Strategizing the Journey to ISO 9001 Certification: A Comprehensive Roadmap
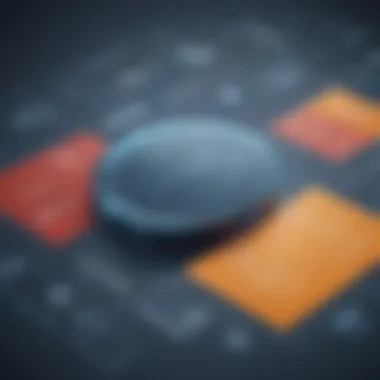
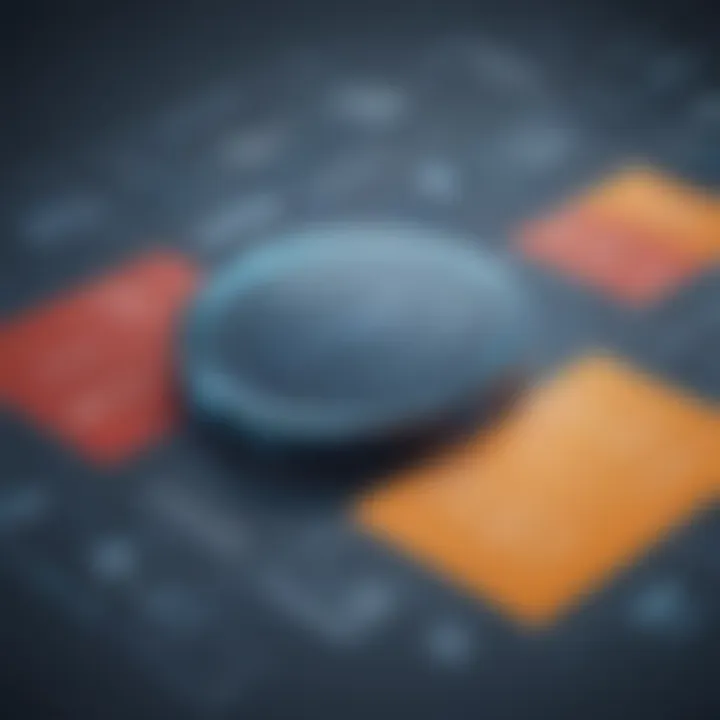
Understanding the ISO Certification Process: A Detailed Overview
Upon embarking on the journey towards ISO 9001 certification, organizations encounter a web of essential steps and requirements. This certification serves as a remarkable milestone signaling adherence to internationally recognized standards for quality management systems. Delving into the intricacies of this process involves meticulous planning and a deep understanding of the foundational principles upheld by ISO 9001.
Navigating Initial Preparation: The Starting Point
The initial phase of ISO 9001 certification propels organizations into preparatory measures that lay the groundwork for a successful quality management system implementation. This preparatory phase involves conducting a gap analysis, identifying existing processes, and aligning them with the ISO 9001 standards. By critically evaluating current practices and procedures, organizations can pinpoint areas that require enhancement to fulfill the stringent requirements of the certification.
Deep Dive into Crafting Quality Objectives and Policies
Subsequent to the preparatory phase is the formulation of quality objectives and policies. Organizations must extensively define these objectives, ensuring they align with the overarching goal of enhancing quality standards throughout the organizational framework. Establishing clear and measurable quality objectives sets the trajectory for continuous improvement and compliance with ISO 9001 criteria.
Implementation and Integration of Quality Management Systems
Transitioning from objective-setting to implementation necessitates a seamless integration of quality management systems within the organizational framework. This phase calls for robust communication channels, comprehensive training programs, and diligent deployment of resources to embed quality-centric practices into daily operations. Implementing these systems effectively calls for cross-functional collaboration and a shared commitment to quality enhancement.
Audit Preparation and Performance Evaluation
As the implementation phase unfolds, organizations prepare for the pivotal stage of audit evaluation. Internal audits serve as a litmus test for the efficacy of implemented quality management systems. These assessments identify gaps, strengths, and areas for refinement to ensure alignment with ISO 9001 standards. Rigorous internal audits set the stage for external certification audits, which determine whether the organization meets the requisite criteria for ISO 9001 certification.
