Exploring the Materials Behind Printed Circuit Boards
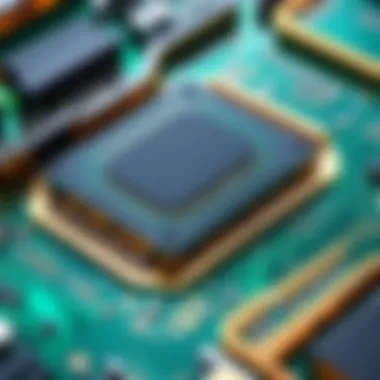

Intro
Printed circuit boards are made from an array of materials, each selected for its distinct properties. Understanding these characteristics can make a noticeable difference in how devices operate. Just like a chef curates ingredients for a signature dish, engineers choose their materials to enhance the functionality of electronics.
Key Points of Discussion
- Primary materials in PCB construction
- Variations in manufacturing processes
- The impact of material choices on performance and reliability
Before we delve deeper, let's clarify what exactly constitutes a printed circuit board.
Prelude to Printed Circuit Boards
Printed circuit boards (PCBs) are at the very core of modern electronics, acting as the backbone that holds various components together and facilitates their connection. As we delve into the topic of PCBs, it’s crucial to ponder the vast implications these rather unassuming boards carry. They are not just pieces of material; they represent a fine balance of engineering, materials science, and design that come together in a seamless manner.
PCBs form the fundamental basis for a myriad of devices, from everyday gadgets like smartphones and microwaves to complex machinery in aerospace and military applications. Understanding their composition is more than an academic exercise; it offers tech professionals and enthusiasts a comprehensive insight into how devices function at a basic level. With sophisticated electronic systems becoming commonplace, the need to grasp how these systems are constructed becomes ever more relevant.
Definition of PCBs
A printed circuit board is essentially a thin board made of insulating material, onto which conductive pathways are etched or printed. These paths create the necessary connections between different electronic components that are mounted on the surface. While the basic idea behind a PCB may seem straightforward, several variants exist, each tailored for specific applications and performance criteria. From single-sided to multi-layer boards, understanding the definition goes beyond mere terminology; it encompasses a whole ecosystem of functionality, reliability, and innovation.
Role of PCBs in Electronics
Without printed circuit boards, the landscape of electronics as we know it would be vastly different. They act as a highway that allows electrons to travel, ensuring signals are transmitted accurately within devices. The roles they play include:
- Signal Distribution: Connects various components, ensuring the smooth flow of information.
- Support Mechanism: Provides structural support for mounting parts like resistors, capacitors, and integrated circuits.
- Thermal Management: Helps dissipate heat generated by components, thereby enhancing durability and efficiency.
- Electrical Insulation: Keeps conductive pathways separate to prevent short-circuiting.
A PCB is not just a passive platform; it actively influences the overall functionality and efficiency of electronic devices.
PCBs are essentially the unsung heroes of technological progress. Their critical nature cannot be overstated. As technology continues to evolve with ever more complex circuitry and compact designs, the understanding of PCBs becomes vital for those engaged in electronics, whether they be professionals or hobbyists.
Basic Materials in PCB Construction
Printed Circuit Boards, or PCBs, are at the heart of nearly all electronic devices, acting as the backbone that allows different components to connect and communicate. Understanding the basic materials used in PCB construction is crucial for anyone involved in electronics, whether they're manufacturing, designing, or simply using the products. The materials selected influence not just the board's durability but also its performance and efficiency. Let's dive into the materials that make up this essential technology.
Substrate Materials
Substrate materials provide the foundational layer of a PCB, ensuring structural integrity and electrical insulation. Three common substrate materials are FR-4, CEM-1, and PTFE.
FR-4
FR-4 is perhaps the most widely utilized substrate material in PCB manufacturing. Its primary characteristic is its excellent electrical insulation and thermal stability. This glass-reinforced epoxy laminate forms a sturdy base that can withstand heat, making it suitable for a variety of applications.
