Mastering Operations Process Mapping for Efficiency
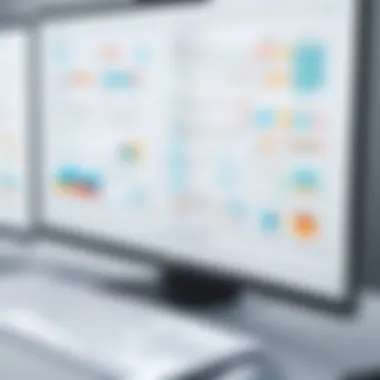

Intro
In today’s fast-paced business environment, efficiency is more than just a buzzword—it's a necessity. Operations process mapping plays a pivotal role in achieving this efficiency by providing a visual representation of organizational workflows. This particular technique allows stakeholders to delve into the workings of operations, pinpoint inefficiencies, and implement strategies to optimize various processes. While it might sound straightforward, there are layers of complexity beneath this essential tool.
The significance of operations process mapping can't be overstated. It serves not only as a diagrammatic tool but also as a linguistic bridge that connects technical staff with management and other stakeholders. Understanding the methodologies that underlie these maps and recognizing how they can be applied across various sectors empowers professionals to make informed decisions. Whether you're part of an IT team aiming to enhance software deployment or a manager looking to streamline production, mastering this domain can make a world of difference.
This article will guide you through the nuances of operations process mapping. By the end, you should have a clearly defined pathway that will enable you to embrace this tool, adjust your operational tactics, and ultimately enhance your organization's efficiency.
Understanding Storage, Security, or Networking Concepts
Intro to the basics of storage, security, or networking
To begin to grasp the essence of operations process mapping, one must first have a foundational understanding of the interconnected roles of storage, security, and networking within an organization. Each of these components is integral to the overall functionality and smooth operation of any workflow.
- Storage involves the management and allocation of digital information. This can range from local databases to cloud environments. Understanding storage concepts ensures that data is accessible and securely managed to support efficient operations.
- Security, as an essential component, encompasses measures and protocols that protect sensitive information. Given the rise of cyber threats, implementing robust security frameworks is non-negotiable for sustaining operational health.
- Networking, which pertains to the connectivity of systems and data flow, underpins all interactions between different platforms and devices within an organization.
Key terminology and definitions in the field
Familiarizing oneself with specific terminology is vital. Here are some terms frequently encountered in operations process mapping and its related domains:
- Data Integrity: Ensures that data remains accurate, consistent, and trustworthy.
- Throughput: The amount of data processed over time, relevant in assessing performance.
- Latency: The time taken to transfer data from one point to another, crucial for optimizing speed and efficiency.
Overview of important concepts and technologies
Numerous concepts and technologies come into play when discussing operations process mapping.
- Workflow Automation: The use of technology to automate complex business processes.
- Lean Methodologies: A mindset focused on reducing waste while maximizing productivity.
- Process Improvement Tools: Such as Six Sigma, which provide frameworks for process refinement.
Understanding these concepts lays a solid groundwork for exploring operations process mapping, as they provide the context in which workflows and efficiencies can be optimized.
Best Practices and Tips for Storage, Security, or Networking
Tips for optimizing storage solutions
- Regular Backups: Always ensure data is backed up to prevent loss.
- Effective Data Organization: Utilize tagging and categorization for easy retrieval.
- Cloud Solutions: Leverage cloud storage for scalability and flexibility.
Security best practices and measures
- Multi-Factor Authentication: Adds an extra layer of security when accessing sensitive information.
- Regular Security Audits: Frequent assessments to identify and mitigate vulnerabilities.
- Employee Training: Equip staff with knowledge on security protocols to prevent breaches.
Networking strategies for improved performance
- Network Monitoring Tools: Solutions like SolarWinds can help keep tabs on performance issues.
- Redundancy Protocols: Implementing backup systems ensures continuity in operations.
- Optimizing Bandwidth: Regularly assess and modify bandwidth usage to prevent congestion.
Industry Trends and Updates
Latest trends in storage technologies
Staying informed about innovations in storage technology is essential. As businesses transition to digital frameworks, AI-driven storage solutions are gaining traction, optimizing the way data is accessed and managed.
Cybersecurity threats and solutions
With threats constantly evolving, organizations must consider advanced methods such as threat detection systems using machine learning to identify anomalies in real-time.
Networking innovations and developments
The advent of 5G technology is ushering in a new era, significantly increasing speed and connectivity options, which will undoubtedly enhance operations across the board.
Case Studies and Success Stories
Real-life examples of successful storage implementations
Many companies have adopted cloud solutions that allow for enhanced storage capacity while reducing costs. For example, a mid-sized retail operation migrated to AWS and saw a 30% reduction in storage costs.