Securing ISO Certification: The Ultimate Milestone
Achieving ISO 9001 certification signifies the culmination of extensive efforts, meticulous planning, and unwavering dedication to quality assurance. Securing this certification elevates an organization's reputation, instills trust among stakeholders, and fosters a culture of continuous improvement. Adherence to ISO 9001 standards not only enhances operational efficiency but also positions organizations as leaders in quality management practices.
Understanding ISO Certification
ISO 9001 Certification is a pivotal aspect in the realm of quality management. This certification serves as a hallmark of an organization's commitment to meeting and exceeding internationally recognized quality standards. It signifies a dedication to continuous improvement, customer satisfaction, and operational excellence. Understanding ISO 9001 involves delving into the history, principles, benefits, and intricacies of this quality management system.
Introduction to ISO
In exploring the History and Significance of ISO 9001, we uncover the roots of this foundational quality standard. The evolution of ISO 9001 and its global adoption highlight its relevance and impact on modern business practices. Understanding the historical context of ISO 9001 provides insights into the basis of current quality management principles and standards. This historical perspective guides organizations in aligning their quality objectives with industry best practices.
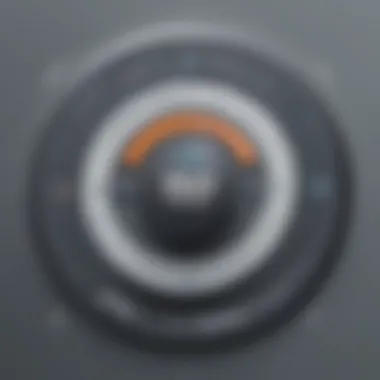
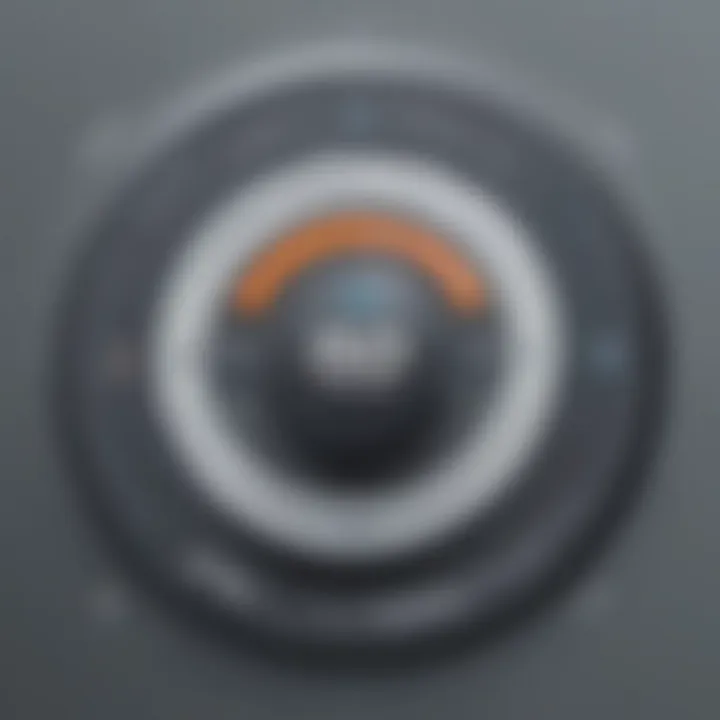
Key Principles of Quality Management
The Key Principles of Quality Management form the bedrock of ISO 9001 compliance. These principles, including customer focus, leadership, engagement of people, process approach, improvement, evidence-based decision making, and relationship management, shape the organizational culture and operations. Implementing these principles fosters a quality-oriented mindset within the organization, driving efficiencies, innovation, and customer satisfaction. Adhering to these principles not only aids in achieving ISO 9001 certification but also propels continuous improvement and sustainable growth.