Advantages:
- It balances cost-effectiveness with performance, making it a popular choice.
- FR-4 can be used in high-speed applications due to its low dielectric constant.
Disadvantages:
- Under extreme conditions, it may lose some mechanical properties over time. However, for most standard applications, its durability makes it a reliable pick for designers.
CEM-1
The CEM-1 material is another choice for lower-cost applications where performance requirements are less demanding. It consists of a paper substrate combined with a resin, which contributes to its lightweight and affordable nature.
Advantages:
- Its low cost makes it attractive for manufacturers looking to produce electronic devices in bulk.
- It is relatively easy to fabricate, which can speed up the manufacturing process.
Disadvantages:
- While effective for basic PCB designs, it falls short in more rigorous environments, particularly in terms of thermal and moisture resistance, compared to FR-4.
PTFE
PTFE, short for Polytetrafluoroethylene, is a specialized substrate that stands out for its exceptional thermal stability and unique low dielectric loss. It's often the go-to choice for high-frequency applications.
Advantages:
- PTFE offers superior performance in high-frequency scenarios such as RF applications.
- Its chemical resistance is remarkable, making it appropriate for certain harsh environments.
Disadvantages:
- The cost of PTFE can be prohibitive, making it less attractive for standard applications that do not demand its unique characteristics.
Conductive Materials
Conductive materials are integral to PCBs as they facilitate electrical connections. The three primary conductive materials include Copper, Gold, and Silver, each possessing unique properties and applications.
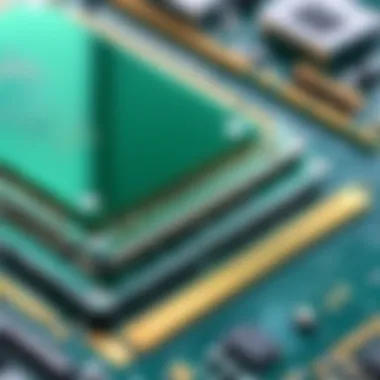
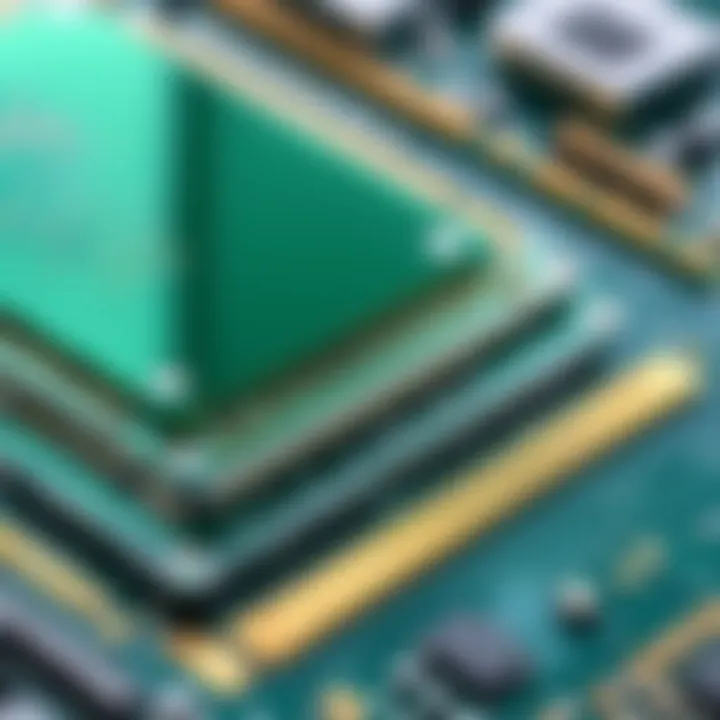
Copper
Copper is the undisputed king of conductive materials in PCB design due to its excellent thermal and electrical conductivity. It is commonly employed in circuits, pads, and traces throughout PCBs.
