Revolutionizing Work Efficiency: A Comprehensive Guide to Lean Work Processes
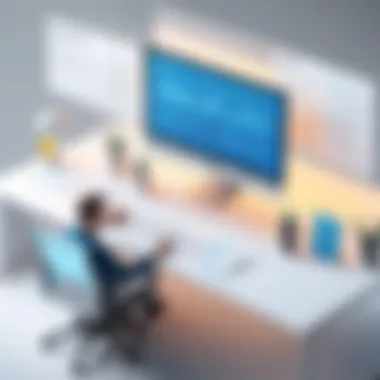
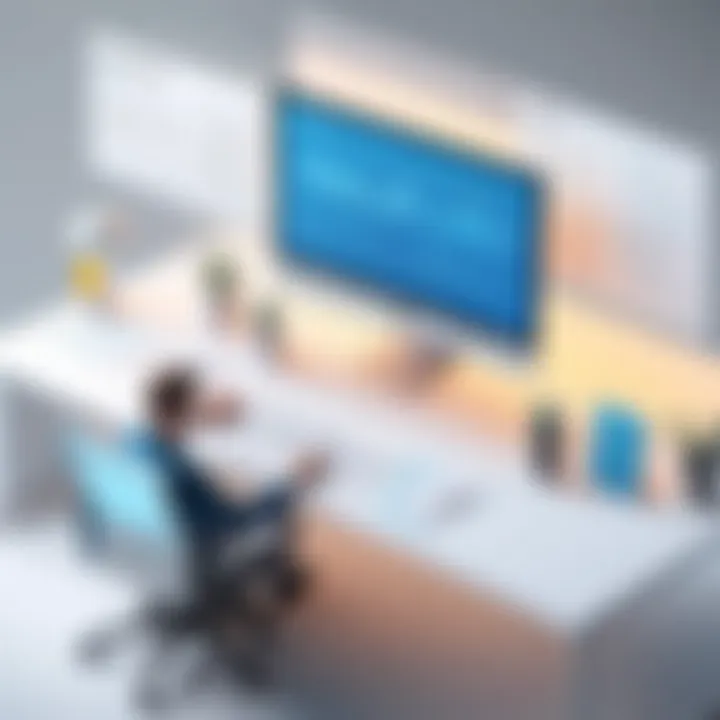
Understanding Lean Work Processes
In this section, we delve into the essence of lean work processes, unraveling the strategies essential for enhancing productivity, efficiency, and a culture of constant improvement in organizational operations. By grasping the fundamental principles of lean management and applying practical workflow optimization techniques, professionals can gain invaluable insights to revolutionize their work processes and drive sustained success.
Best Practices and Tips for Enhanced Productivity
Discover the key strategies for optimizing work processes in this segment. Uncover invaluable tips for maximizing productivity, fine-tuning efficiency, and fostering a workplace ethos of continuous enhancement. By incorporating these best practices, professionals can streamline workflow operations, eliminate redundancies, and cultivate a culture that prioritizes productivity and efficiency.
Leverage Industry Trends and Innovations
Stay at the forefront of work process optimization by exploring the latest industry trends and developments. From cutting-edge technologies shaping workflow efficiency to innovative strategies propelling organizational success, this section provides insights into groundbreaking trends reshaping the landscape of work process optimization. Gain a deep understanding of the evolving dynamics that can drive productivity and competitiveness in the modern workplace.
Real-life Case Studies and Success Blueprints
Engage with real-world examples of successful work process optimizations through insightful case studies. Gain practical insights from success stories that showcase effective strategies and lessons learned from implementing lean principles. Assess cybersecurity incidents, storage transformations, and networking maneuvers that have reshaped organizational operations, offering inspiring stories that illuminate the path to optimized work processes.
Detailed Evaluation of Tools and Products
Dive into a comprehensive evaluation of tools and products instrumental in optimizing work processes. Uncover in-depth reviews of software and hardware solutions, comparative analysis of cybersecurity tools, and critical assessments of networking equipment and services. Through this detailed exploration, professionals can make informed decisions on adopting tools that align with their work process optimization goals.