Benefits of ISO
Embarking on the journey towards ISO 9001 certification reaps various rewards for organizations committed to quality excellence. Enhanced Organizational Efficiency streamlines processes, reduces waste, and optimizes resource utilization. This heightened efficiency leads to cost savings, enhanced productivity, and a more agile operational framework. Improved Customer Satisfaction is another key benefit of ISO 9001 certification, as the quality management system focuses on meeting customer requirements, enhancing productservice quality, and fostering customer trust and loyalty. Satisfying customers through consistent quality outcomes not only drives business success but also reinforces the organization's reputation and market competitiveness.
Preparing for ISO Certification
In this section, we delve into the crucial preparations necessary for achieving ISO 9001 certification. Preparing for ISO 9001 Certification is a pivotal step in the journey towards attaining this renowned quality management standard. It involves meticulous planning, adherence to quality management principles, and aligning organizational processes with the stringent requirements of ISO 9001. By focusing on meticulous preparation, organizations set a strong foundation for the successful implementation and certification of a Quality Management System (QMS). The significance of the preparation phase cannot be overstated, as it lays the groundwork for achieving operational excellence and meeting customer expectations with unmatched quality.
Gap Analysis and Initial Assessment
Identifying Existing Processes and Procedures
Identifying Existing Processes and Procedures forms the cornerstone of Gap Analysis and the initial assessment phase. This pivotal step involves scrutinizing and understanding the current organizational processes, workflows, and systems in place. By meticulously identifying existing procedures, organizations can pinpoint areas that require alignment with ISO 9001 standards. This process allows for a comprehensive evaluation of the organization's operational framework and highlights discrepancies that need to be addressed. The key characteristic of Identifying Existing Processes and Procedures lies in its ability to provide a clear roadmap for organizations to streamline their practices and enhance operational efficiency. This methodical approach enables organizations to identify areas of improvement, rectify inconsistencies, and ensure alignment with ISO 9001 requirements.
Assessing Compliance Gaps
Assessing Compliance Gaps is a critical aspect of the initial assessment stage in preparing for ISO 9001 certification. This process involves evaluating the organization's existing practices against the stringent criteria set forth by ISO 9001. By conducting a thorough assessment of compliance gaps, organizations can identify areas where current practices fall short of the ISO 9001 standard. This assessment highlights deficiencies, non-conformities, and areas requiring immediate attention to ensure compliance with quality management principles. The systematic analysis of compliance gaps provides organizations with valuable insights into areas that need improvement, corrective actions, and process enhancements. Despite the challenges it may reveal, addressing compliance gaps proactively is essential for aligning organizational practices with ISO 9001 requirements.
Quality Management System (QMS) Implementation
Documenting Procedures and Work Instructions
The documentation of procedures and work instructions is a fundamental aspect of Quality Management System (QMS) Implementation. Documenting procedures involves capturing, organizing, and formalizing the processes and instructions that govern various aspects of organizational operations. By meticulously documenting procedures and work instructions, organizations create a comprehensive repository of guidelines that outline how tasks are performed, standards are met, and quality is assured. The key characteristic of documenting procedures and work instructions lies in its ability to provide clarity, consistency, and reference points for employees across levels. This practice ensures continuity of operations, adherence to quality standards, and facilitates the effective implementation of the QMS within the organization.
Training Personnel on QMS Requirements
Training personnel on QMS requirements is a vital component of QMS Implementation. This process involves educating employees at all levels on the requirements, procedures, and guidelines outlined in the Quality Management System. Training personnel on QMS requirements aims to enhance awareness, competence, and compliance with quality management standards. The key characteristic of this training lies in its ability to empower employees with the knowledge and skills necessary to support the successful implementation of the QMS. By equipping personnel with the requisite understanding of QMS requirements, organizations promote a culture of quality, continuous improvement, and active participation in maintaining the ISO 9001 certification.
