Exploring Diverse Examples of Six Sigma Implementations Across Industries
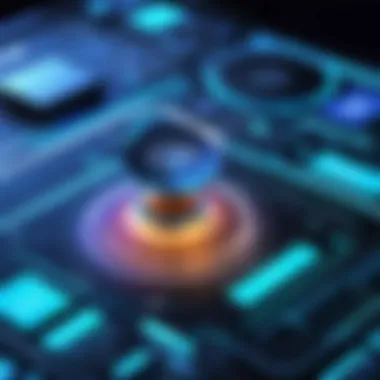
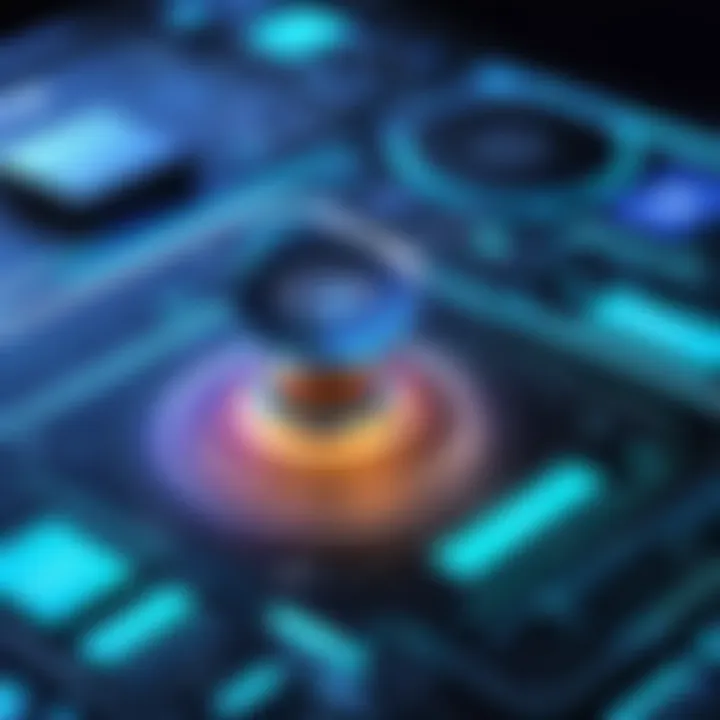
Understanding Concepts of Storage, Security, or Networking
In the realm of Six Sigma methodology, it is imperative to grasp the foundational concepts of storage, security, or networking to fully appreciate its implications in achieving operational excellence. Storage involves the management of data and digital assets, ensuring efficient access and preservation. Security pertains to safeguarding information integrity and confidentiality against unauthorized access. Networking focuses on establishing connections and facilitating communication between various devices and systems. Understanding these fundamental principles is vital for implementing Six Sigma effectively and optimizing processes.
Examples of Best Practices and Tips for Implementation
- Implementing Six Sigma methodologies requires adherence to best practices for optimizing operational outcomes. This entails defining clear objectives, measuring performance metrics, analyzing data, improving processes, and controlling variations. Tips for successful implementation include fostering a culture of continuous improvement, providing adequate training, empowering employees to make data-driven decisions, and embracing innovation to drive efficiency. By incorporating these practices, organizations can enhance quality, streamline operations, and achieve sustainable performance improvements.
Analysis of Industry Trends and Innovations
- Staying abreast of the latest trends and technological advancements in Six Sigma is crucial for organizations striving for excellence. The evolution of storage technologies includes advancements in cloud storage, big data solutions, and data analytics tools to enhance data management and accessibility. Cybersecurity trends encompass the rise of artificial intelligence in threat detection, blockchain for secure transactions, and biometric authentication methods to fortify digital defenses. Networking innovations introduce technologies like 5G, Internet of Things (IoT), and software-defined networking (SDN) to amplify connectivity, speed, and flexibility. By leveraging these trends, organizations can align their processes with cutting-edge solutions and stay competitive in today's dynamic business landscape.
Real-Life Case Studies and Success Stories
- Examining practical examples of successful Six Sigma implementations offers invaluable insights into its transformative impact. Real-life case studies of organizations across different sectors showcase how Six Sigma principles have facilitated quality enhancement, cost reduction, and operational efficiency. From streamlining manufacturing processes to optimizing healthcare delivery and enhancing financial services, these success stories underscore the tangible benefits of implementing Six Sigma methodologies. By studying these cases, businesses can learn from best practices, avoid common pitfalls, and drive continuous improvement initiatives within their own operations.
