Exploring MEMS Sensor Types: A Comprehensive Overview
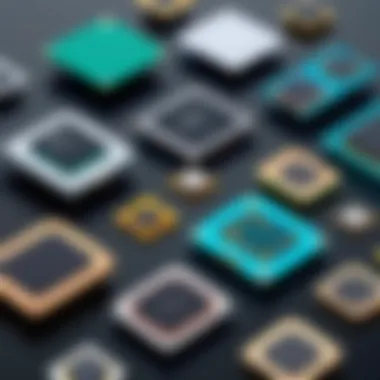
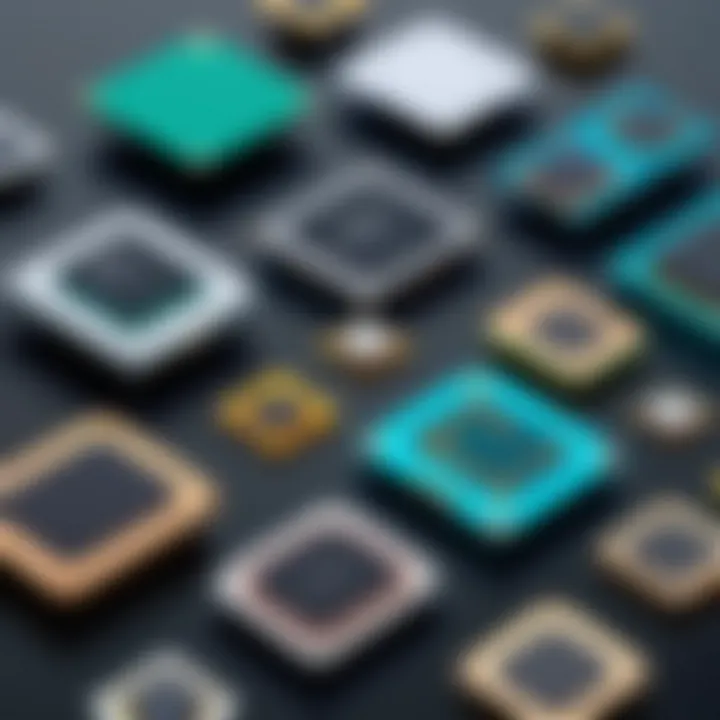
Intro
Micro-Electro-Mechanical Systems, commonly referred to as MEMS, represent a convergence of mechanics, electronics, and embedded systems. They have become indispensable in today’s technological landscape, facilitating advanced applications across diverse industries. This article aims to provide a detailed examination of different MEMS sensor types, their operational principles, classifications, and real-world applications.
As technology evolves, MEMS sensors are at the forefront of innovation, enabling capabilities that were previously unimaginable. Understanding these sensors is crucial not only for professionals in tech-centered fields but also for individuals interested in the pervasive role of technology in everyday life. From automotive safety to mobile device functionality, MEMS sensors are integral to performance and reliability.
In the following sections, we will dissect the primary types of MEMS sensors, including accelerometers, gyroscopes, and pressure sensors, among others. Additionally, we will explore their fundamental working principles, categorize them based on various criteria, and scrutinize the latest trends driving their development.
Understanding MEMS Sensors
Understanding Micro-Electro-Mechanical Systems (MEMS) sensors is essential for grasping their wide-ranging impact in various fields. These small devices convert physical phenomena into electrical signals, facilitating real-time and precise data collection. This capability is crucial in applications from consumer electronics to healthcare and aerospace. The growing reliance on MEMS technology in everyday devices signifies their importance. By studying MEMS sensors, one can appreciate their contribution to innovation and efficiency.
Definition and Mechanism
MEMS sensors are tiny devices that integrate mechanical and electrical components on a single microchip. This integration allows them to sense physical changes like motion, pressure, and temperature and convert these changes into electrical signals. The working mechanism of a MEMS sensor typically involves detecting variations in physical forces or changes in an environment. For example, a MEMS accelerometer detects changes in velocity and orientation, while a MEMS pressure sensor measures pressure variations within a fluid.
Most MEMS sensors operate based on resonant structures or capacitive principles. When an external force is applied, these structures respond with a measurable electrical output. The precision of these sensors comes from their micro-scale dimensions, which enable them to capture very slight changes in their environment.
