In-Depth Analysis of FMEA: Key Concepts and Uses
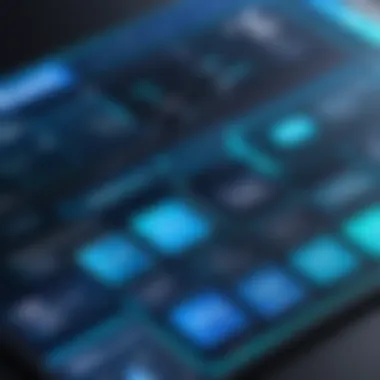
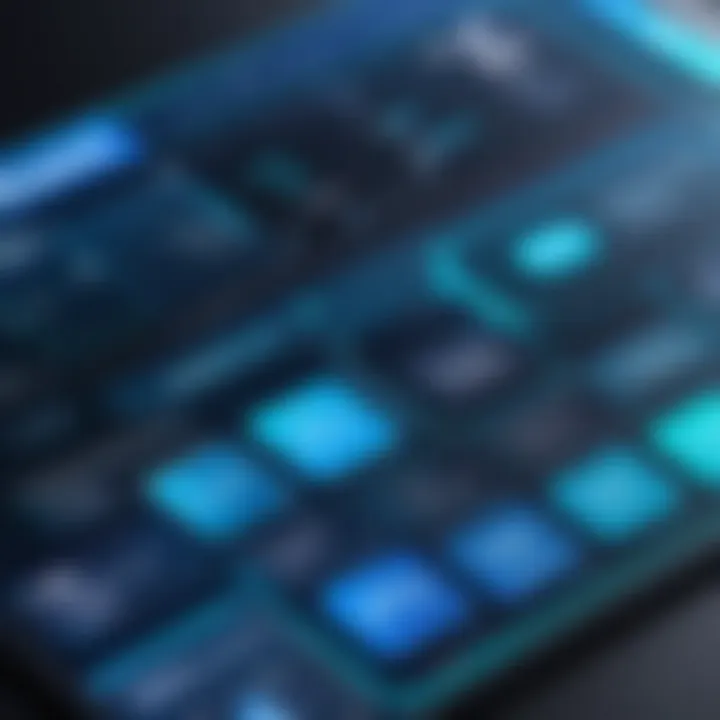
Intro
The intricacies of managing risk and ensuring quality in various sectors can often feel like navigating a minefield. At the heart of effective risk management lies Failure Mode and Effects Analysis (FMEA), a structured approach pivotal for organizations aiming to enhance their product reliability while minimizing potential risks. The journey into understanding FMEA begins by unpacking its principles and methodologies, which are essential for both novices and seasoned experts alike.
Understanding FMEA Principles
FMEA is not merely a check-the-box exercise; it is a dynamic and systematic process. The essence of FMEA is to identify potential failure modes in a system, product, or process and evaluate their effects on the system’s performance. By cataloging these failures, teams can anticipate the consequences, prioritize risks, and implement effective controls to mitigate them.
Key Terminology:
- Failure Mode: The way in which a failure occurs.
- Effect: The impact or consequence of the failure mode.
- Risk Priority Number (RPN): A numerical score calculated as the product of the severity, occurrence, and detection ratings of a failure mode.
These core concepts lay the groundwork for a more in-depth exploration of FMEA, revealing the critical relationships between potential failures and their real-world implications.
Methodologies of FMEA
There are several methods to implement FMEA, each tailored to different organizational needs.
Types of FMEA
- Design FMEA (DFMEA): Focuses on potential issues in design and engineering phases.
- Process FMEA (PFMEA): Centers around manufacturing and assembly processes.
Each type highlights distinct areas where risks can arise, ensuring that teams take a comprehensive approach to risk management. The process typically involves brainstorming sessions, risk assessment with focus on the RPN and the formulation of action plans to address identified risks.
"Proactive identification of failure modes prevents headaches before they occur."
Practical Applications of FMEA
FMEA finds its relevance in myriad industries, including automotive, aerospace, healthcare, and manufacturing, among others. Here’s how it translates in practical scenarios:
- Automotive Industry: Used to improve safety features in vehicle design by anticipating failures in braking systems.
- Healthcare Sector: Applied to streamline processes for patient safety, reducing the risk of medication errors.
Such applications underscore the versatility of FMEA in enhancing standard operating procedures and ensuring compliance with regulatory standards.
Epilogue
Understanding and applying the principles of FMEA is not just beneficial; it is essential for any organization committed to quality and risk management. As industries evolve and technology advances, the strategic implementation of FMEA can lead to increased reliability and consumer trust. It’s crucial for professionals in the field, whether starting fresh or refining their expertise, to engage with the concepts explored here, fostering a deeper appreciation for the nuances and impact of FMEA in today’s dynamic landscape.
Intro to FMEA
Failure Mode and Effects Analysis (FMEA) is not just another buzzword in risk management; it’s a critical tool that many industries rely on to ensure robust quality control. Whether you’re in manufacturing, healthcare, or information technology, understanding FMEA can mean the difference between success and failure. The significance of this methodology lies in its structured approach to identifying potential failures before they happen, allowing organizations to mitigate risks effectively.
When you peel back the layers of FMEA, you find that it does more than just map out potential missteps. It promotes a proactive mindset; organizations can prioritize potential issues based on their impact, leading to more informed decision-making. For example, in the automotive sector, FMEA plays a pivotal role in vehicle design, where even a small oversight can cause catastrophic failures on the road. The process of assessing risk elements makes it easier for teams to tackle the most pressing concerns first, streamlining resources and efforts.
