Optimizing Operational Performance Through Comprehensive Supply Chain Planning
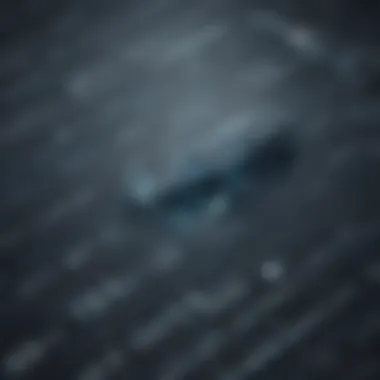
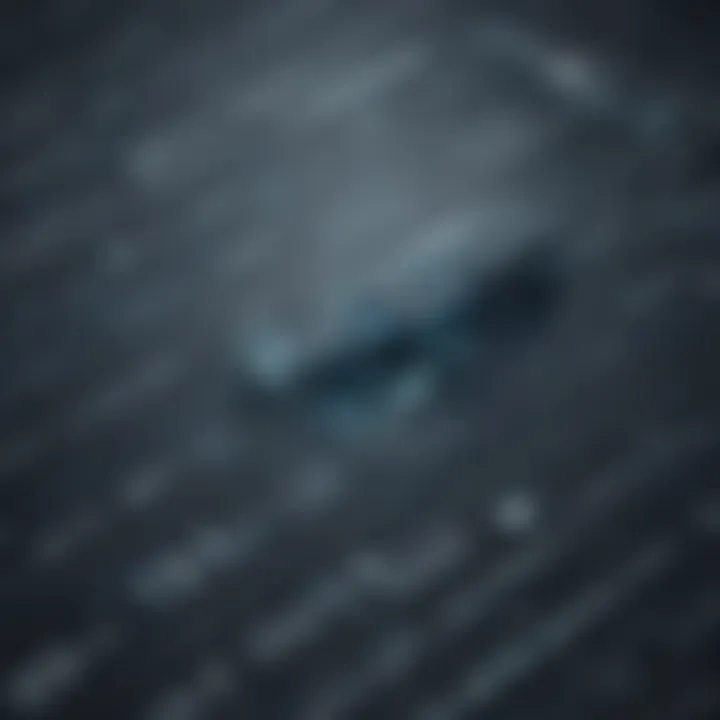
Understanding Supply Chain Efficiency Principles
Supply chain efficiency encompasses the optimization of processes to enhance operational performance. It involves a comprehensive approach ranging from demand forecasting, inventory management to logistics. By integrating various facets of the supply chain, organizations can maximize productivity and streamline operations effectively.
Strategies for Demand Forecasting
Demand forecasting is a critical aspect of efficient supply chain planning. By utilizing advanced data analytics and trend analysis, organizations can anticipate market fluctuations and consumer behavior accurately. Implementing robust forecasting techniques enables proactive decision-making, reducing inventory costs and ensuring timely product availability.
Streamlining Inventory Management Procedures
Efficient inventory management is pivotal in maintaining a well-functioning supply chain. Emphasizing concepts like Just-In-Time (JIT) inventory control and ABC analysis can minimize holding costs, prevent stockouts, and improve order fulfillment rates. Strategic inventory optimization fosters operational efficiency and cost reduction.
Fine-Tuning Logistics Operations
Optimizing logistics operations plays a vital role in enhancing supply chain efficiency. Leveraging technology such as transportation management systems (TMS) and route optimization software can streamline delivery schedules, reduce lead times, and cut down transportation costs. By aligning logistics processes with organizational goals, businesses can achieve greater agility and customer satisfaction.
Realizing Operational Excellence through Collaboration
Collaboration is key to achieving operational excellence in supply chain planning. By fostering strong partnerships with suppliers, distributors, and service providers, organizations can build a resilient and responsive supply chain ecosystem. Collaborative efforts facilitate information sharing, risk mitigation, and continuous process improvement, ultimately driving efficiency and competitiveness in the marketplace.
Introduction to End-to-End Supply Chain Planning
In today's complex business landscape, optimizing efficiency in end-to-end supply chain planning is paramount for organizational success. This section delves into the foundational principles that underpin effective supply chain management. By exploring key elements such as demand forecasting, inventory management, and logistics optimization, businesses can streamline their operations and achieve peak performance.