Evaluation and Comparison of Tools and Products
- Conducting thorough reviews and comparisons of tools and products associated with Six Sigma implementation is essential for making informed decisions. Evaluating storage software and hardware solutions involves assessing factors like scalability, reliability, security features, and compatibility with existing infrastructure. Comparing cybersecurity tools and solutions requires analyzing performance, ease of deployment, threat detection capabilities, and regulatory compliance measures. Similarly, evaluating networking equipment and services entails examining speed, reliability, scalability, and support offerings. By conducting these evaluations, organizations can select the most suitable tools and products that align with their operational requirements and strategic goals.
Intro to Six Sigma
Six Sigma, an innovative methodology that has revolutionized the world of quality management, forms the cornerstone of operational excellence for modern enterprises. In this pivotal section of our article, we explore the fundamental principles that underpin Six Sigma and its profound impact on diverse industries. Understanding the nuances of Six Sigma is crucial for organizations striving for continual improvement and sustainable growth. We delve deep into the intricacies of this methodology, shedding light on how it drives operational efficiency, enhances quality standards, and maximizes customer satisfaction.
Understanding the Basics of Six Sigma
Definition of Six Sigma
Embarking on our journey, we first unravel the essence of Six Sigma by exploring its core definition. Six Sigma epitomizes a data-driven approach to process improvement, aiming to minimize defects and variance within operations. The key characteristic of Six Sigma lies in its emphasis on statistical analysis and problem-solving methodologies to achieve desired outcomes consistently. This methodology's unique feature is its DMAIC (Define, Measure, Analyze, Improve, Control) process, which guides practitioners through structured problem-solving. While Six Sigma offers unparalleled benefits in enhancing quality and productivity, its rigid structure can sometimes hinder innovation in fast-paced environments.
Key Concepts of Six Sigma
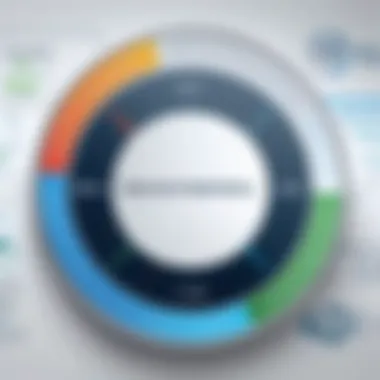
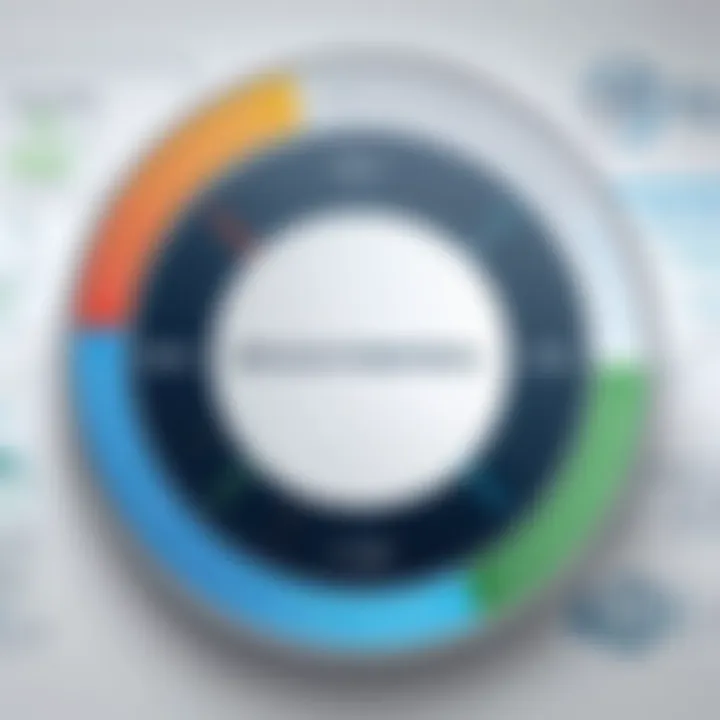
Transitioning into the key concepts of Six Sigma, we navigate through crucial principles that govern its application. Central to Six Sigma are concepts such as process variation, customer focus, and data-driven decision-making. These key characteristics enable organizations to identify root causes of issues, optimize processes, and deliver value to customers efficiently. The distinctive feature of Six Sigma's key concepts is the integration of statistical tools like Control Charts, Pareto Analysis, and Process Mapping to drive process enhancements. While these concepts undeniably offer advantages in terms of streamlining operations and reducing errors, they may pose challenges in terms of training requirements and cultural adaptation within organizations.
