Material Requirement Planning in Modern Manufacturing
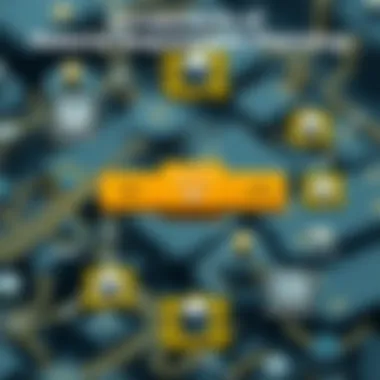
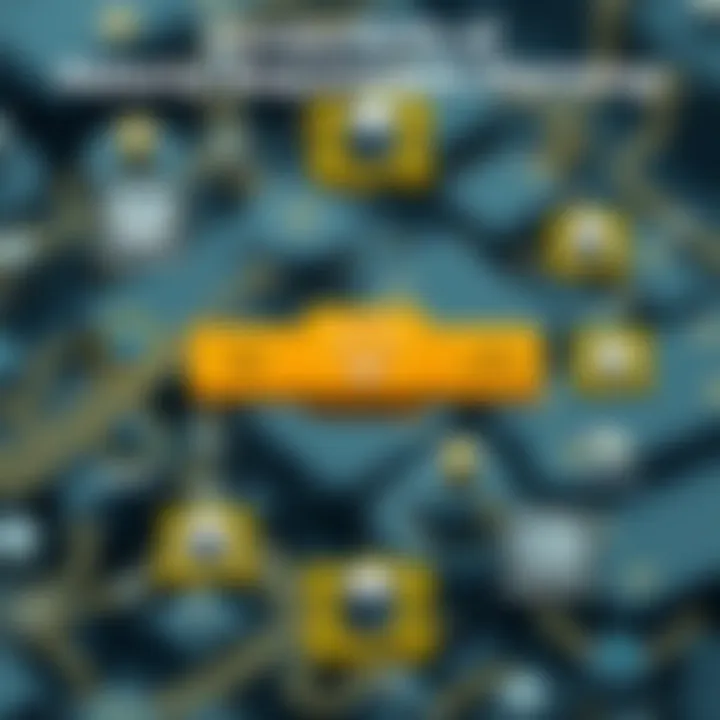
Intro
Material Requirement Planning (MRP) stands at the heart of modern manufacturing, serving as a cornerstone for effective inventory management and production scheduling. In an age where precision and efficiency dictate success, understanding MRP becomes essential for industry professionals. This overview will provide a concise yet thorough look at MRP's significance, its intricate processes, and the benefits it can bestow upon organizations striving for operational excellence.
MRP fundamentally revolves around the principle of ensuring that the right materials are available at the right time, in the right quantity, and at the right place. This intricate dance requires not only foundational knowledge but a keen eye for detail and adaptability in rapidly changing environments. Whether you're a seasoned industrial manager or a budding enthusiast, grasping the MRP landscape will empower you to make informed decisions._
As we explore this case study analysis, key themes will emerge, such as the various methodologies employed in MRP, the challenges faced during implementation, and the tangible benefits observed in real-world scenarios. We'll analyze concrete examples that illustrate how businesses have harnessed MRP systems for optimal efficiency and robust decision-making.
In the following sections, we'll dissect the various aspects of Material Requirement Planning, each illuminating a different facet of its importance and application in today's manufacturing sectors.
Prologue to Material Requirement Planning
Material Requirement Planning, commonly known as MRP, plays a crucial role in the world of manufacturing. Itâs the beating heart of inventory management and production scheduling, integrating various elements to ensure that businesses meet customer demands without running into stock issues. But before jumping into the specifics, itâs vital to appreciate what MRP systems bring to the table.
Overview of MRP Systems
MRP systems act as lifelines for manufacturers, helping them organize raw materials, components, and production processes. The system primarily relies on three key inputs: the master production schedule, the bill of materials, and inventory status records. Think of it like a finely tuned orchestra, where each instrument must be in harmony to produce a melodic tune. Each component contributes to a larger goal, ensuring that materials are available for production at the right time.
The central aim of MRP is to transform forecasted demand into planned production activities. One widely recognized model of MRP is the MRP II system, which extends beyond mere calculations to enhance the entire manufacturing operation. With integrated systems, it's possible to monitor everything from machine availability to labor scheduling, providing a holistic view of operations. This interconnectivity is critical; it keeps teams aligned and mitigates risks associated with production delays.
