Unveiling Diverse Programmable Logic Controller Examples Across Industries


Understanding Programmable Logic Controller Examples
This section aims to delve into a variety of examples showcasing the practical application of Programmable Logic Controllers (PLCs) in industrial automation. By examining real-world instances and case studies, readers will gain valuable insights into the adaptability and effectiveness of PLCs across different industries.
Case Studies and Success Stories
Within this section, we will explore real-life examples of successful PLC implementations. Through these case studies, we will highlight the various strategies and approaches that have resulted in effective automation solutions. By dissecting these success stories, readers can glean valuable lessons and best practices for their own PLC projects.
Reviews and Comparison of Tools and Products
In this segment, we will conduct in-depth reviews of different PLC software and hardware options available in the market. Additionally, we will compare various products to help readers make informed decisions when selecting the most suitable PLC components for their specific automation requirements.
Industry Trends and Updates
Stay informed on the latest trends in the realm of industrial automation with a focus on PLC technologies. Explore emerging innovations, advancements, and developments in PLC systems that are shaping the future of automation. By keeping abreast of industry trends, readers can proactively adapt to changes and optimize their automation processes for enhanced efficiency.
Introduction to Programmable Logic Controllers
Industrial automation relies heavily on Programmable Logic Controllers (PLCs). These electronic devices play a crucial role in the seamless operation of various industrial processes. Understanding the basics of PLCs is essential for professionals in the IT and cybersecurity fields. The architecture of PLCs comprises input and output modules, a central processing unit, and a programming device. The reliability and robustness of PLC architecture make it a preferred choice in industrial automation. One of the key characteristics of PLC architecture is its modular design, allowing for easy customization and scalability. While PLCs offer advantages such as real-time monitoring and control, they may face challenges like limited memory capacity.
Understanding the Basics of PLCs
The Architecture of PLCs
In discussing the architecture of PLCs, it is crucial to highlight the hierarchical structure that enables seamless communication between various components. The input modules receive signals from sensors, the central processing unit processes the input data, and the output modules act based on the processed information. This streamlined process ensures the efficient operation of industrial systems. The modular design of PLC architecture allows for easy maintenance and troubleshooting, enhancing the overall reliability of automated processes.
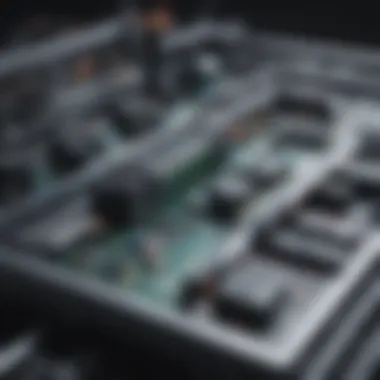

Programming Languages Used in PLCs
PLCs utilize programming languages tailored for industrial automation, such as ladder logic and structured text. These languages are optimized for real-time control and decision-making in complex manufacturing environments. The key characteristic of these languages is their intuitive graphical interface, making it easier for engineers to develop and debug control logic. While ladder logic is widely used for its simplicity, structured text offers more advanced programming capabilities. Choosing the appropriate programming language depends on the specific requirements of the industrial application.
Advantages of Using PLCs
The advantages of using PLCs in industrial automation are manifold. PLCs provide rapid response times, ensuring precise control over manufacturing processes. Their flexibility allows for seamless integration with other automation systems, enhancing overall operational efficiency. Additionally, PLCs offer robust security features to protect sensitive data and prevent unauthorized access. While the advantages of using PLCs are evident, it is essential to consider factors like initial investment costs and ongoing maintenance to maximize their benefits.
Importance of PLCs in Industrial Automation
PLCs play a pivotal role in enhancing efficiency, precision, and flexibility within industrial automation environments. Their significance is prominently observed in manufacturing processes, where efficiency directly impacts productivity and cost-effectiveness. By ensuring precision and accuracy in control systems, PLCs contribute to the consistent quality of final products. Furthermore, the flexibility provided by PLCs enables manufacturers to adapt quickly to changing production demands, ensuring operational agility.
Enhancing Efficiency in Manufacturing Processes
The integration of PLCs in manufacturing processes streamline operations, reducing downtime and enhancing overall productivity. PLCs automate repetitive tasks, minimize errors, and optimize resource utilization. By centralizing control functions, PLCs eliminate bottlenecks and ensure smooth coordination between different components of a system. This efficiency enhancement leads to cost savings and improved output quality.
Ensuring Precision and Accuracy
One of the paramount features of PLCs is their ability to maintain precise control over industrial processes. PLCs facilitate accurate measurement, monitoring, and adjustment of parameters within a system. By reducing human intervention, PLCs minimize the margin of error, resulting in consistent and high-quality output. The combination of precise control and reliable operation positions PLCs as essential tools for maintaining product standards and adhering to regulatory requirements.