Benefits of FMEA in Various Industries
The breadth of FMEA’s applicability to various industries speaks volumes about its flexibility and effectiveness. Here are some benefits that stand out:
- Enhanced Reliability: FMEA can dissect potential failures at the design and process levels, ensuring products and services consistently meet quality standards.
- Cost Savings: By addressing issues during the design phase, organizations can cut down on costly recalls or reworks later on. Knowing where to channel resources can prove invaluable.
- Improved Safety: In sectors such as healthcare, where human lives are at stake, utilizing FMEA to identify possible failure points allows for timely interventions, ensuring patient safety is paramount.
- Regulatory Compliance: Many industries are subject to stringent regulations. FMEA helps organizations demonstrate their commitment to quality and responsibility, which can ease the burden of compliance.
In today’s complex landscape, FMEA also promotes cross-functional collaboration. Different teams bring varying perspectives, allowing for a richer analysis of potential risks. This collaboration ensures that the outcomes are comprehensive and well-rounded.
"The essence of FMEA is not about avoiding failure; it’s about preparing for it. By recognizing risks before they manifest, organizations become resilient rather than reactive."
Through this section, we've set the stage for a deeper exploration of FMEA’s principles, its varied types, and the structured process involved. As we venture further into the intricacies of FMEA, you’ll see how its methodologies translate into practical applications and how it shapes the very fabric of risk management across industries.
Historical Context of FMEA
Understanding the historical context of Failure Mode and Effects Analysis (FMEA) adds a rich layer of depth to its current applications and methodologies. FMEA first emerged in the late 1940s, born out of the necessity for rigorous risk assessment in military projects. The U.S. military was grappling with the complexities of reliability in weapon systems. Hence, FMEA was developed as a proactive approach to identifying potential failures before they became problematic.
The roots of FMEA trace back to influential sectors such as aerospace and defense, where the consequences of failure could be disastrous. This historical backdrop set the stage for its evolution into a standard practice across many domains, including automotive, manufacturing, and healthcare. Its adoption in these industries largely stemmed from the recognition that foreseeing a problem is significantly cheaper than addressing its repercussions.
In the 1960s, FMEA gained traction within the automotive industry, largely influenced by the rise of quality assurance programs. Companies like General Motors and Ford began applying FMEA methodologies as they sought to enhance product reliability and eliminate defects in production processes. Integrating the principles of FMEA into the manufacturing processes transformed how products were designed, making quality an essential part of the development lifecycle.
As industries evolved, so did FMEA. The 1980s and 1990s saw an expansion of the methodology’s application beyond industrial environments, marking its relevance in various organizations that required structured risk assessment methods. The introduction of regulatory standards, such as ISO 9001, further cemented FMEA as a vital tool in ensuring compliance and maintaining quality.
It is not just a methodology; it is a cultural shift towards preemptive action against potential failure.
The framework was increasingly recognized for its versatility, expanding into software systems and information technology by the 2000s. The digital landscape brought forth new risks, making the application of FMEA critical to cybersecurity practices, particularly in assessing software vulnerabilities and ensuring system reliability.
Today, FMEA is not only a cornerstone tool for risk management but also a crucial component of innovation in various sectors. It plays a fundamental role in integrating new technologies, such as artificial intelligence and machine learning, further extending its historical significance.
Thus, appreciating the historical context of FMEA allows readers to understand its legacy and evolving nature. This evolution highlights the adaptability of this methodology in addressing modern challenges, ensuring that the insights drawn remain relevant in today’s complex technological landscape.
To gain further insight into the evolution of risk management systems, readers might find resources like Britannica or Wikipedia helpful.
Fundamental Principles of FMEA
Understanding the fundamental principles of Failure Mode and Effects Analysis (FMEA) is akin to having a reliable compass in a dense forest. This concept serves as the backbone for risk management and quality control in a multitude of industries. By diving deep into the essential tenets of FMEA, professionals can harness its power to enhance processes and ensure the reliability of products.
Definition and Scope
At its core, FMEA is a systematic approach aimed at identifying potential failure modes within a product or process before they manifest. It’s a preemptive strike against risks that could lead to undesired outcomes or safety hazards. The scope of FMEA isn't confined to a single industry; rather, it spans diverse sectors—from manufacturing to healthcare, and even software development.
FMEA operates on the principle that the earlier you identify a failure mode, the easier and less costly it is to address it. This becomes crucial when considering the lifecycle of a product, where failure costs can escalate rapidly the later they are discovered. Does it really need explaining that addressing issues in the design phase saves more than fixing a faulty product on a store shelf?
The application of FMEA is quite broad. It can be utilized in design FMEA, where potential failures of product designs are scrutinized, or process FMEA, focusing on failures in manufacturing processes. This multi-faceted approach allows teams to tailor their analyses to specific needs, ensuring comprehensive coverage of potential pitfalls.
Purpose and Benefits
The purpose of FMEA extends beyond mere compliance—it's a strategic tool that aids organizations in fostering a culture of risk awareness. One primary benefit is the enhancement of product quality. By addressing risks early in development, companies can create trustworthy products that meet or exceed customer expectations.