History and Evolution of Six Sigma
Origins of Six Sigma
Diving into the historical origins of Six Sigma, we uncover its genesis and evolution into a widely adopted quality management approach. Originating from Motorola in the 1980s, Six Sigma gained prominence for its systematic methodology for process improvement. The key characteristic of Six Sigma's origins is its alignment with Total Quality Management (TQM) principles, emphasizing customer satisfaction and continual refinement of processes. The unique feature of Six Sigma's origins lies in its integration of statistical methods from experts like George Box and Walter Shewhart to quantify quality levels accurately. While the origin story of Six Sigma showcases its ability to revolutionize quality practices, implementing this methodology required significant cultural shifts within organizations.
Development of Six Sigma Methodology
Continuing our exploration, we delve into the evolution of Six Sigma methodology and its refinement over the years. The development of Six Sigma methodology saw organizations like General Electric (GE) and Toyota adopt and enhance its principles to drive operational excellence. The key characteristic of Six Sigma methodology's development is its shift towards a more customer-centric approach, aligning business processes with customer expectations. The unique feature of Six Sigma methodology's evolution is the incorporation of Lean principles to streamline processes and eliminate waste. While the development of Six Sigma methodology has undoubtedly led to remarkable financial benefits and quality improvements for organizations, striking a balance between rigorous adherence to principles and flexibility in implementation remains a persistent challenge.
Six Sigma in Manufacturing Sector
When delving into the realm of Six Sigma in the manufacturing sector, one is confronted with a landscape rich in strategies and methodologies that seek to elevate operational efficiency to new heights. This article sheds light on the pivotal role that Six Sigma plays within manufacturing, emphasizing its capabilities to streamline processes and enhance overall quality. By focusing on this sector, readers are exposed to the intricate mechanisms and benefits underlying the successful integration of Six Sigma principles.
Toyota's Application of Six Sigma
Implementation Strategies at Toyota
At the core of Toyota's application of Six Sigma lie intricately crafted implementation strategies that transcend traditional approaches to process improvement. These strategies not only revolutionize the production landscape but also set a benchmark for efficiency and excellence. By exploring the nuances of Toyota's implementation strategies, readers can grasp the essence of meticulous planning and execution that underpins its operational success. The unique feature of Toyota's approach lies in its holistic perspective, encapsulating every facet of the manufacturing process to maximize effectiveness and minimize wastage.
Impact on Production Efficiency
The impact of Toyota's adept application of Six Sigma on production efficiency cannot be overstated. It serves as a beacon of inspiration for other industry players, showcasing the remarkable outcomes that result from a harmonious blend of innovation and precision. Through a detailed analysis of Toyota's achievements in the realm of production efficiency, readers gain a profound understanding of how Six Sigma methodologies can drive tangible improvements across all operational dimensions. The key characteristic of this impact lays in its sustainable nature, fostering a culture of continuous enhancement and adaptability that propels Toyota towards unmatched performance levels.
General Electric's Success with Six Sigma
Integration of Six Sigma at GE
General Electric stands out as a prime example of organizational success through the seamless integration of Six Sigma principles. The meticulous approach taken by GE in infusing Six Sigma into its operations underscores a commitment to excellence and sustainability. By examining the core features of GE's integration strategy, readers can glean invaluable insights into the transformative power of systematic quality management. The unique feature of this integration lies in its scalability and versatility, allowing GE to tailor Six Sigma initiatives to diverse business functions with precision and efficacy.