Facilitating Flexibility in Production
Flexibility is a key attribute of PLCs that enables manufacturers to adapt swiftly to market demands and operational changes. PLCs support the implementation of agile manufacturing practices by allowing for quick reconfiguration of control logic and parameters. This adaptability ensures that production processes remain dynamic and responsive to evolving requirements. Moreover, PLCs facilitate seamless integration with new equipment and technologies, enabling manufacturers to stay competitive in a rapidly evolving industrial landscape.
Real-World Applications of PLCs
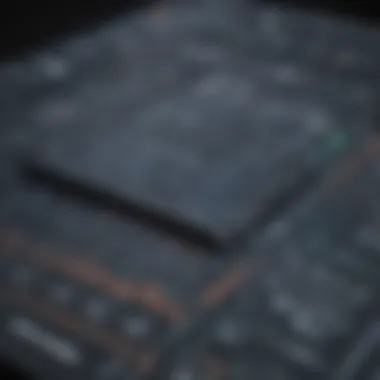

In the realm of industrial automation, the application of Programmable Logic Controllers (PLCs) embodies a pivotal role. These devices serve as the nerve center of automated processes, dictating the efficient functioning of various sectors. The integration of PLCs in real-world scenarios encompasses a myriad of benefits, ranging from streamlined operations to enhanced productivity. By exploring real-world applications of PLCs, we unveil the intricate ways in which these controllers revolutionize industries.
Automotive Industry
Robotic Assembly Lines
When delving into the Automotive Industry, Robotic Assembly Lines emerge as a prominent application of PLC technology. These automated systems leverage programmable logic controllers to orchestrate the precise assembly of vehicle components. Their key characteristic lies in their ability to execute repetitive tasks with unparalleled accuracy, significantly boosting operational efficiency. The utilization of Robotic Assembly Lines in this context proves beneficial due to their capacity to enhance production speed and minimize human errors. Despite their advantages, it is essential to consider the initial investment and maintenance costs associated with implementing such systems in the automotive sector.
Quality Control Systems
Another fundamental aspect within the Automotive Industry is Quality Control Systems, bolstered by PLCs. These systems play a crucial role in ensuring the adherence to specified standards throughout the production process. The key characteristic of Quality Control Systems lies in their capability to detect deviations and anomalies in real-time, thereby safeguarding product quality. The integration of PLCs in these systems proves advantageous as it promotes consistency, reliability, and conformity to quality benchmarks. However, it is imperative to evaluate the complexity and calibration requirements of Quality Control Systems to maximize their effectiveness within the automotive domain.
Case Studies Highlighting PLC Implementations
Case Study 1: Smart Factory Integration
Integration of IoT with PLCs
Delving into the integration of IoT with PLCs unveils a revolutionary approach to industrial automation. This fusion allows seamless communication between devices and systems, fostering interconnected operations within smart factory setups. The crux of this integration lies in harnessing the power of data exchange through IoT sensors and actuators, enabling real-time decision-making and process optimization. The key allure of integrating IoT with PLCs stems from its ability to enhance overall system intelligence, paving the way for predictive maintenance and adaptive production strategies. Despite its complexity, this amalgamation stands out as a prudent choice for modern enterprises seeking to bolster efficiency and agility.
Real-Time Monitoring and Control
The facet of real-time monitoring and control within smart factory environments showcases the responsiveness and precision afforded by PLC implementations. By facilitating instantaneous data capture and analysis, this functionality empowers operators to oversee operations with meticulous detail and make prompt adjustments as needed. The cornerstone characteristic of real-time monitoring and control is its ability to minimize latency in decision-making, thereby optimizing production processes and ensuring seamless workflow orchestration. While offering unfettered operational insights, this feature introduces a layer of complexity that demands adept handling to fully leverage its advantages in enhancing productivity and quality.
Case Study 2: Energy Management System
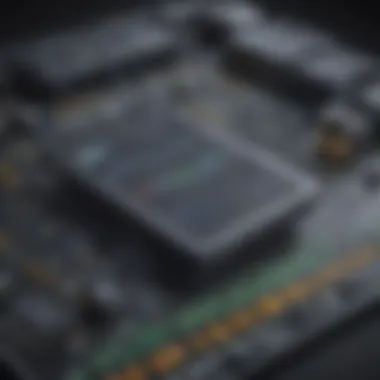

Optimizing Energy Consumption
Scrutinizing the optimization of energy consumption through PLC-driven systems sheds light on sustainable practices and cost-effective measures within industrial settings. This aspect underscores the significance of leveraging PLCs to regulate power usage intelligently, aligning energy demand with operational requirements. The crux of optimizing energy consumption lies in fine-tuning control algorithms and leveraging real-time data analytics to track and adjust energy-intensive processes efficiently. The key characteristic of this optimization approach is its potential to curtail energy wastage and minimize operational costs, rendering it a favorable choice for organizations committed to environmental stewardship and financial prudence.
