Transforming Operational Efficiency: Motorola's Six Sigma Journey
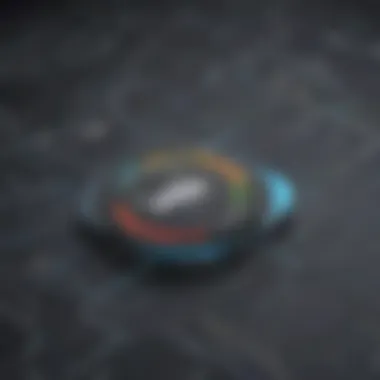
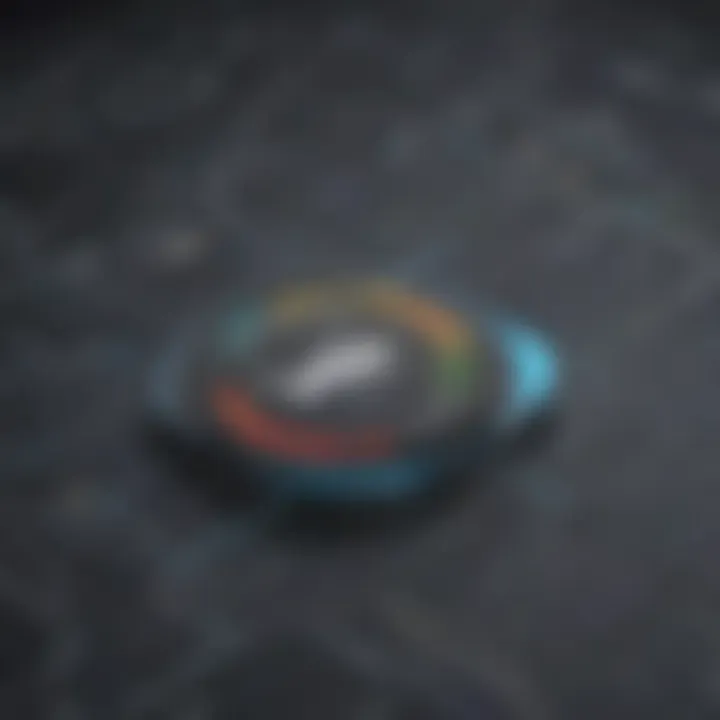
Introduction
In the realm of quality management and operational efficiency, the integration of Six Sigma methodology within Motorola serves as a prime example of transformation and excellence. This article delves into the journey undertaken by Motorola in embracing Six Sigma principles, shedding light on its profound impact on problem-solving and process optimization within the organization.
Inception of Six Sigma at Motorola
The inception of Six Sigma at Motorola marked a pivotal moment in the company's history. It sparked a new wave of emphasis on quality improvement and operational excellence. Understanding how these principles were introduced and integrated into Motorola's existing framework is essential to appreciate the significant changes that followed.
Adoption and Adaptation
As Six Sigma gained momentum within Motorola, the organization not only adopted its core principles but also tailored them to suit its specific needs and challenges. This section will explore the process of adaptation and customization undertaken by Motorola to effectively implement Six Sigma across various functions and departments.
Impact on Operational Efficiency
One of the key outcomes of implementing Six Sigma at Motorola was the substantial improvement in operational efficiency. Through meticulous analysis and data-driven decision-making, the organization was able to streamline processes, reduce defects, and enhance overall productivity. This segment will delve into the specific ways in which Six Sigma revolutionized operational practices at Motorola.
Quality Improvement Initiatives
Quality improvement lies at the heart of Six Sigma, and Motorola's journey is a testament to its effectiveness in this regard. By instilling a culture of continuous improvement and a focus on customer satisfaction, Six Sigma paved the way for enhanced quality standards at Motorola. This part will illuminate the quality improvement initiatives undertaken by the organization.
Synthesizing Key Learnings
Introduction to Six Sigma
Understanding the core foundation of Six Sigma within the context of this article is crucial for unraveling Motorola's journey. Six Sigma, originating at Motorola, has become synonymous with quality management and operational excellence. This section will delve deep into the intricate elements that make up Six Sigma and its relevance to enhancing organizational performance. By exploring the principles, methodologies, and benefits of Six Sigma adoption, readers will grasp the significance of integrating this meticulous approach into business operations.
