Unveiling the Transformative Power of Industry 4.0 in Manufacturing Processes
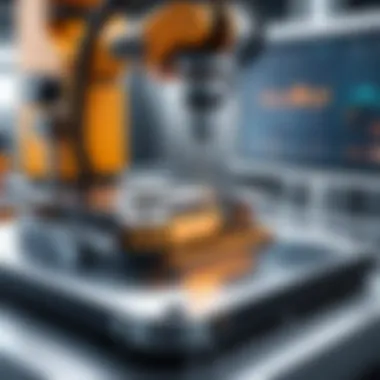
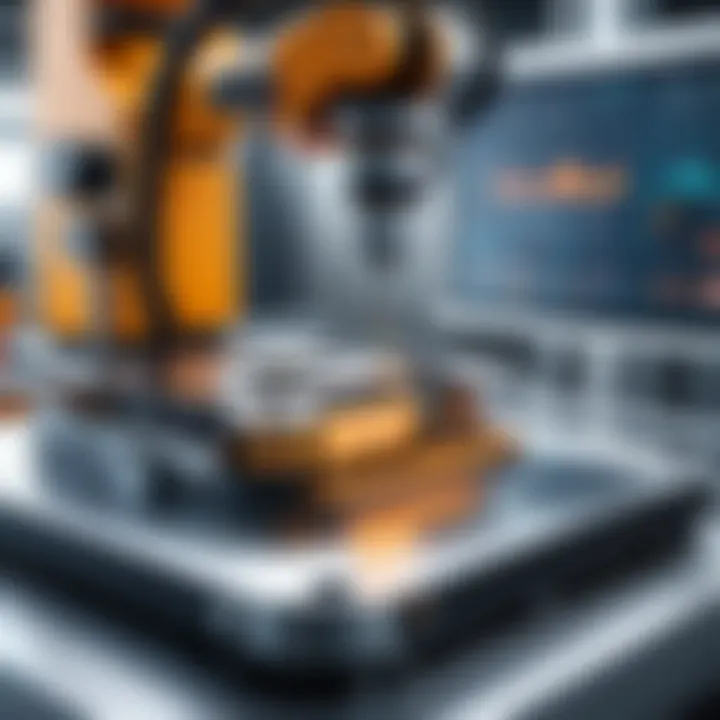
Understanding the Evolution of Industry 4. in Manufacturing
Embracing Industry 4.0 in the manufacturing realm signifies a monumental shift towards optimal utilization of cutting-edge technologies. This transcendence marks a crucial juncture in the industrial domain, ushering in an era of unprecedented advancement. The revolution unfolding within Industry 4.0 is not merely a technological upgrade; it symbolizes a paradigmatic leap into a future where automation, data exchange, and smart systems converge to redefine manufacturing processes.
Revealing the Technological Underpinnings of Industry 4.
The essence of Industry 4.0 lies in its foundational technologies that act as the bedrock of innovation within manufacturing landscapes. These technologies encompass a spectrum of advancements ranging from the Internet of Things (Io T) and Artificial Intelligence (AI) to Cyber-Physical Systems (CPS) and Big Data analytics. Nurturing a profound understanding of these pillars is paramount to unlocking the transformative potential of Industry 4.0 within manufacturing environments.
Impacts of Industry 4. Integration
As Industry 4.0 infuses its disruptive influence into the manufacturing sector, its impact reverberates across multiple dimensions. Enhanced operational efficiency, streamlined production processes, predictive maintenance capabilities, and real-time data analytics stand as the hallmarks of the Industry 4.0 ethos. This integration paves the way for a dynamic ecosystem where agile decision-making and resource optimization become the norm.
Exploring Challenges and Opportunities in Industry 4. Implementation
Navigating the terrain of Industry 4.0 implementation presents a dual-faced scenario characterized by challenges and opportunities. From upskilling the workforce to address technology gaps to ensuring robust cybersecurity measures in the face of digital threats, the journey towards Industry 4.0 excellence is fraught with intricacies. However, amidst these challenges lie boundless opportunities for innovation, growth, and market differentiation.
