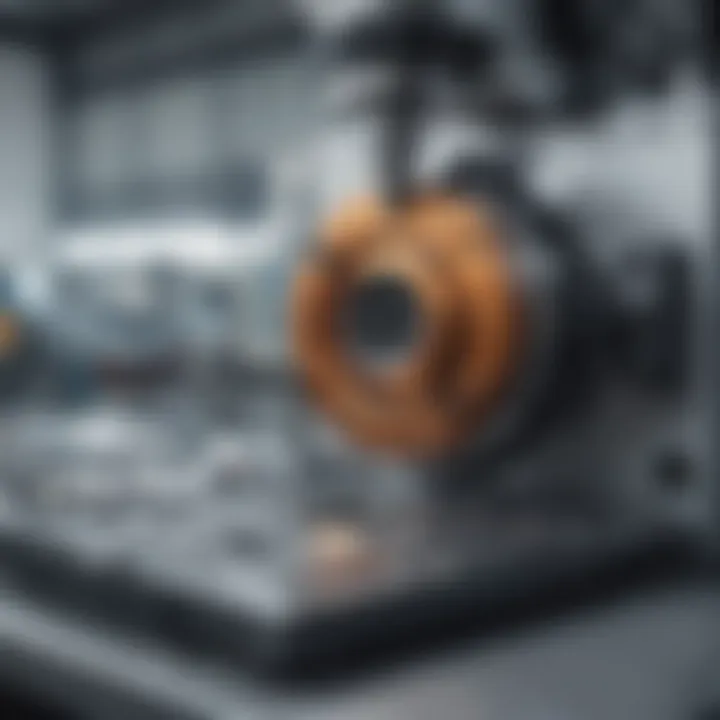
Introduction
In modern manufacturing processes, Computer Numerical Control (CNC) technology plays a pivotal role in enabling precision engineering and automation. This comprehensive guide aims to delve deep into the world of CNC machines, exploring their significance, functionality, and wide-ranging applications. From defining CNC machines to shedding light on their importance in today's industrial landscape, this guide seeks to offer a detailed insight into the realm of CNC technology.
Key Concepts
To comprehend CNC machines effectively, it is crucial to grasp key terminologies and definitions in the field. Understanding terms like 'G-code,' 'CADCAM,' and 'axis movement' is fundamental to navigating the functionality of CNC machines. Moreover, an overview of important concepts and technologies, such as spindle speed control, tool changers, and rapid prototyping, provides a holistic understanding of how CNC machines operate in diverse manufacturing settings.
Operations and Applications
CNC machines are versatile tools used in various industries, including automotive, aerospace, and electronics. By exploring the operations and applications of CNC machines in these sectors, we gain valuable insights into how this technology drives efficiency and quality in production processes. From milling and turning to laser cutting and 3D printing, CNC machines offer a gamut of capabilities that cater to different manufacturing needs with precision and consistency.
Conclusion
Introduction to CNC Machines
The realm of CNC machines holds immense significance in modern manufacturing processes. Understanding the essence of Introduction to CNC Machines in this guide is fundamental for anyone delving into Computer Numerical Control technology. This section serves as the foundation, setting the stage for the subsequent exploration of CNC machines' intricacies. By highlighting various aspects, benefits, and considerations related to Introduction to CNC Machines, readers can grasp the pivotal role these machines play in revolutionizing the industrial landscape.
What Does CNC Machine Mean?
Defining CNC Machines
Delving into the essence of defining CNC machines reveals their core functionality and purpose in modern industry. These sophisticated machines operate on precise instructions programmed into their systems, enabling automated manufacturing processes with unparalleled accuracy and efficiency. The key characteristic of defining CNC machines lies in their ability to execute tasks with minimal human intervention, streamlining production lines and enhancing overall output. The unique feature of CNC machines lies in their versatility and adaptability to a wide range of manufacturing tasks, making them a preferred choice for industries emphasizing precision and consistency.
Evolution of CNC Technology
Exploring the evolution of CNC technology unveils the progressive advancements that have shaped the landscape of modern manufacturing. From rudimentary automated systems to sophisticated computer-controlled processes, the journey of CNC technology showcases a relentless pursuit of precision and innovation. The key characteristic of this evolution is the integration of cutting-edge software and hardware solutions, elevating CNC machines' capabilities to unprecedented levels. The unique feature of CNC technology evolution is its continuous quest for efficiency and optimization, driving industries towards higher productivity and quality standards.