Origins of Six Sigma at Motorola
Early developments
In the early stages of Six Sigma implementation at Motorola, pioneering efforts focused on refining processes and reducing defects. These initial developments laid the groundwork for a data-driven, quality-centric approach that would revolutionize the industry. The emphasis on statistical methods and problem-solving techniques became a hallmark of Motorola's quality management strategies. By emphasizing efficiency and quality control at every stage, Motorola established a solid framework for continuous improvement and innovation.
Key pioneers
Key figures within Motorola played a pivotal role in championing Six Sigma principles. Their leadership and commitment to quality paved the way for widespread adoption within the organization. These pioneers meticulously crafted methodologies and tools that streamlined processes and enhanced decision-making. By championing data-driven practices and a culture of excellence, these individuals shaped the trajectory of Six Sigma at Motorola and set new standards for quality management practices.
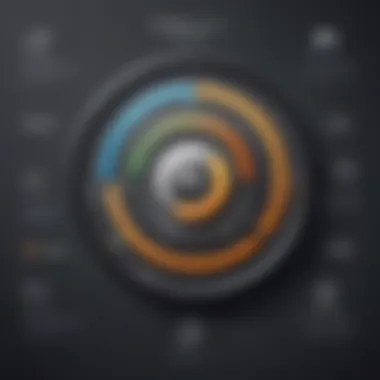
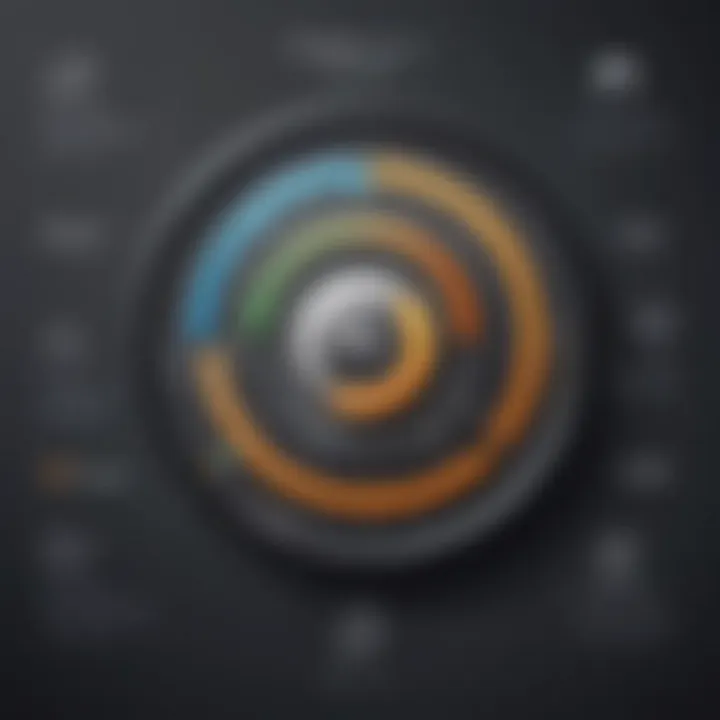
Principles of Six Sigma
DMAIC methodology
At the heart of Six Sigma lies the DMAIC methodology, comprising define, measure, analyze, improve, and control stages. This structured approach to problem-solving ensures a systematic and data-driven process for identifying and rectifying issues. The DMAIC methodology empowers organizations to streamline operations, optimize performance, and deliver consistent results. By emphasizing clear objectives and measurable outcomes, DMAIC serves as a cornerstone of Six Sigma's success within Motorola and beyond.
Focus on customer-centric quality
Six Sigma's focus on customer-centric quality underscores the importance of aligning business processes with customer expectations. By prioritizing customer needs and preferences, organizations can enhance satisfaction levels and build brand loyalty. This customer-centric approach guides key decision-making processes, driving improvements in product quality, service delivery, and overall customer experience. By integrating customer feedback and insights, Six Sigma fosters a culture of continuous improvement and excellence.
