Unveiling the Strategic Lean Manufacturing Principles for Optimal Efficiency
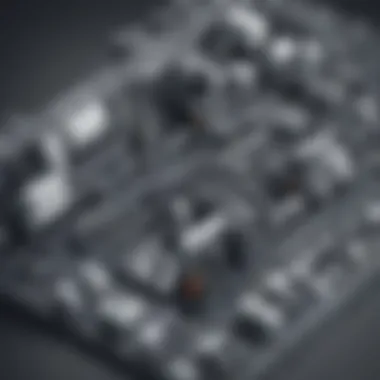
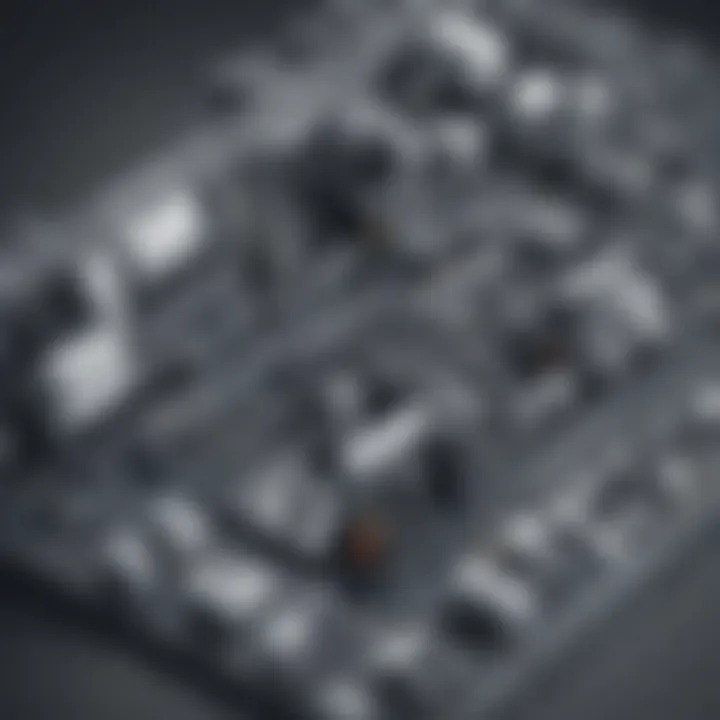
Understanding Lean Principles of Manufacturing
This segment of the article delves deep into unveiling the core principles of lean manufacturing, a strategic approach that underlines waste minimization and maximizing efficiency in the production processes. Lean methodologies will be carefully examined, shedding light on their application in diversified industries. The narrative will provide valuable insights into enhancing performance and gaining a competitive advantage within the prevailing dynamic business environment.
Introduction to Lean Manufacturing
In the realm of industrial processes, Lean Manufacturing shines as a beacon of efficiency and optimization. The core essence of Lean Manufacturing lies in its strategic philosophy of minimizing waste while maximizing productivity. As the bedrock of modern manufacturing practices, understanding the principles and methodologies of Lean Manufacturing is paramount for businesses striving to compete in a fast-paced global market. This section delves deep into the foundational aspects of Lean Manufacturing, shedding light on its significance in revolutionizing traditional production methods.
Understanding the Essence of Lean Manufacturing
Definition and Origins of Lean Principles
Delving into the roots of Lean Manufacturing reveals a methodology honed to perfection through time. Origins in the lean principles can be traced back to post-World War II Japan, notably through the Toyota Production System. The core tenets revolve around the relentless pursuit of eliminating waste in all forms, be it time, resources, or energy. This lean approach hinges on continuous improvement and efficient resource utilization to enhance overall operational efficacy. Its adaptability across industries underscores its relevance in addressing modern business challenges.
Key Objectives of Lean Manufacturing
The key objectives of Lean Manufacturing encompass a holistic approach towards operational excellence. Fostering a culture of waste reduction, process optimization, and value creation lies at the heart of Lean principles. By prioritizing customer value and employee engagement, Lean aims to streamline operations, enhance quality, and drive sustainable growth. Choosing Lean practices empowers organizations to stay agile and responsive in dynamic market conditions, creating a competitive edge through operational excellence and customer-centric solutions.
Historical Evolution of Lean Manufacturing
Origins in Toyota Production System
The Toyota Production System marks a pivotal point in the evolution of Lean Manufacturing. Originating from the innovative practices of Toyota in the 20th century, this system emphasized efficiency, flexibility, and quality in production. By integrating concepts like Just-In-Time manufacturing and autonomation, Toyota set the stage for Lean principles to revolutionize industrial practices globally. The lean thinking embedded in Toyota's DNA continues to inspire businesses worldwide to adopt agile, customer-centric approaches for sustainable success.