Understanding the Scope of Supply Chain Planning
The Evolution of Supply Chain Management
The evolution of supply chain management is a critical aspect to consider when strategizing for end-to-end supply chain planning. This section traces the historical development of supply chain practices, highlighting the shift towards integrated and agile processes. Understanding how supply chains have evolved over time provides invaluable insights into best practices and potential areas for improvement. While traditional supply chain models focused on linear operations, modern approaches emphasize flexibility, collaboration, and innovation.
The Role of Technology in Modern Supply Chains
Technology plays a pivotal role in shaping modern supply chains, revolutionizing how businesses manage their operations. From automated systems to advanced analytics tools, technology enables organizations to enhance efficiency and responsiveness. Embracing digital solutions empowers companies to make data-driven decisions, optimize processes, and adapt to market dynamics swiftly. While technology offers numerous benefits in improving supply chain performance, challenges such as data security and integration complexities must be addressed to realize its full potential.
Key Components of End-to-End Supply Chain Planning
Demand Forecasting
Demand forecasting stands at the forefront of efficient supply chain planning, enabling organizations to anticipate market trends and customer demands. By leveraging historical data, market analysis, and predictive modeling, businesses can optimize inventory levels, production schedules, and resource allocation. Accurate demand forecasting mitigates the risk of stockouts, reduces excess inventory costs, and enhances customer satisfaction. However, the challenge lies in balancing forecasting precision with the inherent volatility of today's markets.
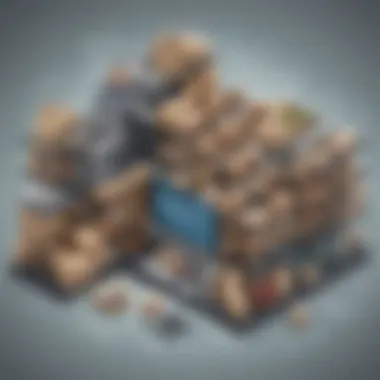
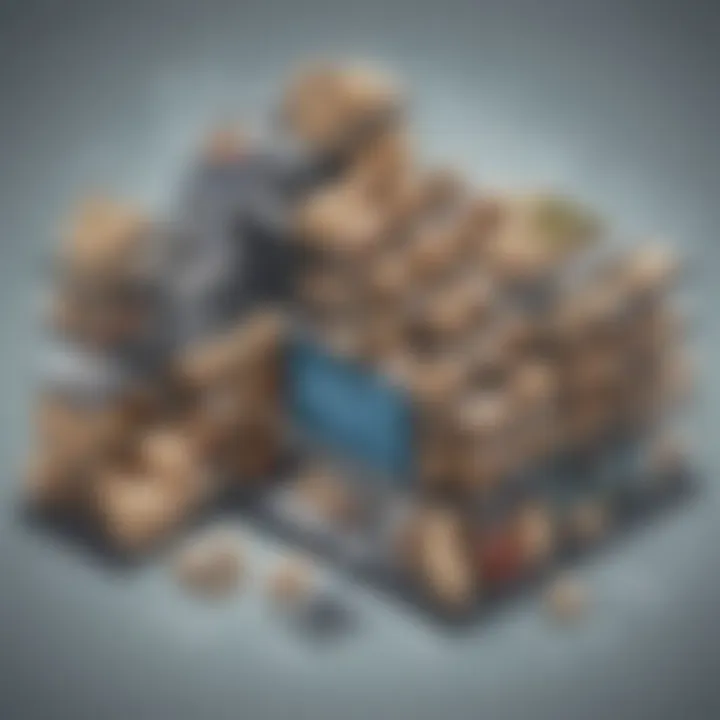
Inventory Optimization
Inventory optimization is a key component of end-to-end supply chain planning, aiming to strike a delicate balance between supply and demand. Effective inventory management involves minimizing carrying costs while ensuring product availability to meet consumer needs. Techniques such as ABC analysis, economic order quantity, and just-in-time practices are utilized to optimize inventory levels and enhance operational efficiency. While lean inventory practices reduce waste and improve cash flow, over-optimization may lead to stock shortages and missed opportunities.
Supplier Relationship Management
Supplier relationship management plays a crucial role in establishing robust partnerships that drive supply chain success. By fostering collaborative relationships with suppliers, organizations can enhance reliability, quality, and innovation across their supply networks. Effective supplier management involves clear communication, mutual trust, and shared goals to align interests and achieve mutual benefits. While strong supplier relationships can lead to cost savings, improved product quality, and faster time-to-market, managing diverse supplier portfolios and global networks presents logistical challenges that require careful navigation.
