Enhancing Operational Efficiency: The Significance of Lean System Integration
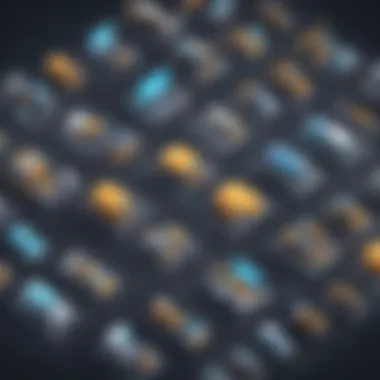
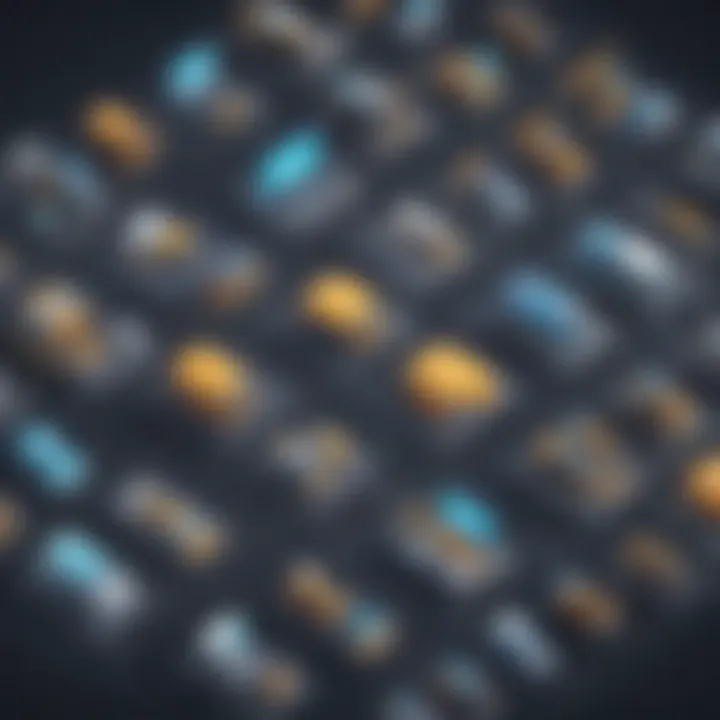
Understanding Lean System in Operations Management
In the realm of operations management, the concept of lean system plays a pivotal role in enhancing efficiency and productivity. It involves the systematic identification and elimination of non-value-added activities within a company's processes, focusing on creating value for the end customer. Lean principles, rooted in continuous improvement and waste reduction, have been proven to streamline operations and drive sustainable growth across various industries.
Key Principles of Lean System
The key principles of lean system in operations management revolve around maximizing customer value while minimizing waste. This includes identifying and eliminating various forms of waste such as overproduction, defects, waiting times, unnecessary transportation, excess inventory, motion, and underutilized talent. By establishing a culture of continuous improvement, organizations can optimize their processes, improve product quality, and enhance overall efficiency.
Strategies for Implementing Lean Practices
Implementing lean practices involves a strategic approach towards process optimization. This can include value stream mapping to identify value-adding and non-value-adding activities, establishing pull systems to regulate workflow based on customer demand, implementing just-in-time production to minimize inventory holding costs, and fostering a culture of employee empowerment and involvement. By incorporating these strategies, businesses can enhance their operational performance and adapt to changing market dynamics effectively.
Importance of Lean System in Today's Business Landscape
In today's competitive business landscape, the implementation of lean system is essential for organizations looking to gain a competitive edge. By optimizing operations, reducing lead times, increasing flexibility, and improving product quality, companies can not only meet customer expectations but also drive innovation and sustainable growth. Embracing lean principles leads to a more agile and responsive organization, capable of thriving in dynamic and uncertain market environments.
Introduction to Lean System in Operations Management
In the realm of operations management, the introduction to Lean System stands as a pinnacle of efficiency and productivity optimization. This article delves into the core significance of embracing Lean methodologies to streamline operations and foster sustainable growth across diverse industries. By adopting Lean principles, organizations can revolutionize their operational frameworks, eliminate wasteful practices, and continuously enhance processes to meet evolving market demands and customer expectations.