Remote Monitoring Solutions
Exploring remote monitoring solutions in the context of PLC implementations reveals a paradigm shift in how industrial systems are supervised and managed. By enabling remote access to critical metrics and control functions, these solutions allow off-site personnel to monitor operations, diagnose issues, and implement corrective measures in real time. The salient feature of remote monitoring solutions is their capacity to mitigate downtime, enhance system reliability, and facilitate proactive maintenance strategies. While offering unparalleled convenience, this remote monitoring capability introduces considerations such as cybersecurity protocols and network resiliency, underscoring the need for robust infrastructure to support its benefits effectively.
Emerging Trends in PLC Technology
In the realm of industrial automation, staying abreast of Emerging Trends in PLC Technology plays a pivotal role in enhancing operational efficiencies and staying competitive in the dynamically evolving landscape. The integration of Industry 4.0 principles with PLCs has revolutionized manufacturing processes by emphasizing interconnectedness and data exchange. This amalgamation facilitates seamless communication between different components of a system, fostering real-time decision-making and adaptive production strategies. Predictive Maintenance Applications, another cornerstone of Emerging Trends in PLC Technology, operate on algorithms that preemptively detect and address potential equipment failures, thus minimizing downtime and optimizing maintenance schedules. By harnessing predictive analytics, organizations can shift from reactive to proactive maintenance paradigms, leading to substantial cost savings and improved operational reliability. Embracing these cutting-edge trends empowers industries to harness automation and intelligence synergistically, unlocking new levels of productivity and resilience.
Industry Integration
Interconnectivity and Data Exchange
Delving into the specifics of Interconnectivity and Data Exchange within the Industry 4.0 framework illuminates its pivotal role in enabling seamless communication among various industrial components. The fundamental characteristic of this integration lies in its ability to establish a network where machines, systems, and processes interact and share information in real-time. This constant data exchange fosters adaptability, efficiency, and improved decision-making within manufacturing ecosystems. The widespread adoption of Interconnectivity and Data Exchange is driven by its capacity to enhance operational visibility, promote predictive analytics, and streamline workflow orchestration. While its benefits are substantial, challenges such as data security and interoperability issues warrant careful consideration in implementing this strategy. By leveraging the unique feature of data-driven interconnectivity, industries can optimize resource utilization, mitigate risks, and propel their journey towards digital transformation.
Predictive Maintenance Applications
Highlighting the essence of Predictive Maintenance Applications underscores its pivotal role in preemptively addressing equipment failures and maximizing asset uptime. At the core of this approach is the utilization of advanced algorithms that analyze equipment performance data to predict and prevent potential malfunctions. The key characteristic of Predictive Maintenance lies in its ability to transition organizations from reactive maintenance practices to a proactive, predictive model. This shift not only minimizes unplanned downtime but also extends the lifespan of machinery and equipment. The unique feature of Predictive Maintenance Applications lies in its ability to optimize operational efficiency, reduce maintenance costs, and enhance overall equipment effectiveness. While the advantages are profound, aspects such as data accuracy, algorithm calibration, and integration complexity necessitate meticulous planning and execution. By strategically implementing Predictive Maintenance Applications, enterprises can elevate their maintenance strategies, increase equipment reliability, and achieve operational excellence.
Artificial Intelligence in PLC Programming
Machine Learning Algorithms
Exploring Machine Learning Algorithms in the realm of PLC programming sheds light on its transformative capabilities in optimizing decision-making processes and enhancing system intelligence. The key characteristic of utilizing Machine Learning algorithms with PLCs lies in their ability to analyze intricate datasets, detect patterns, and make data-driven predictions autonomously. As organizations strive for enhanced automation and efficiency, Machine Learning Algorithms offer a pathway to harness actionable insights from operational data. The unique feature of Machine Learning Algorithms is their adaptability and self-learning capabilities, enabling continuous enhancement of system performance and predictive capabilities. While the advantages of Machine Learning in PLC programming are substantial, considerations such as data quality, model training, and algorithm transparency require meticulous attention for successful implementation. By leveraging Machine Learning Algorithms, organizations can augment their decision-making prowess, optimize processes, and drive innovation within their automation frameworks.
Cognitive Automation
Unveiling the realm of Cognitive Automation within PLC programming underscores its significance in bridging the gap between human cognition and automated processing. The key characteristic of Cognitive Automation is its integration of human-like thought processes with automated decision-making mechanisms, enabling smart and intuitive system responses. This fusion of cognitive abilities with automation technologies empowers systems to perceive complex data patterns, adapt to dynamic scenarios, and optimize operational strategies intelligently. The unique feature of Cognitive Automation lies in its capacity to enhance cognitive capabilities, facilitate adaptive learning, and pave the way for sophisticated automation solutions. While the advantages of Cognitive Automation in PLC programming are profound, challenges such as data integration, cognitive model development, and scalability warrant nuanced considerations for effective deployment. By embracing Cognitive Automation, organizations can elevate the intelligence of their industrial systems, drive predictive insights, and foster a new era of cognitive industrial automation.