Cybersecurity incidents and lessons learned
The infamous Equifax breach highlighted the importance of regular audits and swift remediation processes. Organizations learned that even a single oversight could have devastating impacts.
Networking case studies showcasing effective strategies
Specific enterprises have implemented software-defined networking to boost agility and performance. An example includes Google, which optimized its data center operations using SDN principles, resulting in lower latency and increased throughput.
Reviews and Comparison of Tools and Products
In-depth reviews of storage software and hardware
Tools like Dropbox and Google Drive have revolutionized how businesses store and share files. Their user-friendly interfaces and collaborative tools have made them a staple for many.
Comparison of cybersecurity tools and solutions
Popular solutions such as Norton and McAfee provide comprehensive protection, but an analysis reveals that ESET offers superior malware detection rates in comparative scenarios.
Evaluation of networking equipment and services
In the realm of networking, Cisco's routers are widely recognized for their reliability, though options like Ubiquiti show remarkable flexibility for scaled-down operations.
By understanding these underpinning systems, professionals can better grasp the mechanics of operations process mapping and how they can employ its methodologies for success.
Prologue to Operations Process Mapping
In the world of managing businesses, operations process mapping is like having a treasure map. It's a tool that highlights the pathways through which work flows, showing where value is added, and where snags might occur. When you look at operations through this lens, you can easily appreciate both the nuances and the overarching structures that drive everyday productivity.
Process mapping can be likened to drawing a blueprint for a complex machine. Each part has its role, much like various processes within an organization. You might think of it as a way to visualize the invisible threads that connect different teams and functions. By employing this technique, companies can unlock several benefits.
Definition and Importance of Process Mapping
Operations process mapping is essentially the graphical representation of workflow and processes. It's vital because it allows organizations to distinctly outline each stage of a process, making it easier to comprehend how tasks interlink and how resources are allocated.
The importance of process mapping cannot be overstated. It helps in:
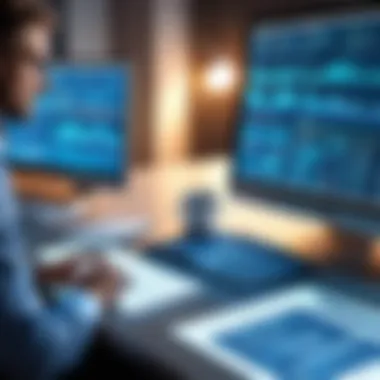

- Identifying inefficiencies: By laying out processes visually, organizations can pinpoint where redundancies occur.
- Enhancing communication: Everyone, from executives to new hires, can understand how things work without getting muddled in jargon.
- Facilitating training: New employees can learn the ropes faster when they have a clear map to guide them.
"Transparency in your operations leads to clarity in your objectives."
Historical Context and Development
To truly grasp operations process mapping, it helps to look back at its evolution. The roots of process mapping can be traced to early practices in manufacturing during the late 19th and early 20th centuries. At that time, thinkers like Frederick Taylor were busy analysis of efficiency and developing time management strategies.
As industries advanced, so did mapping techniques. The introduction of the flowchart in the mid-20th century marked a significant leap, providing managers with a clear visualisation of processes. Over time, methodologies have expanded to include a variety of tools such as swimlane diagrams and value stream mapping, tailored to meet the specific needs of various sectors.
In spirit, operations process mapping today incorporates a blend of both historical insights and modern technological capabilities. With the advancement of software tools, the ability to refine these maps has never been easier, paving the way for organizations to adapt swiftly to ever-changing business landscapes.
Key Components of Operations Process Mapping
Understanding the key components of operations process mapping is vital since these elements form the backbone of effective mapping efforts. They assist organizations in visualizing their workflows, laying out inputs and outputs, and recognizing every player involved in the processes. This clarity not only fosters better efficiency but also creates a more robust framework for evaluating processes, streamlining operations where necessary. Let's unpack this in more detail.
Processes and Workflows
Processes and workflows serve as the fundamental building blocks of any operational framework. A process can be thought of as a series of linked tasks designed to achieve a specific outcome, while workflows illustrate the sequence and flow of these tasks.
Consider this: if a company is assembling a product, the process would outline each step from sourcing materials to final assembly, while the workflow would depict how these steps interlink, like a well-tuned machine.
The key to mastering this component lies in meticulous documentation and clarity in each stage. When processes are clearly laid out, inefficiencies such as bottlenecks become easier to identify. These insights enable informed decision-making that drive improvements. Additionally, having a clear workflow encourages team collaboration and ensures everyone knows their role in the broader picture.