Importance in Manufacturing Industries
The significance of MRP in manufacturing can't be overstated. In an industry landscape where customer expectations run high, businesses can't afford the luxury of delayed shipments or excess inventory. Adopting MRP systems offers a myriad of advantages:
- Efficient Inventory Management: By precisely calculating what, when, and how much to order, companies can maintain optimal inventory levels. No more overstocking or risking missing out on sales due to stockouts.
- Enhanced Production Planning: MRP assists in aligning production schedules with customer demand, therefore streamlining operations and minimizing waste.
- Cost Reduction: Improved inventory control and optimized production processes lead to natural cost savings. This financial flexibility allows companies to redirect resources towards growth initiatives.
- Flexibility: The manufacturing environment constantly evolves. When faced with sudden changes in demand or supply chain disruptions, MRP provides adaptability essential for navigating such challenges.
Ultimately, MRP systems serve as an indispensable tool in modern manufacturing, enabling companies to harness the power of planning and logistics in an increasingly complex global market. By engaging with the principles of MRP, organizations can set themselves on a path toward enhanced operational efficiency, reduced costs, and heightened customer satisfaction.
Key Terminology in MRP
Understanding the key terminology in Material Requirement Planning (MRP) is crucial for grasping how the system operates and can impact manufacturing processes. This section defines the important elements of MRP, focusing on how they contribute to effective inventory management, production scheduling, and overall operational efficiency.
Materials
In the context of MRP, materials refer to the raw goods or components that are essential for manufacturing finished products. These materials are identified based on the needs defined in production schedules and demand forecasts. Having a clear understanding of the types of materials needed, along with their quantities, helps in avoiding overstocking or stockouts, situations that can be detrimental to a company's profitability.
To efficiently manage materials, businesses often categorize them as:
- Raw Materials: Tangible components that have yet to be processed or transformed.
- Semi-finished Goods: Items that have gone through some level of production but are not yet final products.
- Finished Goods: Fully developed products ready for sale.
Integrating a clear materials management strategy within an MRP system assists organizations in reducing waste, optimizing inventory turnover, and maintaining a seamless flow of production.
Bill of Materials (BOM)
The Bill of Materials (BOM) is a vital document in MRP that outlines the components required to manufacture a product. Think of it as a recipe; just as a recipe lists all the ingredients needed to cook a dish, the BOM specifies all materials, parts, and subassemblies required for production. Each item in the BOM is typically associated with a predefined quantity and can include detailed specifications, such as sizes and materials.
A well-structured BOM offers several benefits:
- Clarity: Provides a clear outline of what is necessary to produce each item, reducing confusion on the shop floor.
- Costing: Assists in estimating production costs by evaluating the required materials.
- Inventory Management: Helps in tracking inventory levels more effectively since it provides details about components and quantities.
- Changes Management: Any modifications in design can be easily reflected within the BOM, ensuring the production team has updated information.
The accuracy of the BOM profoundly impacts the efficiency and effectiveness of the MRP system, as discrepancies can lead to production delays and excessive costs.
Inventory Levels
Inventory levels are crucial in MRP, as these figures dictate how much stock a company should have on hand at any given time. Understanding the right inventory levels helps to balance production needs against available resources without tying up unnecessary capital in surplus stock. This balance is essential to maintain agility in production while minimizing carrying costs.
There are several inventory types that should be monitored:
- Safety Stock: Buffer stock that serves as a protection against unpredictable demand fluctuations.
- Cycle Stock: Inventory that is regularly replenished to meet anticipated sales volumes.
- In-Transit Inventory: Goods that are being transported between locations, whose status must be monitored to avoid surprises.
Finding the optimal inventory level often involves using techniques such as Just-In-Time (JIT) inventory management. This approach can significantly minimize waste and decrease holding costs, rendering operations leaner and more efficient. By studying inventory levels in tandem with demand forecasts, businesses can refine their MRP processes and responsiveness to market changes.
The Components of MRP
When delving into Material Requirement Planning (MRP), understanding its core components is a must. These elements work in unison to create a structured approach towards inventory management and production processes in manufacturing environments. The significance of these components cannot be overstated; they are the very backbone that supports efficient and streamlined operations.