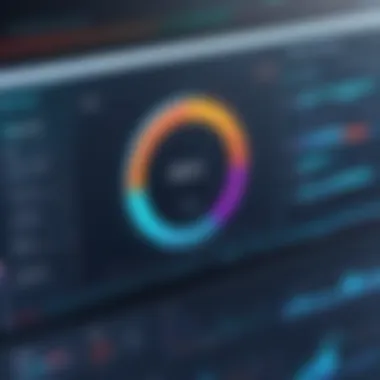

Moreover, FMEA encourages collaborative teamwork. This doesn’t just strengthen the camaraderie among team members, but it also binds diverse experts from various fields who contribute unique insights. For instance, engineers, designers, and safety experts working in harmony can identify issues that might remain invisible to those entrenched within a single specialty.
Some notable benefits of implementing FMEA are:
- Cost Reduction: Identifying potential failures early can significantly lower the costs associated with corrections later in the product lifecycle.
- Increased Safety: Especially in industries like automotive or aerospace, where safety is paramount, FMEA plays an essential role in ensuring that products are safe for end-users.
- Continuous Improvement: FMEA is not a one-time task; it fosters an ongoing dialogue about quality and risk management within organizations.
"In the landscape of risk management, FMEA emerges as a beacon of foresight, helping organizations navigate through the fog of uncertainty."
By integrating these principles into their workflows, businesses can cultivate a proactive approach towards risk management. This ultimately translates into strong financial performance, an enhanced reputation, and most importantly, the trust of their customers.
Types of FMEA
Understanding the different types of Failure Mode and Effects Analysis (FMEA) is crucial as it allows organizations to tailor their approach to specific situations. The effectiveness of FMEA lies in its adaptability to various contexts, and its categorization into distinct types helps clarify where and how it can be utilized most effectively. Each type serves a particular purpose and is designed to address unique challenges associated with either the design, process, or system.
Design FMEA
Design FMEA, often termed DFMEA, focuses on potential failure modes related to product design. It's a proactive approach that enables engineers to identify weaknesses during the design phase, before any physical product is built. This foresight can help prevent costly recalls or redesigns, which, in the world of manufacturing, is akin to throwing good money after bad.
Key elements of Design FMEA include:
- Identification of failure modes: What could go wrong with the design?
- Assessment of effects: How would these failures impact the performance and safety of the product?
- Recommendations for improvements: What changes can be made to alleviate potential risks?
A successful DFMEA can lead to products that not only meet customer expectations but also adhere to safety and regulatory standards. This is paramount in industries like automotive and aerospace, where even minor design flaws could have catastrophic consequences.
Process FMEA
Now, let’s turn our gaze towards the working end of production: Process FMEA, or PFMEA. This type addresses failures that could occur in manufacturing processes instead of the design itself. It examines how processes contribute to product quality and efficiency, scrutinizing each step to reveal vulnerabilities.
Consider this:
- Inputs and factors: What materials, tools, and human elements are involved, and how might they fail?
- Process steps: Are there inconsistencies at any stages of production?
- Effects: If something goes awry, how does it affect the final product?
The end goal of PFMEA is to minimize the risk of defects during production, enhancing consistency and reliability in manufacturing outputs. By systematically identifying and addressing potential process failures, businesses can not only save money but also build a reputation for quality.
System FMEA
Finally, we come to System FMEA. This takes a broader approach than the previous types by examining the interrelations between various components within a system. Think of it as zooming out to see the forest instead of just the trees. System FMEA is often employed in complex environments, such as electronics or integrated machinery, where multiple systems need to function together flawlessly.
Factors that come under the lens include:
- Subsystem interactions: How do various subsystems affect one another?
- Overall system performance: What failures could disrupt the entire system?
- Failure propagation: If one component fails, which others are at risk?
The essence of System FMEA is to guarantee that the whole system operates efficiently and effectively, thereby preventing issues that could lead to system-wide failures. This comprehensive approach is vital in sectors like telecommunications and transportation, where reliability is non-negotiable.
Through these different types of FMEA, organizations are better equipped to manage risks specific to their operations. Each method—be it Design, Process, or System—comes with its unique insights that, when leveraged correctly, bolster overall product quality and operational excellence, ensuring that potential pitfalls are addressed long before they materialize in the real world.
The FMEA Process
The FMEA process is a crucial part of risk management and quality assurance. This structured approach not only identifies potential failures but also assesses their impact, allowing teams to prioritize corrective measures. When implemented correctly, FMEA effectively streamlines problem-solving efforts, leading to improved productivity and enhanced product reliability. As industries evolve and products become more complex, mastering this process becomes indispensable for ensuring both safety and efficiency.
Team Formation and Planning
The first step in the FMEA process involves assembling a well-rounded team. This team should be composed of individuals with diverse expertise relevant to the project at hand. Involving cross-functional members can make a significant difference, as it brings various perspectives to the table. Consider engineers, designers, quality assurance professionals, and other stakeholders who understand the product or process intimately.
The team needs to outline the planning phase clearly. Define objectives, timelines, and deliverables to ensure that everyone is on the same page. A thorough planning phase helps avoid pitfalls later in the process. "Failing to prepare is preparing to fail," as the saying goes. Everybody involved should have a common understanding of what the FMEA process aims to achieve in terms of improving product quality and reducing risks.
Identification of Failure Modes
Once the team is set up, the next step is identifying potential failure modes. A failure mode refers to the ways in which a component or process may fail. Teams can utilize brainstorming sessions or structured approach like the 5 Whys to dig deeper into potential issues. Documenting each mode is essential for a comprehensive review.
Each identified failure mode should be described in detail. Attributes such as the type of failure, its causes, and potential consequences must be recorded. This phase, while seemingly straightforward, may require teams to think critically and challenge assumptions regularly. Missing a potential failure can lead to bigger issues down the line, so vigilance is key.