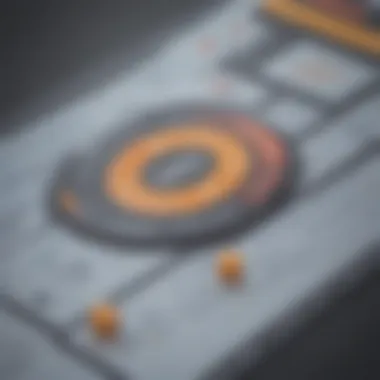
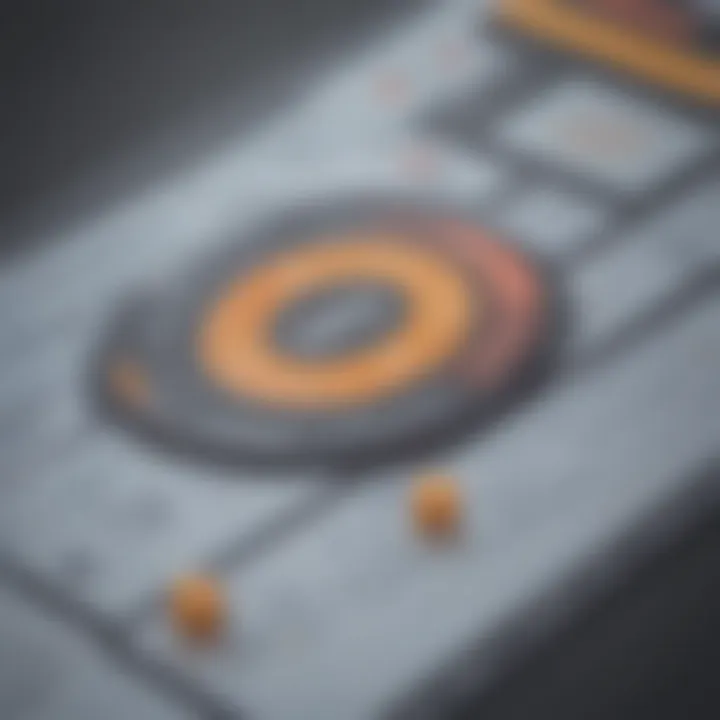
Navigating the Certification Process
Navigating the Certification Process within the context of this comprehensive guide on achieving ISO 9001 certification is a critical phase that organizations must master. This section delves into the intricacies of selecting the right certification body and understanding audit requirements, fundamental elements in the certification journey. By providing detailed insights into these aspects, organizations can enhance their readiness and optimize their certification process. Understanding the nuances of certification bodies and audit requirements is paramount to ensuring a smooth and successful ISO 9001 certification experience.
Choosing a Certification Body
Selecting an Accredited Certification Provider
The selection of an accredited certification provider holds immense significance in the ISO 9001 certification process. Choosing a certification body that holds accreditation adds a layer of credibility and trust to the certification journey. Accredited bodies adhere to stringent quality standards, ensuring that the certification process meets international benchmarks. By opting for an accredited certification provider, organizations can instill confidence in stakeholders regarding the validity and reliability of their ISO 9001 certification. This factor plays a pivotal role in upholding the integrity and authenticity of the certification process outlined in this guide.
Understanding Audit Requirements
Understanding audit requirements is a cornerstone of the ISO 9001 certification process. Comprehending the specific criteria and guidelines set forth by certification bodies is essential for organizational preparedness. By familiarizing themselves with audit prerequisites, organizations can streamline their audit process, prevent deviations, and improve overall audit performance. This proactive approach enables organizations to align their operations with audit expectations, paving the way for a seamless certification journey. Understanding audit requirements creates a framework for organizations to demonstrate conformity to ISO 9001 standards effectively.
Internal Audits and Management Review
Conducting Internal Audits
The process of conducting internal audits serves as a pivotal internal evaluation mechanism within the ISO 9001 certification framework. Internal audits empower organizations to evaluate their quality management system (QMS) against defined criteria and identify areas for improvement. By conducting regular internal audits, organizations can proactively address non-conformities, enhance process efficiency, and uphold QMS effectiveness. This practice not only ensures continual compliance with ISO 9001 standards but also fosters a culture of continuous improvement within the organization. Conducting internal audits is a strategic initiative that drives organizational excellence and operational excellence.