Synthesizing the Future Landscape of Manufacturing
Introduction to Industry 4.
In the realm of modern manufacturing, the concept of Industry 4.0 has emerged as a transformative force, integrating advanced technologies to revolutionize industrial processes. This section serves as a foundational piece, shedding light on the significance of Industry 4.0 in reshaping traditional manufacturing landscapes. By exploring specific elements such as automation, Internet of Things, artificial intelligence, and big data analytics, this article aims to illuminate the substantial benefits and considerations tied to embracing Industry 4.0 in manufacturing operations.
Definition and Evolution
The concept of Industry 4.
The concept of Industry 4.0 encompasses the fusion of digital technologies with traditional manufacturing processes, leading to the creation of 'smart factories.' Its key characteristic lies in the interconnectedness of machines and systems through the Internet, enabling real-time data exchange and automated decision-making processes. The unique feature of Industry 4.0 is its ability to enhance operational efficiency, productivity, and customization capabilities. While presenting numerous advantages in optimizing production processes, the concept of Industry 4.0 also poses challenges related to data security and privacy that manufacturers need to address proactively.
Evolution from traditional manufacturing
The evolution from traditional manufacturing to Industry 4.0 signifies a shift from manual labor to automated, data-driven processes. This evolution emphasizes the integration of advanced technologies like robotics, AI, and Io T to streamline operations and enhance quality. The key characteristic of this evolution is the focus on efficiency, flexibility, and sustainability within manufacturing environments. By leveraging digital tools and connectivity, manufacturers can achieve heightened levels of precision and speed, paving the way for improved production outcomes. However, this evolution may require substantial investments in upgrading infrastructure and reskilling the workforce, underscoring the need for careful planning and execution.
Core Technologies
Internet of Things (IoT)
The Internet of Things (Io T) plays a pivotal role in Industry 4.0 by enabling the interconnectivity of devices, sensors, and systems, fostering data exchange and automation. Its key characteristic is the ability to gather real-time insights from equipment and processes, enhancing monitoring and decision-making capabilities. IoT's unique feature lies in its capacity to reduce downtime, optimize maintenance schedules, and minimize wastage through predictive analytics. While offering significant benefits in enhancing efficiency and productivity, IoT implementation may introduce vulnerabilities that need to be addressed, encompassing data privacy and cybersecurity considerations.
Big Data Analytics
Big Data Analytics serves as a cornerstone in Industry 4.0, empowering manufacturers to harness vast amounts of data for actionable insights and informed decision-making. The key characteristic of big data analytics is its capability to process and analyze complex datasets, uncovering patterns and trends that drive operational improvements. Its unique feature lies in the predictive capabilities that forecast machine failures, market demands, and resource utilization, enabling proactive responses and strategical planning. However, the implementation of big data analytics demands robust infrastructure, skilled personnel, and adaptation to data privacy regulations to maximize its advantages and mitigate challenges related to data quality and interpretation.