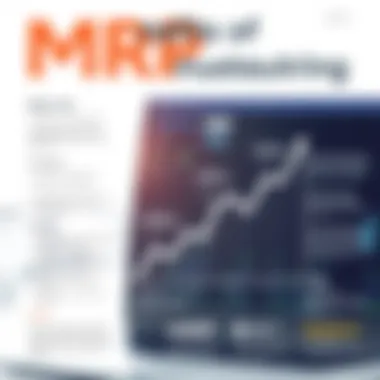
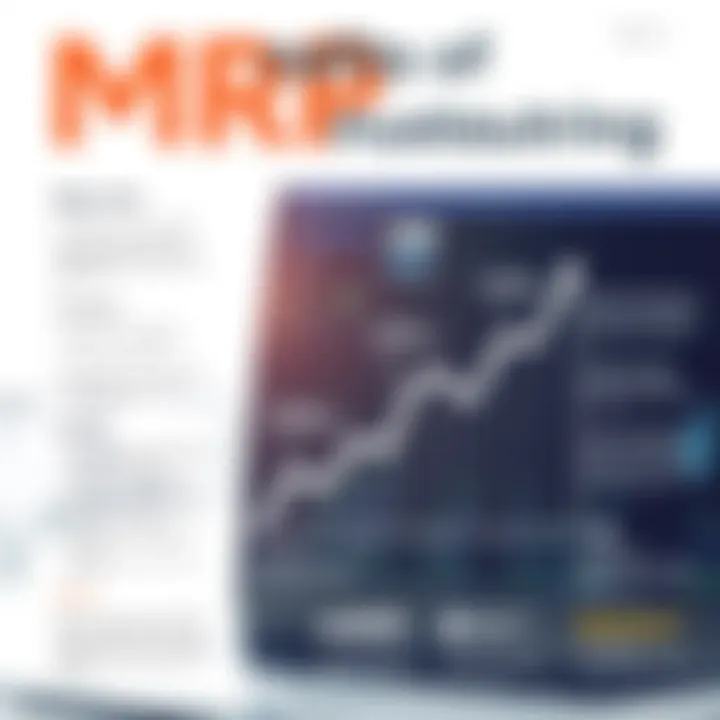
Demand Forecasting
Demand forecasting is the first pillar in the MRP framework. It involves predicting future demand for products based on various factors, including historical sales data, market trends, and customer preferences. A robust forecasting system is like having a crystal ballâit lets companies anticipate the levels of demand and adjust their inventory accordingly.
Effective demand forecasting helps prevent both overstock and stockouts, which can severely impact a companyâs bottom line. For instance, a manufacturer of consumer electronics wouldn't want to find itself with a warehouse filled to the brim with unsold gadgets while missing the boat on fulfilling orders for a hot new product. Using techniques such as statistical modeling or machine learning algorithms enhances the accuracy of these forecasts.
Identifying seasonal trends and adjusting inventory levels ahead of peak times is crucial for maintaining balance. This makes demand forecasting not just a task but an art form that requires finesse and continual adjustment.
Inventory Management
Next up is inventory management, the lifeblood of MRP. This component ensures that the right materials are available at the right time and in the right amounts. Without effective inventory management, even the most sophisticated MRP system can flounder.
To break it down, effective inventory management entails:
- Categorizing Inventory: Understanding different types of inventoryâraw materials, work-in-progress, and finished goodsâhelps streamline processes.
- Monitoring Stock Levels: Keeping an eye on stock levels through techniques like just-in-time inventory can save on costs and improve cash flow.
- Implementing Inventory Control Systems: Utilizing software solutions that integrate with the MRP system allows for real-time tracking of inventory levels.
The concept of Safety Stock also plays a pivotal role here. It acts as a buffer against uncertainties in supply and demandâthink of it as a safety net that provides the flexibility to manage unexpected changes. Having the right balance prepares companies to meet demand without excessive holding costs.
Production Scheduling
Lastly, production scheduling wraps everything up into a comprehensible timeline. This component ensures that the manufacturing processes align smoothly with demand forecasts and inventory levels. It sets the stage for how and when products are made and ensures that production resources are used efficiently.
The importance of production scheduling can be highlighted through its various tasks:
- Setting Production Goals: Establishing what needs to be produced within certain time frames helps prioritize workloads.
- Allocating Resources: Assigning machinery, labor, and materials effectively requires precise planning. A mix-up in scheduling can lead to costly downtimes.
- Monitoring and Adjusting: Things can go awry on the factory floor. Flexible scheduling allows teams to respond to unexpected downtimes or order changes without derailing operations.
"A well-crafted production schedule acts like a roadmap in the seemingly chaotic landscape of manufacturing, directing resources where they are needed most."
In culmination, the components of MRPâdemand forecasting, inventory management, and production schedulingâare integral to crafting an effective planning system. Each element plays a vital role, ensuring that businesses operate smoothly and can adapt to the ever-changing landscape of manufacturing demands. Understanding how these components interact will pave the way for more informed and strategic decision-making, ultimately leading to enhanced efficiency across the board.