Reviewing QMS Performance
Reviewing QMS performance is a critical component of the ISO 9001 certification process, emphasizing the importance of monitoring and evaluating QMS effectiveness. By reviewing QMS performance, organizations can gauge the success of their quality management initiatives, identify areas of strength and weakness, and recalibrate strategies for optimal performance. This iterative process of performance evaluation enables organizations to refine their QMS, enhance operational efficiency, and elevate customer satisfaction levels. Reviewing QMS performance is a proactive approach that fortifies the foundation of ISO 9001 certification, fostering a culture of quality and organizational improvement.
Preparing for the Final Audit
In the intricate journey towards ISO 9001 certification, the stage of preparing for the final audit holds significant importance. This pivotal phase culminates the rigorous process of aligning organizational practices with the stringent standards set by the International Organization for Standardization. With meticulous attention to detail and adherence to quality management principles, organizations undertake crucial steps to ensure compliance and readiness for the impending audit.
Mock Audits and Corrective Actions
Simulating Certification Audit
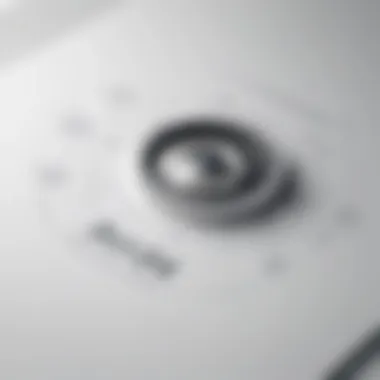
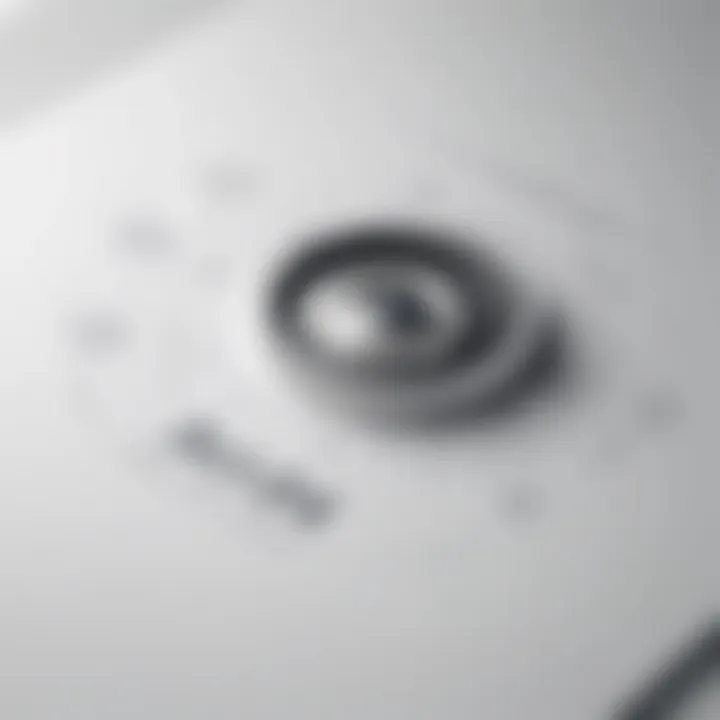
Simulating Certification Audit plays a fundamental role in the preparations for the final ISO 9001 audit. This simulated assessment mirrors the formal certification audit, enabling organizations to identify operational gaps, evaluate process efficiency, and validate the effectiveness of their quality management systems. By emulating real audit scenarios, companies can proactively address deficiencies, refine procedures, and optimize performance, thereby enhancing their prospects of successful certification.
Addressing Non-Conformities
Addressing Non-Conformities stands as a critical aspect of the audit preparation process. By diligently analyzing and rectifying deviations from ISO 9001 requirements, organizations demonstrate their commitment to continuous improvement and regulatory compliance. Resolving non-conformities not only aligns operations with best practices but also showcases a proactive approach towards quality enhancement. Through targeted corrective actions, companies bolster their quality management systems, fostering resilience and sustainability in the face of evolving regulatory landscapes.
