Unveiling Advanced Additive Manufacturing Techniques for Contemporary Applications
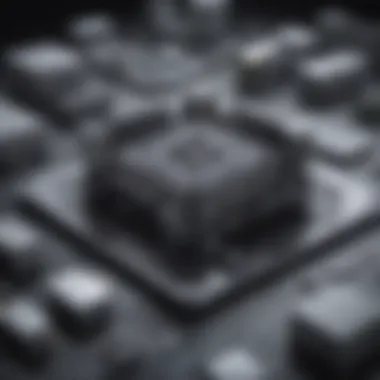
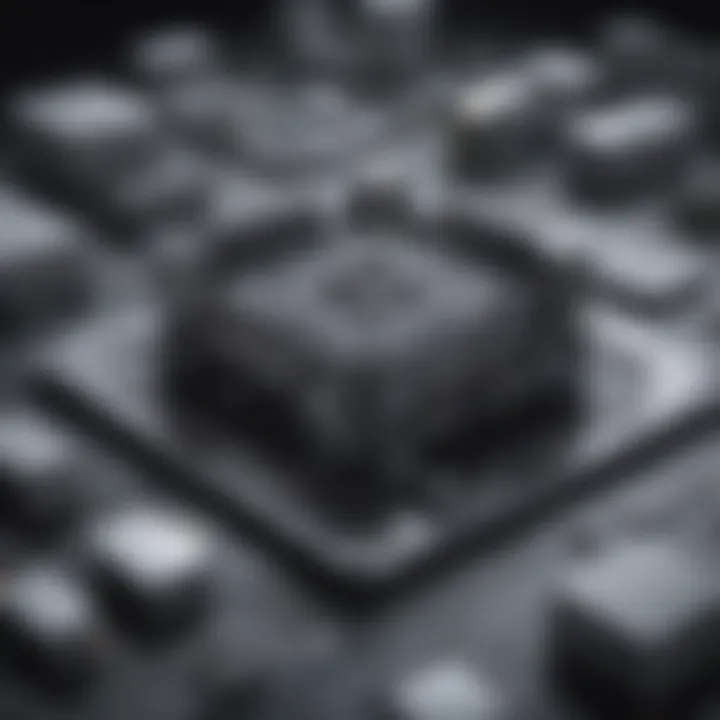
Understanding Additive Manufacturing Methods for Modern Applications
Additive manufacturing methods have transformed the landscape of modern industrial processes, ushering in a new era of innovation and efficiency. These cutting-edge technologies, such as 3D printing and selective laser sintering, play a pivotal role in various industries, offering unprecedented flexibility and precision in production.
Introduction to Additive Manufacturing
In the realm of additive manufacturing, intricacies of layer-by-layer fabrication techniques are paramount. The process involves creating three-dimensional objects from digital models, revolutionizing traditional manufacturing methods. Through the deposition of materials like plastics, metals, or ceramics, intricate designs are materialized with exceptional accuracy and detail.
Key Concepts and Terminology
To comprehend additive manufacturing fully, familiarity with key terminology is indispensable. Terms such as "extrusion," "powder bed fusion," and "stereolithography" are fundamental to grasping the nuances of these advanced techniques. Understanding the diverse materials used, ranging from polymers to composites, is crucial for navigating the intricacies of additive manufacturing processes.
Overview of Cutting-Edge Technologies
Exploring the forefront of additive manufacturing technologies unveils a vast array of possibilities. From binder jetting to electron beam melting, each technique offers unique advantages in terms of speed, cost-efficiency, and material compatibility. Embracing these technologies unlocks a world of endless potential for industries seeking enhanced productivity and innovation.
Introduction to Additive Manufacturing
Additive Manufacturing serves as a pivotal element in the landscape of modern industrial processes, offering innovative techniques that have revolutionized production methodologies. In this article, we delve deep into the essence of Additive Manufacturing, highlighting its crucial role in driving efficiency, precision, and flexibility across various industries. By exploring pioneering technologies such as 3D printing and selective laser sintering, we aim to provide a comprehensive overview of the transformative impact that Additive Manufacturing has had on the manufacturing sector.