Historical Background
The origins of MEMS technology can be traced back to the 1960s when researchers first began experimenting with microfabrication techniques. The development of silicon-based technologies, combined with advances in materials science and miniaturization, set the stage for the rise of MEMS sensors in the late 20th century. The first commercial MEMS products appeared in the 1980s, primarily in automotive applications, such as tire pressure monitoring systems.
Since then, MEMS technology has evolved, driven by the demand for smaller, more efficient devices. By the early 2000s, MEMS sensors had found applications in consumer electronics, most notably in smartphones and wearable devices. Today, MEMS sensors play a vital role in numerous sectors, including healthcare, environmental monitoring, and aerospace. Their historical development highlights the interplay between technological advancements and market needs, which continues to drive innovation in this field.
Types of MEMS Sensors
Understanding the different types of MEMS sensors is crucial for several reasons. First, this categorization helps in identifying the right sensor for a specific application. Each type of MEMS sensor has unique operational principles and specializations. By exploring these variations, technologists and engineers can maximize efficiency in their projects. Furthermore, as industries continue to evolve, the demand for specialized sensors increases. This means understanding these types becomes even more relevant for researchers and practitioners alike.
Accelerometers
Operational Principles
Accelerometers function by measuring the acceleration forces acting on them. This enables the detection of changes in motion or orientation. The main operational principle involves the use of a proof mass suspended on springs. As the device experiences acceleration, the proof mass shifts. This shift is converted into an electrical signal that indicates the rate of acceleration. The compactness and efficiency of accelerometers make them a preferred choice in many applications. Their lightweight nature allows for easy integration into various systems, but they can be sensitive to noise, impacting measurement accuracy.
Applications in Consumer Electronics
Accelerometers play a significant role in consumer electronics. Smartphones, tablets, and gaming devices utilize these sensors to enhance user experience. They enable features like automatic screen rotation and motion-based gaming controls. The key characteristic here is their versatility and responsiveness, which are essential for interactive devices. However, their reliance on mechanical components can lead to wear over time, somewhat limiting their lifespan. Despite this, the benefits they provide in everyday devices justify their widespread use.
Industrial Use Cases
In industrial settings, accelerometers are crucial for monitoring machinery and detecting vibrations. They help in predictive maintenance, allowing companies to anticipate issues before they become critical. The key feature is the ability to operate in harsh environments without compromising performance. This robustness is vital for industries where downtime can lead to significant losses. However, the challenge lies in the calibration process, which can be time-consuming and requires specialized knowledge.
Gyroscopes
Types of Gyroscopes
Gyroscopes are integral in maintaining orientation and angular velocity. They operate on principles of angular momentum and can be categorized into two major types: mechanical and MEMS gyroscopes. MEMS gyroscopes derive their advantages from the miniaturization and integration features typical of MEMS technology. These sensors are lightweight, consume less power, and offer high sensitivity. However, they can be influenced by temperature changes, which might affect accuracy.
Role in Navigation Systems
Gyroscopes are essential for navigation systems in both aerospace and automotive sectors. They provide stability and precise orientation information, aiding in path tracking and maneuvering. The characteristic advantage of gyroscopes in navigation is their ability to function independently of external references. This makes them reliable for applications where GPS signals may be weak or unavailable. Nevertheless, the potential drift in measurements over time necessitates regular recalibration to maintain accuracy.
Integration with Other Sensors
Integrating gyroscopes with other sensors, such as accelerometers, creates advanced sensing systems. This combination allows for improved motion tracking and environmental interaction. The synergy enhances data accuracy, providing a more comprehensive understanding of movements. A notable aspect of this integration is the ability to perform sensor fusion, which combines data for more reliable outputs. However, managing data from several sensors can complicate system design and performance, requiring meticulous programming and calibration.
Pressure Sensors
Types of Pressure Sensors
Pressure sensors are vital for measuring fluid or gas pressure in various applications. They can be classified primarily into capacitive, piezoresistive, and optical types. Each type has unique mechanisms that offer specific advantages. For example, capacitive pressure sensors are known for their high accuracy and long-term stability. The versatility of pressure sensors allows them to be used in multiple sectors, but they might face challenges in extreme environments.