Advantages:
- Highly conductive and widely available, contributing to lower manufacturing costs.
- The versatility of copper allows it to be used in virtually all types of PCBs.
Disadvantages:
- Copper is prone to oxidation, which can impact performance over time if not properly treated.
Gold
Often associated with high-end applications, Gold is used primarily in electroplated surfaces on PCBs, particularly in areas requiring reliable connections.
Advantages:
- Gold provides superior corrosion resistance and maintains its conductivity over time, which is vital for ensuring long-term reliability in critical applications.
- It is used in connectors, edge fingers, and parts of the board requiring high reliability.
Disadvantages:
- The high cost of gold limits its use mainly to premium applications, often making it impractical for consumer electronics.
Silver
Silver also features as a conductive material in PCBs. While it possesses excellent electrical properties, its use in PCBs is nuanced.
Advantages:
- Silver has the highest conductivity of all metals, providing optimal performance in specialized applications.
- Used in conductive inks and can be utilized in high-frequency circuits.
Disadvantages:
- Its tendency to tarnish when exposed to air can lead to issues over time, making it potentially less reliable compared to other materials like gold.
Solder Mask and Silkscreen Layers
Lastly, we have the solder mask and silkscreen layers vital for protecting the PCB surface and providing necessary markings. The solder mask layer prevents unintended soldering and helps safeguard against moisture and dirt. The silkscreen layer provides visual identifiers, making it easier to understand what is what on the board. Both play synergistic roles in ensuring the functionality and longevity of PCBs.
In summary, each material plays a significant role in the overall performance, reliability, and cost of PCBs. Understanding these materials better empowers designers and manufacturers to make informed choices tailored to their specific needs.
The Role of Substrates in PCB Performance
Printed Circuit Boards (PCBs) are the backbone of electronic devices, enabling complex circuit designs to function effectively. An often overlooked but critical component of a PCB is its substrate. The substrate serves as the foundation that supports all other elements of the PCB, influencing both its durability and functionality. Recognizing the role of substrates is crucial for anyone working in electronics or related fields, as it ensures that the design of PCBs meets the necessary performance metrics.
Importance of Dielectric Properties
The dielectric properties of a substrate are paramount for maintaining signal integrity. Dielectric materials do more than just physically support conductive components; they also dictate the electrical characteristics of the board. A substrate with appropriate dielectric constant minimizes signal loss and maintains high-speed data transmission.
When selecting substrate materials, one must consider the dielectric constant—lower constants are preferable for high-frequency applications. For instance, FR-4 is popular for general usage due to its balanced properties, but in high-frequency situations, materials like PTFE are more favorable because of their superior dielectric qualities, which can prevent crosstalk and allow for better impedance matching.
Key Factors:
- Dielectric Constant: The capability of a substrate to store electrical energy.
- Dissipation Factor: Influences the efficiency of signal transmission.
- Frequency Response: How well the substrate performs at various signal frequencies.
Understanding these properties ensures that PCBs designed for high-frequency applications do not suffer from excessive signal degradation.
Thermal Properties
Thermal management is another crucial avenue where substrates shine, or sometimes fail. Substrates must dissipate heat effectively to prolong the lifespan of the circuit and ensure reliable operation. Materials with excellent thermal conductivity are vital in designs that require efficient heat dissipation.
For example, materials like metal-core PCBs provide superior thermal management compared to traditional FR-4 substrates. In high-power applications, such as LED drivers or power conversion circuits, using substrates with high thermal conductivity helps to manage excess heat, preventing failures due to thermal stress.
Considerations in Thermal Management:
- Thermal Conductivity: Ability of a material to conduct heat away from components.
- Coefficient of Thermal Expansion (CTE): Changes in material size with temperature fluctuations can lead to mechanical failures if not aligned with component CTEs.
- Thermal Stability: Ability to maintain performance under elevated temperatures.