Impact of CNC Machines on Manufacturing
Analyzing the impact of CNC machines on manufacturing highlights their transformative effect on production processes. By replacing traditional manual methods with automated precision, CNC machines have revolutionized the efficiency and accuracy of various industries. The key characteristic of this impact is the seismic shift towards streamlined operations and reduced error margins, resulting in enhanced product quality and consistency. The unique feature of CNC machines' impact lies in their ability to drive innovation and competitiveness, positioning organizations at the forefront of technology-driven progress.
Key Components of CNC Machines
In the intricate world of CNC machines, understanding the key components is essential to grasp the underlying mechanisms driving their functionality. Each component contributes uniquely to the overall performance of CNC machines, playing a crucial role in ensuring optimal operation and output. By delving into the specifics of controllers, programmable logic controllers (PLCs), and drive systems, readers can gain a holistic understanding of the intricate workings that power these advanced machines.
Controller
The controller serves as the brain of CNC machines, overseeing the execution of programmed instructions with precision and accuracy. Its key characteristic lies in its ability to interpret complex commands and translate them into mechanical actions, guiding the machine through intricate manufacturing processes. The unique feature of controllers is their adaptability to diverse production needs, enabling seamless integration with various hardware and software solutions. Despite its complexities, the controller enhances operational efficiency and control, making it a pivotal component in the realm of CNC machines.
Programmable Logic Controller (PLC)
The programmable logic controller (PLC) complements the controller by offering additional functionalities and operational flexibility to CNC machines. Its key characteristic lies in its programmable nature, allowing for customization of control logic to suit specific production requirements. The unique feature of PLCs is their robustness and reliability in industrial settings, where consistent performance and adaptability are paramount. By leveraging PLCs, CNC machines can achieve enhanced automation capabilities and seamless integration with various inputoutput devices, optimizing overall production efficiency.

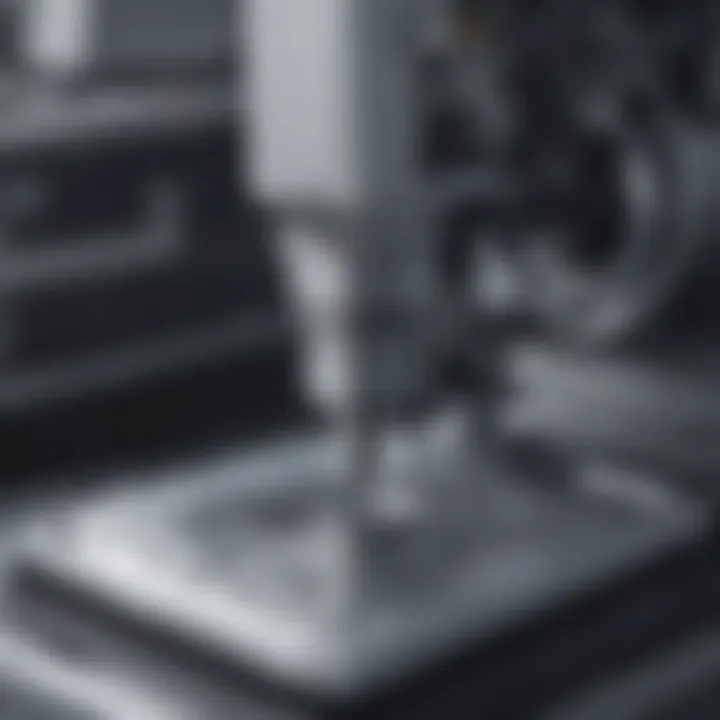
Drive System
The drive system forms the mechanical backbone of CNC machines, translating electrical signals into precise mechanical movements. Its key characteristic lies in its ability to control speed, torque, and positioning with accuracy, facilitating the seamless operation of machine tools and components. The unique feature of drive systems is their scalability and versatility, allowing for customization and optimization based on specific manufacturing needs. By harnessing the power of drive systems, CNC machines can achieve unparalleled precision and repeatability in a wide range of machining operations.