Challenges in Supply Chain Planning
Supply chain planning is a complex landscape that presents numerous challenges to organizations seeking operational efficiency. In this article, the exploration of challenges in supply chain planning is pivotal to understanding the dynamics of modern supply chains. Addressing these challenges head-on is crucial for organizations aiming to optimize their end-to-end supply chain processes. By delving into the intricacies of supply chain challenges, businesses can identify areas of improvement and implement strategic solutions to enhance overall performance.
Globalization and Supply Chain Complexity
Managing International Logistics
Managing international logistics is a critical component of supply chain operations in a globalized marketplace. The intricacies of coordinating transportation, customs, and compliance across international borders add layers of complexity to supply chain management. Organizations must navigate different regulations, time zones, and cultural nuances when managing international logistics. Despite the challenges, efficient management of international logistics can lead to cost savings, improved delivery times, and enhanced customer satisfaction. Leveraging technology solutions, such as transportation management systems, can streamline international logistics operations and provide real-time visibility into the movement of goods.
Mitigating Supply Chain Risks
Mitigating supply chain risks is essential to ensure the smooth flow of operations and minimize disruptions. Proactively identifying and addressing potential risks, such as natural disasters, supplier disruptions, or geopolitical instability, is crucial for maintaining supply chain resilience. By implementing risk mitigation strategies, such as dual sourcing, inventory buffer stock, and data analytics for predictive risk assessment, organizations can safeguard their supply chains against unforeseen challenges. While mitigating supply chain risks requires investment and resources, the long-term benefits of a resilient and agile supply chain outweigh the initial costs.
Integration of New Technologies
Embracing new technologies is imperative for organizations seeking to stay ahead in the evolving landscape of supply chain management. The integration of IoT and AI in supply chain operations revolutionizes traditional processes by enabling real-time monitoring, predictive analytics, and automation. Implementing IoT devices across the supply chain, such as RFID tags and sensors, allows for granular tracking of goods and assets, enhancing visibility and traceability. Similarly, leveraging AI algorithms for demand forecasting, route optimization, and inventory management empowers organizations to make data-driven decisions and respond swiftly to market fluctuations.
Enhancing Data Analytics Capabilities
Enhancing data analytics capabilities is instrumental in unlocking valuable insights and optimizing supply chain performance. By harnessing the power of big data analytics, organizations can derive actionable intelligence from vast volumes of supply chain data. Advanced analytics tools enable predictive modeling, scenario planning, and performance monitoring, empowering decision-makers to proactively identify opportunities for improvement. Investing in data analytics capabilities allows organizations to drive operational efficiencies, enhance forecasting accuracy, and mitigate risks by leveraging real-time data insights.
Strategies for Efficient Supply Chain Planning
In this section, we delve into the essential topic of Strategies for Efficient Supply Chain Planning within the broader context of maximizing efficiency in end-to-end supply chains. Efficient supply chain planning is crucial for organizations looking to streamline operations, reduce costs, and enhance overall performance. By implementing strategic approaches to planning, businesses can optimize their processes and improve customer satisfaction. Some key elements to consider include proactive demand forecasting, optimal inventory management, and effective logistics optimization. Collaborative efforts in supply chain planning play a pivotal role in ensuring seamless operations from suppliers to end-users.
Collaborative Demand Planning
Cross-Functional Alignment:
Cross-Functional Alignment focuses on integrating departments or teams within an organization with the shared objective of achieving supply chain efficiency. By aligning functions such as sales, marketing, and operations, businesses can streamline communication, improve decision-making processes, and enhance overall coordination. The key characteristic of Cross-Functional Alignment lies in its ability to break down silos and foster a cohesive approach to supply chain planning. This collaboration helps in aligning goals and strategies across different departments, leading to improved forecasting accuracy and responsiveness to market changes.
By ensuring that various functions work cohesively towards common objectives, businesses can leverage diverse perspectives and expertise, leading to more robust supply chain planning outcomes. However, challenges may arise from differing priorities or communication breakdowns if not managed effectively.