Impact of Lean Thinking on Global Industries
The impact of Lean thinking reverberates across global industries, reshaping conventional paradigms of production. By prioritizing value creation and waste elimination, Lean methodologies drive operational excellence and sustained growth. Industries embracing Lean practices experience enhanced productivity, reduced costs, and improved product quality. The ripple effect extends to customer satisfaction, as Lean methodologies ensure consistent value delivery and responsive solutions in a dynamic marketplace. Embracing Lean thinking is not just a choice; it's a strategic imperative for organizations aspiring to thrive in competitive landscapes.
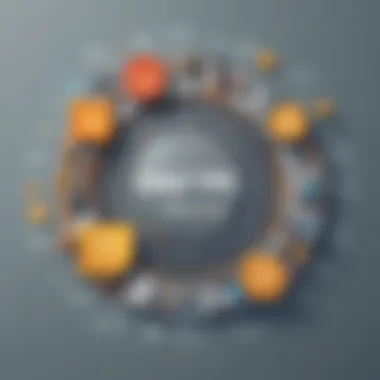
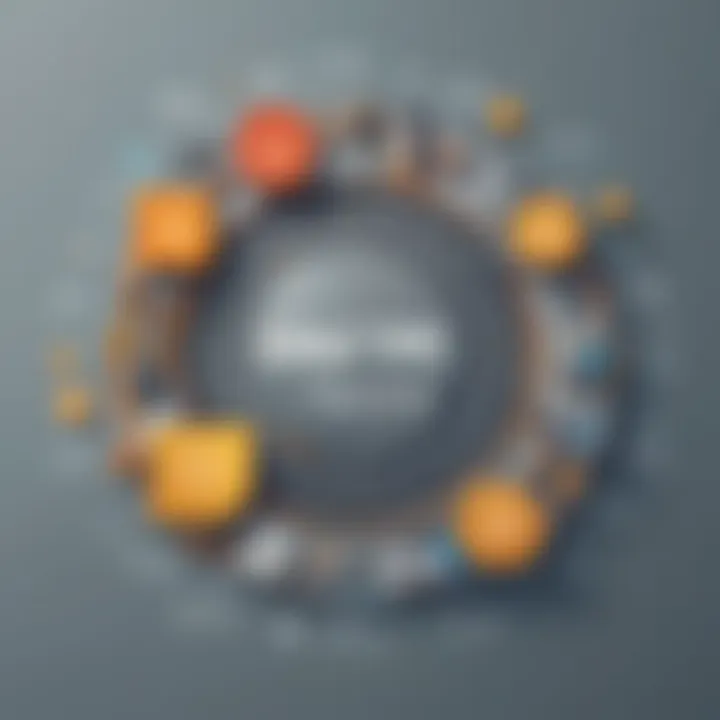
Core Principles of Lean Manufacturing
In the realm of manufacturing, the core principles of Lean Manufacturing stand as pillars of efficiency and optimization. These principles emphasize the critical importance of minimizing waste and maximizing productivity throughout every stage of the production process. By adhering to these principles, organizations can streamline operations, reduce costs, and enhance overall quality. The significance of Core Principles of Lean Manufacturing lies in its ability to create a lean, agile, and competitive business environment.
Just-In-Time (JIT) Production
Concept of JIT
The Concept of Just-In-Time (JIT) Production revolves around the idea of producing goods only as needed, thus eliminating excess inventory and waste. JIT promotes a pull-based system where production is based on customer demand, enhancing efficiency and reducing lead times. This method aims to synchronize workflow to meet customer needs promptly, resulting in lower storage costs and increased responsiveness to market fluctuations. Despite its benefits, JIT requires precise demand forecasting and well-established supplier relationships to ensure seamless operations.
Benefits and Challenges of JIT Implementation
The implementation of JIT offers numerous advantages such as reduced inventory holding costs, improved quality control, and increased production flexibility. However, challenges like a high level of coordination among various departments, vulnerability to supply chain disruptions, and potential risks of stockouts demand careful consideration. Balancing these benefits and challenges is crucial for successful JIT adoption, calling for robust supply chain management and agile response mechanisms.