Types of CNC Machines
The diversity of CNC machines is reflected in their varied types, each tailored to specific manufacturing tasks and requirements. Understanding the distinctions between CNC milling machines, CNC lathes, and CNC plasma cutters provides insights into their unique capabilities and advantages. By delving into the intricacies of these machines, readers can appreciate the diverse applications and functionalities that define the realm of CNC technology.
CNC Milling Machines
CNC milling machines are renowned for their versatility and precision in shaping raw materials into intricate components. A key characteristic of CNC milling machines is their ability to perform complex milling operations with unrivaled accuracy and speed, making them indispensable in industries requiring high-precision machining. The unique feature of CNC milling machines lies in their adaptability to a wide range of materials and geometries, offering manufacturing flexibility and efficiency. Despite their advantages, CNC milling machines require skilled operators to harness their full potential and maximize production output.
CNC Lathes
CNC lathes stand out for their proficiency in turning operations, creating cylindrical components with exceptional precision and consistency. The key characteristic of CNC lathes is their ability to automate the turning process, reducing production lead times and ensuring uniformity in finished products. The unique feature of CNC lathes lies in their efficiency in handling intricate turning tasks, from simple grooving to complex thread cutting, catering to a diverse range of manufacturing needs. While CNC lathes offer notable advantages in precision machining, proper maintenance and calibration are essential to sustain optimal performance and output.
CNC Plasma Cutters
CNC plasma cutters excel in metal cutting applications, offering high-speed precision cutting for a variety of metal materials. The key characteristic of CNC plasma cutters is their ability to deliver rapid and intricate cuts, making them ideal for industries requiring efficient metal fabrication solutions. The unique feature of CNC plasma cutters lies in their non-contact cutting method, minimizing material distortion and facilitating intricate designs with ease. Despite their advantages, CNC plasma cutters necessitate suitable safety measures and quality control mechanisms to ensure optimal cutting performance and operator safety.
Functionality and Operation
In the realm of CNC machines, Functionality and Operation plays a pivotal role, serving as the backbone that ensures precision and efficiency in manufacturing processes. Understanding the working principles of CNC machines is essential to grasp their importance fully. Within this domain, specific elements such as Automation and Precision, Tooling and Workholding, and Software Integration stand out as critical components. Automation and Precision are distinctive features of CNC machines, allowing for unparalleled accuracy and repeatability in machining tasks. The seamless integration of Automation and Precision enhances productivity while maintaining high-quality standards. Tooling and Workholding contribute significantly to optimizing manufacturing operations by providing secure and efficient setups for machining tasks. Their role in ensuring stability and precision cannot be overstated. Moreover, Software Integration brings together various aspects of CNC machine operations, enabling seamless communication between hardware and software systems. This integration streamlines workflows and facilitates the execution of complex machining tasks with ease.
Working Principle of CNC Machines
Automation and Precision
Automation and Precision are fundamental aspects of CNC machines, driving the core functionality of these advanced manufacturing tools. Automation refers to the automatic control of machine tools and processes, reducing human intervention and enhancing operational efficiency. Precision, on the other hand, emphasizes the ability of CNC machines to fabricate components with minimal errors or deviations from design specifications. The interplay between Automation and Precision results in unparalleled accuracy and consistency, making CNC machines the preferred choice in modern manufacturing settings. The unique feature of Automation and Precision lies in their ability to perform intricate tasks with incredible detail and reliability, enabling manufacturers to meet strict quality standards and tight tolerances with ease.
Tooling and Workholding
Tooling and Workholding are integral to the successful operation of CNC machines, ensuring the efficient and accurate production of machined components. Tooling encompasses the selection and utilization of cutting tools, inserts, and accessories tailored to specific machining requirements. Effective tooling not only enhances machining performance but also prolongs tool life and improves surface finish quality. Workholding, on the other hand, refers to the mechanisms for securing workpieces during machining processes. Proper workholding solutions provide stability, vibration damping, and accessibility to various machined surfaces, allowing for precise and consistent results. The unique feature of Tooling and Workholding lies in their ability to optimize machining processes by selecting the right tools and fixtures that align with production goals and machining requirements.
Software Integration
Software Integration in CNC machines plays a crucial role in streamlining operations, facilitating data exchange, and enhancing overall productivity. By integrating software systems into CNC machining processes, manufacturers can automate tasks, optimize toolpaths, and simulate machining operations digitally. This integration enables real-time monitoring, analysis, and adjustment of machining parameters, resulting in enhanced process control and error prevention. The unique feature of Software Integration lies in its capacity to digitize manufacturing workflows, improve collaboration between design and production teams, and expedite the transition from CAD models to finished parts. By leveraging software integration, manufacturers can achieve greater efficiency, accuracy, and adaptability in their manufacturing operations.