Understanding Lean Principles
The foundation of lean thinking
The foundation of lean thinking lies in the relentless pursuit of value optimization and waste reduction within operational workflows. This core principle emphasizes the necessity of identifying and amplifying value-adding processes while eradicating non-value adding activities. By focusing on efficiency and resource utilization, the foundation of lean thinking empowers organizations with the tools to enhance operational effectiveness and drive competitive advantage.
Elimination of waste
A fundamental tenet of Lean System is the elimination of waste at all levels of operation. By targeting inefficiencies, bottlenecks, and unnecessary processes, organizations can streamline their workflows and allocate resources more effectively. This emphasis on waste reduction ensures that operations run smoothly, costs are minimized, and quality standards are upheld to deliver optimal value to customers.
Continuous improvement
Continuous improvement forms the bedrock of Lean practices, advocating for an organizational culture that values innovation, adaptability, and growth. By fostering an environment where every employee is encouraged to contribute ideas, identify bottlenecks, and suggest improvements, companies can drive ongoing enhancements in processes, products, and services. The pursuit of excellence through continuous improvement enables firms to stay ahead in dynamic market landscapes and meet changing consumer needs effectively.
Historical Evolution of Lean System
Ideas from Toyota Production System
The genesis of Lean System can be traced back to the pioneering concepts of the Toyota Production System (TPS). By revolutionizing manufacturing practices with principles like Just-In-Time production and autonomous maintenance, TPS set the stage for Lean methodologies to flourish globally. The emphasis on waste elimination, employee empowerment, and process optimization from TPS continues to inspire organizations seeking operational excellence and sustainable growth.
Spread of lean concepts globally
The global dissemination of Lean concepts represents a paradigm shift in how organizations approach operational efficiency and productivity. As Lean principles transcended borders and industries, they sparked a transformative wave of process optimization and performance enhancement. By embracing Lean practices on a global scale, companies can adapt to market dynamics, leverage best practices, and drive innovation in their operational frameworks.
Benefits of Implementing Lean Practices
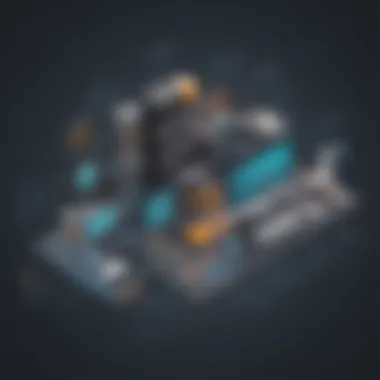
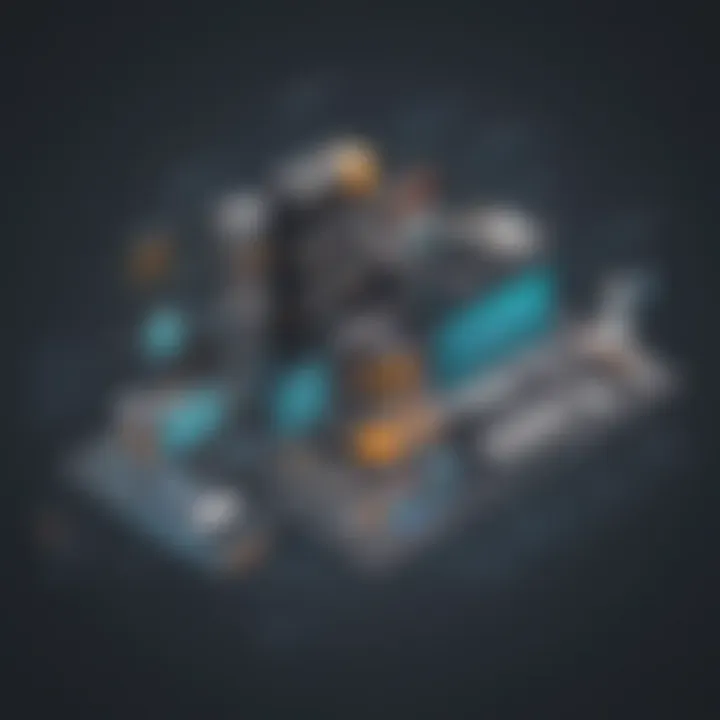
Enhanced operational efficiency
One of the paramount benefits of implementing Lean practices is the realization of enhanced operational efficiency. By streamlining processes, minimizing waste, and empowering employees to contribute to process improvements, organizations can optimize their resource utilization, increase output quality, and drive overall efficiency. This heightened operational efficiency equips companies with the agility and resilience needed to navigate competitive markets effectively.