Understanding Additive Manufacturing
Definition and Principles
Additive Manufacturing, commonly known as 3D printing, embodies a distinctive approach to fabrication, wherein objects are constructed layer by layer from digital designs. This method revolutionizes traditional manufacturing by enabling complex geometries and rapid prototyping. The inherent flexibility and customization potential make Additive Manufacturing a preferred choice for producing intricate components in industries ranging from aerospace to biomedical engineering.
Evolution of Additive Manufacturing
The evolution of Additive Manufacturing has witnessed a profound shift from prototyping to direct part production, signaling a paradigm transformation in manufacturing practices. Through advancements in materials science and process control, Additive Manufacturing has overcome initial limitations to now encompass diverse applications, including functional end-use parts. This progression underscores the adaptability and innovation driving the widespread adoption of Additive Manufacturing as a viable alternative to conventional manufacturing methods.
Importance in Modern Industries
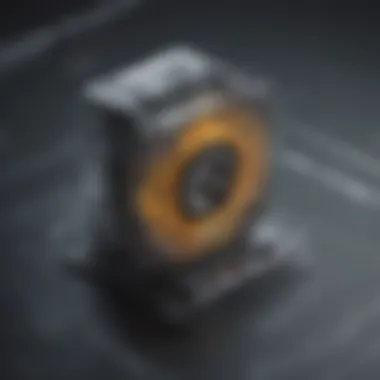

Advantages Over Traditional Manufacturing
The advantages of Additive Manufacturing over traditional methods are multifaceted, with benefits spanning reduced material wastage, accelerated product development cycles, and enhanced design freedom. By eliminating the need for specialized tooling and reducing assembly steps, Additive Manufacturing streamlines production workflows and drives cost efficiencies while facilitating intricate geometries that were previously unfeasible through subtractive processes.
Impact on Production Efficiency
The transformative impact of Additive Manufacturing on production efficiency is evident in its ability to enable rapid iteration, customization, and on-demand manufacturing. By decentralizing production and shifting towards agile manufacturing models, businesses can respond swiftly to shifting market demands, minimize inventory costs, and enhance supply chain resilience. The integration of Additive Manufacturing technologies catalyzes a paradigm shift towards leaner, more adaptable manufacturing frameworks, positioning industries for sustained growth and innovation.
Key Additive Manufacturing Techniques
Additive manufacturing techniques play a pivotal role in modern industrial processes, revolutionizing the way products are designed and manufactured. By utilizing innovative methods such as 3D printing and selective laser sintering, companies can achieve greater flexibility, precision, and efficiency in their production operations. These techniques are at the forefront of technological advancements in manufacturing, offering a wide range of benefits that enhance product quality and reduce time-to-market. Understanding the significance of key additive manufacturing techniques is essential for businesses looking to stay competitive and adaptive in the dynamic industrial landscape.
Fused Deposition Modeling (FDM)
Process Overview
Fused Deposition Modeling (FDM) is a process that involves depositing layers of thermoplastic materials to create a 3D object. This additive manufacturing method is known for its simplicity and cost-effectiveness, making it a popular choice for rapid prototyping and low-volume production. The key characteristic of FDM is its ability to produce complex geometries with ease, allowing designers to bring their concepts to life efficiently. Despite its advantages in terms of speed and affordability, FDM may have limitations in achieving high surface finish quality compared to other techniques.
Applications in Prototyping and Production
The applications of Fused Deposition Modeling (FDM) span across various industries, with particular relevance in prototyping and small-scale production. Its versatility and quick iteration process make it ideal for creating prototypes to test form, fit, and functionality before full-scale manufacturing. Additionally, FDM is utilized in the production of customized parts, tools, jigs, and fixtures where rapid turnaround and cost-effectiveness are critical factors. While FDM excels in producing functional prototypes and low-volume parts, it may not be suitable for applications requiring high accuracy and intricate detailing.