CNC Machine Operations
Toolpath Generation
Toolpath Generation is a critical aspect of CNC machine operations, defining the trajectory and motion of cutting tools during machining processes. This process involves the generation of geometric paths that guide the movement of cutting tools along workpiece surfaces, optimizing material removal and minimizing production time. Efficient toolpath generation can significantly influence machining efficiency and surface finish quality. The key characteristic of Toolpath Generation lies in its ability to generate optimal cutting strategies that facilitate precise and efficient material removal. By selecting the most suitable toolpath generation techniques, manufacturers can achieve enhanced machining performance and cost-effectiveness.
Material Removal Processes
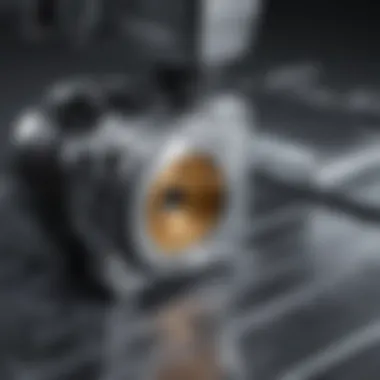
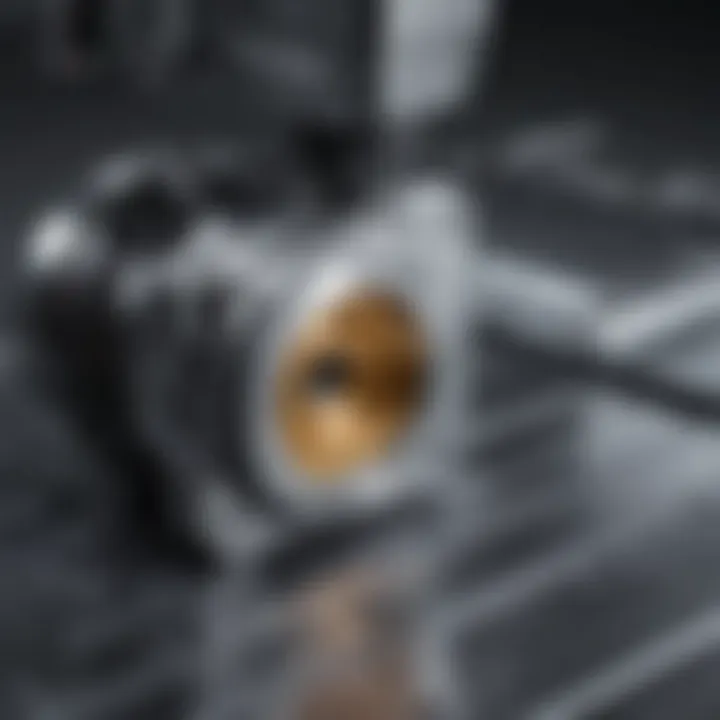
Material Removal Processes are fundamental to CNC machining, encompassing various techniques for shaping and finishing workpieces. These processes involve removing excess material from workpieces using cutting tools, lasers, or other machining methods. Material removal techniques such as milling, turning, and grinding play a vital role in achieving the desired part geometry and surface characteristics. The key characteristic of Material Removal Processes lies in their versatility and precision, allowing manufacturers to create intricate shapes and profiles with exceptional accuracy. By optimizing material removal processes, manufacturers can improve production efficiency, reduce waste, and enhance the overall quality of machined components.
Quality Control Mechanisms
Quality Control Mechanisms are essential components of CNC machine operations, ensuring that machined parts meet specified quality standards and tolerances. These mechanisms involve monitoring and verifying dimensional accuracy, surface finish, and geometric features of machined components throughout the production process. Quality control measures such as in-process inspections, metrology tools, and automated feedback systems help manufacturers maintain consistency and adherence to design requirements. The key characteristic of Quality Control Mechanisms lies in their ability to validate manufacturing processes, identify potential defects, and facilitate continuous improvement. By implementing robust quality control mechanisms, manufacturers can achieve reliable and high-quality production outcomes, boosting customer satisfaction and brand reputation.