Documentation Review and Compliance Check
Ensuring Documented Procedures Accuracy
Ensuring the accuracy of documented procedures serves as a cornerstone in the ISO 9001 certification journey. By meticulously reviewing and validating procedural documentation, organizations establish a robust framework for operational consistency and quality control. Accurate documentation not only safeguards against errors and inconsistencies but also instills confidence in stakeholders regarding the reliability and efficacy of internal processes. Streamlined and precise documented procedures form the bedrock of a resilient quality management system, laying a strong foundation for sustained organizational excellence.
Verifying Compliance with ISO Standards
Verifying compliance with ISO 9001 standards underscores the commitment to upholding industry best practices and regulatory requirements. Through meticulous cross-referencing of documented procedures with ISO 9001 mandates, organizations validate the alignment of their quality management systems with established benchmarks of excellence. This rigorous compliance check not only ensures adherence to regulatory expectations but also cultivates a culture of continual improvement and excellence within the organization. By actively verifying compliance, companies reinforce their dedication to quality assurance and customer satisfaction, positioning themselves as leaders in quality management practices.
Achieving ISO Certification
In the pursuit of ISO 9001 certification, organizations embark on a meticulous journey towards achieving excellence in quality management practices. Attainment of this prestigious certification is not merely a recognition of compliance but a testament to an organization's unwavering commitment to continuous improvement and customer satisfaction. Implementing the ISO 9001 standard necessitates adherence to a structured quality management system designed to enhance operational efficiency, mitigate risks, and foster a culture of excellence within the organization. Organizations that successfully navigate the complexities of ISO 9001 certification stand to gain a competitive edge in the market by demonstrating robust quality management processes that drive organizational success and stakeholder confidence.
Certification Audit Process
On-Site Audit and Evaluation
The on-site audit and evaluation phase of the ISO 9001 certification process plays a pivotal role in assessing the organization's adherence to the standard's requirements within its operational environment. During this critical phase, auditors conduct a comprehensive review of the organization's quality management system, focusing on the implementation and effectiveness of documented processes and procedures. The on-site audit provides auditors with firsthand insights into how the organization functions on a day-to-day basis, allowing them to evaluate the practical application of quality management practices in real-world scenarios. This direct observation enables auditors to identify areas of strength and opportunities for improvement within the organization's quality management system.
Decision on Certification
The decision on certification marks a significant milestone in the ISO 9001 certification journey, as it entails a thorough evaluation of the organization's compliance with the standard's requirements and the effectiveness of its quality management system. Certification bodies review audit findings, observation reports, and corrective actions taken by the organization to address any non-conformities identified during the audit process. The decision to grant ISO 9001 certification is based on the demonstrated ability of the organization to meet the standard's stringent criteria and uphold a consistent level of quality across its operations. Achieving certification signifies the organization's commitment to excellence and serves as a tangible endorsement of its dedication to continuous improvement and customer satisfaction.
Continuous Improvement and Surveillance Audits
Implementing Corrective Actions
Implementing corrective actions is a fundamental aspect of the ISO 9001 certification process that focuses on addressing non-conformities and improving the effectiveness of the quality management system. By systematically identifying and rectifying deviations from the standard's requirements, organizations can enhance their operational efficiency, mitigate risks, and drive ongoing improvement initiatives. The implementation of corrective actions underscores the organization's proactive approach to quality management, highlighting its dedication to upholding the principles of the ISO 9001 standard and delivering consistent quality outcomes.
Periodic Surveillance Audits
Periodic surveillance audits form an essential component of the post-certification phase, ensuring that organizations maintain compliance with the ISO 9001 standard and continually improve their quality management practices. These regular audits serve as checkpoints to assess the organization's ongoing adherence to certification requirements, monitor the effectiveness of implemented quality management initiatives, and identify opportunities for further enhancement. Periodic surveillance audits play a crucial role in validating the organization's commitment to quality excellence and supporting its journey towards sustained performance improvement and customer satisfaction.