Artificial Intelligence (AI)
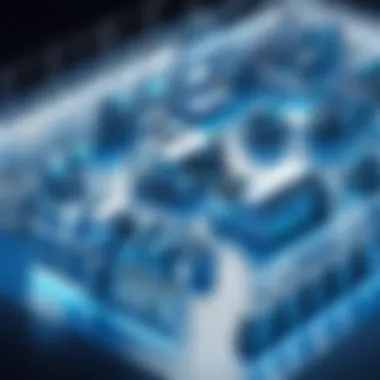
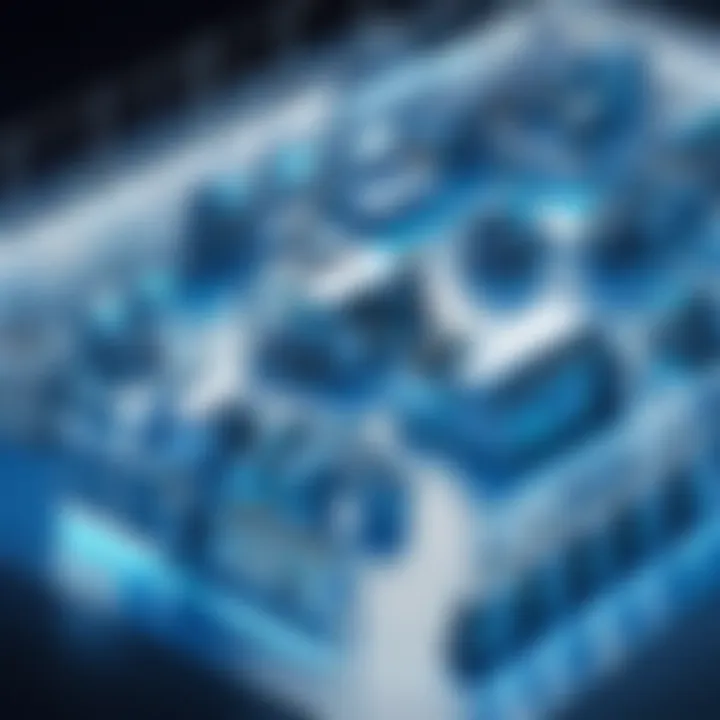
Artificial Intelligence (AI) stands at the forefront of Industry 4.0, offering sophisticated algorithms and machine learning capabilities to enhance operational intelligence and decision-making processes. With its key characteristic in automation, optimization, and cognitive abilities, AI enables manufacturing systems to learn, adapt, and evolve based on data inputs and algorithms. Its unique feature lies in the continuous self-improvement and adaptability exhibited by AI systems, driving efficiencies, predictive maintenance, and personalized product offerings. While AI presents immense benefits in revolutionizing manufacturing processes, ethical considerations, biases in algorithms, and data security concerns must be carefully managed to ensure responsible AI deployment.
Robotics and Automation
Robotics and Automation revolutionize manufacturing operations by introducing robotic systems that automate repetitive tasks and streamline complex processes. The key characteristic of robotics and automation is the precision, speed, and reliability they bring to production lines, enhancing productivity and quality control. The unique feature of robotics and automation lies in their ability to handle intricate tasks safely, efficiently, and consistently, reducing human error and operational costs. While offering significant advantages in labor efficiency, safety, and scalability, the adoption of robotics and automation necessitates careful integration, maintenance, and workforce upskilling to fully leverage their benefits while addressing potential drawbacks related to initial costs and adaptability challenges.
Principles and Pillars
Interconnectivity
Interconnectivity serves as a foundational principle in Industry 4.0, emphasizing the seamless connection of machines, systems, and processes to enable real-time information flow and decision-making. Its key characteristic lies in the networked architecture that fosters data exchange, enabling holistic visibility and control over manufacturing operations. The unique feature of interconnectivity is its potential to integrate disparate systems and devices, harmonizing production workflows and enhancing collaboration across departments. While offering advantages in enhancing communication, productivity, and agility, interconnectivity challenges include interoperability issues, cybersecurity risks, and data management complexities that manufacturers must address to ensure a robust and secure interconnected ecosystem.
Information Transparency
Information Transparency plays a crucial role in Industry 4.0 by promoting access to real-time data and insights across the manufacturing value chain, facilitating informed decision-making and actionable intelligence. The key characteristic of information transparency is its emphasis on open data sharing, enabling stakeholders to retrieve relevant information and analytics seamlessly. Its unique feature lies in the democratization of data access, empowering employees at all levels to make data-driven decisions and contribute to process improvements. While benefiting operations in enhancing visibility, efficiency, and collaboration, information transparency initiatives require clear governance frameworks, data standardization practices, and cybersecurity measures to protect sensitive information and ensure data integrity.