Use in Automotive Applications
The automotive industry heavily relies on pressure sensors for multiple functions, including tire pressure monitoring and engine management systems. The main contribution of pressure sensors in automotive applications is safety. By providing real-time data, they enhance system performance and vehicle safety. Their ability to withstand high temperatures and vibrations is crucial for reliable operation in such settings. However, sensor degradation over time can lead to performance issues, which necessitates periodic maintenance.
Healthcare Monitoring
In healthcare, pressure sensors are used in various devices like blood pressure monitors and respiratory systems. They offer precise measurements essential for accurate diagnostics and treatment monitoring. The characteristic nature of healthcare applications is their requirement for high reliability and accuracy. Pressure sensors can easily meet these needs, making them invaluable in clinical settings. However, there can be challenges associated with sensor calibration, which must be managed to ensure consistent performance in medical devices.
Microphones
How MEMS Microphones Work
MEMS microphones operate on principles similar to traditional microphones but in a miniaturized form. They convert sound waves into electrical signals. The key aspect of MEMS microphones is their small size and ability to handle a wide frequency range. These features allow for compact designs in advanced audio technologies. MEMS microphones are beneficial in applications where space is a premium, yet they can exhibit issues with sensitivity in noisy environments.
Applications in Audio Devices
MEMS microphones are widely used in various audio devices, including smartphones and hearing aids. Their small footprint and cost-effectiveness make them popular in consumer electronics. The primary advantage is the ability to offer high performance in a small package. However, market demands for even better audio quality continue to push the limits of current technologies.
Future Trends
The future trends for MEMS microphones indicate advancements in sensitivity and noise cancellation features. Enhancements in fabrication techniques are also on the horizon. These developments aim to improve sound quality in increasingly compact designs. The focus on integrating these microphones with AI technologies is another area of interest. Although the growing complexity can pose challenges in design and production, the benefits of improved audio experiences are clear.
Chemical Sensors
Detection Mechanisms
Chemical sensors detect specific substances and play a crucial role in environmental and health applications. They function by evaluating the interaction between target chemicals and sensing materials. The significance of detection mechanisms lies in their specificity and sensitivity towards various analytes. MEMS chemical sensors offer improvements in size and power consumption compared to traditional counterparts. However, the need for calibration can present challenges in certain environments.
Applications in Environmental Monitoring
In environmental monitoring, chemical sensors are critical for detecting pollutants and hazardous substances. These sensors provide essential data for air and water quality assessments. The key characteristic of their applications is their ability to offer real-time monitoring, enabling quick responses to environmental threats. However, their deployment can be limited by factors such as response time and environmental conditions.
Implications for Public Health
Chemical sensors have significant implications for public health by detecting toxic substances in various settings. They contribute to ensuring safety standards in workplaces and homes. The primary advantage is their capability to provide immediate information regarding potential hazards. However, limitations exist in terms of calibration accuracy and the availability of reference materials for effective monitoring.
Understanding these various types of MEMS sensors not only aids in the selection of appropriate technologies but also fosters innovation across numerous fields. Their unique operational principles and applications highlight the dynamic nature of the MEMS sensor market.
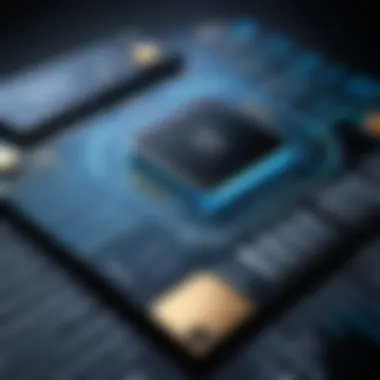
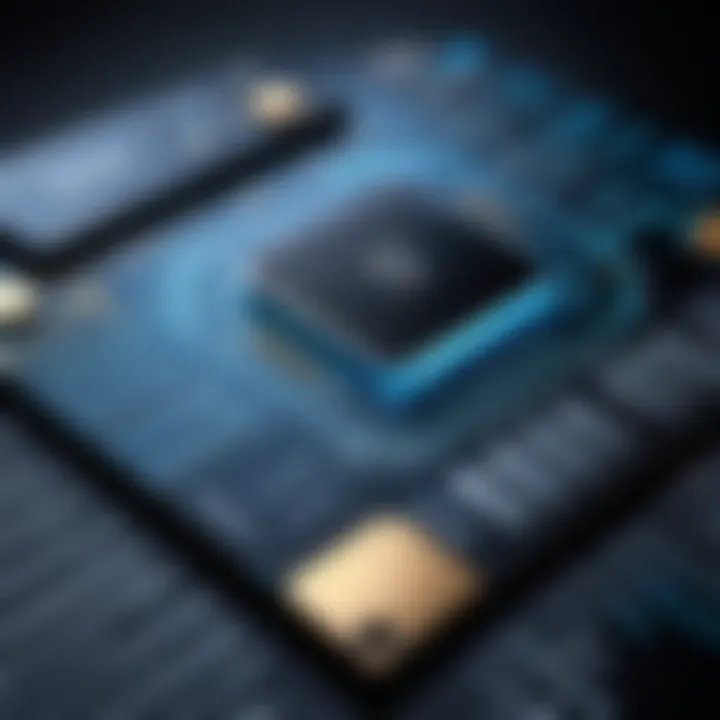
Integration of MEMS Sensors
The integration of MEMS sensors plays a crucial role in enhancing the functionality and performance of various systems. This integration ensures that these tiny devices can work seamlessly within larger technological frameworks. MEMS sensors convert physical phenomena into electronic signals and are increasingly used in diverse areas. Properly integrating these sensors can lead to improved accuracy, efficiency, and overall system effectiveness.