In sum, the role of substrates goes beyond mere support; they are integral to the performance and reliability of PCBs. The interplay between dielectric and thermal properties substantially affects how well a PCB can serve in various applications, from consumer electronics to critical communication devices. Understanding these factors allows designers to optimize PCBs for specific tasks, making informed choices about materials to ensure longevity and functionality.
The substrate not only supports, it defines the PCB's performance architecture.
Various Types of Copper in PCBs
Copper serves as the lifeblood of printed circuit boards (PCBs), acting as the primary conductive material that enables the flow of electricity throughout the board. The characteristics and variations of copper used in PCBs can markedly affect the performance, reliability, and cost of the final product. Thus, understanding the different types of copper is not just an academic exercise; it is a critical component for anyone invested in PCB design and manufacturing.
The two main types of copper discussed here, electrolytic copper and oxygen-free copper, offer distinct benefits and considerations that can be decisive based on the intended application of the PCB. Knowing when to employ each type can enhance the effectiveness of electronic circuits and devices.
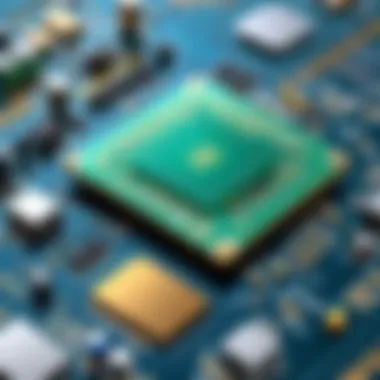
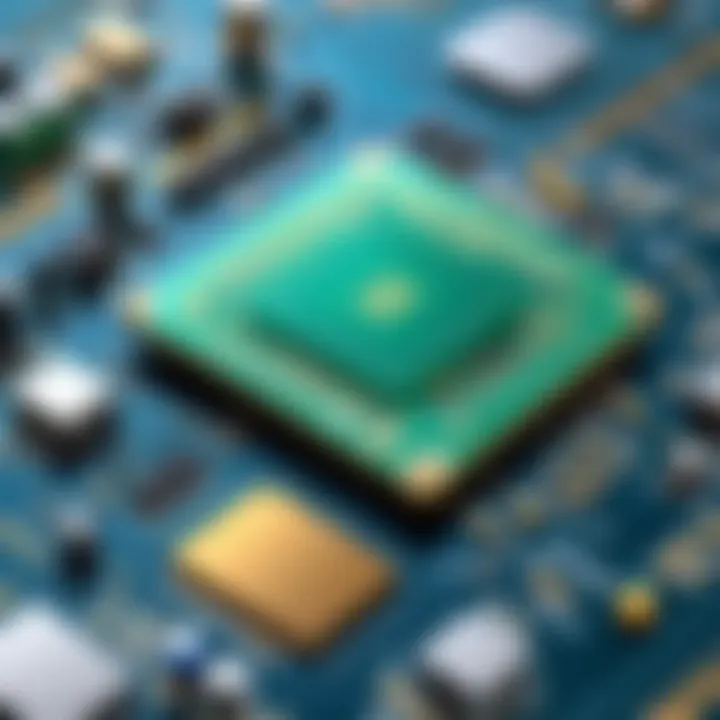
Electrolytic Copper
Electrolytic copper is widely utilized in PCB manufacturing due to its excellent electrical conductivity and its relatively low cost. This type of copper is produced via an electrolytic process which purifies copper to achieve a high level of conductivity, often around 99.99% pure.
The benefits of this copper type include:
- High electrical conductivity: It ensures efficient current flow, making it suitable for a range of applications from consumer electronics to industrial devices.
- Cost-effectiveness: Its production method allows for scalability and reductions in cost, which can be crucial when working on projects with tight budgets.
- Availability: Electrolytic copper can be found readily in the market, making it easier for manufacturers to procure.
However, electrolytic copper also has some limitations:
- Thermal elongation: It can expand when heated, which might lead to mechanical stress in high-temperature environments.
- Oxidation issues: If not treated properly, electrolytic copper can oxidize, which can impact the connections on PCBs and lead to failures.