Reduced lead times
Reducing lead times is a crucial advantage of Lean implementation, allowing organizations to respond swiftly to market demands and customer needs. By eliminating bottlenecks, optimizing production schedules, and improving workflow coordination, companies can shorten the time required to deliver products or services. This reduction in lead times not only enhances customer satisfaction but also enables firms to capitalize on market opportunities promptly.
Improved quality standards
Through the adoption of Lean practices, organizations can elevate their quality standards to exceed customer expectations consistently. By prioritizing quality at every stage of the production process, focusing on error-proofing mechanisms, and promoting a culture of continuous improvement, companies can achieve unparalleled levels of product integrity and customer satisfaction. Improved quality standards become a hallmark of organizations that embrace Lean methodologies, driving loyalty and trust among their clientele.
Key Strategies for Lean Implementation
In the realm of operations management, the key strategies for Lean implementation play a crucial role in optimizing processes and driving efficiency. These strategies, such as Value Stream Mapping, Just-In-Time Inventory Management, and Kaizen Philosophy, form the backbone of Lean methodologies. They highlight the importance of identifying value-adding processes, minimizing inventory holdings, and fostering a culture of continuous improvement. By integrating these strategies, organizations can streamline operations, reduce lead times, and enhance overall quality.
Value Stream Mapping
Identification of Value-Adding Processes
The identification of value-adding processes within Value Stream Mapping holds significant importance in Lean implementation. This aspect focuses on recognizing activities that directly contribute to value creation for the end customer. By pinpointing these processes, organizations can eliminate inefficiencies, reduce waste, and enhance productivity. The key characteristic of this process lies in its ability to provide a clear visual representation of the entire production flow, enabling stakeholders to identify bottlenecks and areas for improvement. Although it requires detailed analysis and documentation, the benefits of identifying value-adding processes far outweigh the initial investment. Organizations can optimize their operations, improve customer satisfaction, and drive sustainable growth.
Elimination of Non-Value Adding Activities
In Lean implementation, the elimination of non-value adding activities is a crucial step towards operational efficiency. This process focuses on removing tasks that do not directly contribute to the final product or service. By cutting down on wasteful activities, organizations can streamline their processes, reduce costs, and increase overall productivity. The key characteristic of this approach is its emphasis on lean principles such as minimizing inventory, optimizing resource utilization, and enhancing workflow efficiency. While the initial removal of non-value adding activities may require substantial effort, the long-term advantages, including improved lead times and enhanced quality standards, make it a valuable choice for organizations looking to adopt Lean practices.
Just-In-Time Inventory Management
Minimization of Inventory Holding Costs
The minimization of inventory holding costs is a critical aspect of Just-In-Time (JIT) Inventory Management in Lean operations. This strategy focuses on maintaining minimal inventory levels to meet customer demand while reducing storage and carrying costs. By implementing JIT principles, organizations can optimize their supply chains, improve inventory turnover, and enhance cash flow. The key characteristic of minimizing inventory holding costs is its ability to create a lean and responsive production system where goods are produced only as needed. While this approach requires careful coordination and a high level of supply chain visibility, the benefits of reduced waste, increased efficiency, and cost savings make it a popular choice for organizations seeking to streamline their operations.
Reduction of Lead Times
Another key aspect of JIT Inventory Management is the reduction of lead times, which plays a significant role in Lean operations. By minimizing the time it takes to fulfill orders and deliver products to customers, organizations can improve customer satisfaction, increase agility, and respond more effectively to market demands. The key characteristic of this strategy is its focus on process optimization, workflow efficiency, and the elimination of bottlenecks that cause delays. While reducing lead times may present challenges in terms of coordination and synchronization, the advantages of improved responsiveness, enhanced competitive edge, and operational flexibility make it a beneficial choice for organizations embracing Lean practices.
Kaizen Philosophy
Cultivating a Culture of Continuous Improvement
At the heart of Lean operations lies the Kaizen Philosophy, which emphasizes the importance of fostering a culture of continuous improvement. This approach focuses on empowering employees at all levels to identify, analyze, and solve problems proactively. By instilling a mindset of constant refinement and innovation, organizations can drive sustainable growth, enhance employee engagement, and adapt to evolving market dynamics. The key characteristic of this philosophy is its emphasis on incremental changes, continuous learning, and employee involvement in decision-making processes. While cultivating a culture of continuous improvement requires dedication, investment in training, and open communication channels, the long-term benefits of enhanced productivity, innovation, and organizational resilience make it a valuable choice for organizations committed to excellence.