Inputs, Outputs, and Resources
Every successful process necessitates a thorough understanding of inputs, outputs, and the resources at play. Inputs are the various materials, information, or effort required to initiate processes. Outputs quantify what the processes yield, such as finished products or services.
- Inputs: Can include raw materials, labor hours, information, etc.
- Outputs: Could be completed products, deliverables, or even customer satisfaction.
Resources can range from human labor to technology. By critically assessing inputs and outputs, organizations can streamline their processes for maximum output with minimal waste. This optimization is key to maintaining an edge in competitive markets, where efficiency often translates to revenue.
One key point to remember is that having regular reviews of your inputs and outputs enables continuous improvement. Adjustments based on changing demands can make all the difference.
Stakeholders and Their Roles
Finally, no process exists in a vacuum. Stakeholders—everyone from team members and managers to suppliers and customers—play pivotal roles in the outcome of operations.
Understanding who the stakeholders are and clearly defining their roles ensures that everyone is aligned towards common goals. A well-articulated stakeholder map clarifies how each individual's efforts contribute to the overall success of processes. This clarity fosters collaboration and accountability within teams.
Involving stakeholders in the process mapping exercise can also unveil perspectives and insights that might be overlooked otherwise. This collaborative approach allows organizations to tap into collective knowledge, ultimately enriching the process.
"A process is only as strong as its weakest link. Every stakeholder plays a role in bolstering or undermining that strength.”
In summary, focusing on processes, understanding inputs and outputs, and aligning stakeholder roles are crucial in mastering operations process mapping. These components, when effectively harnessed, can lead to enhanced performance, improved workflows, and successful outcomes.
Methodologies for Process Mapping
In the world of operations process mapping, methodologies provide the framework needed to visualize workflows and analyze inefficiencies. Selecting the right methodology is crucial because it shapes how information is gathered and represented. A well-structured approach can reveal insights that not only streamline processes but also enhance overall productivity. Each method has its own characteristics. Hence, it is essential to evaluate them against organizational needs, complexity, and the specific outcomes sought. By comprehensively understanding methodologies, organizations can build robust processes and foster a culture of continuous improvement.
Flowcharting Techniques
Flowcharting techniques represent one of the most straightforward and widely used methodologies for process mapping. Flowcharts employ symbols and arrows to illustrate how tasks flow logically from one stage to another. This visual representation simplifies complex processes and serves as a foundational tool for understanding operations.
- Simple to Understand: Flowcharts are not laden with jargon. They are accessible for teams regardless of technical knowledge.
- Visual Clarity: The use of shapes, such as ovals for start and end points or diamonds for decisions, enhances understanding.
- Identifying Gaps: Gaps or redundancies become visible, allowing immediate attention on areas needing improvement.
Despite their benefits, flowcharts do have limitations. They may become cumbersome with intricate processes, where excessive detail leads to clutter. In such cases, combining flowcharts with other methodologies can yield better results.
Swimlane Diagrams
Swimlane diagrams take flowcharting to another level by adding layers of accountability. This methodology divides activities into lanes that represent different stakeholders or departments. Each lane illustrates who is responsible for what tasks, enhancing clarity and ownership.
- Responsibility Assignment: Swimlane diagrams answer the age-old question: "Who's doing what?" By visually mapping tasks to individuals or teams, it fosters ownership of responsibilities.
- Process Flow: They still maintain a flowchart format, but with added context about who is involved at each step.
- Clear Communication: These diagrams facilitate better communication between teams, as they clearly outline how departments interact.
Swimlane diagrams may prove beneficial in highly collaborative environments but can become overwhelming in processes with numerous stakeholders. Finding the right balance of detail is crucial.
Value Stream Mapping
Value stream mapping, often associated with Lean practices, focuses on optimizing the flow of materials and information. This methodology involves mapping out all steps—value-adding and non-value adding—in a process. By scrutinizing the entire process, teams can identify waste and enhance efficiency.
- Waste Identification: Value stream mapping is particularly effective at exposing waste, offering a path to actionable improvements.
- Holistic View: It encourages teams to see the process as a whole rather than in isolated parts, paving the way to integrated solutions.
- Collaborative Effort: Engaging diverse team members in this mapping serves as a powerful tool for collective improvement.
However, value stream mapping requires detailed understanding and accurate data gathering. It might also be less effective in environments where processes are less stable or frequently change.
Business Process Model and Notation (BPMN)
Business Process Model and Notation (BPMN) represents a standardized method for mapping processes. Unlike the more casual flowcharting or swimlane approaches, BPMN provides a set of symbols and rules, making it a rigorous language for modeling processes.
- Standardization: With BPMN, there's a common language that transcends different departments and industries. This accelerates understanding among varied stakeholders.
- Detail and Precision: This methodology can capture intricate details, making it suitable for complex processes.