Continuous Improvement (Kaizen)
Kaizen Methodology
Kaizen, a Japanese management philosophy, focuses on continuous improvement through small, incremental changes in processes and systems. This methodology fosters a culture of gradual enhancements, encouraging employee participation and the identification of inefficiencies for targeted improvements. By emphasizing ongoing refinement rather than large-scale overhauls, Kaizen ensures long-term sustainable growth and adaptability to evolving market dynamics.
Application of Kaizen in Process Optimization
Applying Kaizen in process optimization involves empowering employees to suggest and implement incremental changes that enhance efficiency and quality. This bottom-up approach not only cultivates a sense of ownership and responsibility among workers but also aligns individual goals with the organization's objectives. The flexible nature of Kaizen allows businesses to adapt swiftly to changing consumer demands and technological advancements, fostering innovation and resilience.
Respect for People
Employee Empowerment
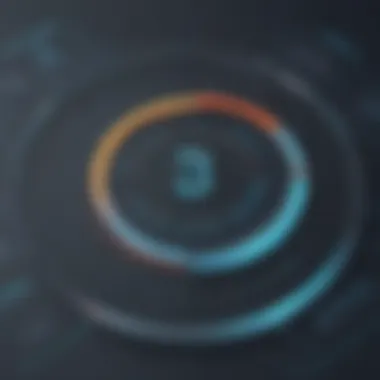
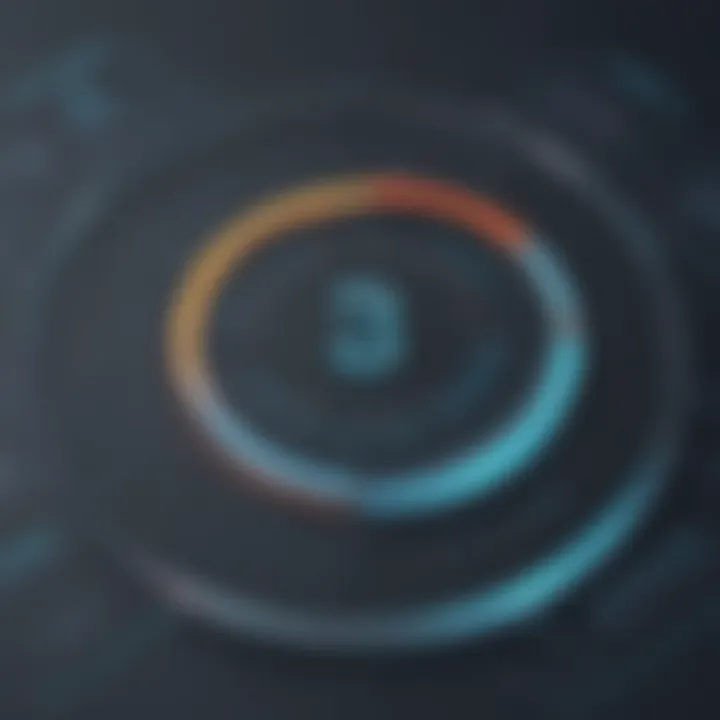
At the heart of Lean Manufacturing is the principle of empowering employees to take initiative, make decisions, and contribute to process improvements. Employee empowerment not only enhances job satisfaction and morale but also leads to a more efficient and innovative workplace. By recognizing the expertise and insights of frontline workers, organizations can tap into a valuable resource for driving continuous improvement and competitiveness.
Building a Culture of Respect and Collaboration
Creating a culture of respect and collaboration within an organization fosters trust, open communication, and teamwork. When employees feel valued, heard, and respected, they are more likely to actively engage in problem-solving, share knowledge, and collaborate towards common goals. This inclusive and supportive environment not only fuels productivity but also cultivates a culture of learning and adaptability.
Value Stream Mapping
Mapping Value-Adding Processes
Value Stream Mapping involves analyzing and visualizing the flow of materials and information required to deliver a product or service to customers. By mapping value-adding processes, organizations can identify inefficiencies, bottlenecks, and areas for improvement, leading to enhanced productivity and resource optimization. This systematic approach enables teams to streamline operations, eliminate waste, and enhance overall value delivery.
Identifying and Eliminating Non-Value-Adding Activities
Identifying and eliminating non-value-adding activities is essential for Lean Manufacturing to streamline operations and enhance efficiency. By distinguishing between value-adding and non-value-adding tasks, organizations can focus resources on activities that directly contribute to customer satisfaction and business success. Eliminating waste and optimizing processes through continuous evaluation and improvement drives a culture of excellence and operational effectiveness.