System Integration
Challenges in Integration
Integrating MEMS sensors within existing systems presents a range of challenges. One significant aspect of these challenges is the miniaturization of components while maintaining performance. This complexity arises because MEMS sensors often require specific conditions to function optimally. Interfacing them with larger systems can lead to compatibility issues.
Key characteristics of these challenges include managing signal distortion and ensuring reliable power consumption. These factors are especially crucial as they dictate how effectively MEMS sensors can perform in integrated applications.
Despite the difficulties, tackling these challenges can be a beneficial choice for achieving enhanced performance. This is very relevant in high-tech sectors such as automotive and healthcare. The advantages include better accuracy and responsiveness, which are vital in critical applications.
Innovative Solutions
Innovations in technology offer solutions to tackle integration challenges effectively. Techniques such as system-on-chip (SoC) designs are becoming popular in developing integrated MEMS systems. This characteristic allows multiple components to share resources, thereby reducing the layout space required.
A unique feature of these innovative solutions is their ability to streamline production and reduce costs. This makes it easier for companies to implement MEMS sensors into their product lines. The benefits are clear: companies can provide more sophisticated features in smaller packages, enhancing the competitive edge. However, there are some limitations, such as potential increases in design complexity and costs during the initial phases.
Examples of Integrated Systems
Numerous examples illustrate successful integration of MEMS sensors into various systems. One notable instance is the use of MEMS accelerometers in smartphones. These sensors provide essential functionality for user interfaces, impacting how users interact with their devices.
A critical characteristic of these examples is their ability to enhance user experience. The integration of MEMS sensors allows for functionalities like screen rotation and gaming controls. The advantage of this integration lies in its ease of use and improved interfacing.
Yet, there are disadvantages, such as potential vulnerabilities related to crowded chip designs, impacting reliability over time.
Interfacing with Digital Systems
Common Interfaces
The ability to interface MEMS sensors with digital systems relies on several common interfaces. Protocols like I2C and SPI are frequently used in these contexts. Such interfaces allow for effective communication between sensors and microcontrollers, which is key for data acquisition and processing.
The defining characteristic of these common interfaces is their capacity for supporting various data transfer rates. Opting for these protocols is beneficial, particularly in systems that demand real-time monitoring or control. Their flexibility enhances the overall functionality of MEMS sensors in digital ecosystems. However, their implementation can be complicated, necessitating thorough understanding from design engineers.
Signal Processing Techniques
Efficient signal processing techniques are essential for maximizing the potential of MEMS sensors. These techniques involve filtering, amplification, and digitization processes to enhance sensor data quality. A key characteristic is the ability to mitigate noise, which is crucial for applications demanding high precision.
Advantages of employing advanced signal processing techniques include improved measurement accuracy and increased reliability of outputs. Nevertheless, this could come at the cost of added complexity in processing resources, potentially leading to longer development cycles.
Data Transmission Protocols
Data transmission protocols form an integral part of MEMS sensor systems. Protocols such as UART and RS-232 are commonly utilized to transmit processed data to various applications. The main characteristic of these protocols lies in their established reliability and ease of implementation.