Stereolithography (SLA)
Principles and Workflow
Stereolithography (SLA) is an additive manufacturing technique that uses photopolymerization to solidify liquid resin into precise, high-resolution 3D objects. The key characteristic of SLA lies in its ability to produce parts with exceptional surface quality and fine details, making it suitable for applications that demand superior aesthetic appearance. SLA's workflow involves a resin vat, a movable platform, and a UV laser that selectively cures the resin layer by layer, resulting in intricately fabricated components. While SLA offers unmatched accuracy and surface finish, its main drawback is the limited material selection compared to other technologies.
Medical and Dental Applications
Within the medical and dental fields, Stereolithography (SLA) has found extensive applications due to its ability to produce customized implants, prosthetics, and surgical guides. The precision and biocompatibility of SLA-produced parts make them ideal for use in patient-specific medical treatments and devices. From dental crowns to anatomical models, SLA contributes to improving patient care by offering tailored solutions with high accuracy and reliability. However, the cost and material limitations of SLA may pose challenges in certain medical and dental applications that require specific material properties.

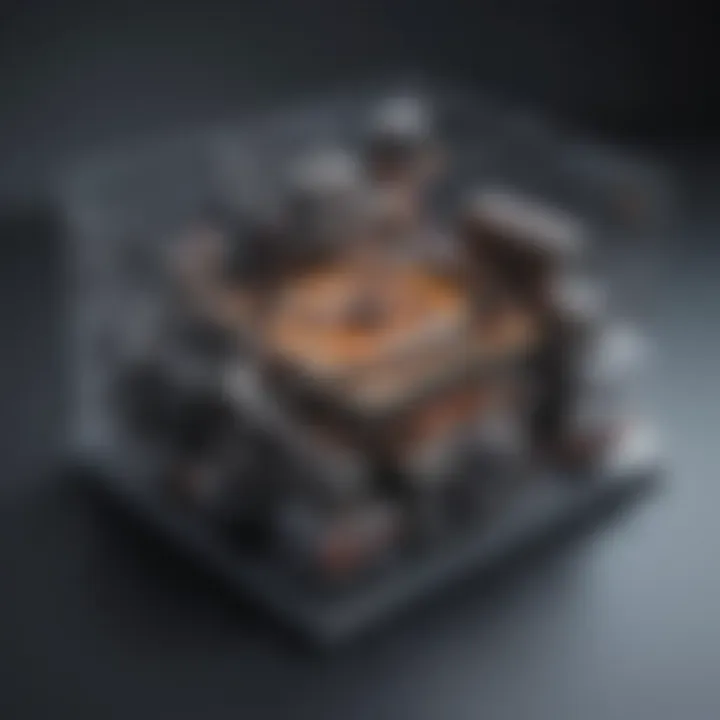
Selective Laser Sintering (SLS)
Powder Bed Fusion Process
Selective Laser Sintering (SLS) is a powder bed fusion process that utilizes a high-powered laser to sinter powdered materials, such as nylon or metal, into solid 3D objects. The key characteristic of SLS lies in its ability to produce strong, durable parts with complex geometries and excellent mechanical properties. This makes SLS ideal for applications in industries like aerospace and automotive, where lightweight yet robust components are crucial. Despite its advantages in material diversity and part strength, SLS may have limitations in achieving fine surface details and may require additional post-processing for certain applications.
Aerospace and Automotive Utilization
The aerospace and automotive sectors benefit significantly from the capabilities of Selective Laser Sintering (SLS) in producing lightweight structural components and functional parts. SLS enables the rapid prototyping of complex geometries, optimizing designs for weight reduction and performance enhancement. In aerospace, SLS is utilized for creating components like brackets, housings, and ducting systems, contributing to overall fuel efficiency and aircraft sustainability. Similarly, in the automotive industry, SLS is employed to manufacture parts such as engine components, brackets, and interior fittings, showcasing the versatility and reliability of this additive manufacturing technique.
Direct Metal Laser Sintering (DMLS)
Metal Additive Manufacturing
Direct Metal Laser Sintering (DMLS) is a cutting-edge additive manufacturing process that enables the production of metal parts with exceptional precision and mechanical properties. The key characteristic of DMLS is its ability to directly sinter metal powder using a high-power laser, allowing for the creation of complex, fully dense components. This technique is favored for applications requiring high strength, corrosion resistance, and thermal conductivity, making it indispensable in industries like aerospace, healthcare, and precision engineering. While DMLS offers unparalleled capabilities in metal additive manufacturing, challenges such as material waste and post-processing requirements need to be considered for optimal utilization.