Data-driven decision-making
A fundamental tenet of Six Sigma is its reliance on data-driven decision-making processes. By leveraging statistical tools and analytics, organizations can make informed decisions that drive operational efficiency and quality enhancement. Data plays a central role in identifying trends, predicting outcomes, and optimizing processes for superior results. Through continuous data analysis and monitoring, Six Sigma practitioners can proactively address challenges and capitalize on opportunities for improvement.
Benefits of Six Sigma Adoption
Improved processes
Embracing Six Sigma principles leads to significant improvements in operational processes. By standardizing workflows, eliminating waste, and enhancing efficiency, organizations can achieve streamlined operations and consistent output quality. The emphasis on process optimization and continuous evaluation ensures that operations remain agile and responsive to market demands. Through a focus on efficiency and effectiveness, Six Sigma drives operational excellence and sustainable performance outcomes.
Cost savings
One of the most tangible benefits of Six Sigma adoption is the realization of cost savings across all operational facets. By identifying and mitigating sources of waste, inefficiency, and defects, organizations can streamline processes and reduce costs. The systematic approach to problem-solving and process optimization inherent in Six Sigma yields measurable financial benefits, resulting in improved profitability and sustainability. Cost savings generated through Six Sigma practices contribute to long-term organizational success and competitiveness.
Enhanced customer satisfaction
Six Sigma's impact on customer satisfaction is profound, as organizations align their processes and products with customer expectations. By consistently delivering high-quality products and services that meet or exceed customer requirements, organizations can enhance customer loyalty and satisfaction. The focus on quality assurance, continuous improvement, and customer feedback mechanisms ensures that organizations remain attentive to customer needs and preferences. Through targeted quality initiatives and service enhancements, organizations can boost customer satisfaction levels and drive loyalty in competitive markets.
Integration of Six Sigma at Motorola
The integration of Six Sigma at Motorola stands as a pivotal point in the company's operational evolution, revolutionizing its approach to quality management and process optimization. This section delves into the significance of incorporating Six Sigma principles within Motorola, highlighting key elements that have propelled the company towards organizational excellence in quality management. By implementing Six Sigma methodologies, Motorola has experienced enhanced efficiency, streamlined processes, and a customer-centric focus, leading to improved products and services.
Company-wide Implementation
Training Programs
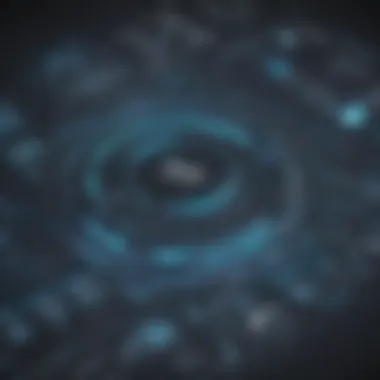
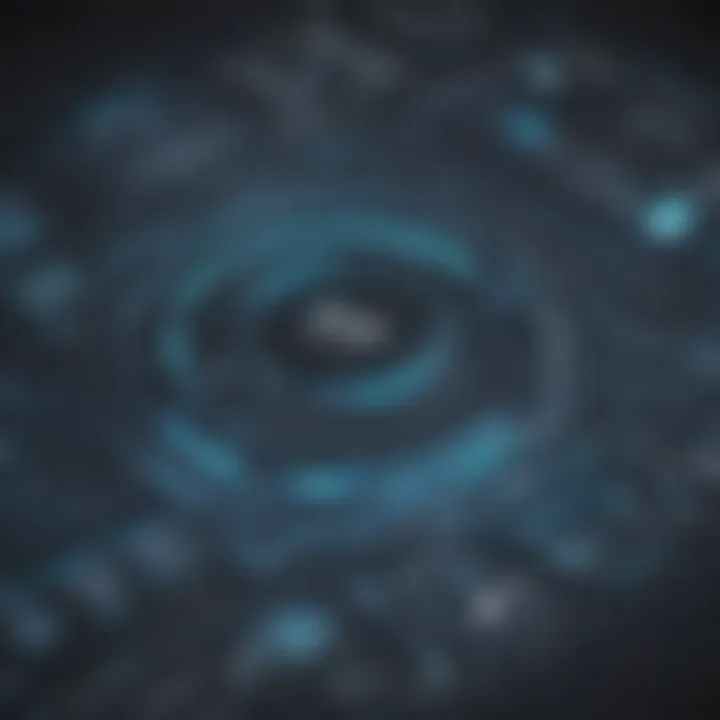
The training programs introduced at Motorola play a crucial role in ensuring that employees are equipped with the necessary knowledge and skills to effectively apply Six Sigma principles across the organization. These programs emphasize the importance of data-driven decision-making, process improvements, and customer satisfaction. The key characteristic of these training programs lies in their comprehensive curriculum that covers various aspects of Six Sigma, from basic concepts to advanced methodologies. This approach benefits the company by fostering a culture of continuous improvement and providing employees with the tools to drive meaningful change within their respective roles.