- Automatable: BPMN diagrams lend themselves to automation more readily than other methodologies, which can align with technology-driven organizations' goals.
Despite these strengths, BPMN can feel overwhelming to those unfamiliar with its symbols. Adequate training and practice are often necessary to reap its full benefits.
"Choosing the right process mapping methodology is akin to selecting the right tool for the job; it can vastly influence the results you achieve."
Identifying Areas for Improvement
Identifying areas for improvement is a crucial step in operations process mapping. Without this phase, any effort put into mapping may end up as just a theoretical exercise. This part deals with understanding where things might be going wrong and how processes can be enhanced to promote efficiency. It’s not just about spotting errors; it’s about looking for opportunities to optimize workflows, and effectiveness.
Analyzing Current Processes
To kick things off, organizations need to thoroughly analyze their current processes. This analysis goes beyond merely looking at what employees do on a daily basis. It should involve collecting data on each step of a process—the time, resources, and efforts involved.
An effective way to grasp current practices is to use tools like flowcharts or swimlane diagrams. By visually representing steps, stakeholders can gain a better understanding of workflows. Here's what to consider:
- Data Collection: Gather quantitative data, like timing how long each task takes. This will reveal areas that may need faster processing.
- Feedback from Employees: Since they’re in the trenches, employees can provide insights about inefficiencies that might not be visible to management.
- Current Performance Metrics: How does the current performance stack up against industry benchmarks? Identifying gaps can provide a target for improvement.
This initial step lays the groundwork for unveiling hidden issues and setting a base for subsequent measures.
Recognizing Bottlenecks and Inefficiencies
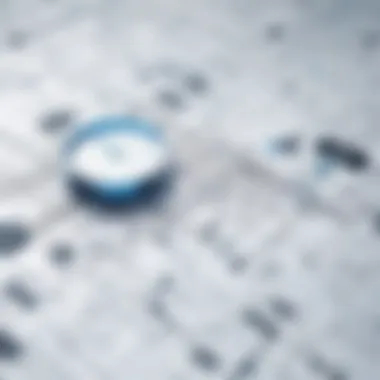

Next up is recognizing bottlenecks and inefficiencies. In any workflow, bottlenecks can act like a ripple in a pond. They slow down the entire process, leading to delays and frustrated stakeholders. Identifying these problem areas is essential to streamline operations effectively.
Common signs that a bottleneck may exist include:
- Long Wait Times: Are tasks piling up in one specific point within a process?
- Error Rates: High rates of mistakes often point to unclear processes or too much pressure at certain points.
- Employee Feedback: Listen to the team; they often know where the pinch points are.
A helpful method is using a cause-and-effect diagram, which visually lays out problems and potential causes. This way, it’s easier to address the roots of inefficiencies rather than just the symptoms.
Setting Measurable Objectives
Finally, setting measurable objectives is about defining what success looks like after identifying areas for improvement. Without clear objectives, it can be challenging to measure the effectiveness of any changes made.
Here’s how organizations can set those objectives:
- SMART Goals: Ensure goals are Specific, Measurable, Achievable, Relevant, and Time-bound. For example, reducing processing time by 20% within six months gives a clear target.
- Key Performance Indicators (KPIs): Develop KPIs that reflect both efficiency and effectiveness. These could include throughput rate or error rate.
- Continual Review: Objectives should be revisited regularly to adapt. If a process improves but performance stalls, reassess the situation and set new targets.
Setting these measurable benchmarks will mark a clear direction for improvement efforts. As simple as it sounds, having these targets aligns everyone towards common goals and promotes accountability.
"Identifying areas for improvement is like hunting for treasure hidden within the depths of an organization’s processes. It requires patience, keen observation, and a willingness to delve deeper. Only then can the gems of efficiency be uncovered."
Implementing Process Mapping in Organizations
Implementing process mapping in organizations is like laying down a roadmap to navigate through the intricacies of workflows. It sheds light on the various tasks, the people involved, and the information needed to keep everything churning smoothly. The huge advantage of this implementation is that it goes beyond just visualizing processes; it empowers teams to pinpoint inefficiencies and foster improvement. If organizations really want to boost their efficiency and decision-making capabilities, this step is essential.
Gathering Data and Requirements
Before diving headfirst into process mapping, gathering data and requirements is akin to gathering all the tools before a big repair job. The data comes from various sources, like existing documentation, interviews, and observations. It involves engaging with the folks who are in the trenches, day in and day out, to truly get a handle on how things work.
Key aspects to consider when collecting data include:
- Current Documentation: Examine what’s already available. This could include process documents, previous mapping efforts, or performance reports.
- Stakeholder Interviews: Talk to the people involved in the processes. They can provide insights that are often not captured in documents.