Implementation Strategies and Case Studies
In the realm of Lean Manufacturing, the section of Implementation Strategies and Case Studies holds immense significance as it pertains to the practical application and real-world examples of Lean principles. Delving into this section provides readers with actionable insights into translating theoretical knowledge into tangible outcomes within manufacturing settings. By exploring the nuances of implementation strategies alongside case studies, individuals can grasp the challenges, benefits, and considerations associated with adopting Lean practices in diverse operational environments. The seamless integration of Lean methodologies requires a strategic approach that aligns with organizational objectives, drives process optimization, and fosters a culture of continuous improvement. Through the examination of case studies, readers gain holistic perspectives on the transformative impact of Lean initiatives in enhancing operational efficiencies, reducing costs, and achieving sustainable growth.
Effective Deployment of Lean Practices
Training and Skill Development
Training and Skill Development occupy a pivotal position in the landscape of Lean Manufacturing implementation. This facet directs attention towards equipping workforce with the requisite knowledge, competencies, and tools crucial for Lean adoption. The tailored training programs aim to enhance employees' understanding of Lean principles, methodologies, and tools, nurturing a culture of continuous learning and improvement. Emphasizing skill development empowers individuals to identify waste, streamline processes, and drive efficiency gains within their respective roles. The structured training modules not only enhance individual capabilities but also cultivate a collective mindset of accountability, collaboration, and adaptability essential for sustaining Lean practices long term. While training and skill development serve as foundational pillars for successful Lean implementation, organizations must continually invest in upskilling their workforce to adapt to evolving market dynamics.
Cross-Functional Team Collaboration
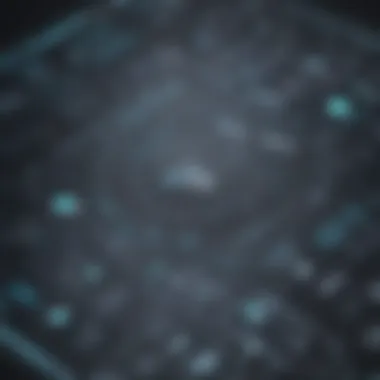
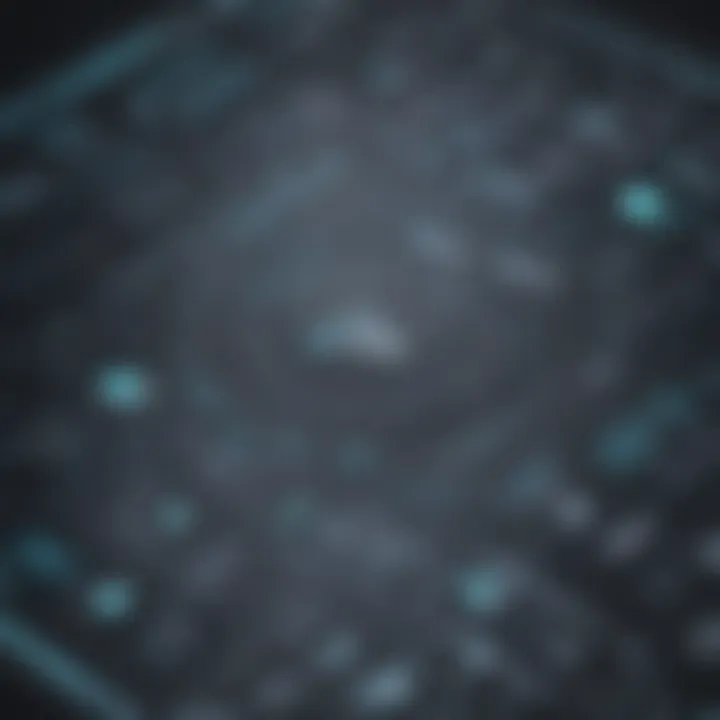
Cross-Functional Team Collaboration emerges as a cornerstone in the successful deployment of Lean practices, epitomizing the integration of diverse expertise and perspectives towards a common goal. By fostering collaboration across departments, functions, and hierarchies, organizations can leverage the collective intelligence and experience of team members to drive impactful process improvements and innovation. The interdisciplinary collaboration not only breaks down silos but also promotes knowledge sharing, creativity, and problem-solving capabilities essential for addressing multifaceted challenges. Through cross-functional team collaborations, organizations can harness the synergies of varied skill sets to streamline workflows, enhance communication channels, and accelerate decision-making processes. However, effective team collaboration requires clear communication channels, defined roles and responsibilities, and a shared commitment to organizational objectives, ensuring alignment and cohesiveness in Lean initiatives.