Introduction to Lean Work Processes
The concept of lean work processes is foundational in the optimization of organizational productivity. In our comprehensive guide to Lean Work Processes, we delve into strategies that streamline operations, enhance efficiency, and cultivate a culture of perpetual enhancement. Understanding and implementing lean management principles is crucial for businesses aiming for sustainable success. By embracing lean practices, companies can revolutionize their work methodologies, allowing for quicker adaptation to market fluctuations and improved customer satisfaction, among other benefits.
Defining Lean Management
The Origins of Lean Thinking
The Origins of Lean Thinking trace back to the Toyota Production System in Japan, where the methodology was first developed. This approach emphasizes the elimination of waste, continuous improvement, and respect for people. One key characteristic of The Origins of Lean Thinking is its focus on creating value for customers while minimizing resources, a strategy particularly relevant in today's competitive business landscape. The unique feature of The Origins of Lean Thinking lies in its holistic approach to efficiency, addressing not just the production process but also the entire value stream.
The Principles of Lean Work Processes
The Principles of Lean Work Processes are rooted in the core ideologies of lean management, including the elimination of waste, respect for people, and continuous improvement. One key characteristic of these principles is their adaptability across various industries, making them a popular choice for organizations seeking operational excellence. The unique feature of The Principles of Lean Work Processes is their ability to create a culture of continuous improvement, encouraging employees at all levels to identify and address inefficiencies proactively.
Benefits of Implementing Lean Practices
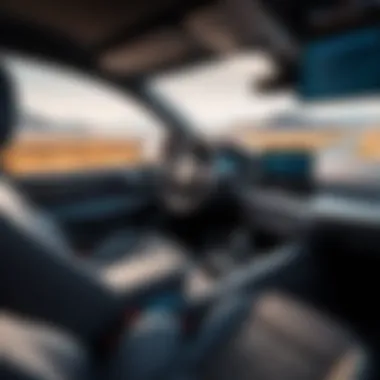
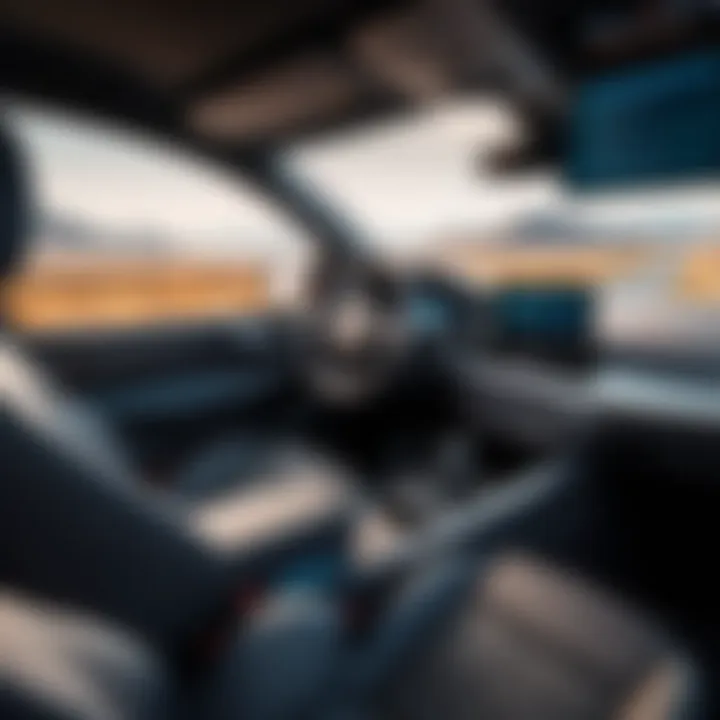
Enhanced Efficiency
Enhanced Efficiency is a central aspect of lean practices, focusing on optimizing workflows to reduce lead times and enhance productivity. By improving process efficiency, organizations can cut down on wasted resources and operate more competitively in the market. The unique feature of Enhanced Efficiency lies in its ability to streamline operations without compromising quality standards, ultimately driving sustainable growth for businesses.