Oxygen-Free Copper
In contrast to electrolytic copper, oxygen-free copper is specifically refined to eliminate oxygen impurities. This purity result is crucial, particularly in high-end electronic applications such as aerospace and military industries. The absence of oxygen enhances thermal and electrical conductivity while reducing the likelihood of oxidation, which can be detrimental to circuit integrity.
Key considerations for oxygen-free copper include:
- Superior conductivity: It outperforms many other conductive materials under high power conditions, providing consistent performance in demanding applications.
- Reduced junction resistance: This makes it particularly suitable for high-frequency applications where minimizing loss is imperative.
- Longevity: Oxygen-free copper exhibits high resistance to thermal and mechanical fatigue, extending the operational life of PCBs.
However, there are also trade-offs:
- Higher cost: The production process is more complex and typically results in higher prices than electrolytic copper.
- Limited availability: It may not be as readily available as other copper types, which can affect project timelines if sourcing is an issue.
Choosing between electrolytic and oxygen-free copper involves a careful assessment of the specific needs of the project, including performance requirements and budget constraints. An informed decision can greatly enhance the functionality and reliability of electronic designs.
"Understanding the properties of copper is just as crucial as the PCB design itself. It's the heart of electronic connectivity."
In the landscape of PCB materials, the type of copper one chooses can significantly impact overall quality, durability, and efficiency. Being equipped with this knowledge empowers IT professionals, cybersecurity experts, and students alike to make intelligent decisions in their quest for superior electronic performance.
Surface Treatments for Enhanced Performance
Surface treatments play a crucial role in the function and longevity of printed circuit boards (PCBs). These methods enhance the physical and chemical properties of the conductive surfaces, thus directly impacting performance qualities like durability, corrosion resistance, and solderability. With modern electronic demands becoming more complex and stringent, understanding these treatments is essential for anyone involved in PCB design and manufacturing.
Immersion Gold
Immersion gold is one of the most common surface finishes used for PCBs, particularly for components where reliability is critical. The process involves immersing the PCB in a gold-containing solution, depositing a thin layer of gold over the copper traces. This layer acts as a protective barrier, preventing oxidation and extending the lifespan of the PCB.
Benefits of Immersion Gold:
- Corrosion Resistance: Gold does not tarnish or oxidize easily, making it an ideal choice for environments susceptible to moisture.
- Solderability: The presence of gold on the pads enhances soldering performance, ensuring a reliable connection for electronic components.
- Flat Surface: The smooth surface created by immersion gold allows for precise contact when soldering components, which is vital in densely packed PCB designs.
However, it’s not without its considerations. The cost of gold can be high, leading designers to weigh the benefits against the budget constraints. In general, immersion gold is favored when high performance and reliability are non-negotiable factors.
Nickel-Au and HASL
Nickel-Gold (Ni-Au) and Hot Air Solder Leveling (HASL) are two additional surface treatments that serve distinct purposes and are suited for different applications.
Nickel-Au Treatment:
This method involves plating a nickel layer before gold is applied, combining the beneficial features of both metals. Nickel provides a strong substrate that protects copper from tarnishing, while gold gives a reliable surface for soldering.
Advantages of Nickel-Au:
- Enhanced Durability: The nickel layer adds yet another level of protection against corrosion compared to immersion gold alone.
- Thermal Stability: This finish maintains strong connections even in temperature-sensitive situations, adding yet another layer of reliability.
HASL Treatment:
HASL is a more traditional surface finish that uses a solder coating to protect copper traces. The PCB is dipped in molten solder and then leveled off with hot air, leaving a thin layer of solder on the surfaces.
Attributes of HASL:
- Cost-effective: It’s one of the more economical surface finishes, making it popular for lower-cost PCBs.
- Sufficent solderability: It provides good solderability, although it may be less than preferred when compared to nickel-gold finishes.