- Observational Research: Sometimes, seeing things first-hand offers a perspective that is hard to put down in writing. Watch how tasks are executed and identify pain points.
By being thorough in this phase, organizations can ensure that the resulting maps are not only accurate, but also relevant. This solid foundation sets the stage for successful mapping later on.
Engaging Stakeholders
Engaging stakeholders isn’t mere window dressing; it’s a critical part of the process. Think of it as forming a team to tackle a complex puzzle where every piece matters. Stakeholders vary from department heads to frontline employees, and their buy-in is what will power the initiative.
To effectively bring stakeholders into the fold, consider these points:
- Communicate the Vision: It’s vital to articulate what process mapping is all about and why it’s important. The clearer the vision, the more likely they are to get on board.
- Encourage Input: Make it clear that everyone’s perspective is valuable. This not only improves the quality of the maps but also fosters a sense of ownership.
- Regular Updates: Keep stakeholders in the loop with progress reports. Transparency breeds trust, and it ensures that everyone feels involved in the journey.
When organizations engage stakeholders thoughtfully, it leads to a more comprehensive and accurate representation of processes, while also paving the way for smoother implementation.
Drafting the Initial Map
After gathering information and getting stakeholders engaged, the next logical step is drafting the initial map. This is where the dots start connecting, and the design takes shape. Initial mapping should be an iterative process—more like sketching a blueprint than painting a masterpiece. It’s about visualizing processes in a way that highlights flows, roles, and information.
As organizations create these maps, they should keep the following in mind:
- Clarity is Key: Use clear symbols and terminology. A flowchart that looks like a jigsaw puzzle won’t help anyone.
- Focus on the Big Picture: While details are important, it’s essential to maintain a holistic view. Start with broader steps before drilling down into specifics.
- Collaborative Refinement: Once the initial draft is ready, get feedback from stakeholders. This might lead to necessary adjustments that sharpen the map.
The goal is to craft a map that encapsulates operations effectively. This initial document serves as a launching pad for discussions about further improvements and efficiencies that can be achieved.
Tools and Software for Process Mapping
In the realm of operations process mapping, having the right tools and software can be a game changer. These resources not only facilitate clear visualization of workflows but also enhance analysis and optimization efforts. By leveraging specialized applications, organizations can streamline their processes, making it easier to identify inefficiencies while engaging team members in collaborative efforts.
Overview of Popular Tools
When selecting tools for process mapping, it's crucial to understand what options are available and how they serve different needs. Here are some notable tools that come highly recommended:
- Lucidchart: This cloud-based platform offers intuitive drag-and-drop functionalities. Its ease of use makes it a go-to choice for many users. Ideal for teams spread across various locations, the real-time collaboration feature enables concurrent edits.
- Microsoft Visio: A classic in the world of diagramming, Visio integrates well with other Microsoft Office applications. It's great for creating detailed diagrams, and its templates can serve as a starting point for new users.
- Bizagi: Known for its PowerModeling technology, Bizagi facilitates the creation of process models without necessitating extensive technical knowledge. It’s particularly useful for its capabilities in business process management and automation.
- Miro: This collaborative platform fuses visual project management with process mapping. It effectively promotes brainstorming sessions and can help in the construction of mind maps combined with process flows.
- Draw.io: A versatile tool that operates within web browsers, it supports various diagram types and can also integrate with platforms like Google Drive and GitHub for easy sharing and collaboration.
These tools, among others, serve diverse functions, allowing IT professionals and project managers to tailor their solutions to specific workflow needs.
Evaluating Software Based on Needs
Choosing the right software isn't merely about preference. It requires a thoughtful evaluation of several key aspects that can significantly affect the user experience and the effectiveness of process mapping.
- User-Friendliness: Consider how intuitive the interface is. A steep learning curve can slow down implementation and reduce overall adoption by team members.
- Compatibility: Ensure the software aligns with existing tools within your organization. Compatibility can streamline collaboration and reduce friction when transitioning to a new platform.
- Customization Options: Look for tools that allow customization of maps and workflows. This gives teams freedom to design processes that accurately reflect their operations.
- Collaborative Features: In today's hybrid work setups, it’s essential that software facilitates teamwork. Public or shared access, commenting capabilities, and version control are important here.
- Integration with Other Systems: Evaluate how well the tool integrates with databases, project management software, or other relevant platforms. This will ensure a smoother flow of information and reduce redundant data entry.
- Scalability: As organizations grow, their process mapping needs may change. Choose tools that can scale alongside your operations to avoid future headaches or the need to retrain staff on different software.
"The tools you choose for process mapping can shape the way your organization operates. It’s like picking the right set of tools for a craftsman; the right choice can mean the difference between seamless productivity and chaos."