Financial Benefits Achieved
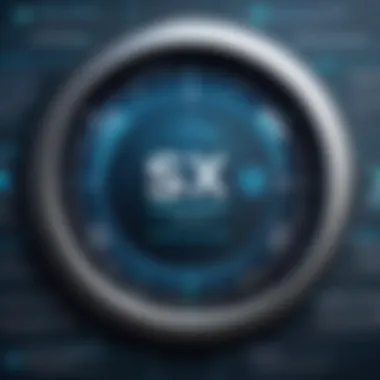
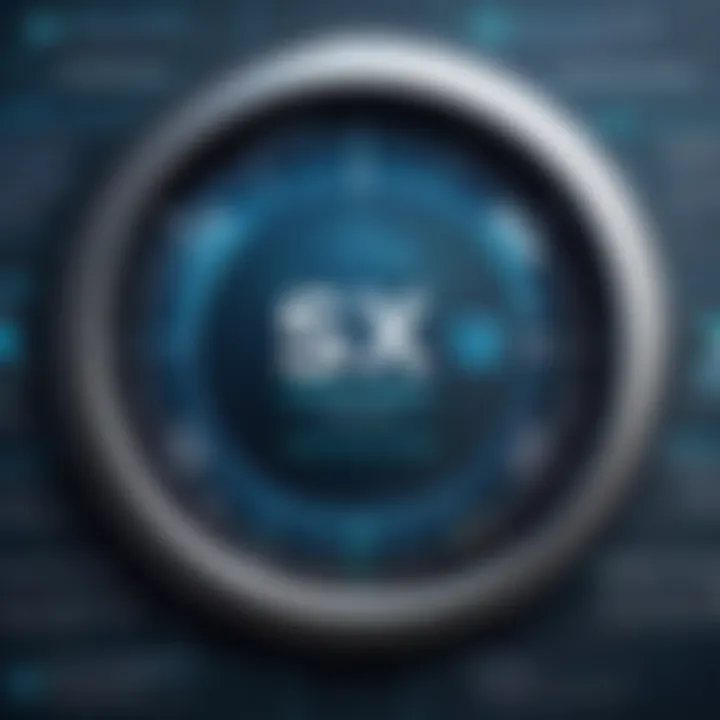
The financial benefits reaped by General Electric following its embrace of Six Sigma illuminate the profound impact of quality-driven practices on an organization's bottom line. Through a diligent examination of the financial milestones achieved by GE, readers are exposed to the direct correlation between quality enhancements and fiscal prosperity. The key characteristic of these benefits lies in their long-term sustainability, positioning GE as a trailblazer in realizing both operational excellence and financial success through the lens of Six Sigma principles.
Six Sigma in Service Industries
In this comprehensive exploration of Six Sigma principles, the focus shifts towards Service Industries, a domain where quality and efficiency are paramount. Six Sigma techniques play a pivotal role in enhancing processes, reducing errors, and improving overall customer satisfaction. By implementing Six Sigma methodologies in Service Industries, organizations can achieve significant operational improvements and drive sustainable growth. This section delves deep into the specific elements, benefits, and considerations related to Six Sigma in Service Industries.
Banking Sector and Six Sigma
Improving Customer Experience
Delving deeper into the application of Six Sigma in the Banking Sector unveils a critical aspect - Improving Customer Experience. This strategic focus on enhancing client interactions and satisfaction levels is a cornerstone of successful Six Sigma implementations in banks. The key characteristic of Improving Customer Experience lies in its ability to drive loyalty, retention, and profitability for financial institutions. By prioritizing customer-centric strategies, banks can differentiate themselves in a competitive market landscape. However, challenges such as consistent service delivery and personalization must be carefully navigated to reap the full benefits of this approach.
Reducing Error Rates
Another vital component of Six Sigma integration in the Banking Sector is Reducing Error Rates. Minimizing mistakes and enhancing operational accuracy are crucial for financial institutions to maintain regulatory compliance and trust among customers. The essence of Reducing Error Rates lies in its capacity to mitigate risks, lower costs, and streamline processes efficiently. While aiming for near-perfect accuracy is commendable, banks must strike a balance between operational speed and error reduction to optimize business outcomes. The unique feature of Reducing Error Rates lies in its dual impact on operational efficiency and customer satisfaction, making it a strategic priority in Six Sigma initiatives within the banking domain.
Healthcare's Adoption of Six Sigma
Enhancing Patient Care
Shifting focus to healthcare, the integration of Six Sigma principles revolves around Enhancing Patient Care. This aspect emphasizes the continuous improvement of medical services, patient outcomes, and overall healthcare experiences. The key characteristic of Enhancing Patient Care is its alignment with clinical excellence, safety standards, and patient-centric care deliveries. By incorporating Six Sigma methodologies, healthcare providers can optimize treatment processes, reduce medical errors, and foster a culture of quality within medical facilities. However, the challenge lies in effectively balancing efficiency with patient empathy and holistic care approaches to ensure comprehensive and sustainable improvements.