Involvement of All Employees in Problem-Solving
Another vital aspect of the Kaizen Philosophy is the involvement of all employees in problem-solving activities. By empowering frontline workers to identify and address issues in real-time, organizations can create a more agile and responsive operational environment. The key characteristic of this approach is its focus on decentralizing decision-making, encouraging collaboration, and fostering a shared sense of responsibility for problem resolution. While involving all employees in problem-solving may require a culture shift and training initiatives, the advantages of increased engagement, empowerment, and operational efficiency make it a valuable strategy for organizations seeking to embed Lean principles into their daily operations.
Challenges in Implementing Lean Practices
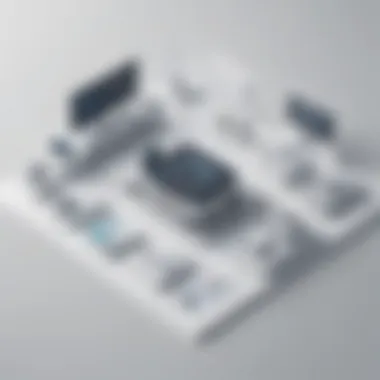
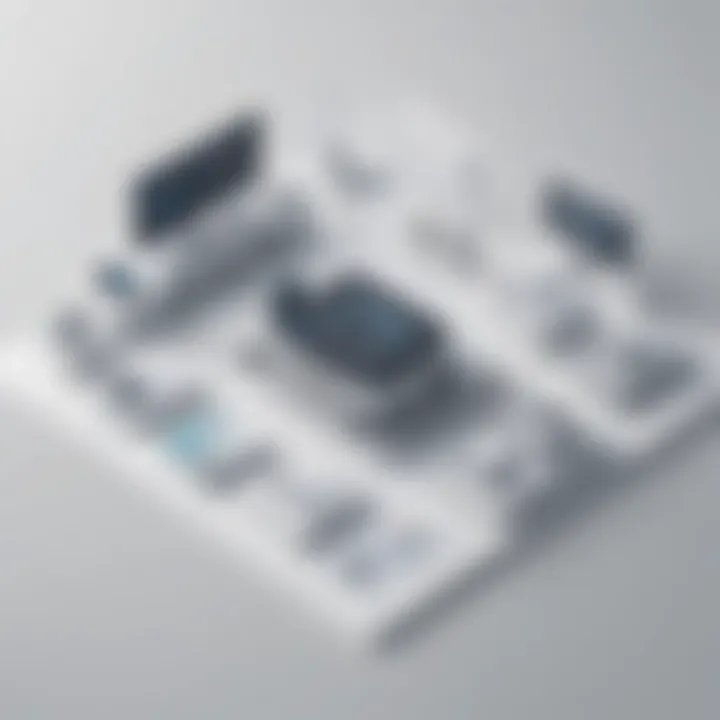
When delving into the realm of optimizing operations through the lens of Lean System in Operations Management, one cannot overlook the critical importance of addressing the challenges that accompany the implementation of Lean practices. These challenges serve as significant hurdles that organizations must navigate to unlock the full potential of Lean methodologies. Among the specific elements that make challenges in implementing Lean Practices a pivotal topic are the potential benefits of streamlining operations, reducing inefficiencies, and fostering a culture of continuous improvement. Additionally, considerations surrounding the financial investments required, the need for comprehensive training programs, and the long-term commitment necessary to sustain Lean practices over time underscore the complexities involved in this facet of operations management.
Resistance to Change
Overcoming employee reluctance
Within the spectrum of resistance to change lies the nuanced issue of overcoming employee reluctance, a crucial aspect in steering organizations towards successful Lean implementation. The key characteristic of focusing on employee buy-in and participation highlights the significance of aligning organizational goals with individual motivations to cultivate a culture of engagement and commitment. Overcoming employee reluctance stands as a popular choice for this article due to its direct impact on operational efficiency and the overall success of Lean initiatives. The unique feature of personalized change management strategies tailored to employees' concerns and aspirations showcases the tailored approach required to address resistance effectively.