Case Study Selection Criteria
When diving into the world of Material Requirement Planning (MRP), understanding how to select relevant case studies becomes critical. This selection affects the insights drawn from the analysis as well as its applicability to real-world scenarios. Not only does it guide the choice of companies or industries to examine but also shapes the conclusions presented in the study.
Criteria for Effective MRP Implementation
- Organization Size and Complexity
It's essential to consider the size and structural complexity of the organization in question. Larger companies often have more intricate supply chains, which can provide more substantial data for analysis. A case study on a multi-national corporation may yield insights that aren't applicable to a small manufacturing firm, where the MRP system might be less complicated and uniquely tailored. - Industry Type
Different industries implement MRP in various ways depending on their operational needs. For instance, a case study focusing on the automotive sector will emphasize just-in-time inventory practices, while a pharmaceutical company might highlight regulatory compliance and safety. It's vital to choose case studies that align with the diverse ranges of MRP applications seen across industries. - Historical Performance
Analyze the historical performance of the company prior to MRP implementation. Companies that have faced significant operational challenges may provide richer insights into the transformational benefits of MRP. Understanding a companyâs past can illustrate just how effective MRP has been in addressing specific shortcomings. - Technology Adoption
The degree of technology integration within the selected organization can indicate the potential for successful MRP implementation. Companies employing advanced software solutions for MRP will have different experiences compared to those relying on manual processes. Therefore, the availability of relevant technology resources is a considerable factor in the case study selection process.
"The key to drawing valuable insights from case studies lies in meticulous selection criteria that reflect the diverse experiences within MRP implementations."
Industry Types Covered
The range of industries considered when selecting case studies plays a profound role in understanding MRPâs versatility:
- Automotive Industry
This sector often deals with complex supply chains and rapid production cycles, making MRP crucial for managing both inventory levels and production schedules efficiently. - Aerospace
With stringent regulatory requirements, aerospace has unique MRP challenges, particularly related to quality control and compliance tracking. - Consumer Goods
MRP in this industry often centers on pacing production with seasonal demand fluctuations, requiring adaptive forecasting methods. - Pharmaceuticals
MRP within pharmaceutical manufacturers emphasizes stringent batch control and traceability, necessitating precise planning and execution methodologies. - Electronics
This rapidly changing industry can benefit greatly from MRP by accommodating swift changes in both technology and consumer preferences.
By considering these industries, one can better understand how MRP adapts to diverse operational landscapes, thus enhancing the relevance of the insights drawn from the case study.
Detailed Analysis of Selected Case Study
Examining a specific case study in Material Requirement Planning (MRP) offers a wealth of knowledge that goes beyond theoretical frameworks. A detailed analysis allows us to identify real-world applications of MRP, illustrating both its potential benefits and the challenges organizations may face during implementation. By peeling back the layers, insights are gained that can significantly enhance tactical decision-making and operational efficiency.
In todayâs fast-paced manufacturing environment, understanding how MRP can be adapted and integrated into existing processes is crucial. Every organization has unique dynamics. Therefore, the specific elements examined within a case study provide a tangible context that informs best practices, highlights the importance of flexibility, and emphasizes the necessity of a well-thought-out implementation strategy.
Company Background and Overview
Let's explore the company featured in our case study, TransSys Manufacturing, a mid-sized manufacturer of automotive components. Established over two decades ago, the company has positioned itself as a trusted supplier in the industry. Yet, with increasing competition and evolving customer expectations, TransSys faced challenges around inventory accuracy, order fulfillment times, and production inefficiencies.
To address these issues, senior management decided to adopt an MRP system. The decision stemmed from their recognition that an efficient MRP would not only streamline their processes but would also enable them to respond quicker to industry demand changes. This case study provides a snapshot into how TransSys implemented MRP and the effects that followed.
MRP System Implementation Process
The transition to an MRP system at TransSys was neither simple nor straightforward. It required meticulous planning and active participation from various departments.
Key steps in the implementation process included:
- Needs Analysis: Evaluating current inventory processes and identifying areas needing improvement.
- Software Selection: After thorough research, TransSys opted for SAP Business One, renowned for its comprehensive capabilities tailored to middle-market enterprises.
- Training: An extensive training program for employees was initiated to ensure everyone understood the new procedures and technology involved.
- Pilot Testing: A phased pilot rollout was undertaken, starting with one of the least complex product lines to gauge the system's effectiveness.
- Feedback Loops: Regular meetings were held to collect feedback and make necessary adjustments during the implementation phase.