Streamlining Medical Processes
Streamlining Medical Processes emerges as a paramount objective in leveraging Six Sigma within healthcare settings. The core of this initiative is to optimize operational workflows, enhance resource utilization, and maximize the efficiency of healthcare delivery systems. The key characteristic of Streamlining Medical Processes lies in its ability to reduce waiting times, improve clinic throughput, and standardize treatment protocols for better patient outcomes. While focusing on process efficiency is critical, healthcare organizations must also consider the implications on staff workload, patient communication, and clinical decision-making processes. The unique feature of Streamlining Medical Processes is its potential to revolutionize healthcare delivery models through systematic, data-driven improvements.
Case Studies of Six Sigma Success
In the realm of Six Sigma, case studies serve as illuminating beacons showcasing the practical application and tangible outcomes of this methodology. Delving into case studies allows for a thorough exploration of successful implementations across various industries. Such detailed examinations serve as invaluable learning tools, offering insights into the transformative power of Six Sigma principles in driving process improvement, enhancing efficiency, and achieving operational excellence.
Motorola's Six Sigma Journey
Impact on Quality Standards
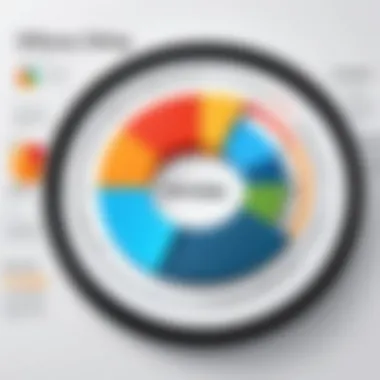
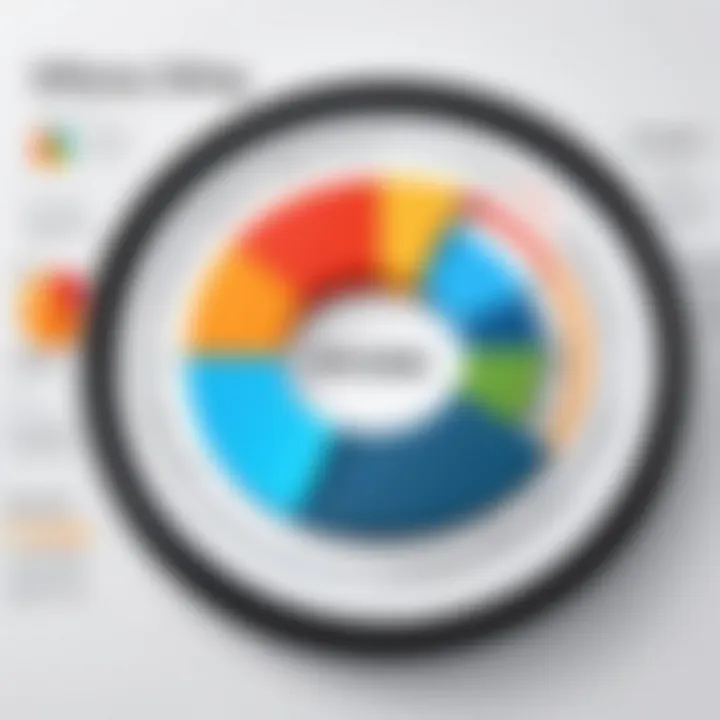
Motorola's Six Sigma journey exemplifies a relentless pursuit of quality excellence. The impact on quality standards has been profound, ushering in a new era of stringent quality control and meticulous attention to detail. By focusing on eliminating defects and enhancing processes, Motorola set a benchmark for achieving unparalleled quality levels, setting a precedent for other organizations to emulate. The emphasis on quality standards not only ensured product perfection but also instilled a quality-driven culture within the company, permeating through every facet of its operations.
Global Expansion through Six Sigma
Motorola's global expansion through Six Sigma underscores the methodology's scalability and universality. By leveraging Six Sigma principles in its expansion strategies, Motorola facilitated seamless growth across diverse geographies, transcending cultural and operational barriers. The disciplined approach offered by Six Sigma provided a structured framework for sustainable growth, enabling Motorola to maintain consistency in quality standards while adapting to local market nuances. This expansion not only bolstered Motorola's global presence but also solidified its reputation as a quality-driven multinational corporation.