Reduced Waste
Reducing Waste is a key benefit of implementing lean practices, as it allows organizations to eliminate non-value-adding activities and optimize resource usage. This not only minimizes costs but also supports environmental sustainability by reducing unnecessary consumption. The unique feature of Reduced Waste is its focus on continuous improvement, where even small adjustments can lead to significant long-term benefits for the organization.
Improved Quality Standards
Enhancing Quality Standards is another prominent advantage of lean practices, as it cultivates a culture of excellence and customer satisfaction. By emphasizing quality in every aspect of the operation, businesses can build trust with their clientele and establish a solid reputation in the market. The unique feature of Improved Quality Standards is their impact on overall organizational performance, influencing everything from employee morale to brand loyalty.
Core Concepts of Lean Work Processes
In the realm of optimizing work processes, understanding the core concepts of Lean Work Processes is paramount. This section delves into the fundamental principles that drive efficiency and productivity within organizations. By grasping the essence of Lean principles, companies can streamline their operations, reduce wastage, and enhance overall quality standards. The essence of Lean Work Processes lies in focusing on value-adding activities while eliminating non-value-adding tasks, which ultimately leads to a more streamlined and effective workflow.
Value Stream Mapping
Identifying Value-Adding Activities
Discussing identifying value-adding activities is pivotal in the context of Lean Work Processes. This process involves analyzing each step of the workflow to pinpoint activities that directly contribute to the final product or service. By identifying and emphasizing value-adding activities, companies can optimize their processes, reduce unnecessary tasks, and enhance overall productivity. The key characteristic of identifying value-adding activities lies in its ability to maximize resource utilization and output efficiency, making it a popular choice in Lean methodologies. The unique feature of this practice is its focus on enhancing output quality and customer satisfaction while minimizing operational inefficiencies.
Eliminating Non-Value-Adding Tasks
Conversely, eliminating non-value-adding tasks is equally crucial in Lean Work Processes. This entails recognizing and removing activities that do not contribute to the end product or service. By eliminating such tasks, organizations can enhance their operational efficiency, reduce waste, and improve overall process effectiveness. The key characteristic of eliminating non-value-adding tasks is its impact on streamlining workflows and optimizing resource allocation, making it a beneficial choice for Lean implementations. The unique feature of this practice lies in its ability to enhance cost-effectiveness and operational transparency while minimizing downtime and resource misallocation.
Kaizen Philosophy
Continuous Improvement Culture
The concept of a continuous improvement culture is foundational to Lean Work Processes. By fostering a culture that values ongoing enhancements and innovations, organizations can continuously evolve and adapt to market changes. The key characteristic of a continuous improvement culture is its emphasis on employee involvement and feedback integration, making it a popular choice in Lean environments. The unique feature of this aspect is its ability to promote adaptability, creativity, and proactive problem-solving within teams, leading to sustained growth and competitiveness.
Pursuit of Perfection
Aligned with continuous improvement is the pursuit of perfection, a core tenet of Lean methodologies. By striving for perfection in all processes and outcomes, organizations can set high standards for quality and performance. The key characteristic of the pursuit of perfection is its commitment to excellence and precision, making it an essential choice for driving operational excellence in Lean contexts. The unique feature of this philosophy lies in its insistence on constant refinement, innovation, and adherence to best practices, ensuring long-term success and customer satisfaction.