Certification Processes
Certification processes at Motorola validate the proficiency and expertise of individuals in implementing Six Sigma practices successfully. These processes certify employees at different levels of competency, such as Green Belt, Black Belt, and Master Black Belt, based on their knowledge and experience in leading Six Sigma projects. The key characteristic of certification processes is their role in establishing a standardized framework for implementing Six Sigma, ensuring consistency and quality across projects. While these processes add credibility to employees' skills and competence, they also serve as a motivator for personal and professional development within the organization.
Cultural Transformation
Embracing Data-Driven Decision-Making
The cultural transformation at Motorola towards embracing data-driven decision-making reflects a fundamental shift towards basing strategies and actions on factual analysis rather than assumptions. This aspect highlights the company's commitment to leveraging data and analytics to drive informed decisions, leading to improved outcomes and performance. The key characteristic of this transformation is its focus on objectivity and accuracy, ensuring that decisions are grounded in quantitative evidence rather than subjective opinions.
Continuous Improvement Mindset
The continuous improvement mindset embedded within Motorola's culture fosters an environment where employees are encouraged to seek opportunities for innovation and enhancement continually. This mindset promotes a proactive approach to problem-solving, quality enhancement, and operational efficiency. The key characteristic of this mindset is its role in instilling a sense of ownership and accountability among employees, driving them to contribute towards the company's overarching goal of sustained excellence.
Success Stories within Motorola
Case Studies
The incorporation of case studies within Motorola's practices serves as a valuable resource for showcasing real-world applications of Six Sigma methodologies. These studies offer practical insights into how Six Sigma principles have been implemented to address specific challenges, improve processes, and deliver tangible results. The key characteristic of utilizing case studies is their ability to provide context and relevance to theoretical concepts, making the implementation of Six Sigma more accessible and comprehensible for employees.
Operational Excellence Achievements
Achieving operational excellence at Motorola signifies the successful integration of Six Sigma principles into its core operations, resulting in measurable improvements in quality, efficiency, and customer satisfaction. These achievements serve as demonstration points for the effectiveness of Six Sigma methodologies in driving meaningful change and delivering value to the organization. The key characteristic of operational excellence achievements is their role in setting benchmarks for performance and quality standards, inspiring continuous innovation and excellence within the company.
Impact of Six Sigma on Motorola's Performance
The topic of the impact of Six Sigma on Motorola's performance holds immense significance within this article. It delves deep into how Six Sigma principles have revolutionized the way Motorola operates, emphasizing on operational efficiency and quality enhancement. Exploring this aspect sheds light on the crucial role quality metrics play in driving organizational excellence and achieving strategic objectives. By evaluating specific elements such as defect reduction rates and process improvement outcomes, the article aims to provide a comprehensive analysis of how Six Sigma has shaped Motorola's performance trajectory.
Quality Metrics Enhancement
Given its pivotal role, quality metrics enhancement drives continuous improvement and sustainable growth within organizations. In examining defect reduction rates, the article underscores the importance of identifying and eliminating defects in procedures, products, or services. Highlighting key characteristics like defect prevention strategies and error-proofing techniques, it becomes evident why defect reduction rates are a preferred choice for optimizing operational processes. Moreover, the unique feature of defect reduction rates lies in their effectiveness in ensuring consistent quality standards and enhancing customer satisfaction levels.
Concerning process improvement outcomes, the focus shifts towards enhancing productivity, reducing waste, and streamlining operations. By highlighting key characteristics such as root cause analysis and performance metrics tracking, the article showcases why process improvement outcomes are crucial for achieving organizational goals. The distinct feature of process improvement outcomes lies in their ability to foster a culture of continuous enhancement and drive sustainable business growth.