Amazon's Efficiency with Six Sigma
Innovative Practices Implemented
Amazon's efficiency with Six Sigma is epitomized by its innovative practices that revolutionized the e-commerce landscape. Through the implementation of cutting-edge methodologies and advanced analytics, Amazon enhanced its operational efficiency, optimizing processes, and accelerating delivery timelines. The innovative practices introduced by Amazon reshaped industry standards, setting a new bar for operational excellence and customer satisfaction. By integrating Six Sigma into its core strategic initiatives, Amazon not only achieved operational efficiency but also set a precedent for leveraging data-driven decision-making in modern business environments.
Enhanced Customer Satisfaction
Amazon's relentless focus on enhancing customer satisfaction underscores the core ethos of Six Sigma principles. By prioritizing customer-centric strategies and service excellence, Amazon secured unwavering loyalty and trust from its consumer base. The emphasis on enhanced customer satisfaction not only drove business growth but also cultivated a loyal customer following, positioning Amazon as a paragon of customer service excellence. Through the alignment of Six Sigma methodologies with customer-focused initiatives, Amazon set new benchmarks for achieving unparalleled customer satisfaction and loyalty.
Challenges and Limitations of Six Sigma
In dissecting the crucial segment concerning the Challenges and Limitations of Six Sigma within the broader context of this insightful article, it becomes imperative to unravel the intricate fabric of obstacles that organizations encounter on their Six Sigma journey. Delving into the nuances of this topic sheds light on the hurdles that can impede the seamless implementation of Six Sigma methodologies. Understanding these aspects is paramount to harnessing the full potential of Six Sigma principles and achieving operational excellence.
Overcoming Resistance to Change
Strategies for Change Management
Exploring the realm of Strategies for Change Management within the realm of Six Sigma unveils a systematic approach towards mitigating resistance amidst organizational transformations. This specialized facet plays a pivotal role in navigating the turbulent waters of change within the Six Sigma framework. By emphasizing proactive strategies and robust communication channels, Change Management transcends mere adaptation, becoming a cornerstone for successful Six Sigma implementation. The unique characteristic of adaptability inherent in Strategies for Change Management renders it a favored tool for organizations aiming to fortify their operational frameworks. Despite its merits, it is vital to acknowledge potential drawbacks such as scalability challenges that may arise in the context of this article.
Engaging Stakeholders Effectively
The aspect of Engaging Stakeholders Effectively in the panorama of Six Sigma underscores the significance of collaboration and cohesion in driving organizational change. This facet serves as a linchpin, fostering alignment and buy-in from key stakeholders within the Six Sigma ecosystem. By amplifying the voices of stakeholders and promoting a sense of ownership, effective stakeholder engagement propels the realization of Six Sigma objectives. The distinguishing feature of inclusivity embedded in Engaging Stakeholders Effectively positions it as a strategic asset for amplifying the impact of Six Sigma initiatives. However, challenges such as diverging interests among stakeholders might factor in as potential hurdles within the scope of this article.
Balancing Rigor with Flexibility
Customizing Six Sigma for Different Industries
Navigating through the realm of Customizing Six Sigma for Different Industries illuminates a tailored approach towards aligning Six Sigma methodologies with the nuanced requirements of diverse sectors. This bespoke adaptation underscores the adaptability of Six Sigma frameworks to suit the unique operational landscapes across industries. The intrinsic feature of versatility within Customizing Six Sigma for Different Industries champions its versatility as a versatile tool for harmonizing Six Sigma practices with industry-specific demands. While its benefits are pronounced, potential challenges such as resource intensiveness could present considerations within the purview of this article.
Adapting to Market Dynamics
Delving into the domain of Adapting to Market Dynamics within Six Sigma discourse underscores the aptitude for organizations to remain agile and responsive in the face of fluctuating market conditions. This dynamic aspect highlights the strategic acumen required to align Six Sigma methodologies with evolving market trends. The indispensable characteristic of nimbleness inherent in Adapting to Market Dynamics positions it as a strategic enabler for organizations seeking to weather market uncertainties through Six Sigma frameworks. Notwithstanding its advantages, aspects like scalability constraints may warrant scrutiny within the context of this article.