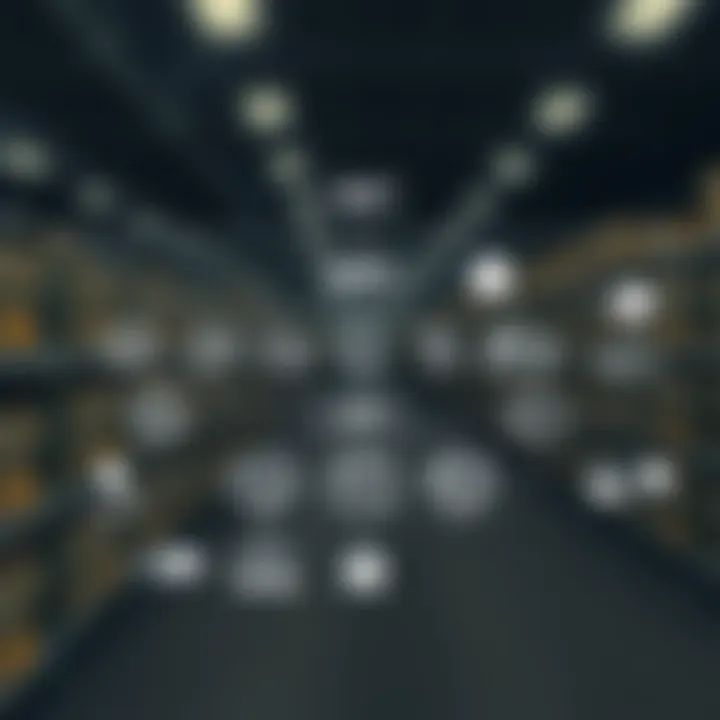
Leading up to the full launch of the MRP system, it was crucial to maintain open communication, ensuring all stakeholders were aligned with the project's goals.
Challenges Faced During Implementation
Of course, not everything went off without a hitch. TransSys encountered several challenges during the MRP implementation:
- Data Accuracy: Initial issues arose due to inaccurate inventory counts. It took significant time to clean up historical data to ensure reliable inputs for the new system.
- Resistance to Change: Many employees were reluctant to adopt the new system, fearing disruptions in their routines and job security. Overcoming this resistance took dedicated effort from management.
- Integration Issues: There were complications integrating new MRP software with existing systemsâlike CRM solutionsâresulting in temporary delays in operations.
Despite these hurdles, TransSys remained committed to their vision of harnessing MRP's potential. They continued to refine their processes, resulting in a strong realization of MRP benefits. This case study not only highlights the importance of resilience in implementation but also serves as a guide for other organizations looking to embark on their MRP journey.
Benefits Realized from MRP Implementation
Material Requirement Planning (MRP) stands tall as a vital cog in the machinery of manufacturing. The adoption of MRP systems goes beyond mere inventory management; it encapsulates a holistic approach aimed at improving various facets of production and financial performance. In this section, we will dissect the significant benefits realized from MRP implementation and understand how these create a ripple effect throughout an organization.
Enhanced Inventory Control
One of the primary benefits that organizations derive from MRP is enhanced inventory control. MRP systems provide almost crystal-clear visibility of inventory levels, allowing manufacturers to pinpoint precisely how much raw material and finished goods are available at any given moment.
- Reduced Excess Inventory: Traditional methods often lead to overstocking, tying up capital unnecessarily. MRP helps in aligning inventory with actual demand, thus preventing excess and reducing holding costs.
- Eliminated Stockouts: With accurate forecasting, MRP aids organizations in ensuring they have enough inventory on hand to meet customer demand without delays. This proactive approach can significantly enhance customer satisfaction and trust.
- Automation: Automating inventory tracking underpins efficiency and accuracy, minimizing errors common in manual systems. This can free up staff to focus on more strategic tasks, rather than time-consuming data entry.
As a result, a well-implemented MRP can create a leaner, more responsive inventory system capable of adapting to changing market conditions.
Improved Production Efficiency
Improvement in production efficiency is another hallmark of effective MRP implementation. When companies have a clear understanding of their production needs combined with accurate timelines, the benefits are multi-faceted:
- Streamlined Processes: MRP fosters a seamless flow of materials through various stages of production. By ensuring that components arrive just in time, manufacturers can minimize interruptions caused by delays.
- Labor Management: With a clear scheduling system in place, resource allocation becomes more efficient. Workers can be scheduled according to production demands, reducing downtime and optimizing labor costs.
- Flexibility and Scalability: The agile nature of MRP allows organizations to respond swiftly to market changes or unexpected demands. Whether itâs ramping up production or scaling it back, effective planning is central to operational success.
Ultimately, the improvement in production efficiency directly correlates with enhanced output and profitability, contributing to a stronger bottom line.