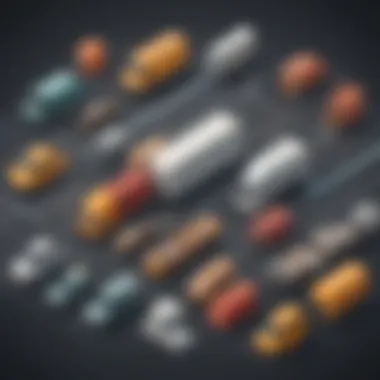
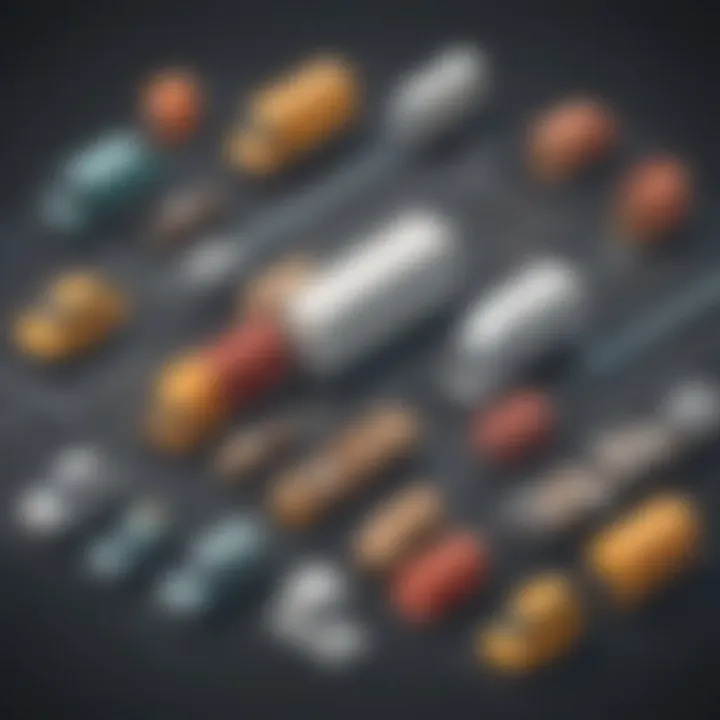
Customer-Centric Forecasting:
Customer-Centric Forecasting prioritizes customer needs and preferences in the demand forecasting process. By analyzing consumer behavior, market trends, and feedback, businesses can tailor their forecasts to meet customer demands effectively. The key characteristic of Customer-Centric Forecasting is its focus on understanding and predicting customer behavior accurately. This approach enables businesses to align their inventory levels and production schedules with customer expectations, thereby enhancing customer satisfaction and loyalty.
A significant advantage of Customer-Centric Forecasting is the ability to anticipate shifts in demand patterns and adjust supply chain activities accordingly. However, challenges may arise from volatile market conditions or fluctuations in consumer behavior, necessitating flexibility and adaptability in forecasting strategies.
Effective Inventory Management
Just-in-Time Inventory Practices:
Just-in-Time Inventory Practices emphasize minimizing inventory levels to reduce holding costs and improve operational efficiency. By synchronizing production with demand forecasts, businesses can optimize inventory levels while ensuring timely order fulfillment. The key characteristic of Just-in-Time Inventory Practices is their focus on lean principles and continuous process improvement. This approach helps in reducing waste, enhancing flexibility, and increasing responsiveness to market changes.
The unique feature of Just-in-Time Inventory Practices lies in their ability to create a demand-driven supply chain, where inventory is replenished only as needed. This leads to lower inventory carrying costs, reduced obsolescence risks, and increased capital efficiency. However, challenges may arise from supply chain disruptions or fluctuating demand patterns, requiring robust risk management and contingency planning.
ABC Analysis for Inventory Segmentation:
ABC Analysis for Inventory Segmentation categorizes inventory items based on their value and contribution to overall revenue. By classifying items as A (high-value), B (medium-value), and C (low-value), businesses can prioritize resources and focus on managing critical inventory more effectively. The key characteristic of ABC Analysis is its ability to optimize inventory control and resource allocation based on the importance of each item.
The unique feature of ABC Analysis lies in its capacity to identify high-impact items that require closer monitoring and strategic inventory decisions. This method helps in reducing stockouts, improving inventory turnover rates, and enhancing overall supply chain efficiency. However, challenges may arise from accurate classification and consistent review processes to ensure alignment with business objectives.
Enhanced Logistics Optimization
Route Optimization Strategies:
Route Optimization Strategies aim to enhance the efficiency of distribution networks by optimizing delivery routes and schedules. By leveraging data analytics and geographic information systems, businesses can minimize transportation costs, reduce delivery times, and improve fleet utilization. The key characteristic of Route Optimization Strategies is their focus on maximizing delivery performance while minimizing operational expenses.
The unique feature of Route Optimization Strategies lies in their ability to adapt to real-time traffic conditions, weather disruptions, and changing customer requirements. This dynamic approach enables businesses to achieve cost savings, reduce carbon emissions, and enhance customer satisfaction. However, challenges may arise from integrating route optimization software, training personnel, and managing route deviations effectively.