Assessment of Effects
Following identification, the next phase is assessing the effects of those failure modes. This analysis aims to understand the implications of each failure, addressing how it affects product performance, safety, or compliance. Teams typically use a systematic approach to categorize each failure effect based on severity, detecting how crucial the failure is in terms of risk.
At this stage, consider asking questions such as:
- How does this failure impact end-users?
- Are there regulatory implications to consider?
This assessment not only informs risk prioritization but also helps to direct focus toward the most significant threats, enhancing resource allocation.
Determining Risk Priority Numbers
Once effects are assessed, determining the Risk Priority Number (RPN) becomes essential. This number quantitatively reflects the risk associated with each failure mode, making it easier to prioritize action plans. RPN is calculated by multiplying three factors: severity, occurrence, and detection—the final score helps in understanding the urgency of addressing each issue.
The formula can be summarized as:
RPN = Severity x Occurrence x Detection
Each factor is rated on a predetermined scale. The results guide teams in prioritizing their focus where it’s most needed, allowing efficient allocation of time and resources.
Developing Action Plans
With priorities set, the final stage involves developing detailed action plans to address the identified failure modes. Each plan should outline corrective actions alongside assigned responsibilities and deadlines. It’s vital to ensure that these plans are not overly complicated. Simplicity often leads to practicality, enabling the team to implement changes smoothly.
Involving everyone in the drafting process can enhance buy-in and accountability. It's important to monitor the implementation closely and adjust plans as necessary. Remember, action without follow-up doesn’t yield results. Regularly reviewing the effectiveness of the actions taken can also help mitigate the risk of new failures emerging after initial fixes.
"An ounce of prevention is worth a pound of cure."
In summary, the FMEA process comprises essential steps regarding team formation, failure identification, effect assessment, RPN determination, and action plan development. Mastering these steps can lead to significant enhancements in product quality and safety, positioning organizations to thrive in an increasingly competitive environment.
Challenges in Implementing FMEA
Implementing Failure Mode and Effects Analysis (FMEA) presents certain hurdles that can complicate even the most straightforward processes. Understanding these challenges is crucial for team members and management alike, as it reveals the underlying considerations that come into play when integrating FMEA into organizational practices. Addressing these potential pitfalls not only bolsters the effectiveness of FMEA but also ensures that the objectives of quality control and risk management are attained with precision.
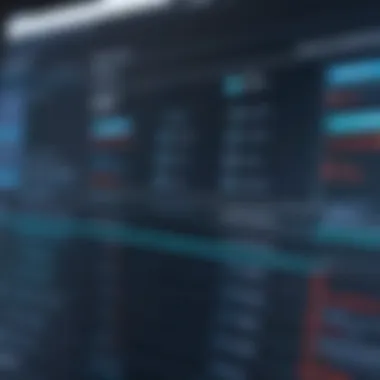
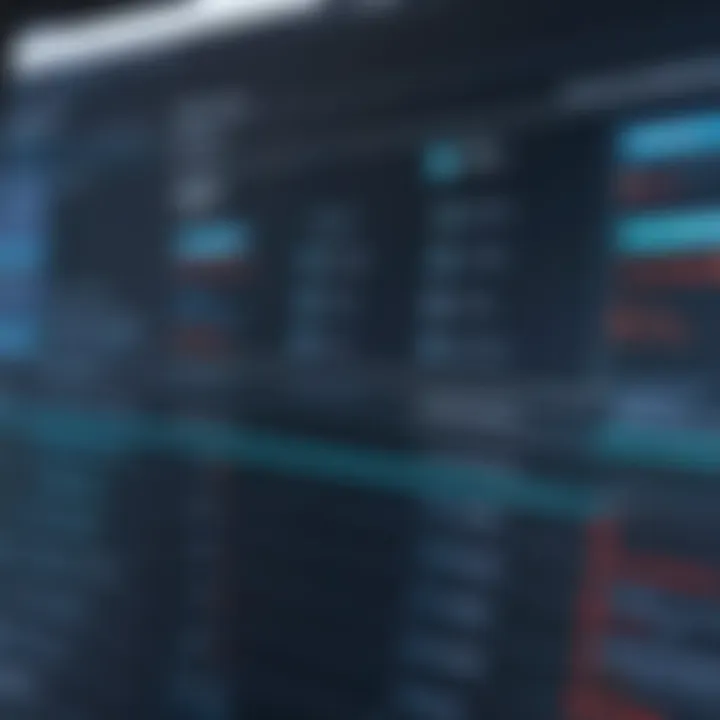
Data Collection Limitations
Data serves as the backbone for the entire FMEA process. Without it, one might as well be venturing into the wilderness without a map. Unfortunately, data collection can often be fraught with challenges, stemming from a variety of sources.
- Limited Availability: Sometimes, relevant historical data simply isn't accessible. This absence can lead to assumptions rather than grounded conclusions, leaving teams uncertain about failure probabilities.
- Inconsistent Quality: Even when data is available, the quality may fluctuate. Relying on inconsistent data sets—or worse, anecdotal evidence—can cloud judgment and muddle the findings.
- Complexity of Data Types: Different types of data, such as qualitative and quantitative, must be analyzed in tandem. Merging these varying sources into a coherent assessment can present its own set of headaches, particularly if team members lack experience with certain data methodologies.
Ensuring a robust data collection process is critical. Establishing standard procedures for gathering and analyzing data can address many of these limitations and enhance the FMEA's overall effectiveness.
"Quality data is not just an asset; it’s the lifeblood of FMEA. Navigating around data limitations can often spell the difference between merely going through the motions and genuinely enhancing reliability."