Technical Assistance
Technical Assistance in Industry 4.0 pertains to the integration of advanced technologies such as augmented reality, virtual reality, and digital twin systems to support manufacturing processes and empower employees. Its key characteristic lies in providing real-time guidance, training, and visualization tools to enhance operational efficiency and skills development. The unique feature of technical assistance is its ability to simulate scenarios, troubleshoot issues, and deliver personalized training experiences tailored to individual learning needs. While offering benefits in improving workforce competencies, reducing downtime, and enhancing decision-making, technical assistance implementations necessitate investment in infrastructure, employee training, and continuous technology enhancements to maximize their contribution to operational excellence and innovation.
Decentralized Decision-making
Decentralized Decision-making signifies a fundamental shift in manufacturing paradigms, empowering frontline employees and machines to make autonomous decisions based on real-time data and predefined algorithms. Its key characteristic is the delegation of decision authority to local nodes within the manufacturing environment, enabling rapid, contextual responses to dynamic production conditions. The unique feature of decentralized decision-making lies in fostering agility, adaptability, and responsiveness within manufacturing operations, promoting innovation and continuous improvement. While offering advantages in accelerating decision cycles, fostering employee empowerment, and enhancing customization capabilities, decentralized decision-making requires clear guidelines, robust algorithms, and monitoring mechanisms to ensure alignment with strategic objectives, regulatory compliance, and quality standards.
Impact on Manufacturing Sector
In the realm of Industry 4.0, the Impact on Manufacturing Sector stands as a pivotal focus area, driving significant changes and advancements within the industrial landscape. This section delves into the core transformations and enhancements brought about by the integration of Industry 4.0 principles in manufacturing operations. By embracing cutting-edge technologies such as Internet of Things (Io T), Big Data Analytics, Artificial Intelligence (AI), and Robotics, manufacturers can streamline processes, enhance productivity, and foster innovation.
Enhanced Efficiency and Productivity
Optimized production processes
Optimized production processes represent a cornerstone of Industry 4.0's Impact on Manufacturing Sector, revolutionizing how products are fabricated. This approach emphasizes the utilization of real-time data and smart technologies to enhance operational efficiency and output quality. Manufacturers can achieve a higher level of precision, minimize waste, and increase overall productivity through streamlined processes. The flexibility and adaptability offered by optimized production methods cater to the dynamic demands of modern manufacturing environments.
Real-time monitoring and control
Real-time monitoring and control play a crucial role in driving efficiency and productivity within manufacturing facilities. By leveraging advanced sensors and data analytics, manufacturers can access instantaneous insights into their production processes, enabling proactive decision-making and rapid intervention when deviations occur. This real-time oversight enhances quality assurance, reduces downtime, and optimizes resource utilization. However, ensuring data accuracy and system reliability are essential considerations to maximize the benefits of real-time monitoring and control.
Quality Improvement and Innovation
Predictive maintenance
Predictive maintenance emerges as a key aspect of enhancing quality and innovation within the manufacturing sector under Industry 4.0 principles. By leveraging sensor data and machine learning algorithms, manufacturers can predict equipment failures before they occur, enabling preemptive maintenance actions to prevent costly downtime. This proactive approach not only optimizes machine performance but also extends the lifespan of assets, reducing overall maintenance costs and enhancing operational resilience.