Precision Engineering Applications
In precision engineering, Direct Metal Laser Sintering (DMLS) finds extensive applications in manufacturing intricate components, tooling inserts, and functional prototypes. Its ability to produce parts with tight tolerances and complex geometries enhances the efficiency and reliability of precision engineering processes. DMLS is particularly valued for its capacity to fabricate parts in materials like titanium, stainless steel, and cobalt chrome, meeting the stringent requirements of industries that demand exceptional mechanical properties and geometrical accuracy. While DMLS offers unmatched precision and material strength, its high initial investment and operating costs may pose challenges for small-scale productions.
Innovations in Additive Manufacturing
Innovations in Additive Manufacturing play a pivotal role in driving technological advancements. This section sheds light on groundbreaking developments revolutionizing modern industrial processes. From bioprinting to advanced materials, these innovations enhance efficiency, precision, and functionality in additive manufacturing techniques. By exploring cutting-edge research and applications, this article aims to showcase the transformative potential of these technological innovations.
Bioprinting and Tissue Engineering
Organ Fabrication
Organ Fabrication stands at the forefront of medical innovation, enabling the production of customized organs for transplantation. The key characteristic of Organ Fabrication lies in its ability to create complex biological structures with precise functionality. This aspect is particularly beneficial for addressing organ scarcity issues, offering a viable solution for patients in need of organ transplants. The unique feature of Organ Fabrication is its ability to replicate patient-specific anatomical structures, reducing the risk of rejection post-transplantation while improving overall health outcomes.
Clinical Implications
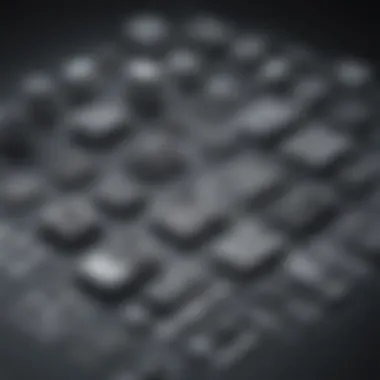
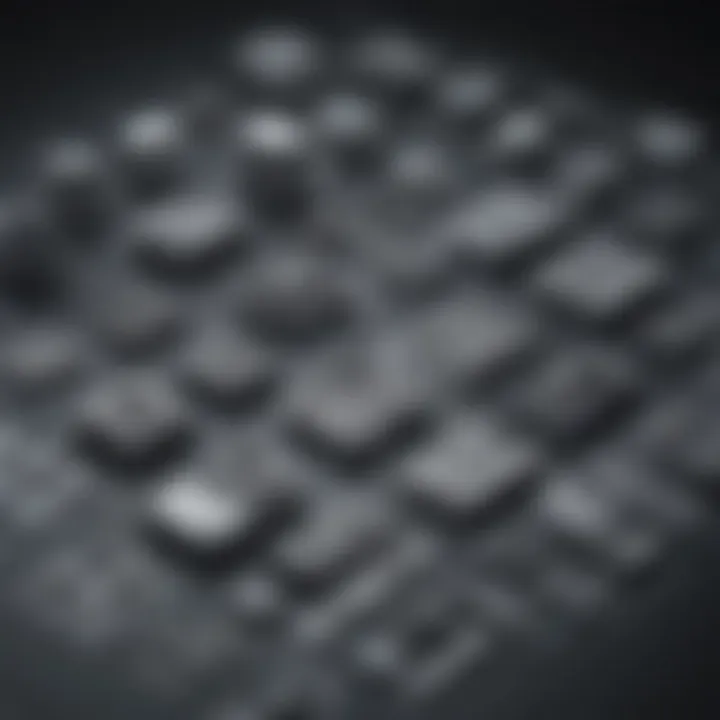
The Clinical Implications of bioprinting and tissue engineering are vast, encompassing improved patient outcomes and personalized medical treatments. Emphasizing the convergence of technology and healthcare, Clinical Implications highlight the potential for tailored therapies based on individual patient needs. This aspect serves as a valuable tool for medical professionals, offering enhanced precision in treatment planning and execution. Despite its advantages in customizability and efficacy, Clinical Implications also pose challenges related to regulatory approval and scalability, which are vital considerations in integrating these innovations into mainstream healthcare practices.