Team Dynamics and Expertise
The effectiveness of FMEA is heavily influenced by the teamwork involved in its execution. Without a solid group backing the process, FMEA can feel like riding a bicycle with a flat tire—uneven and sometimes out of control.
- Diverse Skill Sets: A successful FMEA team requires a fusion of skills, spanning areas such as engineering, quality assurance, and project management. Having the right mix can expedite problem identification and analysis. However, missing even one essential skill can create gaps in the analysis.
- Communication Barriers: Miscommunication can occur when team members hail from different departments or backgrounds. What feels like a minor misunderstanding could lead to significant oversights in identification and prioritization.
- Variation in Commitment Levels: Not all team members may be equally invested in the FMEA process. Lack of active participation can skew results, leading to missed opportunities for prevention.
Recognizing the importance of team dynamics is essential. Building a cohesive unit through open communication channels and mutual respect enhances both the process and the final outcomes of FMEA.
Integration of FMEA with Other Methodologies
Integrating Failure Mode and Effects Analysis (FMEA) with other established methodologies can significantly bolster risk management strategies across various industries. FMEA alone provides a robust framework for identifying potential failures and prioritizing associated risks. However, when combined with methodologies like Six Sigma and ISO Standards, organizations can enhance their operational effectiveness, product reliability, and overall quality control.
The overlap between these methodologies is not just beneficial but essential for achieving cohesive risk management. Companies often face challenges in navigating complex projects with numerous interconnected variables. The integration helps to streamline processes, foster collaboration among teams, and ensure that risk assessments are thorough. This section explores how FMEA dovetails with complementary methodologies.
FMEA and Six Sigma
Six Sigma is a data-driven approach aimed primarily at process improvement and variation reduction. When FMEA is integrated into the Six Sigma framework, it enhances the capability to foresee and mitigate risks early in the project lifecycle. The synergy between the two methodologies can be explained through several critical aspects:
- Proactive Risk Management: By employing FMEA during the Define and Measure phases of Six Sigma, teams can identify high-risk areas before delving into improvement initiatives. This leads to a more focused and efficient project direction.
- Data-Driven Decisions: Six Sigma emphasizes the importance of statistical data. FMEA complements this by offering qualitative insights into what risks might affect the project, which can then be validated through quantitative measures.
- Continuous Improvement: Both methodologies aim for continual enhancement. Using FMEA in the Analyze phase allows teams to identify root causes of failures, which can then be addressed in design modifications or process changes to move toward higher quality outcomes.
As organizations seek to implement improvements, incorporating FMEA within Six Sigma projects facilitates a thorough understanding of potential pitfalls, enabling businesses to be ten steps ahead of potential issues.
FMEA and ISO Standards
ISO standards are internationally recognized frameworks that guide organizations in achieving quality assurance and operational excellence. Integrating FMEA with ISO management systems, such as ISO 9001, can provide numerous advantages:
- Standardized Risk Assessment: FMEA offers a systematic approach to assess risks, which aligns well with ISO standards' structured procedures. Organizations can ensure that risk evaluations meet international quality benchmarks.
- Comprehensive Documentation: ISO emphasizes the requirement for clear documentation and traceability. FMEA results can easily be documented within ISO frameworks, aiding in compliance and audits.
- Enhanced Communication: Utilizing FMEA within an ISO framework fosters better communication among teams regarding potential risks and actions needed to mitigate those risks. This alignment is crucial in organizations with diverse teams or international operations.
Integrating FMEA with ISO standards not only promotes a culture of quality but also serves stakeholders by building trust through transparent processes and consistent improvement efforts.
In today's competitive landscape, effectively integrating FMEA with methodologies like Six Sigma and ISO standards is not just a good practice—it’s a strategic necessity.
The benefits of integrating FMEA with these methodologies are clear: improved risk management, enhanced product quality, and increased organizational resilience. These integrations should be thoughtfully considered by IT professionals, cybersecurity experts, and students alike, as it amplifies the significance of FMEA in real-world applications.
Real-World Applications of FMEA
The impact of Failure Mode and Effects Analysis (FMEA) stretches far beyond its theoretical foundations; it plays a crucial role in various industries and real-world applications. At its core, FMEA serves as a structured approach aimed at identifying and mitigating potential failures before they occur. This proactive methodology ensures that both products and processes achieve the highest possible standards of reliability and safety.
In sectors such as aerospace, automotive, and healthcare, the stakes are incredibly high. A failure in any of these domains can lead to catastrophic consequences, not only financially but also in terms of human safety. Here are some illustrative examples:
- Aerospace: In the aviation industry, FMEA is integrated into the design and manufacturing processes of aircraft components. For instance, consider a scenario involving an aircraft’s hydraulic system. FMEA helps teams to analyze potential failures, such as leaks or system pressure loss, and to implement corrective measures even during the design phase. This diligence ensures that when the aircraft flies, passengers are safeguarded against possible malfunctions.
- Automotive: The automotive sector employs FMEA to refine vehicle safety features. Take, for instance, the deployment of airbags. Through FMEA, automotive engineers can evaluate various failure modes such as sensors not deploying the airbag or deployment at inappropriate times. Addressing these issues during design results in safer vehicles with fewer recalls.
- Healthcare: In healthcare, FMEA addresses the complexities of patient safety. Hospitals use FMEA to scrutinize processes like medication administration. For example, if a system is prone to mislabeling medication dosages, FMEA helps identify these risks and allows for the implementation of more stringent verification procedures, therefore reducing the likelihood of medication errors.