This choice is advantageous, especially in industrial applications, where robust data transmission is critical. However, limitations exist, such as the potential for lower data rates compared to newer standards like TCP/IP, which may influence overall system performance.
In summary, the integration of MEMS sensors is a multifaceted process that involves addressing various challenges while leveraging innovative solutions to improve functionality. Understanding these processes is essential for anyone invested in the future of MEMS technology.
Applications of MEMS Sensors
The applications of MEMS sensors represent a critical dimension of their functionality. This section highlights the many ways MEMS sensors integrate into various sectors. Their roles in improving efficiency, accuracy, and convenience cannot be overstated. In particular, these sensors enable innovative solutions in consumer electronics, transportation, healthcare, and aerospace, shaping modern technology.
Consumer Electronics
Smartphones and Tablets
Smartphones and tablets utilize MEMS sensors to enhance user experience. The integration of accelerometers and gyroscopes allows for features such as screen rotation and motion sensing. These sensors support efficient navigation in applications, making the devices not just functional but also intuitive to use. The flexibility they offer in design is a notable aspect.
Key Characteristics: MEMS sensors in smartphones and tablets are small and lightweight, adding minimal bulk to devices.
Advantages:
- Increased functionality
- Improved user interaction
Disadvantages:
- Potential sensitivity to shock or damage
Wearable Technology
Wearable technology, such as fitness trackers and smartwatches, greatly benefits from MEMS sensors. These sensors monitor physical activities and health metrics like heart rate and movement. They contribute significantly to the growing trend of health awareness and fitness regimes. The real-time data gathered is crucial for users looking to enhance their lifestyles.
Key Characteristics: Wearable technology often incorporates MEMS sensors for precise motion tracking.
Advantages:
- Continuous monitoring capabilities
- Enhanced user engagement
Disadvantages:
- Limited battery life due to constant usage
Smart Home Devices
Smart home devices represent another significant area where MEMS sensors are applied. These devices use sensors to monitor environmental conditions and user interactions. They enable automation and establish more efficient household management. For example, temperature sensors can intelligently regulate heating or cooling systems, enhancing comfort.
Key Characteristics: Smart home devices often incorporate multiple MEMS sensors for comprehensive data collection.
Advantages:
- Improved energy efficiency
- Increased convenience for users
Disadvantages:
- Lifecycle of individual components may vary
Automotive Sector
Safety Features
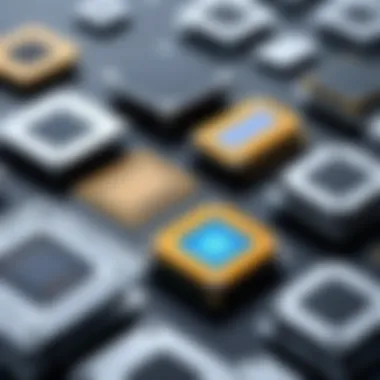
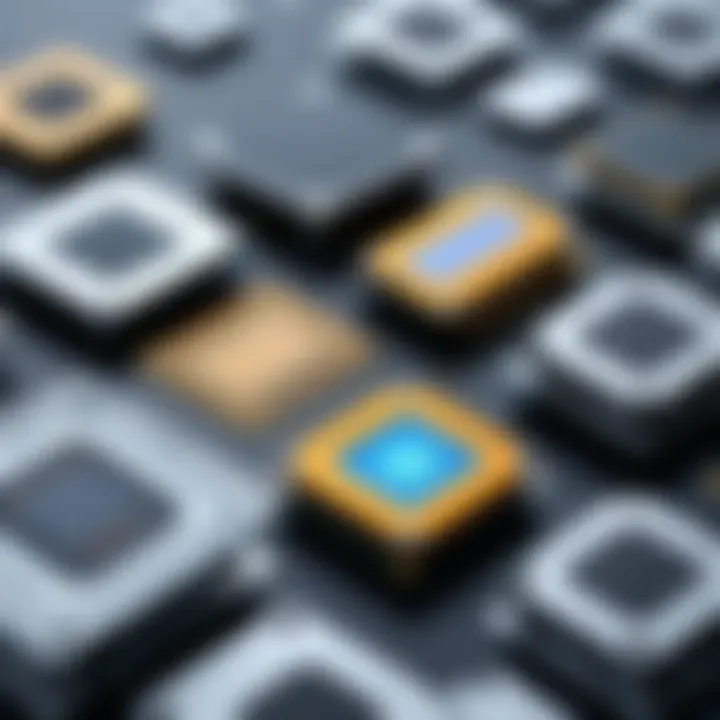
In the automotive sector, MEMS sensors play a vital role in enhancing safety features. These sensors include accelerometers and gyroscopes that aid in vehicle stability and control systems. They help in preventing accidents by providing timely data to safety systems such as airbags and electronic stability control.