Applications and Industries
In the realm of CNC machines, the understanding of applications and industries forms a crucial element. The utilization of CNC machines spans across various industries, revolutionizing manufacturing processes worldwide. These machines are integral in the automotive industry, aerospace sector, and medical device manufacturing, among others. Recognizing the specific applications and industries where CNC technology thrives is paramount in comprehending its significance within modern production landscapes.
Industrial Applications of CNC Machines
Automotive Industry
Within the automotive industry, CNC machines play a pivotal role in enhancing precision and efficiency in the production of vehicle components. The automation and accuracy provided by CNC technology contribute to the consistent quality and reliability of automobile parts. The automotive sector benefits greatly from the speed and precision of CNC machines, leading to streamlined production processes and cost-effectiveness. However, the main disadvantage lies in the initial investment costs associated with acquiring and maintaining CNC equipment.
Aerospace Sector
The aerospace sector relies heavily on CNC machines for the fabrication of intricate and high-precision components used in aircraft and spacecraft. CNC technology enables the production of complex geometries with utmost accuracy, meeting the stringent requirements of the aerospace industry. The key advantage of CNC machines in this sector is the ability to achieve tight tolerances and superior surface finishes essential for aeronautical applications. Despite its advantages, the aerospace sector faces challenges concerning the skilled workforce required to operate and program CNC equipment.
Medical Device Manufacturing
In the realm of medical device manufacturing, CNC machines contribute significantly to producing intricate and customized medical components with unparalleled accuracy. The precise manufacturing capabilities of CNC technology ensure the fabrication of orthopedic implants, surgical instruments, and prosthetic devices with utmost precision. CNC machines cater to the unique requirements of the medical industry, where quality standards are paramount. One drawback of CNC technology in this sector is the necessity for strict regulatory compliance to uphold quality and safety standards.
Emerging Trends in CNC Technology
Additive Manufacturing
Additive manufacturing, also known as 3D printing, has emerged as a revolutionary trend in CNC technology. It offers the ability to create complex geometries layer by layer, expanding design possibilities and reducing material waste. Additive manufacturing provides a cost-effective solution for rapid prototyping and small-scale production, with the key advantage of producing highly customized and intricate parts. However, challenges exist in achieving uniform material properties and addressing post-processing requirements.
IoT Integration
The integration of Internet of Things (Io T) technology with CNC machines enables real-time monitoring, predictive maintenance, and data-driven decision-making. IoT integration enhances operational efficiency by providing insights into machine performance and production processes. The key characteristic of this integration is the connectivity and data exchange between CNC equipment and centralized systems, facilitating remote monitoring and control. Despite its benefits, security concerns regarding data vulnerabilities and cyber threats pose risks to implementing IoT technology in CNC operations.
Industry 4. Initiatives
Industry 4.0 initiatives encompass the digital transformation of manufacturing processes through automation, data exchange, and smart technologies. CNC machines play a vital role in Industry 4.0 by enabling interconnected and optimized production systems. The key feature of Industry 4.0 initiatives is the integration of cyber-physical systems, cloud computing, and Big Data analytics for enhanced productivity and flexibility. While Industry 4.0 offers immense opportunities for efficiency improvement, organizations must address challenges related to skill gaps and data security.
Future Prospects of CNC Machines
Smart Factories
The advent of smart factories represents a significant evolution in CNC technology, where interconnected systems enable autonomous production and decision-making. Smart factories leverage CNC machines equipped with sensors and AI capabilities to optimize manufacturing processes in real-time. The key characteristic of smart factories is the seamless integration of machine learning and automation to achieve self-optimizing production systems. This advancement presents advantages in adaptive production, resource efficiency, and predictive maintenance, yet requires substantial investment in technology and workforce upskilling.