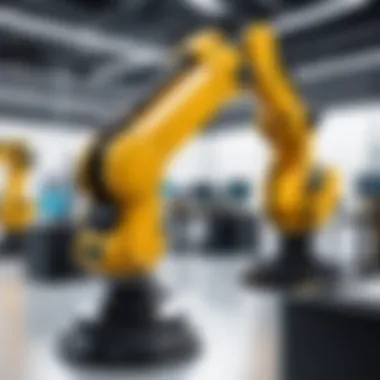
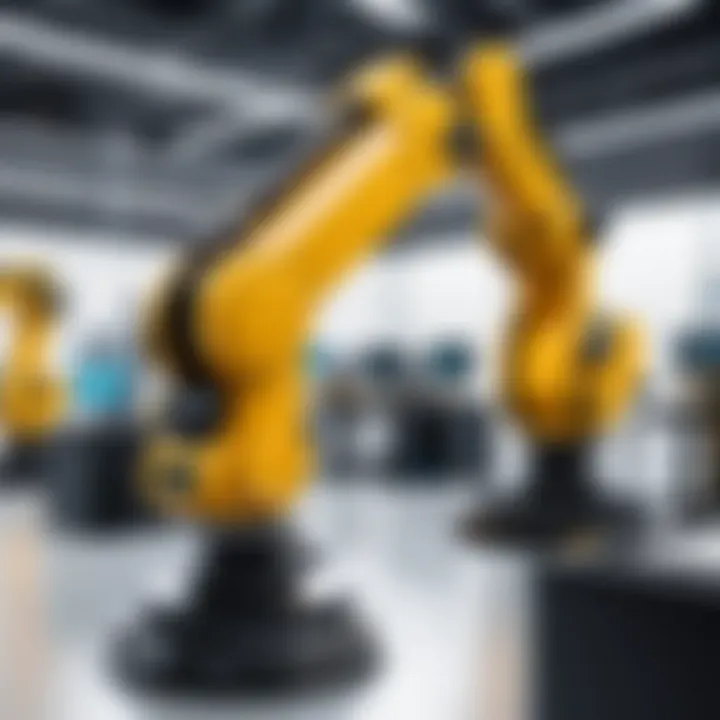
Customization and personalization
Customization and personalization represent critical elements in driving innovation and meeting consumer demands in modern manufacturing. Industry 4.0 facilitates the customization of products through flexible production processes and personalized services tailored to individual preferences. By leveraging data analytics and smart technologies, manufacturers can deliver bespoke solutions at scale, enhancing customer satisfaction and market competitiveness. However, balancing personalized production with operational efficiency and cost-effectiveness remains a key challenge in integrating this aspect into manufacturing operations.
Supply Chain Optimization
Inventory management
Efficient inventory management plays a vital role in optimizing supply chains and meeting fluctuating market demands. Industry 4.0 enables real-time inventory tracking, demand forecasting, and automated replenishment systems to ensure optimal stock levels and minimize carrying costs. By digitizing inventory processes and automating stock monitoring, manufacturers can achieve Just-In-Time (JIT) inventory management, reducing storage overheads and improving order fulfillment efficiency. However, integrating sophisticated inventory management systems necessitates robust data security measures and seamless integration with existing operational frameworks.
Logistics and distribution
Streamlining logistics and distribution processes is imperative in enabling timely product delivery and cost-effective operations. Industry 4.0 leverages automation, data analytics, and AI-driven algorithms to optimize route planning, warehouse operations, and last-mile delivery logistics. By enhancing visibility across the supply chain and implementing smart distribution strategies, manufacturers can reduce lead times, lower transportation costs, and enhance overall customer satisfaction levels. However, addressing infrastructure compatibility and workforce training needs are essential considerations when implementing advanced logistics solutions within manufacturing environments.
Challenges and Implementation
In the realm of Industry 4.0 in Manufacturing, the section on Challenges and Implementation plays a pivotal role in delineating the hurdles and opportunities that organizations face when integrating advanced technologies. It is imperative to comprehend the nuances of navigating through these challenges to unlock the full potential of Industry 4.0. Addressing issues related to data security, workforce training, and scalability is essential for a successful implementation. By focusing on meticulous planning and strategic execution, companies can harness the benefits of Industry 4.0 to enhance productivity and innovation within the manufacturing sector.
Data Security and Privacy
Cybersecurity risks
Delving into the intricate domain of data security and privacy within Industry 4.0, cybersecurity risks emerge as a critical aspect that demands meticulous attention. With the ever-evolving cyber threats and vulnerabilities in the digital landscape, safeguarding sensitive information and maintaining the integrity of data becomes paramount. Cybersecurity risks encompass various threats such as data breaches, ransomware attacks, and unauthorized access, posing significant challenges to the security of manufacturing operations. Understanding the intricate nature of these risks and implementing robust security measures are imperative to fortify the resilience of organizations against potential cyber threats.