Addressing organizational inertia
Addressing organizational inertia serves as another dimension in the landscape of implementing Lean practices wherein entrenched processes and traditional mindsets act as impediments to transformation. The key characteristic of facilitating organizational restructuring and realignment emphasizes the fundamental shift required to embed Lean principles within the organizational DNA. Addressing organizational inertia is a beneficial choice for this article as it sheds light on the structural adjustments needed to drive sustainable change effectively. The unique feature of leveraging leadership buy-in and grassroots movements highlights the multifaceted approach required to combat institutional resistance.
Resource Constraints
Investment requirements for lean transformation
Navigating the terrain of Lean implementation entails grappling with the financial implications encapsulated in investment requirements for lean transformation. The key characteristic of balancing short-term costs with long-term gains underscores the strategic planning necessary to allocate resources judiciously and maximize the returns on Lean investments. Investment requirements for lean transformation assume significance within this article as they elucidate the financial commitments essential for driving operational efficiency and continuous improvement. The unique feature of incentivizing investments through calculated ROI projections showcases the proactive approach organizations can adopt to secure funding for Lean initiatives.
Training costs
Training costs present a distinctive challenge within the realm of Lean implementation, necessitating organizations to allocate resources for upskilling employees and fostering a culture of learning and development. The key characteristic of investing in employee competence and skill enhancement underscores the pivotal role that knowledge transfer plays in embedding Lean practices within the workforce. Training costs are a pertinent choice for this article as they spotlight the educational investments required to empower employees with the tools and techniques essential for Lean success. The unique feature of utilizing blended learning methodologies and mentorship programs accentuates the multifaceted approach needed to bridge the skills gap and facilitate organizational growth through continuous learning.
Sustaining Lean Practices Over Time
Preventing regression to old habits
In the context of Lean practices, preventing regression to old habits emerges as a critical consideration when aiming to institutionalize Lean methodologies and prevent backsliding into previous operational paradigms. The key characteristic of establishing feedback loops and performance monitoring mechanisms underscores the vigilance required to identify signs of regression and address them proactively. Preventing regression to old habits is a beneficial choice for this article as it highlights the ongoing efforts needed to maintain the momentum of Lean initiatives and safeguard against complacency. The unique feature of fostering a culture of accountability and transparent communication exemplifies the foundation upon which sustainable Lean practices can thrive.
Ensuring long-term commitment to continuous improvement
Ensuring long-term commitment to continuous improvement acts as the cornerstone for sustaining Lean practices over time and fostering a culture of perpetual advancement. The key characteristic of embedding Kaizen principles and fostering innovation at all levels emphasizes the transformative power of continuous improvement in driving organizational success. Ensuring long-term commitment to continuous improvement resonates within this article as it illuminates the mindset shifts and structural changes required to engrain Lean practices into the organizational fabric for lasting impact. The unique feature of instituting cross-functional collaboration and knowledge sharing underscores the collaborative ethos essential for nurturing a culture of continuous improvement and innovation.
Case Studies Illustrating Lean Success Stories
Case studies illustrating lean success stories play a crucial role in shedding light on the practical applications and outcomes of lean principles in real-world settings. These in-depth analyses provide invaluable insights into how organizations have leveraged lean methodologies to enhance operational efficiency and drive sustainable growth. By examining successful implementations of lean practices, readers can glean specific strategies, challenges faced, and impactful results achieved across various industries.
Toyota: Pioneering Lean Manufacturing
Lean principles at the core of Toyota's operations
Delving into Toyota's pioneering approach to lean manufacturing reveals a fundamental commitment to efficiency and waste reduction. At the heart of Toyota's operations lies a steadfast dedication to the continuous improvement of processes, exemplifying the core tenets of lean thinking. The meticulous attention to detail and emphasis on value creation distinguish Toyota's implementation of lean principles, setting a benchmark for operational excellence within the industry. By prioritizing the elimination of waste and fostering a culture of relentless improvement, Toyota has established itself as a trailblazer in lean manufacturing.
Impact on competitiveness and innovation
The impact of lean practices on Toyota's competitiveness and innovation is profound, reshaping industry standards and driving sustained growth. By embedding lean principles into its operations, Toyota has achieved unparalleled levels of efficiency and effectiveness, bolstering its competitive edge in the market. The relentless pursuit of improvement and optimization has not only enhanced Toyota's operational performance but also fueled a culture of innovation that continues to drive the company's success. By prioritizing lean thinking and continuous improvement, Toyota has not only remained competitive but has also set new benchmarks for operational excellence and innovation.