Financial Performance Metrics
When delving into the financial aspects, MRP systems provide metrics that are essential to any businessâs growth trajectory. They deliver insights that help organizations keep their finances healthy:
- Cost Savings: By optimizing inventory levels and improving production, organizations can significantly lower their operational costs. This includes reductions in spoilage, labor costs, and warehousing expenses.
- Revenue Growth: With improvements in fulfilling orders on time and meeting customer demands, revenue naturally increases. Responsive production scheduling directly impacts sales performance.
- Access to Data: MRP systems generate valuable data that helps in budgeting and forecasting, enabling firms to make informed financial decisions. Keeping track of how much is spent versus how much profit is made can highlight areas needing attention or improvement.
Understanding these financial performance metrics ensures that organizations can sustain and grow their profitability over time. MRP systems are not just a tool for managing materials but a comprehensive approach to improving financial health.
Effective MRP implementation can transform inventory control, enhance production efficiency, and provide critical financial insights, positioning organizations for sustainable success.
MRP Software Solutions
The significance of MRP software solutions cannot be understated in the realm of Material Requirement Planning. These systems act as the backbone of any effective MRP implementation, helping companies to streamline their processes and mitigate inefficiencies. Eating up time and resources without a solid software underpinning isnât just bad businessâitâs downright detrimental.
One of the first aspects to consider is how these tools empower organizations to maintain accurate data. Accurate data leads to informed decisions. Without the right software, managing stock levels can turn into a guessing game. An MRP solution provides real-time visibility, ensuring that a company knows what they have on hand, what they need, and when they need it. This allows businesses to become proactive rather than reactive, ultimately keeping their production lines moving smoothly.
Moreover, MRP software fosters an environment of collaboration. In a manufacturing setting, various departments need to communicate effectively, and a robust MRP system can facilitate that. Whether it's purchasing, production, or sales, everyone can access the same data, which minimizes hiccups and keeps everyone on the same page.
In summary, MRP software is not simply a luxury; it has become a necessity for companies looking to optimize their production processes.
Overview of Popular MRP Software
When diving into the sea of MRP software options, several names bob to the surface, each offering distinct functionalities tailored to varying manufacturing contexts. SAP S/4HANA, for instance, is revered for its comprehensive enterprise resource planning capabilities. It allows businesses not just to manage materials effectively, but also to integrate various business functions seamlessly.
Oracle NetSuite is another player worth noting; it caters predominantly to small to medium-sized enterprises. Its cloud-based solution streamlines various aspects of business management, from inventory control to order processingâcutting down operational woes.
Then thereâs Microsoft Dynamics 365, which combines MRP capabilities with finance and customer relationship management. It stands out for its adaptability and user-friendly interface, allowing even non-technical staff to navigate without much fuss.
- SAP S/4HANA: Extensive coverage and integration capabilities.
- Oracle NetSuite: Ideal for smaller firms with comprehensive needs.
- Microsoft Dynamics 365: Best for businesses wanting an all-in-one platform.
Criteria for Software Selection
Selecting the right MRP software is akin to picking the right tool for a job; choose poorly, and you're bound to run into trouble down the line. Several key criteria should guide the decision-making process:
- Scalability: The software should grow alongside the business, accommodating increases in production demands without a hitch.
- User-Friendliness: If the interface is complicated, it may lead to resistance from employees. A clean, intuitive layout ensures smoother transitions and quicker adoption.
- Integration Capabilities: The chosen solution must integrate smoothly with other existing systems. Data silos can create significant headaches down the line.
- Customization Options: Every business is unique; therefore, having a software option that offers flexibility for customization can make all the difference in meeting specific needs.
- Cost-Effectiveness: While investing in software is crucial, companies must weigh the potential return on investment against the costs involved. This includes not only the upfront expenses but also ongoing maintenance and training costs.