Regulatory compliance
In the realm of Industry 4.0, regulatory compliance stands as a cornerstone in ensuring adherence to established standards and protocols governing data security and privacy. Complying with regulations such as GDPR, HIPAA, or industry-specific guidelines not only mitigates legal risks but also fosters trust among consumers and stakeholders. Upholding regulatory compliance empowers organizations to uphold data integrity, confidentiality, and accessibility, aligning with ethical principles and industry best practices for a secure operational framework. Striking a harmonious balance between innovation and compliance is essential to navigate the dynamic landscape of Industry 4.0.
Skill Gap and Workforce Training
Reskilling initiatives
Amid the technological disruptions brought forth by Industry 4.0, reskilling initiatives emerge as integral solutions to bridge the skill gap within the workforce. Empowering employees with competencies in data analytics, artificial intelligence, and automation equips them to navigate the digital transformation seamlessly. Reskilling initiatives not only enhance workforce productivity but also instill a culture of continuous learning and adaptation, driving organizational growth and competitiveness in the evolving industrial landscape.
Adapting to new technologies
As organizations transition towards embracing Industry 4.0 technologies, adapting to new technological paradigms becomes crucial for maintaining operational efficiency. Familiarizing employees with emerging technologies such Io T sensors, AI-powered analytics, and cloud-based platforms is indispensable to harnessing the full potential of Industry 4.0. Adapting to new technologies requires agile strategies, effective change management, and a culture of innovation to enable seamless integration and utilization of advanced tools and systems within the manufacturing ecosystem.
Integration and Scalability
Legacy systems compatibility
When contemplating the integration of Industry 4.0 technologies, ensuring compatibility with legacy systems emerges as a fundamental consideration for organizations. Bridging the gap between traditional infrastructure and digital innovations necessitates strategic planning and seamless integration to prevent operational disruptions and inefficiencies. Legacy systems compatibility entails evaluating legacy systems' functionality, identifying potential bottlenecks, and implementing tailored solutions to enable interoperability and synergy between existing and new technologies, fostering a harmonious digital transformation journey.
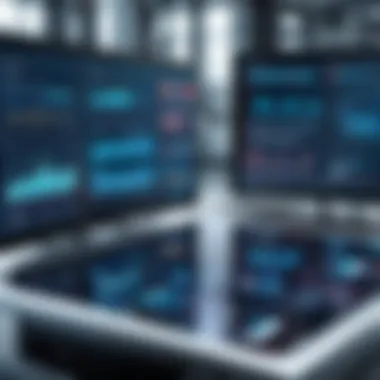
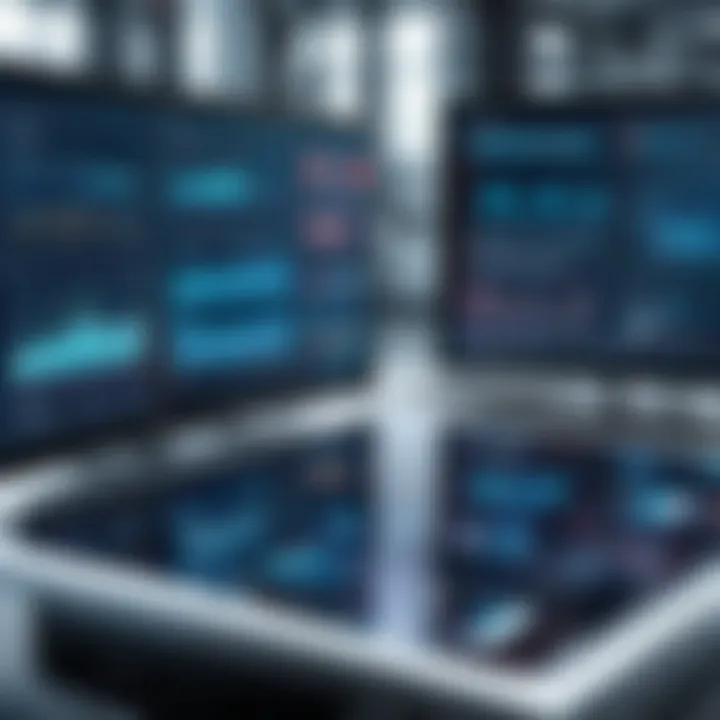
Scaling up operations
In the landscape of Industry 4.0, scaling up operations denotes the imperative act of expanding manufacturing capacities and capabilities in alignment with evolving market demands. Scalability is synonymous with flexibility, responsiveness, and resilience, enabling organizations to adapt to fluctuating market conditions, technological advancements, and consumer preferences seamlessly. Scaling up operations necessitates a robust infrastructure, agile methodologies, and proactive strategies to enhance production efficiencies, optimize resource utilization, and sustain long-term growth within the competitive manufacturing sector.