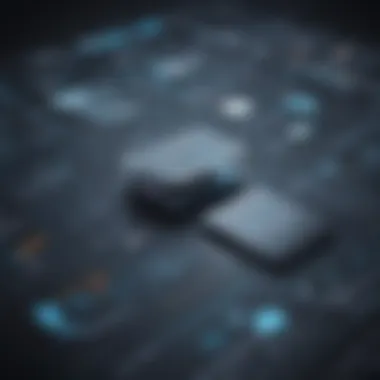
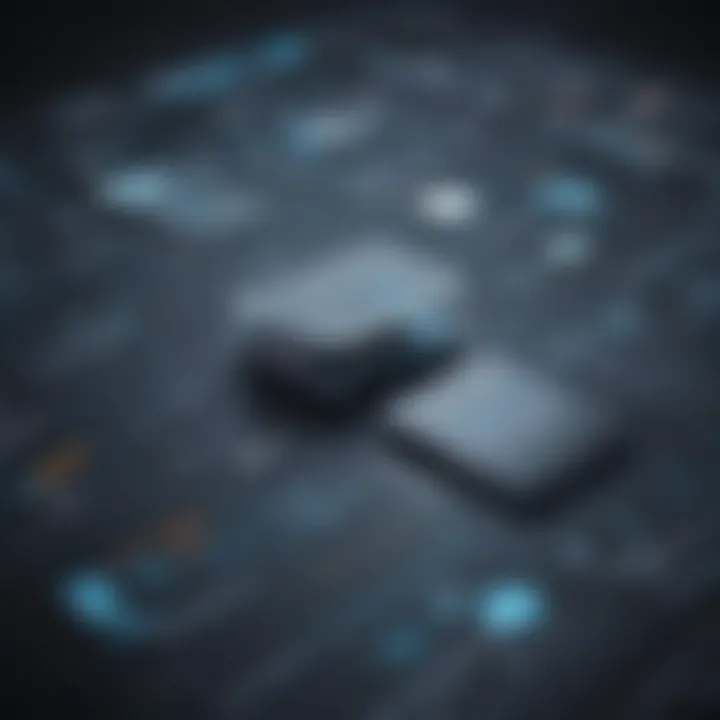
Amazon: Lean in E-Commerce Fulfillment
Application of lean concepts in warehouse management
Amazon's successful integration of lean concepts in warehouse management underscores the transformative impact of lean principles on e-commerce fulfillment. By implementing efficient inventory management and optimizing warehouse operations, Amazon has streamlined its logistics processes, minimizing delays and maximizing operational throughput. The meticulous application of lean principles in warehouse management has enabled Amazon to meet customer demands with precision and speed, setting a new standard for efficiency in e-commerce fulfillment.
Efficiency gains and customer satisfaction
The efficiency gains and enhanced customer satisfaction resulting from Amazon's lean practices showcase the tangible benefits of implementing lean methodologies. By reducing lead times, eliminating bottlenecks, and optimizing resource utilization, Amazon has elevated the customer experience and solidified its reputation as a leader in e-commerce fulfillment. The customer-centric approach enabled by lean principles has not only improved operational efficiency but also fostered long-term customer loyalty and satisfaction, driving sustainable growth for the company.
Tesla: Lean in Agile Manufacturing
Integration of lean principles with agile production
Tesla's innovative integration of lean principles with agile manufacturing exemplifies a dynamic approach to production optimization and flexibility. By combining lean methodologies with agile principles, Tesla has fostered a manufacturing environment that thrives on responsiveness and adaptability. The seamless integration of lean practices with agile processes has empowered Tesla to rapidly iterate on its production lines, respond to market changes swiftly, and maintain high levels of manufacturing efficiency.
Flexibility and responsiveness in manufacturing
The emphasis on flexibility and responsiveness in Tesla's manufacturing processes underscores the transformative potential of lean strategies in agile settings. By embracing lean principles that prioritize waste reduction, continuous improvement, and value creation, Tesla has cultivated a production ecosystem that is capable of swiftly adapting to evolving customer demands and market dynamics. The inherent flexibility and responsiveness ingrained in Tesla's lean-agile hybrid approach not only enhance operational efficiency but also position the company as a trailblazer in agile manufacturing practices.