Moreover, the FMEA method is not confined strictly to engineering or production teams. It fosters cross-departmental collaboration, leading to a culture of quality assurance across organizations. Here are the specific benefits of adopting FMEA in real-world applications:
- Enhanced Product Reliability: By highlighting potential failure points early in the development phase, teams can design more reliable products.
- Risk Mitigation: FMEA provides a systematic approach to evaluate risks, allowing companies to prioritize corrective actions where they matter most.
- Cost Efficiency: Preventing failures is often less costly than addressing them post-implementation. Organizations save money on warranty claims and product recalls.
Considerations for Implementing FMEA
While FMEA presents numerous benefits, certain considerations must be taken into account:
- Team Involvement: A cross-functional team is necessary for successful FMEA. It demands inputs from diverse expertise, from engineering to marketing, ensuring a holistic view of potential failures.
- Regular Reviews: FMEA is not a one-time exercise. Organizations must periodically revisit and revise their assessments as products and processes evolve.
In summary, the real-world applications of FMEA illustrate its significance as a vital tool across various industries. It empowers organizations to preemptively tackle failures, fostering innovation supported by a robust safety net of analysis. With a firm grasp on the FMEA process, industries can enhance reliability, minimize risks, and, ultimately, serve their clientele with confidence.
"FMEA is the safety net where innovation takes flight. Without it, you gamble with failure."
Case Studies Demonstrating FMEA Effectiveness
Case studies serve as a powerful tool in illustrating the real-world application of FMEA. They not only provide concrete examples of how this methodology can enhance decision-making processes but also showcase its effectiveness in mitigating risks. When we delve into specific instances where FMEA has been applied, it becomes clear that understanding the nuances of failure modes and their effects is crucial for any industry.
Importance of Case Studies
Engaging with case studies of FMEA effectiveness offers several key benefits:
- Demonstration of Practical Application: They present detailed accounts of how FMEA is utilized in various sectors, illustrating both the methodology and the results achieved.
- Learning Opportunities: Through analyzing these cases, IT professionals and students can understand potential pitfalls and best practices.
- Validation of Methodology: These studies provide evidence that FMEA leads to improved product reliability and efficiency when implemented correctly.
One notable example originates from the aerospace industry, where safety and reliability are paramount. In one case, a prominent aircraft manufacturer utilized FMEA to analyze potential failure modes in a new engine design. This involved assessing risks related to failure of components, from fuel systems to electronic controls. By identifying likely failure modes early in the design phase, the organization was able to institute preventive measures that not only heightened the safety profile but also saved significant costs associated with faults detected post-manufacturing.
Specific Elements of Case Studies
In examining case studies on FMEA, we often find common elements that illustrate its effectiveness:
- Comprehensive Team Involvement: The success of the analysis typically hinges on the collaboration of multidisciplinary teams. Experts from design, engineering, and quality assurance all contribute their insights, making for a thorough assessment of risks.
- Data-Driven Decision Making: Many examples highlight the importance of precise data collection. Successful FMEA applications showcase detailed documentation of failure modes, their frequency, and potential impact.
- Actionable Outcomes: The results of these studies frequently lead to specific corrective actions. For instance, in one automotive manufacturer’s case, the identification of a critical failure mode in braking systems led to redesigning components to enhance reliability.
Considerations About Effectiveness
While many case studies are inspirational, it's crucial to also acknowledge that results can vary based on several factors. Variables such as team experience with FMEA, availability of accurate data, and organizational culture play significant roles in determining the outcome. Furthermore, consistency in applying the methodology and conducting reviews periodically can lead to revised FMEA documents that reflect the evolving risk landscape.
"Case studies are the fingerprints of success in FMEA application; they tell the story of what works and what doesn't," one expert noted.
In summary, case studies not only highlight the direct benefits of FMEA but also provide a framework for understanding the intricacies involved in risk management. They demonstrate that when FMEA is executed thoughtfully, the outcomes can lead to enhanced quality, safety, and customer satisfaction in various industries. By learning from these narratives, professionals can adapt their strategies to foster greater reliability in their projects.
Future Trends in FMEA
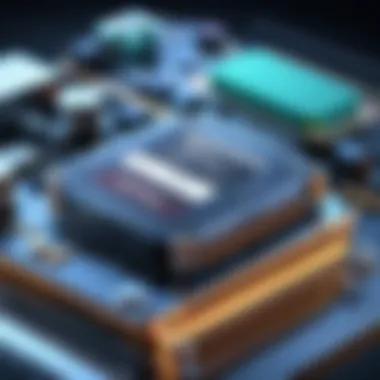
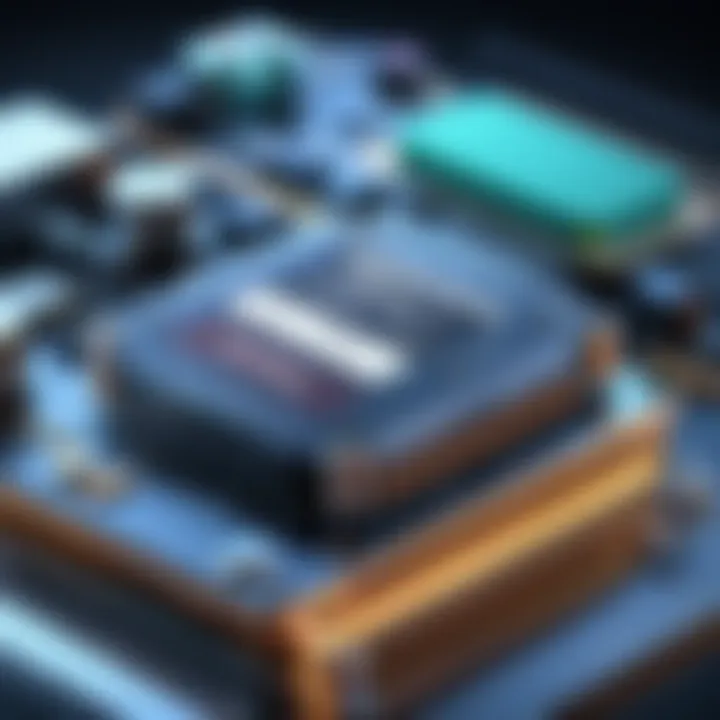
In the rapidly evolving landscape of technology and industry, staying ahead means recognizing and adapting to emerging trends. This section highlights the pivotal developments in Failure Mode and Effects Analysis (FMEA) that resonate within contemporary practices. As industries grapple with the increasing complexity and pace of change, understanding future trends in FMEA becomes paramount.