By carefully considering these factors, businesses can select the software that not only meets their current needs but also positions them for future success in operations management.
Case Studies and Applications
Case studies and applications allow organizations to see practical examples of how operations process mapping can bring significant values. These real-world instances illuminate how specific industries, such as manufacturing, healthcare, and service sectors, use process mapping to tackle their unique challenges and improve efficiency. By examining these successful applications, one can glean insights and strategies that can be adapted and implemented within their own contexts. Additionally, these examples highlight the benefits of process mapping in driving continuous improvement and fostering collaboration among stakeholders.
Manufacturing Sector Examples
In the manufacturing realm, precision and efficiency are paramount. Take, for instance, the case of Toyota and its famous Production System, which exemplifies the application of process mapping. The company implemented value stream mapping to identify waste in its production processes. Through this detailed analysis, Toyota pinpointed non-value-adding activities and streamlined workflows. As a result, they minimized lead times, improved quality, and ultimately enhanced customer satisfaction.
Another notable case is General Electric. They utilized process mapping in their Six Sigma initiatives. By mapping their electrophysical manufacturing operations, GE was able to highlight defects in processes and engineer solutions that led to substantial cost savings and reduced process cycle times. Thus, it becomes evident that for manufacturing firms, clear process mapping can lead not only to operational efficiency but also to a competitive edge in a crowded marketplace.
Healthcare Process Mapping
Healthcare services often run into complexities that can be difficult to navigate. For example, consider the application of process mapping at Virginia Mason Medical Center. They adopted a Lean approach and employed process mapping to visualize the flow of patient care. Through this process, they identified bottlenecks in patient flow that caused delays. By addressing these points, they optimized waiting times and improved overall patient experience.
Additionally, Cleveland Clinic applied operations process mapping to streamline its scheduling system for surgeries. By thoroughly analyzing their procedures, they were able to enhance coordination among various departments, cut down on scheduling errors, and ultimately increase the number of surgeries performed each day. This not only improved patient care but also maximized the use of their surgical facilities, demonstrating the profound impact of effective process mapping in healthcare settings.
Service Industry Applications
In the bustling service sector, operational efficiency frequently determines the level of customer satisfaction. A prominent example can be found in the fast-food giant McDonald's. By implementing process mapping, McDonald's was able to standardize their service delivery across various locations, ensuring consistent quality and quick service times. Their detailed mapping of food preparation and service processes led to the development of training protocols that improved staff performance and customer experiences.
Another compelling case is that of Airbnb. The company faced challenges in customer service as they scaled. By employing process mapping, they were able to identify pain points in customer interactions and streamline their support processes. This led to a more seamless experience for their users, showcasing how even technology-driven businesses can benefit from traditional process mapping techniques.
In essence, case studies across various sectors reveal that operations process mapping is not just an academic exercise, but a tangible strategy to enhance productivity and meet ever-evolving customer demands. Leveraging such examples can inspire organizations to embrace process mapping and adapt it for their distinct challenges.
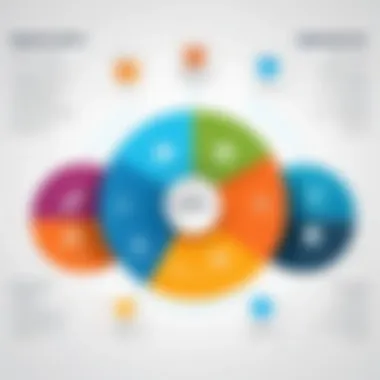

Benefits of Operations Process Mapping
Operations process mapping offers a variety of advantages that can significantly impact an organization’s performance. By providing a clear visual representation of workflows, it empowers stakeholders to delve deeper into how processes operate, which is essential for identifying bottlenecks, inefficiencies, and opportunities for optimization. Below are key benefits that underscore its importance:
Enhanced Efficiency and Productivity
One of the primary benefits of process mapping is its potential to boost efficiency and productivity. When processes are visually mapped out, it becomes easier to see redundancies or unnecessary steps. This clarity allows teams to:
- Eliminate Waste: By identifying non-value-adding activities, organizations can streamline workflows. For instance, if an employee spends too much time on a redundant approval step due to unclear communication, removing that step can accelerate project timelines.
- Standardize Processes: Mapping encourages consistency in operations. When everyone follows the same process, it reduces errors and variability. For example, a well-defined customer service process can ensure that every representative addresses inquiries uniformly, improving the customer experience.
- Use Resources Wisely: Understanding detailed processes helps manage resources efficiently. When teams know the workflow inside and out, they can allocate staff and tooling effectively without overloading any single part of the operation.