Just-in-Time Production
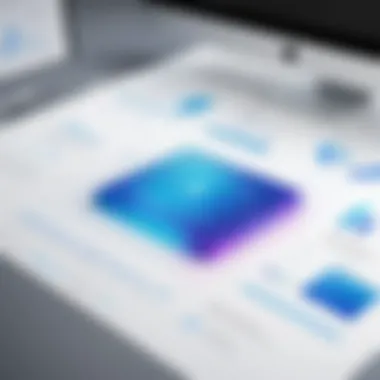
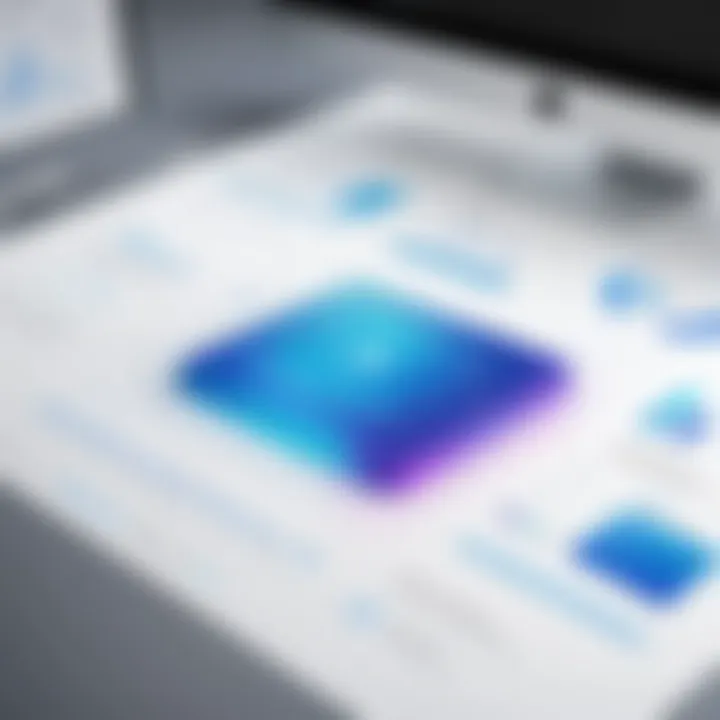
Reducing Inventory
Reducing inventory levels is a critical aspect of Just-in-Time production, a cornerstone of Lean Work Processes. By minimizing excess stock and materials, companies can operate more efficiently, reduce storage costs, and improve responsiveness to customer demand. The key characteristic of reducing inventory is its focus on flexibility and waste reduction, making it a valuable choice for enhancing operational agility in Lean frameworks. The unique feature of this strategy is its ability to enhance cash flow, minimize obsolescence risks, and improve overall supply chain efficiency.
Minimizing Lead Times
Minimizing lead times is another key component of Just-in-Time production within Lean methodologies. By reducing the time taken to fulfill orders and deliver goods or services, organizations can enhance customer satisfaction, responsiveness, and operational efficiency. The key characteristic of minimizing lead times is its focus on speeding up processes, eliminating bottlenecks, and enhancing overall workflow effectiveness, making it a preferred choice for Lean practitioners. The unique feature of this approach lies in its ability to drive competitive advantage, enhance market positioning, and foster a culture of timeliness and reliability within organizations.
Practical Strategies for Implementing Lean Work Processes
In the realm of optimizing work processes, the Practical Strategies for Implementing Lean Work Processes section holds paramount significance. This section delves into actionable methodologies that organizations can use to streamline their operations and boost efficiency. By adopting the 5S Methodology, Kanban System, and Root Cause Analysis, companies can achieve notable improvements in productivity and quality standards. Implementing lean practices through practical strategies is crucial for ensuring sustainable success and driving continuous improvement within organizational workflows.
5S Methodology
Sort
Sorting, as a crucial aspect of the 5S Methodology, plays a pivotal role in eliminating clutter and organizing workspaces efficiently. By categorizing items based on their necessity and relevance, organizations can optimize space utilization and enhance operational efficiency. The key characteristic of sorting lies in decluttering, resulting in a cleaner and more organized work environment. Through systematic sorting, companies can improve productivity and minimize the time spent searching for tools or documents, ultimately leading to enhanced workflow efficiency.