Emerging Technologies and FMEA
With the advent of machine learning, artificial intelligence, and Internet of Things (IoT) technologies, FMEA is undergoing a fundamental transformation. These technologies enable real-time data analysis, enhancing the ability to predict and mitigate failure modes before they impact production. For instance, utilizing predictive analytics, companies can evaluate large sets of operational data to recognize patterns that might elude traditional methods.
Moreover, consider how automation can streamline the FMEA process. Automated systems can assist in identifying potential failure modes by analyzing historical performance data and correlating it with current operations, making it easier for teams to stay ahead of potential issues.
"The integration of tech tools with FMEA can drive a proactive approach to risk management."
The benefits of such integration are manifold:
- Real-time Monitoring: Constant supervision of systems reduces latency in identifying potential failures.
- Enhanced Accuracy: Advanced algorithms can potentially reduce human error associated with traditional analyses.
- Cost Effectiveness: Early detection minimizes losses and decreases costly downtimes.
FMEA in Agile Environments
As industries increasingly adopt agile methodologies, integrating FMEA into these frameworks presents both challenges and opportunities. Agile emphasizes quick iterations and responsive design processes, which can sometimes clash with the more methodical nature of traditional FMEA. However, by adopting an agile mindset, organizations can refine the FMEA process itself, ensuring it is more adaptable and faster.
In an agile environment, the focus shifts toward continuous improvement and feedback loops. This leads to:
- Adaptable Risk Assessments: Rather than static evaluations, teams can revisit and revise FMEA assessments regularly throughout the development cycle.
- Cross-Functional Collaboration: FMEA can benefit from insights across disciplines. Agile teams often consist of varied expertise, leading to richer discussions and outcomes.
- Fostering Innovation: A more dynamic approach allows teams to integrate FMEA earlier in the design process, enabling innovative solutions to surface sooner.
Utilizing FMEA within agile practices not only improves product reliability but also aligns risk management with fast-paced development timelines. This reinvention of FMEA holds significant promise, as it allows organizations to remain competitive amid the shifting tides of industry demands and consumer expectations.
FMEA Software and Tools
When delving into the realm of Failure Mode and Effects Analysis (FMEA), it becomes abundantly clear that the role of specialized software cannot be understated. As industries evolve and the demand for efficiency increases, organizations are looking towards FMEA software as a critical component in streamlining the risk assessment process. This section discusses the fundamental aspects of FMEA software, revealing its significance to practitioners in various fields.
One primary advantage of utilizing dedicated FMEA software is its ability to facilitate collaboration among team members. Many of these platforms allow users to contribute simultaneously, ensuring that input from diverse perspectives is captured. Moreover, this engagement can significantly improve communication, which is often a stumbling block in traditional paper-based approaches. An effective tool can help bridge gaps in understanding and promote a shared vision among team members.
FMEA software also enhances data management capabilities. The ability to store and organize information efficiently is crucial. As teams identify failure modes and assess associated risks, maintaining a comprehensive database becomes vital. This feature enables quicker retrieval of data, aiding in trend analysis or historical comparisons that can lead to future improvements.
Overview of Commercial Tools
The landscape of FMEA software is rich with options, each offering distinct features tailored to various industry needs. Some of the key tools in the market include the following:
- Apollo FMEA: Known for its user-friendly interface, this tool enables teams to navigate through the risk management process with ease. Its reporting functionalities stand out, providing visual insights that help in decision-making.
- FMEA-Pro: This software is widely appreciated for its customizable templates, catering to different project requirements. It emphasizes ease of use without compromising advanced analytical capabilities.
- Palisade's DecisionTools Suite: This powerful software combines FMEA with Monte Carlo simulation, allowing teams to assess risks with a degree of sophistication that traditional methods cannot provide.
While evaluating these tools, it’s important to consider various features including:
- User interface: A simple, intuitive interface is essential especially when team members have varying levels of technical acumen.
- Integration capabilities: The software should seamlessly integrate with existing systems, ensuring data consistency across platforms.
- Support and training: Reliable customer support and comprehensive training resources can make a world of difference when teams are acclimating to new software.
Best Practices for Tool Selection
Selecting the right FMEA software is a task that shouldn't be taken lightly. Here are a few best practices to guide organizations through this process:
- Define Specific Needs: Each organization has its unique challenges. It’s prudent to outline specific needs such as regulatory compliance, cross-functional collaboration, or advanced reporting requirements before zeroing in on a tool.