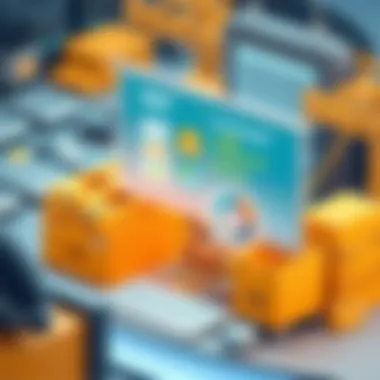
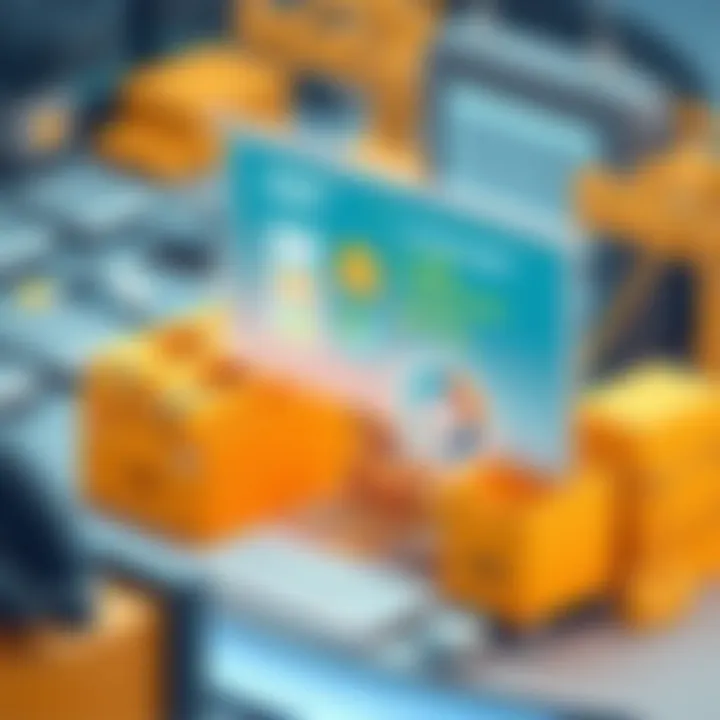
As emphasized:
"Choosing the right MRP software can either set the company's sails straight or leave them stranded in turbulent waters."
Taking the time to methodically analyze these factors will ensure that the chosen MRP solution aligns well with the organization's overarching strategy and long-term goals.
Future Trends in MRP
The landscape of Material Requirement Planning (MRP) is shifting as new technologies and methodologies emerge. Understanding these trends is critical for businesses striving to maintain a competitive edge in an increasingly complex manufacturing environment. As organizations become more sophisticated, the integration of technology and a shift in manufacturing practices are not just enhancements but necessities that can define success in lean times and prosperous ones alike.
Integration with Emerging Technologies
In the sphere of MRP, the convergence of emerging technologies such as artificial intelligence, machine learning, and the Internet of Things (IoT) is revolutionizing traditional methods. This shift is not merely about software updates; it's a holistic rewrite of how data is collected, shared, and utilized across the manufacturing workflow.
- Artificial Intelligence: AI algorithms can analyze vast datasets to predict demand patterns with greater accuracy. By recognizing historical trends and customer behaviors, businesses can optimize inventory levels, ensuring they have the right materials at the right time to meet production demands without overstocking.
- Machine Learning: This facet helps adjust MRP systems dynamically. As systems learn from fluctuations in demand or supply chain disruptions, they automatically adjust order quantities and production schedules. It turns predictions into proactive management, reducing waste and inefficiency.
- IoT Devices: With IoT sensors embedded in machinery and storage facilities, real-time data collection offers visibility into inventory levels and equipment status. This information can trigger automatic reordering processes or maintenance alerts, ensuring everything runs smoothly. "Smart" factories are becoming the norm rather than the exception.
The benefits of these integrations are monumental. They enhance real-time decision-making, reduce lead times, and allow organizations to pivot quickly in reaction to unexpected changes in the market.
Shifts in Manufacturing Practices
As the manufacturing landscape evolves, so too do the practices. This evolution towards more agile and resilient operations necessitates an informed approach to MRP. Several key shifts can be identified:
- Just-In-Time (JIT) Manufacturing: This philosophy minimizes stock levels and encourages a more responsive supply chain. MRP systems must adapt to manage inventory efficiently without excess, which can bog down cash flow.
- Sustainability: Increasingly, organizations are leaning towards sustainable practices. This trend impacts MRP as suppliers and materials are evaluated not just on cost, but on environmental impact as well. Software systems are now integrating these parameters into their algorithms to guide supply chain choices.
- Customization and Small Batch Production: The consumer demand for personalized products is pushing manufacturers to adopt smaller batch production runs. MRP systems are evolving to handle these complexities, allowing for flexibility in production scheduling that meets unique customer needs while still maintaining efficiency.
The message is clear: staying ahead means anticipating these shifts and adapting MRP strategies accordingly.
"The future of MRP lies in its ability to integrate seamlessly with the evolving landscape of technology and manufacturing practices."
As we look to the horizon of manufacturing, it is evident that those who can harness these trends will not merely survive but thrive, positioned at the forefront of the industry.