Straighten
Straightening focuses on arranging items in a structured manner to promote visual management and easy access. This key aspect of the 5S Methodology emphasizes the importance of organizing workstations to enhance workflow visibility and productivity. By maintaining a neatly arranged workspace, employees can locate necessary tools or materials promptly, reducing downtime and improving overall operational efficiency. The unique feature of straightening lies in its ability to create a well-organized and visually appealing workspace, boosting worker morale and efficiency.
Shine
Shining involves cleaning and maintaining workspaces to uphold cleanliness standards and prevent safety hazards. By emphasizing regular workplace cleaning, organizations can ensure a safe and hygienic environment for employees, promoting a culture of professionalism and accountability. The key characteristic of shining is its focus on sustaining a clean and organized workspace, fostering employee well-being and productivity. Regular cleaning not only enhances workplace aesthetics but also contributes to operational efficiency by reducing the risk of accidents or delays.
Standardize
Standardizing practices involves implementing consistent procedures and visual standards to maintain organizational efficiency. By establishing standardized workflows and processes, companies can eliminate variability and enhance work consistency across departments. The key characteristic of standardizing is its emphasis on creating uniformity and precision in operational tasks, reducing errors and improving overall productivity. Through standardization, organizations can boost quality control measures and streamline operational processes effectively.
Sustain
Sustaining practices aim to reinforce the adoption of lean principles and ensure long-term adherence to efficient work practices. By instilling a culture of continuous improvement and regular self-auditing, companies can sustain the benefits of lean implementation over time. The unique feature of sustainability lies in its focus on maintaining lean practices through ongoing training, monitoring, and improvement initiatives. Sustaining lean principles is essential for embedding efficiency into the organizational culture and driving sustained success in the long run.
Kanban System
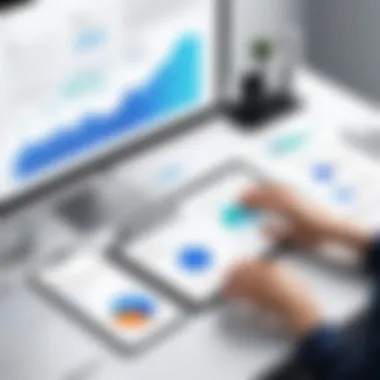
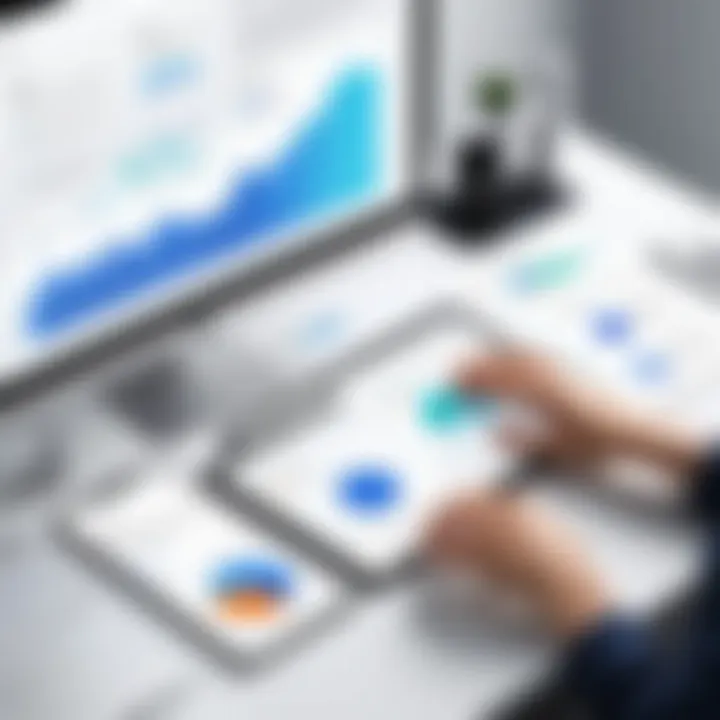
The Kanban System is a prominent tool for visualizing workflows and optimizing task management within organizations. By visualizing work processes through Kanban boards and cards, teams can monitor progress, identify bottlenecks, and facilitate a pull-based system for task completion. This system enhances agility, promotes transparency, and empowers teams to self-manage their workload effectively. Visualizing workflows through Kanban fosters efficiency, collaboration, and continuous improvement, aligning teams towards common goals and enhancing overall productivity.