- Conduct a Trial Run: Many companies offer free trials. Take advantage of this opportunity to gauge how well the tool fits into your team's workflow.
- Seek Feedback from Users: Engage team members who will use the software regularly. Their insights on usability can help highlight potential issues that may not be immediately apparent.
- Compare Costs vs. Benefits: Initial investment is just one side of the coin. Analyze the long-term benefits the software can bring to ensure it provides sufficient value.
"Choosing the right software is not just about price; it’s about finding a solution that aligns with your workflow and enhances your productivity."
By following these best practices, organizations can ensure they select a tool that not only meets their current needs but also scales with them as they grow, ultimately enhancing their FMEA processes and outcomes.
Training and Certification in FMEA
Training and certification in Failure Mode and Effects Analysis (FMEA) are crucial elements that can significantly enhance an organization's approach to risk management and quality control. The realm of FMEA is intricate, demanding not only a theoretical understanding but also practical skills that can be obtained through structured training programs. This section aims to detail the importance of these educational pathways, the benefits they confer, and the various certification possibilities available to professionals in this field.
Importance of Training Programs
Training programs centered on FMEA are essential for several reasons. First and foremost, they lay the groundwork for a comprehensive understanding of the methodology, ensuring that individuals grasp both the theoretical principles and practical applications. Such knowledge is indispensable in sectors ranging from automotive to healthcare, where the consequences of failures can be dire.
- Structured Learning: Programs often follow a step-by-step approach, breaking down complex concepts into manageable pieces. This helps participants absorb and retain information better.
- Hands-On Experience: Many training programs include case studies and simulations, allowing learners to apply their knowledge in real-world scenarios. This hands-on experience deepens comprehension and can highlight nuances that theory alone might not convey.
- Collaboration Skills: FMEA requires a team-oriented approach where cross-functional teams collaborate to assess risks. Training fosters teamwork, enabling professionals to develop communication and collaborative skills critical for successful FMEA practices.
In addition, proper training can lead to better decision-making across teams, as individuals become adept at identifying potential failure modes and assessing their impacts based on established criteria.
Certification Paths for Professionals
Acquiring certification in FMEA showcases an individual’s commitment to excellence and proficiency in the methodology. Various organizations offer certification programs, each with its own set of criteria and focus areas. Here are some of the paths that professionals can pursue:
- Certified FMEA Practitioner (CFP): Offered by various industry bodies, this certification is aimed at individuals who wish to certify their understanding and application of FMEA in real-world projects. The CFP credential can boost a candidate’s profile and demonstrate their capability to lead FMEA initiatives.
- FMEA Training Modules: Many organizations provide modular training courses. Each module may culminate in an assessment, leading to a certificate for that specific area, such as Design FMEA or Process FMEA. This flexibility allows professionals to focus on areas most relevant to their work.
- Industry-Specific Certifications: Some sectors have tailored certifications that align FMEA with unique industry requirements. For instance, in the aerospace industry, professionals may pursue specific training that emphasizes the rigorous standards required in that field.
Ultimately, certification not only elevates one’s career prospects but also instills confidence in employers seeking skilled practitioners adept at conducting effective FMEA.
"Proper training and certification in FMEA are not merely optional—they are essential for ensuring that professionals can skillfully navigate potential failures and enhance product reliability."
Closure: The Value of FMEA in Modern Industries
In the ever-evolving landscape of modern industries, the significance of Failure Mode and Effects Analysis (FMEA) cannot be overstated. It's more than just a theoretical framework; it's a robust tool that arms organizations with the capability to anticipate and mitigate risks before they manifest into costly failures.
The Importance to Organizations
FMEA serves as a lens through which companies can scrutinize their processes and designs. As they navigate complex projects, the identification of potential failure modes becomes imperative. By systematically evaluating the effects of each failure, organizations can prioritize their focus—channeling resources where they are most needed. This proactive approach not only enhances reliability but also boosts customer confidence in products and services. Just as an ounce of prevention is worth a pound of cure, applying FMEA can save businesses from potential pitfalls that could derail their operations.
Benefits Across Industries
Many sectors benefit from the implementation of FMEA:
- Automotive: In the fast-paced world of automotive manufacturing, ensuring safety is paramount. FMEA helps in identifying less obvious failure modes that could compromise vehicle integrity.
- Healthcare: Medical devices undergo stringent scrutiny to safeguard patient health. Here, FMEA identifies risks associated with device malfunctions, thus protecting lives.
- Aerospace: In aviation, the stakes are even higher. FMEA assists in thorough risk assessments to prevent accidents that could arise from overlooked failure options.
These examples showcase how the methodology transcends industry boundaries, providing a standardized approach to risk management.
Continuous Improvement
Moreover, FMEA is not just a one-time endeavor. Its cyclical nature encourages continuous improvement. Regular updates and reviews ensure that products evolve in tandem with new technologies and emerging challenges. By embedding FMEA into their quality management systems, organizations create a culture of vigilance and accountability.
"An organization that neglects FMEA risks its ability to adapt to change and innovate effectively."
Finale
In short, the value of FMEA in modern industries is multifaceted. It drives enhanced product quality, safeguards customer trust, and fosters a preventive mindset. As industries face increasing complexities and pressures, incorporating FMEA into operational frameworks isn’t just beneficial; it’s essential. For IT professionals and cybersecurity experts, understanding and applying FMEA principles could well be the difference between success and failure in projects that demand precision and reliability. The key lies in recognizing that every failure mode presents a learning opportunity that can fuel future growth.