Customized Production
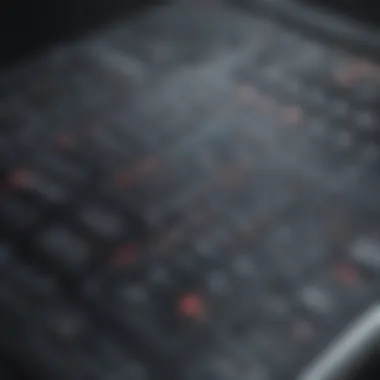
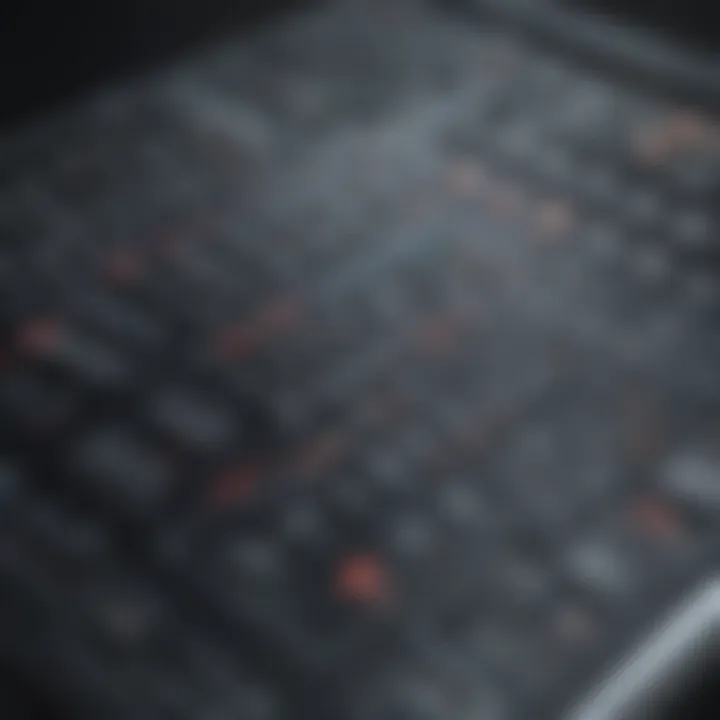
Customized production reflects the future of CNC machines, where flexibility and personalization drive manufacturing practices. CNC technology allows for the cost-effective production of tailored components without the need for extensive tooling changes. The key advantage of customized production lies in meeting individual customer demands with precision and speed, enhancing customer satisfaction and market competitiveness. However, challenges arise in scalable implementation and process optimization to meet dynamic market demands.
Sustainable Manufacturing
Sustainable manufacturing initiatives highlight the shift towards eco-friendly and resource-efficient production practices enabled by CNC machines. CNC technology plays a vital role in achieving sustainability goals through optimized material usage and energy-efficient processes. The unique feature of sustainable manufacturing is the emphasis on reducing environmental impact while maintaining product quality and operational efficiency. Despite the benefits of sustainable manufacturing, organizations face challenges in balancing sustainability objectives with cost considerations and operational constraints.
Challenges and Considerations
In understanding CNC machines comprehensively, it is crucial to delve into the challenges and considerations that come with this advanced technology. These factors play a significant role in shaping how CNC machines are utilized in various industries and settings. Firstly, the initial investment costs associated with implementing CNC technology are paramount. The financial aspect is a key consideration for businesses looking to adopt CNC machines, as the upfront expenses can be substantial. Companies need to carefully evaluate the cost-benefit analysis and ensure that the investment aligns with their long-term goals and manufacturing needs. Additionally, the skilled workforce requirement is another crucial aspect to consider. Operating CNC machines requires a specialized skill set that not all employees may possess. Companies need to invest in training programs to ensure that their workforce is adequately equipped to operate and maintain CNC machines effectively. Moreover, maintenance and calibration are critical considerations for continuous and optimal performance. Regular maintenance checks and calibration of CNC machines are essential to prevent breakdowns, optimize efficiency, and maintain product quality. Companies must establish robust maintenance schedules and protocols to ensure that their CNC machines operate at peak performance levels.
Limitations of CNC Technology
Initial Investment Costs
When discussing the limitations of CNC technology, the aspect of initial investment costs stands out as a significant consideration. The upfront financial outlay required to acquire and set up CNC machines can be substantial, especially for small to medium-sized enterprises. This initial capital investment includes the cost of purchasing the CNC machine, installation, training of personnel, and any necessary software or upgrades. Despite the high initial costs, investing in CNC technology can lead to long-term cost savings through increased efficiency, precision, and productivity. Companies must carefully weigh the upfront expenses against the potential long-term benefits of adopting CNC technology to make informed decisions about integrating this technology into their operations.