Improved Communication and Collaboration
In organizations, communication is key. Maps provide a common language—visual aids that foster alignment across teams. This helps in:
- Breaking Down Silos: Different teams may operate in isolation. When everyone can see the full process, it promotes collaboration. A design team can understand the production constraints, while the marketing team aligns its campaigns with production timelines.
- Clarifying Roles: Using a process map, stakeholders can identify their responsibilities. This brings accountability to the forefront. Say, a new software update requires input from IT and marketing; a clearly defined map will help delineate who needs to contribute what information and when.
- Encouraging Feedback: With a visual aid in hand, teams can easily offer insights and suggestions for improvement. The process can evolve based on feedback from those directly involved.
Facilitating Continuous Improvement
Process mapping is not a one-and-done task; it is a vital part of fostering a culture of continuous improvement. It allows organizations to:
- Regularly Assess Processes: Having a visual guide makes it easier to review operations periodically. Teams can come together to assess what’s working and what isn’t during reviews. A utility company, for instance, can pinpoint inefficiencies in their outage response process over time.
- Adapt to Changes: As industries evolve, organizations also need to pivot. A process map provides a framework for integrating new practices seamlessly. When regulations change in healthcare, for example, a mapping exercise allows staff to adapt quickly while maintaining compliance.
- Drive Innovation: Lastly, seeing the entire process can inspire creative solutions. When teams understand the challenges they face, they can brainstorm innovative methods to tackle them. Think of an automotive manufacturer rethinking assembly line efficiency by incorporating just-in-time parts arrival, showcased in their process map.
"Operations process mapping is a compass; it shows where you are now and guides you to where you want to be."
With these benefits in mind, it is clear that conducting operations process mapping isn’t just about creating a visual aid; it's about setting the stage for enhanced performance, improved teamwork, and a culture that eagerly embraces change.
Through a combination of efficiency, collaboration, and a commitment to improvement, organizations can harness process mapping to elevate their operational success.
Challenges in Process Mapping
In the realm of operations process mapping, acknowledging challenges isn't just an afterthought; it's a cornerstone for successful implementation. The process may appear straightforward at first, but the complexities can be quite staggering. Various factors influence how well an organization can adopt and use process mapping effectively. This section will delve into three primary hurdles: resistance to change, maintaining accuracy and relevance, and managing complexity.
Resistance to Change
One of the most formidable barriers to effective process mapping comes from within the organization itself—resistance to change. It's a universal truth that people often cling to the familiar, even when it's inefficient or outdated. When you introduce new workflows and methodologies, it can feel like shaking the foundation of their daily routines.
Employees might feel threatened, fearing they will lose their job or that the new processes will complicate their work. Such sentiments need careful navigation. To address this, management should prioritize communication and education. Citing relevant examples from successful implementations can foster understanding and acceptance—showing staff that change can lead to personal career growth.
- Training sessions can build skills and confidence.
- Feedback mechanisms allow employees to voice concerns, ensuring they feel heard.
- Involving key team members during the mapping process can pave the way for buy-in.
Maintaining Accuracy and Relevance
Another critical challenge revolves around the accuracy and relevance of the processes being mapped. Any inaccuracies can mislead stakeholders and inhibit the overall benefits sought from process mapping. It's important to remember that what worked yesterday might not work today in a fast-evolving environment. Thus, mapping needs to be a living document—dynamic and responsive to changes in workflows, regulations, and industry standards.
To maintain accuracy, regular reviews are essential:
- Create a schedule to refine maps routinely.
- Implement metrics to track process performance.
- Engage stakeholders frequently to ensure all voices are considered.
By doing this, organizations can ensure that their process maps reflect reality rather than a static snapshot.
Managing Complexity
Lastly, the sheer complexity of modern operations can intimidate even the most seasoned professionals. As businesses scale, their processes grow intricate, with numerous interdependencies and stakeholders involved. Mapping out these processes may become an overwhelming task, leading to confusion rather than clarity.
To tame this complexity, here are several strategies:
- Break processes down into manageable chunks. Trying to visualize everything at once can lead to a cluttered and confusing mapping.
- Use visual aids like swimlane diagrams and flowcharts to demystify workflows, showing how different departments interact within the process.
- Prioritize the development of a few key processes before expanding the mapping efforts to more intricate operations.
"Simplicity is the ultimate sophistication." - Leonardo da Vinci. Keeping this in mind will help steer efforts toward clarity.
In summary, addressing resistance to change, ensuring accuracy and relevance, and managing complexity are fundamental challenges that require careful consideration. Overcoming these obstacles not only results in better process mapping but also paves the way for enhanced organizational efficiency.