In a fast-evolving electronic landscape, the choice of surface treatment must balance performance needs and cost constraints.
In summary, the selection of surface treatments is not merely about what’s available but should be a strategic decision influenced by the specific application and expected environmental factors. Whether opting for the robust protection of immersion gold or the economic advantages of HASL, understanding the implications of these choices helps craft PCBs that meet and exceed modern demands.
Comparative Analysis of PCB Materials
In the world of printed circuit boards (PCBs), material choice plays a pivotal role in determining overall performance, durability, and cost-efficiency. This section aims to shed light on the comparative analysis of different PCB materials, providing an understanding of their unique properties, advantages, and drawbacks. With the technology sector advancing at a rapid pace, having a keen insight into these elements becomes essential for IT professionals, cybersecurity experts, and students alike.
Cost Considerations
When it comes to manufacturing PCBs, cost considerations can’t be overlooked. Material expenses can vary significantly based on the chosen components, which poses an important question: how does one balance budget constraints with the quality of the final product?
For example, FR-4 is a widely used substrate known for its cost-effectiveness. However, while budget-friendly, it may not perform as well as higher-end materials like PTFE when it comes to applications requiring superior thermal management or high-frequency performance. As a result:
- Prioritizing low-cost materials might save money upfront but could lead to increased expenses down the line if failures occur.
- It’s crucial to consider the total lifecycle cost of the PCB. Investing in more expensive materials may yield better longevity and lower maintenance needs, ultimately saving money.
In essence, making a choice based solely on initial expense, without considering performance requirements, can lead companies down a slippery slope of more frequent repairs and replacements.
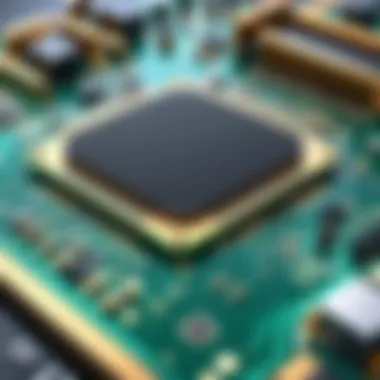
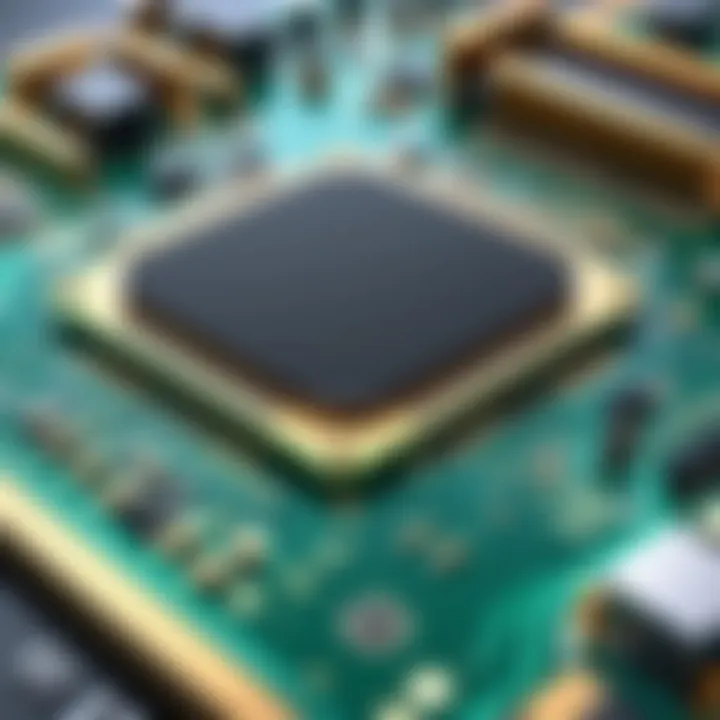
Performance Trade-offs
Performance trade-offs in PCB materials significantly impact how well a board will handle various operational stresses, including heat dissipation, signal integrity, and environmental factors. The interplay between material choice and performance becomes a balancing act that designers must execute adeptly.