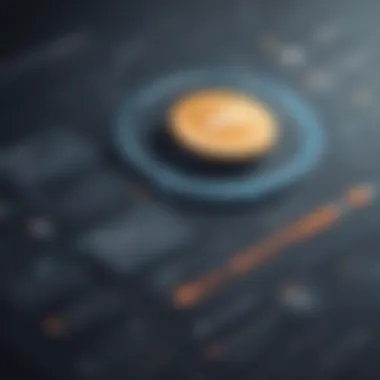
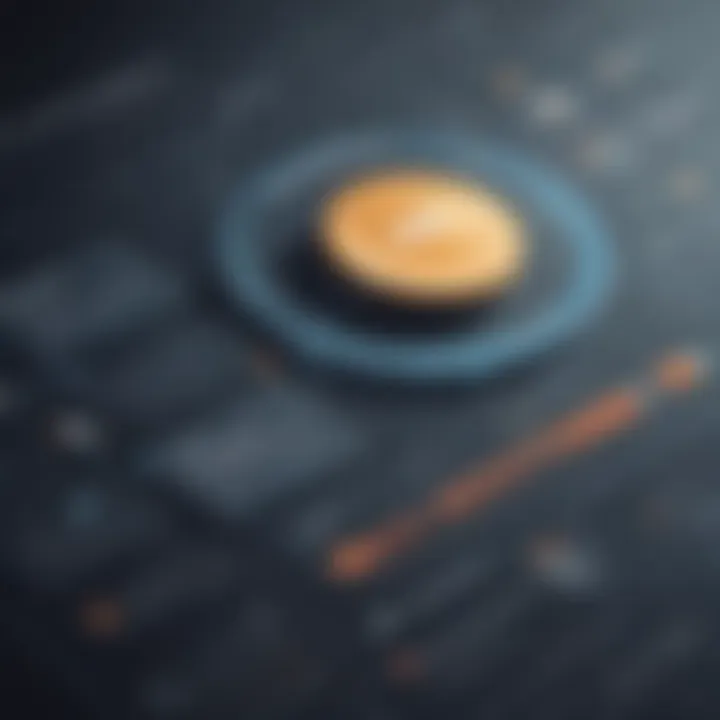
Financial Gains
Delving into financial gains resulting from Six Sigma implementation provides insights into how Motorola has reaped tangible benefits from quality management strategies. When analyzing cost reduction analysis, the article emphasizes the significance of minimizing costs, optimizing resources, and increasing profitability. By accentuating key characteristics like cost-benefit analysis and resource allocation optimization, it becomes clear why cost reduction analysis is a favored approach for enhancing operational efficiency. Furthermore, the unique feature of cost reduction analysis lies in its capacity to identify cost-saving opportunities and drive bottom-line improvements.
In exploring revenue growth statistics, the focus extends to revenue generation strategies, market expansion initiatives, and customer acquisition approaches. By highlighting key characteristics like revenue forecasting methods and sales performance tracking, the article exemplifies why revenue growth statistics are instrumental in achieving financial objectives. The distinct feature of revenue growth statistics lies in their ability to gauge market demand, enhance revenue streams, and sustain long-term business success.
Market Competitiveness
When analyzing market competitiveness, the discussion centers around how Motorola has positioned itself as a leader in the industry through effective quality management practices. By evaluating product quality comparisons, the article underscores the importance of benchmarking against competitors, analyzing customer feedback, and enhancing product offerings. Highlighting key characteristics such as quality audits and performance benchmarking, it becomes evident why product quality comparisons are vital for gaining a competitive edge. The unique feature of product quality comparisons lies in their role in fostering brand loyalty, customer retention, and market differentiation.
Turning to industry leadership impact, the focus shifts towards examining how Motorola's quality management practices have influenced industry standards and norms. By highlighting key characteristics like best practices adoption and benchmarking against industry leaders, the article showcases why industry leadership impact is crucial for establishing credibility and trust within the market. The distinct feature of industry leadership impact lies in its ability to drive innovation, set industry benchmarks, and inspire continuous improvement initiatives.