Future Trends and Prospects
Future Trends and Prospects hold a pivotal role in shaping the landscape of Industry 4.0 in the manufacturing sector. As technology advances at an exponential pace, it is imperative to delve into the emerging trends that will define the future of manufacturing processes. The integration of cutting-edge technologies like Smart Factories and Digital Twins paves the way for unprecedented efficiencies and innovations in the industrial domain. Analyzing the trajectory of future trends empowers industry players to stay ahead of the curve and capitalizing on upcoming opportunities.
Smart Factories and Digital Twins
Smart Factories and Digital Twins epitomize the essence of Industry 4.0, offering a glimpse into a highly automated and data-driven manufacturing environment. The concept of Virtual simulations within Smart Factories revolutionizes production methodologies by enabling virtual testing and prototyping of manufacturing processes. Its key characteristic lies in providing a risk-free environment for experimentation, optimizing production workflows, and enhancing product quality. The utilization of Virtual simulations in this context significantly reduces time-to-market and accelerates innovation, making it a popular choice for manufacturers aiming to streamline their operations efficiently.
Predictive maintenance models, another aspect within Smart Factories and Digital Twins, play a critical role in predictive analysis of machinery and equipment performance. By leveraging real-time data and machine learning algorithms, predictive maintenance models can forecast potential breakdowns, schedule maintenance proactively, and prevent costly downtime. Their unique feature lies in enhancing operational reliability and minimizing maintenance costs, thus increasing overall efficiency in manufacturing operations. However, there are challenges such as data accuracy and model complexity that need to be carefully navigated for optimal implementation of predictive maintenance models within manufacturing settings.
Sustainable Manufacturing Practices
Embracing Sustainable Manufacturing Practices is imperative for industries looking to minimize their environmental footprint while maximizing operational sustainability. Environmental impact reduction strategies focus on minimizing waste generation, optimizing energy consumption, and reducing carbon emissions throughout the production cycle. The key characteristic of environmental impact reduction initiatives is their ability to align profitability with environmental responsibility, making it a beneficial choice for manufacturers seeking to balance economic gains with ecological preservation. The unique feature of environmental impact reduction lies in fostering a culture of eco-consciousness and corporate social responsibility, which can enhance brand reputation and stakeholder trust.
Resource-efficient processes are instrumental in promoting sustainable manufacturing by optimizing resource utilization and minimizing resource wastage. By implementing advanced technologies such as Io T sensors and automated systems, manufacturers can achieve resource efficiency through real-time monitoring, predictive analytics, and process optimization. The key characteristic of resource-efficient processes is their capacity to drive cost savings, improve operational efficiency, and reduce environmental impact concurrently. While resource-efficient processes offer significant advantages in terms of sustainability and cost-effectiveness, challenges like initial investment costs and technology integration complexities need to be addressed for seamless adoption and integration.