Success Stories of Lean Implementation
Toyota's Lean Journey
The narrative of Toyota's Lean Journey exemplifies a pioneering approach to Lean Manufacturing that has revolutionized the global automotive industry. Rooted in the principles of continuous improvement, waste reduction, and respect for people, Toyota's Lean practices have become synonymous with operational excellence and efficiency. By embracing Kaizen methodologies, Just-In-Time production systems, and value stream mapping, Toyota has set industry benchmarks for quality, productivity, and customer satisfaction. The Lean culture embedded within Toyota's DNA drives a relentless pursuit of perfection, encouraging employees at all levels to contribute ideas, identify inefficiencies, and implement sustainable solutions. Despite facing challenges along the way, Toyota's commitment to Lean principles has propelled them towards resilience, adaptability, and sustained growth, positioning them as a beacon of Lean success in the competitive automotive landscape.
Lean Practices in Various Industries
The diversification of Lean practices across various industries underscores its universal applicability and transformative impact on organizational performance. From healthcare to aerospace, retail to services, Lean methodologies have transcended traditional manufacturing domains, catalyzing operational excellence, customer-centricity, and agility. By leveraging Lean tools such as 5S, Kanban, and Gemba walks, industries have optimized workflows, minimized lead times, and enhanced product quality, showcasing tangible outcomes of Lean adoption. The customization of Lean practices to suit industry-specific requirements highlights its adaptive nature and scalability, enabling organizations to create value, drive innovation, and stay ahead in dynamic markets. While each industry presents unique challenges and opportunities for Lean integration, the common thread lies in fostering a culture of continuous improvement, employee engagement, and customer focus, reflecting the enduring relevance of Lean principles in driving sustainable growth and competitive advantage.
Challenges and Future Outlook
The section on Challenges and Future Outlook plays a pivotal role in this comprehensive article on the Lean Principles of Manufacturing. It sheds light on the crucial aspects that businesses need to consider while implementing lean methodologies to drive operational efficiency and competitive advantage. By addressing the obstacles and opportunities that come with adopting lean practices, organizations can proactively strategize and navigate towards successful lean transformation. In essence, understanding and mitigating challenges while staying abreast of emerging trends are instrumental for sustainable growth in a rapidly evolving market landscape.
Overcoming Barriers to Lean Adoption
Cultural Resistance to Change
Cultural resistance to change is a fundamental aspect to address within the context of lean adoption. It encompasses the inherent reluctance or opposition that employees may exhibit towards altering established workflows and processes. This cultural inertia can impede the successful implementation of lean strategies and hinder organizational progress. Recognizing the root causes of resistance, fostering open communication, and cultivating a culture that embraces continuous improvement are essential facets to overcome cultural barriers effectively within the lean framework. While resistance may initially pose challenges, addressing cultural aspects can lead to improved employee engagement, innovation, and overall organizational resilience.
Leadership Commitment and Strategic Alignment
Leadership commitment and strategic alignment are critical components that significantly influence the successful deployment of lean principles within an organization. A supportive leadership cohort that champions lean initiatives, fosters a culture of collaboration, and provides the necessary resources and guidance is paramount for driving sustainable change. Strategic alignment ensures that lean objectives are aligned with broader organizational goals, enhancing the overall efficacy and impact of lean practices. Effective leadership commitment facilitates employee buy-in, promotes a shared vision, and cultivates a conducive environment for continuous improvement and operational excellence.
Emerging Trends in Lean Manufacturing
Industry Integration
The integration of Industry 4.0 concepts within lean manufacturing heralds a new era of interconnected and intelligent production systems. Industry 4.0 leverages digital technologies, such as IoT, AI, and data analytics, to optimize processes, enhance communication, and enable predictive maintenance within the manufacturing ecosystem. By incorporating Industry 4.0 principles into lean frameworks, organizations can achieve heightened levels of efficiency, flexibility, and customization while leveraging real-time data insights to drive informed decision-making and operational agility.
Lean Sustainable Practices
The adoption of lean sustainable practices underscores a commitment towards environmental stewardship, resource efficiency, and social responsibility within manufacturing operations. Embracing sustainability principles alongside lean methodologies allows businesses to optimize resource utilization, minimize waste generation, and mitigate environmental impact while driving long-term value creation. Incorporating sustainable practices not only contributes to cost savings and regulatory compliance but also enhances brand reputation, fosters innovation, and cultivates stakeholder trust. By integrating sustainability into lean strategies, organizations can foster a culture of responsibility and resilience, positioning themselves for long-term success in a competitive market landscape.