Real-Time Tracking Technologies:
Real-Time Tracking Technologies involve the use of GPS, RFID, or IoT devices to monitor the movement of goods in the supply chain in real-time. By obtaining instant visibility into shipment status and location, businesses can enhance inventory control, improve delivery accuracy, and mitigate supply chain risks. The key characteristic of Real-Time Tracking Technologies is their capability to provide timely and accurate information for better decision-making.
The unique feature of Real-Time Tracking Technologies lies in their ability to proactively identify issues such as delays, theft, or damage during transit, enabling immediate intervention and resolution. This proactive monitoring reduces lead times, enhances order fulfillment rates, and strengthens supply chain resilience. However, challenges may arise from initial technology investment costs, data privacy concerns, and integration complexities with existing systems.
Implementing Technology Solutions in Supply Chain Planning
In the realm of end-to-end supply chain planning, Implementing Technology Solutions plays a pivotal role in enhancing operational efficiency and optimizing processes. By integrating advanced technological tools and systems, organizations can streamline their supply chain management, improve decision-making capabilities, and adapt to dynamic market demands. It is essential to comprehend the nuances of technology integration to leverage its benefits fully.
Adoption of Supply Chain Management Software
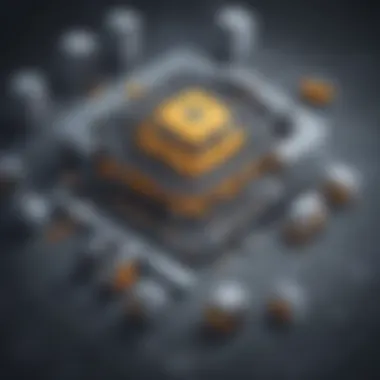
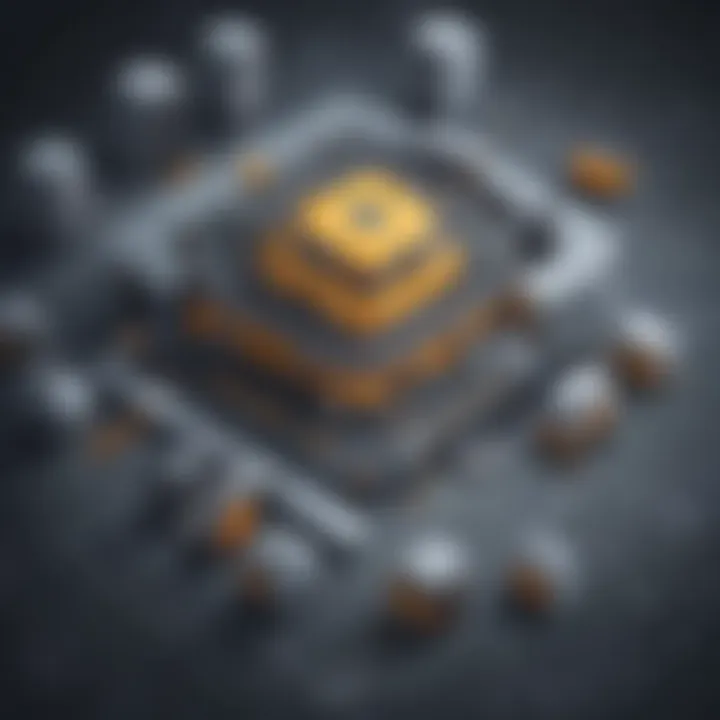
ERP Systems for Integrated Planning:
ERP Systems play a vital role in streamlining various aspects of supply chain management, including inventory control, order tracking, and resource planning. The key characteristic of ERP Systems lies in their ability to consolidate disparate operational functions into a cohesive digital platform, facilitating seamless data flow and process automation. This centralized approach enhances visibility, coordination, and decision-making across the supply chain ecosystem. Organizations opt for ERP Systems due to their scalability, flexibility, and ability to align with evolving business requirements. Despite their advantages, ERP Systems may pose challenges related to implementation costs, customization complexities, and integration issues within complex supply chain networks.
Warehouse Management Solutions:
Warehouse Management Solutions are instrumental in optimizing inventory handling, storage, and order fulfillment processes within supply chain operations. The key characteristic of Warehouse Management Solutions is their capacity to enhance warehouse efficiency by automating tasks, optimizing storage space, and ensuring accurate inventory tracking. Organizations choose these solutions for their real-time monitoring capabilities, integration with other supply chain modules, and scalability to accommodate varying business scales. However, potential disadvantages of Warehouse Management Solutions may include initial setup costs, training requirements for staff, and potential system integration challenges within existing infrastructure.