Global Adoption and Standardization
Driving Global Adoption and Standardization of Industry 4.0 principles is essential for fostering a collaborative ecosystem and ensuring interoperability across international manufacturing landscapes. International collaboration facilitates knowledge exchange, best practice sharing, and collaborative innovation, which are fundamental for global industry advancement. The key characteristic of international collaboration is its ability to catalyze cross-border partnerships, leverage diverse expertise, and accelerate technological advancements on a global scale. International collaboration emerges as a beneficial choice for this article by emphasizing the interconnected nature of Industry 4.0 applications and highlighting the significance of collaboration in overcoming geographical barriers and fostering innovation.
Regulatory frameworks play a pivotal role in standardizing practices, ensuring compliance, and safeguarding ethical considerations within the Industry 4.0 realm on a global scale. By establishing regulatory guidelines and standards, countries can streamline technological implementation, mitigate risks, and enhance consumer trust in emerging technologies. The unique feature of regulatory frameworks lies in promoting industry accountability, ethical conduct, and legal compliance, which are crucial components for sustainable growth and societal acceptance of Industry 4.0 innovations. While regulatory frameworks offer clear advantages in terms of ensuring safety and regulatory adherence, challenges such as regulatory divergence between countries and regulatory compliance costs may pose obstacles that require careful navigation and strategic planning for successful implementation in the manufacturing domain.
Conclusion
In the vast landscape of Industry 4.0 in Manufacturing, the Conclusion serves as a pivotal point in understanding the transformative potential this technological revolution holds. It encapsulates the essence of adaptation and innovation, emphasizing the paradigm shift taking place in manufacturing operations worldwide. By embracing Industry 4.0 principles, companies can enhance efficiency, optimize processes, and pave the way for unprecedented growth. The Conclusion acts as a beacon, guiding businesses towards a future where smart technologies and agile strategies reign supreme.
Key Takeaways
Transformational Impact of Industry 4.
Exploring the depths of the Transformational Impact of Industry 4.0 unveils a revolutionary change in how manufacturing processes are conceptualized and executed. This aspect stands as the cornerstone of progress, enabling organizations to streamline operations, reduce costs, and unlock new revenue streams. The hallmark of this impact lies in its ability to foster seamless connectivity, real-time insights, and data-driven decision-making, revolutionizing the traditional manufacturing landscape. While challenges such as cybersecurity threats and regulatory adherence may arise, the benefits of enhanced productivity, agility, and competitiveness outweigh the risks.
Continuous Adaptation and Innovation
The concept of Continuous Adaptation and Innovation underscores the dynamic nature of Industry 4.0, emphasizing the need for perpetual evolution and creativity. By embracing a culture of adaptability, organizations can stay ahead of the curve, responding swiftly to market demands and technological advancements. This aspect champions flexibility, strategic foresight, and iterative improvement as essential drivers of success in the Industry 4.0 era. While the pace of change may pose challenges, the ability to innovate and adapt ensures resilience, sustainability, and relevance in a rapidly evolving industrial landscape.
Final Thoughts
Embracing the Future of Manufacturing
Embracing the Future of Manufacturing heralds a new era of possibilities, where traditional paradigms give way to digital innovations and cyber-physical systems. This aspect encourages companies to adopt forward-thinking approaches, integrating cutting-edge technologies to optimize operations and drive value creation. The key characteristic of this approach lies in its ability to future-proof businesses, enabling them to harness the full potential of Industry 4.0 and stay ahead of market disruptions. While initial investments and skill development may pose initial hurdles, the long-term advantages of sustainability, scalability, and market leadership make this choice indispensable.
Staying Agile in a Dynamic Landscape
Staying Agile in a Dynamic Landscape epitomizes the resilience and adaptability required to thrive amidst the complexities of modern manufacturing environments. This aspect underscores the importance of responsiveness, innovation, and strategic agility as foundational pillars for success in Industry 4.0. By cultivating a culture of agility, organizations can navigate uncertainty, seize opportunities, and mitigate risks effectively. The unique feature of this approach lies in its capacity to drive continuous improvement, foster collaboration, and empower employees to drive change. While embracing agility may necessitate a shift in mindset and operational practices, the rewards of adaptability, market responsiveness, and sustained growth make it a strategic imperative in today's volatile industrial landscape.