Future Trends in Lean Operations Management
In exploring the future trends in lean operations management, it is crucial to understand the evolving landscape of operational efficiency and productivity. The integration of lean principles with digital technologies represents a significant advancement in optimizing operations. Combining lean methodologies with Industry 4.0 practices is paramount for businesses aiming to stay competitive in modern markets. This fusion not only enhances process efficiency but also enables companies to leverage automation and data analytics for informed decision-making.
Digital Transformation and Industry
Integration of lean with digital technologies
Discussing the integration of lean with digital technologies sheds light on the seamless marriage between traditional lean practices and innovative digital solutions. This convergence streamlines operational processes by digitizing manual tasks, reducing errors, and improving real-time monitoring. The key characteristic of this integration lies in its ability to enhance overall operational visibility and control. Implementing digital tools in lean operations can drive operational excellence by providing data-driven insights for continuous improvement initiatives. However, the potential downside of over-reliance on digital technologies could lead to a disconnect from the human element in operations.
Smart manufacturing and automation
Exploring smart manufacturing and automation within the context of lean operations management reveals a fundamental shift towards efficient and adaptive production processes. Smart manufacturing leverages cutting-edge technologies like IoT sensors, AI, and robotics to optimize production workflows and minimize resource wastage. The key characteristic of smart manufacturing is its emphasis on real-time data analytics and predictive maintenance to proactively address production challenges. While this approach significantly improves operational efficiency and cost-effectiveness, the reliance on automation may pose challenges in terms of employee skill development and job displacement.
Sustainability and Environmental Management
Considering sustainability and environmental management in lean operations showcases a growing emphasis on green practices and eco-friendly initiatives in modern businesses. Green lean initiatives prioritize environmentally conscious decision-making, aiming to minimize waste generation and promote renewable energy usage. The key characteristic of green lean initiatives is their focus on promoting sustainable practices that reduce the organization's carbon footprint. Embracing green initiatives can not only enhance corporate social responsibility but also lead to cost savings through energy-efficient operations. However, the adoption of green lean practices may require initial investments in eco-friendly technologies and employee training.
Reduction of carbon footprint
Discussing the reduction of carbon footprint within the scope of lean operations highlights the strategic importance of addressing environmental concerns in operational strategies. Reducing the carbon footprint involves implementing measures to minimize greenhouse gas emissions and energy consumption throughout the value chain. The key characteristic of this endeavor is its long-term impact on environmental conservation and climate change mitigation. By incorporating carbon footprint reduction initiatives, organizations can strengthen their sustainability goals and meet regulatory requirements. However, the complexities of tracking and quantifying carbon emissions pose challenges in accurately assessing the effectiveness of such initiatives.
Agile Lean Hybrid Approaches
Examining agile lean hybrid approaches in operations management signifies a dynamic shift towards adaptable and responsive business frameworks. Combining agile and lean methodologies fosters a culture of continuous improvement while enabling swift adaptation to market demands. The key characteristic of this approach is its ability to reconcile the structured efficiency of lean with the flexibility of agile practices. Implementing agile lean hybrid approaches empowers organizations to navigate changing business landscapes with agility and innovation. Yet, balancing agility with lean principles may require organizational restructuring and cross-functional collaboration to achieve seamless integration.
Combining agile and lean methodologies
Delving into the combination of agile and lean methodologies unveils a versatile approach to operations management that emphasizes both iterative development and waste reduction. This integration allows businesses to iterate quickly on product development while maintaining operational efficiency. The key characteristic of this combination is its dual focus on adaptability and value creation, ensuring that processes remain responsive to customer needs. Adopting agile lean methodologies can catalyze innovation and streamline project delivery, yet aligning the differing timelines and methodologies of agile and lean presents challenges in synchronization and prioritization.
Adaptability in dynamic business environments
Exploring adaptability in dynamic business environments underlines the necessity for operational frameworks that can swiftly respond to changing market conditions. The key characteristic of adaptability lies in its capacity to adjust operations in real-time based on evolving customer demands and industry trends. Embracing adaptability within lean operations enables organizations to foster resilience and agility in the face of uncertainty. However, maintaining adaptability may require continuous monitoring of market dynamics and proactive strategizing to anticipate changes effectively. Striking a balance between stability and flexibility is essential to harnessing the benefits of adaptability in dynamic business environments.