Key Characteristics: Reliability and quick response to vehicle dynamics are crucial for safety mechanisms.
Advantages:
- Direct improvement in passenger safety
- Reduction of accident risks
Disadvantages:
- Dependency on sensor accuracy
Self-Driving Technology
Self-driving technology leverages MEMS sensors to navigate and understand surroundings. These sensors provide essential data for making real-time decisions. Their accuracy and responsiveness are crucial for creating reliable autonomous systems, paving the way for safer roads.
Key Characteristics: Integration of MEMS sensors ensures improved perception of environmental conditions.
Advantages:
- Enhanced automation capabilities
- Reduction in human error
Disadvantages:
- High complexity in system integration
Telematics
Telematics systems use MEMS sensors to track vehicle data, optimizing performance and safety. This application is essential for fleet management and personal vehicle monitoring. Sensors collect data on speed, location, and driving patterns to inform both users and companies, leading to better operational decisions.
Key Characteristics: Real-time data relay supports immediate feedback for users.
Advantages:
- Enhanced operational efficiency
- Improved safety standards
Disadvantages:
- Potential privacy concerns with data collection
Healthcare
Patient Monitoring Systems
Patient monitoring systems utilize MEMS sensors to track vital signs and conditions. They allow healthcare providers to remotely monitor patients, ensuring timely interventions. This application is vital in chronic disease management and post-operative care, promoting proactive health measures.
Key Characteristics: Continuous monitoring capabilities are essential for serious medical conditions.
Advantages:
- Improved patient outcomes through timely data
- Enhanced accessibility for patients
Disadvantages:
- Risk of inaccurate readings under specific conditions
Diagnostic Instruments
Diagnostic instruments increasingly rely on MEMS sensors for accurate measurements. These sensors help in detecting various conditions quickly, aiding in early diagnosis. Their integration into medical technology enhances reliability in lab environments.
Key Characteristics: Precision is key in diagnostic tools to avoid false positives.
Advantages:
- Enhanced accuracy in tests
- Improved speed of diagnostics
Disadvantages:
- Maintenance of instruments can be costly
Robotic Surgery Tools
Robotic surgery tools use MEMS sensors for enhanced precision and control. These tools benefit surgeons with higher accuracy during procedures, ensuring better outcomes. They allow for minimally invasive operations, reducing recovery times for patients.
Key Characteristics: The miniaturization of components plays a critical role in robotic systems.
Advantages:
- Reduction in patient trauma during surgeries
- Higher success rates in complex operations
Disadvantages:
- High costs associated with robotic systems
Aerospace and Defense
Navigation and Control Systems
In aerospace and defense, MEMS sensors are critical for navigation and control systems. They provide reliable data for position and orientation, essential for aircraft and spacecraft operation. These sensors support the stability and accuracy of navigation systems under various conditions.
Key Characteristics: Highly accurate sensors are vital for system reliability.