Root Cause Analysis
Identifying Underlying Issues
Root Cause Analysis is essential for identifying the fundamental triggers of operational inefficiencies or quality deviations within processes. By conducting thorough investigations and root cause analysis exercises, organizations can pinpoint the underlying issues causing recurrent problems. The key characteristic of identifying underlying issues is its commitment to uncovering the root causes rather than addressing surface-level symptoms. By delving deep into the core issues, companies can implement targeted solutions and prevent issues from recurring, thus enhancing process reliability and organizational performance.
Implementing Sustainable Solutions
Implementing sustainable solutions entails addressing root causes effectively and implementing robust countermeasures to prevent reoccurrence. By developing sustainable solutions based on root cause analysis findings, organizations can drive long-lasting improvements in operational effectiveness and quality standards. The key characteristic of implementing sustainable solutions is its focus on developing preventive actions that address root causes directly, ensuring lasting solutions to persistent challenges. Through sustainable solutions, companies can fortify their processes, mitigate risks, and foster a culture of continuous improvement for enduring success.
Cultivating a Lean Work Culture
Leadership Engagement
Setting the Vision
The aspect of 'Setting the Vision' plays a pivotal role in establishing the direction and goals of an organization. By articulating a clear and compelling vision, leaders provide employees with a roadmap for success, guiding their efforts and inspiring commitment. A well-defined vision serves as a unifying force, aligning teams towards a common objective and instilling a sense of purpose. In the context of this article, 'Setting the Vision' underscores the importance of strategic leadership in driving organizational change and fostering a culture of continuous improvement.
Empowering Employees
Empowering employees involves delegating authority, recognizing contributions, and fostering a sense of ownership among team members. This approach motivates individuals to take initiative, solve problems creatively, and contribute meaningfully to the organization's objectives. In the context of this article, 'Empowering Employees' is highlighted as a key strategy for cultivating a lean work culture. By empowering employees, organizations can tap into the full potential of their workforce, driving innovation, and nurturing a culture of accountability.
Employee Involvement
Encouraging Continuous Learning
Encouraging continuous learning involves promoting a culture of skill development, knowledge sharing, and professional growth within the organization. By prioritizing ongoing education and self-improvement, companies can adapt to changing market dynamics, stay abreast of industry trends, and enhance workforce capabilities. In the context of this article, 'Encouraging Continuous Learning' is emphasized as a cornerstone of a lean work culture, fostering adaptability and resilience in the face of evolving challenges.
Fostering Collaboration
Fostering collaboration entails creating opportunities for teamwork, open communication, and cross-functional cooperation. By breaking down silos and promoting a collaborative environment, organizations can leverage diverse perspectives, drive innovation, and maximize productivity. In the context of this article, 'Fostering Collaboration' is highlighted as a fundamental element of cultivating a lean work culture, enabling synergies among team members, and promoting a shared sense of achievement.
Training and Development
Building Competency
Building competency involves investing in employee training, skill development, and performance enhancement initiatives. By equipping employees with the necessary knowledge and capabilities, organizations can improve operational efficiency, deliver high-quality productsservices, and maintain a competitive edge in the market. In the context of this article, 'Building Competency' is portrayed as a strategic priority for cultivating a lean work culture, nurturing a skilled workforce, and driving organizational excellence.
Promoting Innovation
Promoting innovation entails fostering a culture of creativity, experimentation, and risk-taking within the organization. By encouraging fresh ideas, embracing change, and supporting entrepreneurial endeavors, companies can stay ahead of the curve, drive market differentiation, and fuel growth. In the context of this article, 'Promoting Innovation' emerges as a critical aspect of cultivating a lean work culture, stimulating continuous improvement, and inspiring breakthrough solutions.