Utilizing Predictive Analytics Tools
Forecast Accuracy Improvement:
Forecast Accuracy Improvement is a critical element in supply chain planning, enabling organizations to anticipate demand fluctuations, optimize inventory levels, and enhance resource allocation. The key characteristic of Forecast Accuracy Improvement lies in its data-driven predictive modeling capabilities, which forecast future trends based on historical data patterns and market insights. Organizations opt for this tool to mitigate stockouts, reduce excess inventory costs, and enhance customer satisfaction through timely order fulfillment. Despite its advantages, Forecast Accuracy Improvement may face challenges related to data quality, algorithm accuracy, and the complexity of integrating diverse data sources within the predictive model.
Risk Prediction Models:
Risk Prediction Models play a significant role in identifying potential disruptions, vulnerabilities, and uncertainties within the supply chain, enabling proactive risk mitigation strategies. The key characteristic of Risk Prediction Models is their ability to leverage advanced algorithms and machine learning techniques to forecast potential risks based on historical patterns and external factors. Organizations integrate these models to enhance supply chain resilience, minimize losses during unforeseen events, and optimize contingency planning processes. However, challenges may arise concerning data security, model interpretation robustness, and the continuous adaptation of risk models to evolving business landscapes.
Measuring Success in Supply Chain Planning
In the realm of supply chain planning, the concept of measuring success holds paramount importance. It serves as the compass guiding organizations towards operational excellence and efficiency. By establishing robust performance metrics, companies can gauge the effectiveness of their supply chain strategies and identify areas for improvement. Successful measurement encompasses a comprehensive evaluation of key performance indicators that resonate with the core objectives of the business. Insights derived from these metrics empower decision-makers to make data-driven choices that optimize processes and drive sustainable growth.
Performance Metrics for Supply Chain Efficiency
Order Fulfillment Rates
Order Fulfillment Rates play a pivotal role in assessing supply chain efficiency. This metric quantifies the percentage of customer orders fulfilled within a specified timeframe. High order fulfillment rates signify operational proficiency and customer satisfaction. Maintaining optimal fulfillment rates is essential for meeting customer expectations and fostering loyalty. However, challenges such as inventory inaccuracies or fulfillment delays can impact this metric negatively, highlighting areas needing attention and refinement.
Inventory Turnover Ratios
Inventory Turnover Ratios offer insights into how quickly a company converts its inventory into sales. A high turnover ratio indicates strong sales performance and inventory management efficiency. Monitoring this metric enables businesses to optimize inventory levels, minimize holding costs, and maximize cash flow. Nevertheless, excessively high turnover rates may suggest stockouts or inadequate inventory levels, underscoring the delicate balance required for optimal inventory turnover.
Supply Chain Lead Time
Supply Chain Lead Time represents the duration from order placement to order fulfillment. Minimizing lead times is critical for enhancing operational agility and meeting evolving customer demands. Shorter lead times diminish the risk of stockouts, enable timely order processing, and enhance customer satisfaction. However, optimizing lead times requires synchronized coordination across the entire supply chain, from procurement to delivery, to streamline processes and mitigate delays.
Continuous Improvement Initiatives
Continuous Improvement Initiatives are cornerstone to fostering operational excellence in supply chain planning. These initiatives, such as Kaizen Practices and Lean Six Sigma Methodologies, drive ongoing enhancements and efficiency gains within the supply chain.
Kaizen Practices
Kaizen, a Japanese philosophy emphasizing continuous improvement, promotes a culture of incremental enhancements and waste reduction. By encouraging employees at all levels to contribute to process refinement, organizations can achieve sustainable growth and operational excellence. The iterative nature of Kaizen fosters innovation, employee engagement, and a relentless pursuit of excellence within the supply chain.
Lean Six Sigma Methodologies
Lean Six Sigma combines Lean Manufacturing principles and Six Sigma methodologies to eliminate defects and enhance efficiency. This data-driven approach focuses on streamlining processes, reducing variability, and optimizing performance. By leveraging Lean Six Sigma tools such as DMAIC (Define, Measure, Analyze, Improve, Control), organizations can systematically identify and rectify inefficiencies, driving continuous improvement and bolstering supply chain effectiveness.