Advantages:
- Enhanced safety in navigation
- Increased operational efficiency
Disadvantages:
- Must cope with harsh environments influencing sensor performance
Remote Sensing Applications
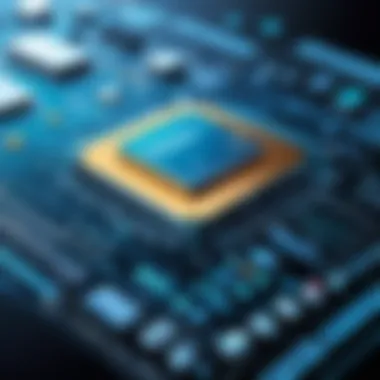
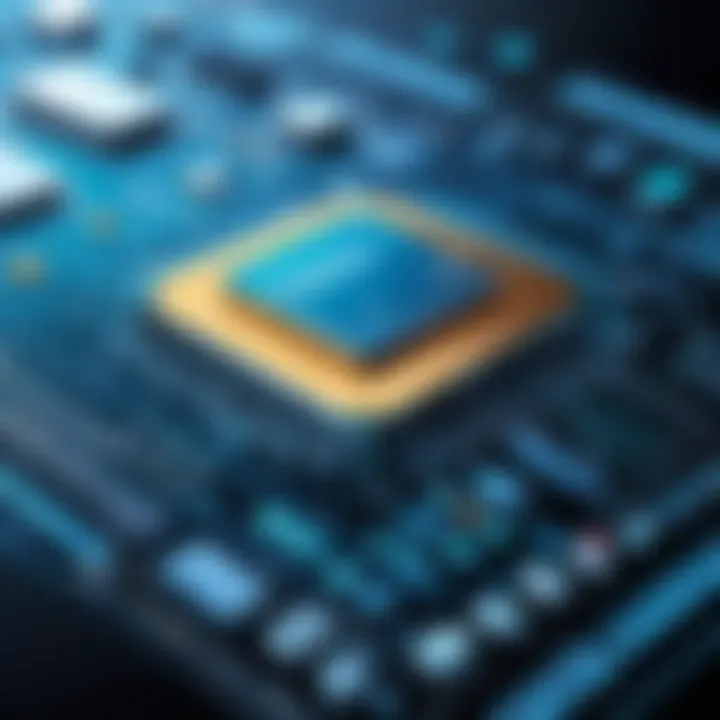
Remote sensing applications utilize MEMS sensors for environmental monitoring and data collection. These sensors gather information about weather, terrain, and atmospheric conditions, contributing to critical data for research and development.
Key Characteristics: Precision in data collection is essential for accurate analysis.
Advantages:
- Provides necessary data for scientific research
- Enhances public safety through environmental awareness
Disadvantages:
- Data interpretation can be complex
Material Monitoring
Material monitoring integrates MEMS sensors to ensure structural integrity in aerospace applications. They monitor conditions in real-time, ensuring that materials meet safety standards. This application is vital for both performance and safety in high-stakes environments.
Key Characteristics: Continuous monitoring allows for immediate response to changes in material conditions.
Advantages:
- Prevents catastrophic failures
- Enhances maintenance planning
Disadvantages:
- Higher initial installation costs
MEMS sensors are transforming industries by enhancing functionality and facilitating innovation.
Advantages and Limitations of MEMS Sensors
Understanding the advantages and limitations of MEMS sensors is crucial. These factors can significantly influence their application and effectiveness across various industries. The strengths of MEMS sensors often make them preferred choices for many tech applications. However, the limitations should not be overlooked as they can impact performance and reliability. Thus, evaluating both aspects offers a comprehensive view of their practical use.
Advantages
Size and Weight Benefits
The size and weight of MEMS sensors are defining characteristics. Their miniaturized design means they can be integrated into small devices. This compactness allows for innovative applications, especially in consumer electronics like smartphones and wearables. The reduced weight facilitates deployment in systems where weight is critical. For example, drones and portable medical devices benefit from lighter components. This can lead to improved portability and ease of use in everyday applications.
Cost-effectiveness
Cost-effectiveness is another notable advantage of MEMS sensors. They are often cheaper to manufacture compared to traditional sensors. The mass production capabilities reduce unit costs, making MEMS sensors attractive for large-scale implementations. For businesses looking to integrate sensors, this economic efficacy is a beneficial element. It allows for investment in additional functionalities without a significant budget increase. Consequently, more sectors can access advanced sensor technology, fostering innovation and competitiveness.
Energy Efficiency
Energy efficiency is a key aspect of MEMS sensors. Their design allows for low power consumption, which is crucial for battery-operated devices. This efficiency extends the lifespan of devices that rely on MEMS, such as wearables and IoT devices. By minimizing energy usage, manufacturers can promote sustainability while maintaining performance. The benefit of using less power often translates to reduced heat generation, ultimately enhancing the overall performance of electronic systems.
Limitations
Noise and Sensitivity Issues
Despite their many advantages, MEMS sensors face noise and sensitivity challenges. External factors like temperature and vibration can provoke noise, which may affect accuracy in readings. Sensitivity varies among different MEMS types, making some more susceptible to error than others. Awareness of these limitations is essential when implementing MEMS sensors in sensitive environments like healthcare or aerospace. Ensuring proper calibration is critical to mitigate these effects.