Finale and Recommendations
The importance of the conclusion and recommendations section in this article cannot be overstated. It serves as the final touchstone, encapsulating the core insights derived from the case study while simultaneously guiding industry professionals toward best practices in Material Requirement Planning. In a world where efficiency is king, synthesizing the findings from the detailed analysis offers a roadmap that companies can follow to optimize their MRP systems.
Key Takeaways from the Case Study
Reflecting on the case study, several pivotal points emerged, emphasizing the significant role of MRP systems:
- Tailored Strategies: Different organizations face unique challenges. One company might struggle with supply chain bottlenecks, while another grapples with inventory excess. The case study illustrates how customizing MRP strategies can address these specific issues effectively.
- Inter-departmental Collaboration: The insights gained show the necessity for seamless communication between departments. MRP does not operate in a vacuum; demand forecasting, production scheduling, and inventory management must work in unison. Successful implementation hinged on breaking down silos and fostering a cohesive environment where data flowed freely.
- Adaptability: The case study highlighted how flexibility in planning can lead to significant operational improvements. Adapting to changes in demand, resource availability, or production capabilities can differentiate successful companies from those that struggle.
"In an age where change is the only constant, the ability to pivot can be the key to survival in manufacturing."
Strategic Recommendations for Companies
As organizations look towards refining their MRP strategies, several recommendations can be drawn from the case study analysis:
- Invest in Training: Ensure that staff at all levels understand MRP systems. Comprehensive training reduces errors and enhances efficiency. Knowledge sharing creates a workforce that adapts quickly to evolving processes.
- Utilize Advanced Analytics: Employ modern analytics tools to predict trends, assess risks, and optimize inventory levels. Real-time data can provide valuable insights and enable proactive decision-making, helping prevent issues before they escalate.
- Focus on Supplier Relationships: Building strong partnerships with suppliers can lead to better pricing, reliability, and flexibility in production schedules. A well-established supplier network can be pivotal in adapting to emerging needs.
- Regularly Review MRP Performance: Set formal cycles to assess MRP effectiveness in meeting operational goals. These evaluations should incorporate feedback from various stakeholders, allowing adjustments to be made to continually enhance the process.
- Leverage Technology: As the manufacturing landscape diversifies, companies should leverage emerging technologies such as IoT, AI, and machine learning. Integrating these innovations with MRP systems can enrich data accuracy and facilitate smarter planning.
By taking these recommendations to heart, companies can unlock the full potential of MRP systems, leading to improved efficiency, reduced costs, and better alignment with market demands. The end goal is to derive not only operational success but also strategic advantage over competitors.
References and Further Reading
Understanding Material Requirement Planning (MRP) requires a firm grasp of the nuances introduced throughout the case study. This final segment will detail references and further reading options that can significantly enhance your comprehension of MRP, its systems, and broader applications within manufacturing. Accessing high-quality literature is a cornerstone of effective learning in this field, enabling professionals to cross-reference established knowledge with modern practices.
Essentially, the objective here is twofold: to underscore the significance of remanding back to authoritative sources and to guide readers towards comprehensive texts that address various aspects of MRP. As with any highly specialized topic, diving into a variety of references prevents one from becoming myopic.
Key Texts on MRP
When seeking to deepen your understanding of MRP, it is vital to turn to a selection of canonical texts. Some pivotal books include:
- "Production and Operations Analysis" by Steven Nahmias and Tava Lennon Eskandarian: This book offers an in-depth insight into production systems, with sections committed to MRP.
- "Manufacturing Planning and Control for Supply Chain Management" by F. Robert Jacobs and William Lee Berry: A classic that presents essential theories in MRP and its integration with supply chain strategies.
- "Material Requirements Planning: Principles and Practice" by G. T. Gunderson: This text provides both theoretical frameworks and practical examples, making it a must-read.
Additionally, consider accessing the electronic resources available through academic libraries or online platforms, as these can often lead you to the latest editions or relevant publications you might not typically encounter.
Research Articles and Journals
For those who thrive on academic rigor, peer-reviewed journals are a treasure trove of current research in MRP theory and its applications. Noteworthy journals include:
- International Journal of Production Research: Focused heavily on new advancements in production techniques, including MRP methodologies.
- Journal of Operations Management: This source often publishes studies that examine practical implementations of MRP in various industries.
- Production Planning & Control: Offering insights and empirical studies on the optimization of production processes through MRP.
Engaging with these publications allows IT professionals, students, and industry stakeholders to remain informed about emerging trends and dysfunctions within existing frameworks. Research articles can reveal case studies that either reinforce or challenge established understanding, thereby fostering a rich exchange of ideas.
"Research isnât just about gathering information, but a pathway to innovation in the field of MRP. Embracing different perspectives leads to more coherent and adaptable strategies."