Nanocomposites and Advanced Materials
Enhanced Mechanical Properties
Enhanced Mechanical Properties represent a significant advancement in material science, delivering unparalleled strength and durability to manufactured components. The key characteristic of these materials lies in their ability to withstand high stress environments while maintaining structural integrity. This feature is highly beneficial in industries requiring robust and resilient materials for diverse applications, ranging from aerospace to automotive sectors. The unique feature of Enhanced Mechanical Properties is their flexibility in design and compatibility with additive manufacturing processes, enhancing the production of complex geometries with superior mechanical performance.
Electronics and Wearable Technology
Electronics and Wearable Technology represent a fusion of traditional electronics with additive manufacturing, enabling the production of smart devices and wearables with enhanced functionality. The key characteristic of these applications is their integration of tech components into lightweight and ergonomic designs, catering to consumer preferences for portable and multifunctional gadgets. This amalgamation offers benefits such as real-time data monitoring, connectivity, and customized features tailored to individual user needs. Despite their advantages in terms of innovation and user experience, Electronics and Wearable Technology face challenges in terms of power consumption optimization and regulatory compliance, requiring continual research and development efforts to meet evolving technological demands.
Challenges and Future Prospects
In the realm of additive manufacturing methods, the challenges and future prospects play a critical role in shaping the trajectory of this innovative technology. Addressing these aspects is fundamental to understanding the evolution and impact of additive manufacturing in modern applications. By delving into the challenges and prospects, we gain insights into the hurdles that need to be overcome and the potential advancements that can revolutionize various industries.
Regulatory Hurdles and Quality Control
Regulatory hurdles and quality control are paramount in ensuring the efficacy and safety of additive manufacturing processes. Within the context of this article, scrutiny is placed on the stringent regulations governing this technology, emphasizing the need for standards to uphold quality and reliability.
Standardization Efforts
Standardization efforts hold a pivotal role in harmonizing practices and benchmarks within the additive manufacturing landscape. By discussing the nuances of standardization in this article, we uncover how adherence to predefined protocols enhances interoperability and facilitates seamless integration across diverse manufacturing settings. The distinct characteristic of standardization lies in its ability to streamline operations and promote uniformity, making it a favored choice for advancing additive manufacturing methodologies.
Certification Processes
Certification processes serve as the gatekeepers of quality assurance in additive manufacturing. Examining the certification protocols within this piece sheds light on the meticulous procedures designed to validate the precision and performance of printed components. The unique feature of certification lies in its ability to instill confidence in end-users, certifying product integrity while highlighting areas for enhancement. Understanding the advantages and disadvantages of certification processes in this article offers a nuanced perspective on their pivotal role in ensuring additive manufacturing excellence.
Industry Integration
The integration of Industry 4.0 principles is a transformative aspect in the landscape of additive manufacturing. Emphasizing this integration within the article underscores the synergistic relationship between smart technologies and manufacturing processes, heralding a new era of efficiency and adaptability.
Automation and Smart Manufacturing
Automation and smart manufacturing revolutionize the production landscape by infusing intelligence and autonomy into manufacturing systems. Within the context of this article, we explore how automation optimizes workflows, minimizes errors, and accelerates production cycles. The key characteristic of automation lies in its ability to enhance productivity and precision, making it a sought-after solution for streamlining additive manufacturing operations.
IoT and Data Analytics
The convergence of IoT and data analytics empowers additive manufacturing with real-time insights and predictive capabilities. Unpacking this fusion in the article elucidates the role of data-driven decision-making in optimizing production processes and driving innovation. The unique feature of IoT and data analytics lies in their ability to deliver actionable intelligence, enabling manufacturers to proactively address challenges and capitalize on emerging opportunities. By examining the advantages and disadvantages of IoT and data analytics in this context, we gain a comprehensive understanding of their relevance in propelling additive manufacturing towards unprecedented advancements.