Calibration Challenges
Calibration of MEMS sensors is often complex and demanding. Variations in manufacturing can lead to discrepancies that necessitate individual adjustments for optimal performance. This can be resource-intensive and time-consuming. Systems relying on MEMS sensors need regular calibration to ensure they operate correctly, particularly in high-precision applications. Thus, designers must consider these calibration challenges during the integration of MEMS technology.
Durability Concerns
Durability is a notable concern with MEMS sensors. Being smaller also makes them more susceptible to physical damage from shocks or extreme conditions. The materials used in MEMS construction may not withstand harsh environments well without additional protection. This poses constraints in industries like automotive or aerospace where reliability is crucial. Therefore, evaluating the durability of MEMS sensors before application is essential.
"A thorough understanding of MEMS sensors' strengths and weaknesses is vital for informed decision-making in technology integration."
Future Trends in MEMS Sensor Technology
Future trends in MEMS sensor technology are vital for understanding how these devices will evolve and impact various industries. Their development is influenced by many elements including market demands, technological capabilities, and advancements in related fields. MEMS sensors play a key role in applications that desire precision, miniaturization, and energy efficiency. Keeping track of future trends will help professionals stay updated and informed in an increasingly competitive environment.
Emerging Technologies
Advancements in Fabrication Techniques
Advancements in fabrication techniques are significant because they enhance the quality and functionality of MEMS sensors. Improved methods such as micro-manufacturing, 3D printing and new lithography techniques contribute to creating sensors with better dimensions and performance. The key characteristic of these advancements is their ability to produce more complex structures while maintaining lower production costs.
A unique feature of these improved techniques is the potential for customization, allowing sensors to be tailored for specific applications. This can lead to enhanced performance in terms of accuracy and reliability. However, the high initial investment in these technologies can pose a challenge for smaller companies.
Integration with AI
Integration with artificial intelligence significantly enhances the utility of MEMS sensors. By combining AI with these sensors, data processing becomes more efficient and relevant insights can be realized more quickly. The key characteristic of this integration is the capacity for real-time data analysis, which is crucial in applications such as healthcare and autonomous vehicles.
A unique feature here is the ability of AI algorithms to improve the accuracy of data interpretation. While this integration provides numerous benefits, it also raises questions about data privacy and security, which need careful consideration.
Trends in Miniaturization
Miniaturization of MEMS sensors continues to be a noteworthy trend, as smaller devices can fit into increasingly compact systems. This feature is especially beneficial in consumer electronics and medical devices, where space is often limited. The key characteristic of miniaturization is its capability to maintain performance while reducing size.
A unique aspect is the potential for multi-sensor deployment, where many functions can be embedded within a single tiny device. However, challenges related to heat dissipation and durability must be addressed in the development of these small-scale sensors.
Market Outlook
Market outlook for MEMS sensors appears promising, indicating a growing field that will impact multiple sections like automotive, healthcare, and industrial applications. Keeping an eye on market trends is essential for strategic planning and investment decisions.
Projected Growth Rates
Projected growth rates for MEMS sensors are particularly noteworthy. The market is expected to expand at a rate that reflects increasing investments in technology and the growing adoption of smart devices. The key characteristic of this growth is the rising demand for automation and connectivity, which drives innovation across the board.
A unique feature of these projections is the anticipated demand in emerging markets, providing new opportunities for manufacturers. The risk, however, lies in potential oversaturation in certain segments, which could lead to price wars.
Key Players in the Industry
Key players in the industry such as Bosch Sensortec, STMicroelectronics, and Microchip Technology play instrumental roles in shaping the market landscape. Their contributions include developing cutting-edge technologies and forming strategic partnerships. The key characteristic of these players is their diverse product offerings, which cater to various applications.
A unique feature is the ongoing research and development efforts, which could lead to breakthrough technologies. On the downside, the competition among these companies can sometimes lead to aggressive pricing strategies that might lower profit margins.
Potential Market Disruptors
Potential market disruptors can significantly influence MEMS sensor technology. Innovations from startups and advancements in competing technologies pose challenges to established players. The key characteristic of these disruptors is their ability to introduce unique solutions and business models that challenge traditional methods.
A unique aspect is the rise of IoT (Internet of Things), where connectivity and data sharing are mandatory. While this creates new avenues for MEMS sensors, it also emphasizes the need for robust cybersecurity measures.