Future Trends in Process Mapping
As organizations continuously evolve, understanding the future trends in process mapping becomes crucial. This section delves into how these trends can significantly enhance operational efficiency, adaptability, and overall effectiveness. Incorporating up-to-date methodologies keeps stakeholders on their toes and helps in making timely decisions that are vital in today's fast-paced environment. Knowing what's coming around the bend can arm professionals with the foresight necessary to stay competitive and agile.
Integration with Advanced Technologies
Integrating advanced technologies into operations process mapping is changing the game. With tools like Internet of Things (IoT) devices, cloud computing, and big data analytics, organizations can gain unprecedented insights into their workflows. Here are some elements to consider:
- Real-Time Data Collection: Technologies facilitate live monitoring of processes. This means managers can track progress as it happens, spotting glitches faster than ever before.
- Enhanced Visualization Tools: Virtual reality (VR) and augmented reality (AR) are beginning to make waves in process mapping. Imagine walking through a process in a 3D environment, identifying inefficiencies while experiencing the actual workflow.
- Informed Decision-Making: Advanced analytics sift through data to present actionable insights, helping companies decide not just based on instinct but on solid evidence of what works best.
Being open to adopting these technologies can lead to greater precision in process mapping. As businesses embrace these changes, the potential for improved efficiency becomes increasingly tantalizing.
AI and Automation in Process Mapping
Artificial Intelligence (AI) is reshaping various facets of business operations, including process mapping. The integration of AI leads to automation, efficiency, and decision-making improvements. Here’s how:
- Predictive Analytics: AI algorithms analyze historical data to forecast future process outcomes. This foresight allows businesses to anticipate bottlenecks before they occur, thus minimizing disruptions.
- Automated Workflows: Routine and repetitive tasks can be automated, freeing up employees to focus on more strategic activities. For instance, AI can handle basic data entry, allowing human resources to focus on cultivating talent.
- Adaptive Learning: Machine learning capabilities enable processes to evolve based on past performance. Processes can automatically adjust to enhance productivity without constant human intervention.
Investing in AI not only streamlines operations but also equips organizations with tools for future adaptability. Businesses that harness these technologies will not only survive but thrive in the competitive landscape.
"The need for organizations to embrace these trends isn't just about keeping up but ensuring they lead the pack in efficiency and effectiveness."
This understanding can help to enhance decision-making capabilities and lead organizations into a more productive future.
Culmination and Key Takeaways
In the realm of organizational excellence, operations process mapping stands as a foundational tool that not only elucidates workflows but also enhances a company’s ability to pinpoint inefficiencies. Throughout this article, we've journeyed through the intricate layers of process mapping, revealing its critical role in meeting the demands of operational efficiency and effectiveness. The essence of operations process mapping lies in its capability to provide transparency within complex systems, allowing stakeholders to visualize the flow of activities from start to finish.
Summarizing the Importance of Process Mapping
To crystallize the significance of process mapping, one must recognize its multifaceted benefits:
- Visual Clarity: Process mapping employs visual tools like flowcharts and diagrams to help decipher convoluted workflows, making it easier for teams to understand their roles in the bigger picture.
- Enhanced Communication: By presenting processes graphically, process maps bridge the gap between various stakeholders, from front-line employees to management, fostering a common understanding of workflows and expectations.
- Identification of Improvement Opportunities: Without a doubt, one of the most potent applications of process mapping is its ability to spotlight bottlenecks and redundancies. This capability drives organizations toward a continuous improvement mindset.
- Standardization of Processes: Documenting processes gives organizations a solid foundation upon which they can build standardized practices. This standardization leads to consistent output and better quality control.
In essence, the significance of process mapping cannot be overstated. It is akin to providing a road map for a traveler; without it, the journey can become aimless and fraught with obstacles.
Encouraging Continuous Learning
The advent of technology and the ever-evolving landscape of business necessitates that professionals engage in a culture of continuous learning regarding operations process mapping. Here are a few key considerations to promote this mindset:
- Stay Updated: With trends like automation and AI integration gaining traction, keeping abreast of recent developments in process mapping methodologies is crucial. Engaging with forums or communities on platforms such as Reddit can spark new ideas and insights.
- Iterative Learning: Practicing regularly with tools and techniques discussed in this article reinforces learning. Simulation exercises can help drill down core principles effectively.
- Seek Feedback: Actively inviting feedback from peers and superiors on process mapping outputs can facilitate deeper understanding and skill enhancement.
- Industry-Specific Knowledge: Since different sectors face unique challenges, tailoring one’s learning around industry-specific applications of process mapping can add significant value. Consider exploring resources like encyclopedic entries to gather context.
By fostering a commitment to constant development, organizations can ensure their operations process mapping efforts remain relevant and impactful, creating pathways for enhanced decision-making and strategic alignment. In a world that thrives on adaptability, embracing learning as a continuous journey is not just beneficial; it's vital.