Continued Evolution of Six Sigma at Motorola
Adapting to Technological Advancements
Integration of AI and Big Data
Within the realm of modern quality management, the integration of artificial intelligence (AI) and big data holds paramount importance. At Motorola, incorporating AI and big data into the Six Sigma framework has revolutionized decision-making processes and enhanced analytical capabilities. The key characteristic of this integration lies in its ability to extrapolate valuable insights from vast datasets, enabling precise problem diagnosis and strategic decision-making. The unique feature of leveraging AI and big data in Six Sigma implementation at Motorola is the augmentation of predictive analytics and the automation of quality control processes. This integration proves beneficial for the organization by elevating operational efficiency, mitigating risks, and facilitating informed business decisions.
Digital Transformation Strategies
Digital transformation strategies play a pivotal role in shaping the future of Six Sigma practices at Motorola. These strategies encompass the adoption of digital tools, technologies, and processes to streamline operations and drive innovation. The key characteristic of digital transformation lies in its ability to enhance connectivity, data management, and operational agility within the quality management framework. Embracing digital transformation enables Motorola to automate manual tasks, integrate disparate systems, and facilitate real-time monitoring of quality metrics. While the primary advantage of digital transformation is improved efficiency and productivity, it comes with the challenge of effectively managing organizational change and ensuring data security in a rapidly evolving digital ecosystem.
Global Reach and Scalability
International Deployment
The international deployment of Six Sigma principles at Motorola signifies the organization's commitment to maintaining consistent quality standards across diverse geographical locations. By implementing Six Sigma methodologies globally, Motorola ensures that best practices are harmonized, and quality metrics are universally upheld. The key characteristic of international deployment lies in the fostering of a collaborative culture across borders, encouraging knowledge-sharing and cross-functional collaboration. The unique feature of international deployment is the adaptation of Six Sigma principles to local contexts, considering cultural nuances and regulatory requirements. While international deployment enhances operational coherence and standardization, it demands meticulous coordination and communication to overcome logistical challenges and ensure alignment with diverse stakeholder expectations.
Standardization Efforts
Standardization efforts within Motorola's Six Sigma framework focus on establishing uniformity in processes, metrics, and quality benchmarks across the organization. By standardizing quality management practices, Motorola aims to drive consistency, reliability, and continuous improvement in its operational processes. The key characteristic of standardization efforts is the creation of streamlined workflows, predefined quality metrics, and structured methodologies for problem-solving. The unique feature of standardization lies in its capacity to facilitate benchmarking, performance tracking, and root cause analysis across different business units. While standardization fosters alignment and transparency, it requires proactive maintenance, periodic review, and adaptability to changing business dynamics.
Future Prospects and Innovations
Industry Trends Analysis
Conducting rigorous industry trends analysis within the Six Sigma framework enables Motorola to stay abreast of market developments, emerging technologies, and competitive strategies. By scrutinizing industry trends, Motorola gains insights into customer preferences, market demands, and technological advancements shaping the quality management landscape. The key characteristic of industry trends analysis is its ability to inform strategic decision-making, risk mitigation, and performance optimization based on external market dynamics. The unique feature of this analysis is the identification of opportunities, threats, and best practices for quality management, positioning Motorola as a proactive and agile industry player. While industry trends analysis fosters anticipatory decision-making, it necessitates continuous monitoring, adaptability, and contextual understanding to leverage market insights effectively.
Predictive Analytics Considerations
Incorporating predictive analytics considerations into Six Sigma processes empowers Motorola to forecast quality outcomes, anticipate risks, and drive preemptive quality control measures. By leveraging predictive analytics, Motorola can proactively identify process inefficiencies, quality deviations, and corrective actions needed to enhance operational performance. The key characteristic of predictive analytics considerations is its capacity to extrapolate patterns, derive insights, and optimize decision-making based on data-driven forecasts. The unique feature of incorporating predictive analytics lies in its alignment with continuous improvement practices, enabling iterative enhancements and proactive quality assurance. While predictive analytics offers a predictive edge, it requires robust data infrastructure, analytical proficiency, and strategic alignment to realize its full potential in enhancing quality management practices at Motorola.