Skilled Workforce Requirement
A key limitation of CNC technology is the need for a skilled workforce capable of operating and maintaining these sophisticated machines. CNC machines require operators with specialized knowledge and training to program, monitor, and troubleshoot various machining processes. Employing skilled personnel comes at a cost, as companies must invest in training programs to develop their workforce's expertise in CNC technology. Additionally, the shortage of skilled CNC operators in the job market can pose challenges for companies seeking to leverage this technology in their operations. Hence, recruiting and retaining competent CNC professionals is crucial for maximizing the benefits of CNC technology within an organization.
Maintenance and Calibration
Maintenance and calibration are essential aspects of overcoming the limitations of CNC technology and ensuring optimal machine performance. Regular maintenance procedures involve inspecting and servicing CNC machines to identify and address potential issues proactively. Calibration procedures are necessary to maintain the precision and accuracy of CNC machines over time. Neglecting maintenance and calibration can lead to reduced operational efficiency, increased downtime, and lower product quality. Therefore, companies must establish comprehensive maintenance schedules, adhere to manufacturer guidelines, and invest in skilled technicians to carry out routine maintenance and calibration tasks.
Security and Cyber Risks
Data Vulnerability
In the realm of CNC technology, data vulnerability is a critical issue that companies must address to safeguard their sensitive information and intellectual property. CNC machines rely on digital instructions and data inputs to execute manufacturing processes accurately. However, this reliance on digital data also exposes CNC systems to potential cyber threats and data breaches. Companies need to implement robust data protection measures, encryption protocols, and access controls to mitigate the risk of data vulnerability and unauthorized access to CNC systems and networks.
Cyber Attacks
The threat of cyber attacks poses a significant risk to CNC technology, as malicious actors may target CNC systems to disrupt operations, steal proprietary information, or compromise production processes. Cyber attacks on CNC machines can result in production delays, equipment damage, financial losses, and reputational damage for businesses. Companies should proactively assess their cybersecurity posture, conduct regular vulnerability assessments, and implement intrusion detection systems to detect and prevent cyber attacks on CNC systems. Employee training on cybersecurity best practices is also essential to enhance awareness and prevent social engineering attacks targeting CNC operators.
Protective Measures
To mitigate the risks of cyber threats and potential attacks on CNC systems, companies must implement comprehensive protective measures to enhance cybersecurity defenses. Protective measures may include implementing firewalls, antivirus software, intrusion detection systems, and cybersecurity monitoring tools to monitor network traffic and detect suspicious activities. Regularly updating software systems and conducting security audits help identify vulnerabilities and weaknesses that could be exploited by cyber criminals. By prioritizing cybersecurity measures and adopting a proactive stance against potential threats, companies can strengthen their defenses and safeguard their CNC systems from cyber attacks.
Regulatory Compliance
Quality Standards
Ensuring regulatory compliance with quality standards is paramount in the utilization of CNC technology to maintain product quality, consistency, and meet industry requirements. Quality standards govern the manufacturing processes, materials, and final products produced using CNC technology to guarantee adherence to specified quality benchmarks. Companies must align their CNC operations with industry-specific quality standards, certifications, and regulatory frameworks to demonstrate compliance, ensure product quality, and build trust with customers and stakeholders.
Environmental Regulations
Compliance with environmental regulations is essential for companies leveraging CNC technology to minimize their environmental impact, promote sustainability, and adhere to legal requirements. CNC operations can have environmental implications, such as energy consumption, waste generation, and emissions. By complying with environmental regulations, companies can minimize their carbon footprint, adopt eco-friendly practices, and contribute to environmental conservation efforts. Implementing sustainable manufacturing processes, waste management strategies, and energy-efficient practices can help companies mitigate the environmental impact of CNC operations and operate in an environmentally responsible manner.
Ethical Considerations
Ethical considerations play a significant role in the use of CNC technology, particularly concerning ethical practices, social responsibility, and stakeholder engagement. Companies must uphold ethical standards in their CNC operations, supply chain practices, and business conduct to ensure transparency, integrity, and accountability. Ethical considerations encompass fair labor practices, diversity and inclusion, human rights protection, and community engagement initiatives. Upholding ethical values and principles in CNC operations fosters trust, credibility, and long-term relationships with customers, employees, and the broader community. By integrating ethical considerations into their business strategies and decision-making processes, companies can demonstrate their commitment to ethical practices and social responsibility in the context of CNC technology.