When comparing materials, one must consider factors such as:
- Thermal conductivity: Higher thermal conductivity materials like copper or gold can provide better heat dissipation. Conversely, materials with lower thermal conductivity may lead to overheating.
- Mechanical integrity: While some materials may boast high thermal stability, they might compromise on strength. For instance, CEM-1 offers decent mechanical properties, but in situations requiring top-notch mechanical resilience, alternative materials could be more beneficial.
Moreover, let’s not ignore the frequency characteristics of various materials. For example, PTFE has excellent high-frequency performance, perfect for RF applications, but it's more expensive than its counterparts.
A prime example of these trade-offs could be:
- Choosing a gold finish for surface treatment enhances performance by minimizing signal loss. But the gold plating comes at a cost, which may be an uneconomical choice for projects with tight budgets.
"In PCB design, every material has its purpose, and understanding these trade-offs could be the difference between a successful product launch and a technical failure."
Impact of Material Selection on PCB Lifespan
The selection of materials for printed circuit boards (PCBs) can significantly influence their lifespan. This section will explore how the choice of materials affects both the durability and longevity of these critical components in electronic devices. It's important to understand that not all materials stand the test of time; some can degrade faster, particularly in challenging environments. By making informed choices about materials, manufacturers can increase reliability and minimize maintenance costs.
Environmental Resistance
When we talk about environmental resistance, we mean how well a PCB can withstand various external factors like heat, moisture, chemicals, and even physical stress. Materials such as FR-4, often used for the substrate, have established their worth here. FR-4 is a fiberglass-reinforced epoxy laminate that offers good thermal stability, but it can falter in environments with extreme humidity or corrosive substances.
The right coating or treatment can enhance a board's resistance to these factors. For instance, using conformal coatings helps protect the PCB from moisture and dust. These coatings can be silicone-based or polyurethane-based, each offering different levels of resistance, depending on the application. The aim is to ensure that even in hostile environments, the integrity and functionality of the PCB remain intact.
"Choosing the right materials isn’t just about performance; it’s about longevity."
Moreover, certain materials can be engineered to resist higher temperatures. In situations where a PCB might encounter heat (like in automotive or industrial applications), selecting materials with higher thermal ratings becomes crucial. This can prevent delamination and ensure that the physical properties maintain their reliability over time.
Mechanical Stability
Mechanical stability offers another layer of consideration regarding PCB lifespan. It entails how well a PCB can endure physical pressures, flexing, vibration, or shock. A significant part of this lies in the substrate material. High-quality substrates like polyimide provide excellent mechanical stability, making them suitable for applications that require flexibility, like in certain aerospace technologies.
In contrast, cheaper materials might crumble under stress, leading to circuit failure. It’s not just the substrate; the choice of copper thickness, solder types, and surface finishes can also impact mechanical durability. Conductive traces can weaken or break if subjected to stress beyond their design parameters. This is particularly relevant in mobile devices where drop impact is a design consideration.
Investing in superior materials might involve higher upfront costs, but over the lifespan of the PCB, it translates to fewer failures and lower replacement costs. It’s far wiser for a company to spend a bit more on materials that won't fail unexpectedly than to face the repercussions of a board that has a shortened lifespan due to material inadequacies.
By knowing the interactions of these materials with environmental and mechanical factors, manufacturers can make choices that not only improve performance but also extend the useful life of their products.
Future Trends in PCB Material Technologies
As we step into an era dominated by rapid technological advancements, the significance of staying abreast of emerging trends in printed circuit board (PCB) material technologies is paramount. This section endeavors to shed light on the innovative materials shaping the future of PCBs, with a focus on sustainability and performance. Understanding these trends not only helps in making informed decisions but also optimizes designs for upcoming applications.
Biodegradable Materials
In the age of mounting environmental concerns, biodegradable materials for PCBs are gaining traction. These materials offer an alternative that addresses the long-lasting impact traditional PCBs impose on landfills and ecosystems. Research has been pushing boundaries, exploring polymers and composites derived from renewable resources, like cellulose or polylactic acid (PLA).
Implementing biodegradable materials provides several benefits:
- Reduced Environment Impact: They decompose naturally after disposal, significantly lowering the long-term ecological footprint.
- Regulatory Advantages: Governments and organizations are increasingly mandating eco-friendly practices. Using biodegradable materials ensures compliance with future regulations that aim to reduce electronic waste.
- Market Differentiation: Companies can leverage sustainability as a selling point, appealing to environmentally conscious consumers.
Despite these advantages, challenges remain. There are considerations around production costs and ensuring the performance of these materials aligns with rigorous industry standards. However, ongoing innovations are addressing these hurdles, promising exciting developments in the near future.
Nanotechnology in Electronics
Another frontier that is shaping the landscape of PCB material technologies is nanotechnology. Using nanoscale materials can enhance the performance of PCBs in various significant ways. For instance, integrating nanomaterials can improve the thermal and electrical conductivity significantly.
Benefits of nanotechnology in PCBs include:
- Enhanced Performance: Nanomaterials like carbon nanotubes can result in faster signal transmission and reduced loss, which are critical for high-speed applications.
- Miniaturization: The ability to fabricate components at the nanoscale opens avenues for creating smaller, lighter, and more complex devices, a growing demand in the industry.
- Improved Durability: Nanotechnology also promises increased robustness against environmental factors, extending the lifespan of PCBs under challenging conditions.
Nonetheless, while the potential is vast, practical applications are still in their infancy. Ongoing research aims to tackle the challenges surrounding manufacturing scalability and cost-effectiveness.
"The future of PCB technologies may very well hinge on our ability to merge innovation with sustainability."
The End
The exploration into the world of printed circuit boards, encapsulated in this article, underscores the vital relationship between materials and performance. Every aspect discussed, from substrates to treatments, showcases how material choice can either enhance or limit functionality in the realm of electronics. Understanding these intricacies not only provides clear directions for designing more efficient and durable PCBs but also echoes the significance of remaining updated with current trends and innovations.
Summary of Key Insights
In reviewing the key insights from our discussion, several vital points emerge:
- Diverse Materials: A myriad of materials affects the performance and reliability of PCBs. The choice between FR-4, CEM-1, or specialized materials can lead to vastly different outcomes in heat resistance and longevity.
- Copper's Role: Copper remains a cornerstone in PCB construction. The variations in types, like electrolytic and oxygen-free copper, significantly influence conductivity and overall performance.
- Surface Treatments: Surface treatments like immersion gold and HASL cater to specific needs, affecting solderability and durability. These can also extend the life of a PCB by protecting against environmental factors.
- Performance vs. Cost: Finding the sweet spot between cost and performance is a recurring theme. Manufacturers have to balance budget constraints with the desire for a high-quality end product, which is no simple task.
Being aware of these insights can empower IT professionals and enthusiasts alike, leading to better decision-making in PCB design and manufacturing.
The Importance of Material Knowledge in PCB Design
In the ever-evolving landscape of technology, the importance of material knowledge cannot be overstated. An understanding of each component's characteristics allows designers to tailor PCBs for specific applications, ensuring optimal performance in diverse environments. This acumen can foster innovation as professionals explore new materials, such as biodegradable options or advancements through nanotechnology.
Moreover, recognizing the impact of environmental resistance and mechanical stability on a board's lifespan can lead to more sustainable practices within the industry. Knowledge of materials helps in mitigating potential risks while maximizing efficiency, a key consideration in sectors like IT, cybersecurity, and beyond.
Ultimately, an informed approach to material selection not only enhances the immediate utility of printed circuit boards but lays the groundwork for future advancements in electronics. By integrating this knowledge into PCB design, professionals can forge a path toward more resilient and environmentally responsible technological solutions.