Understanding the Crucial Role of PCBs in Modern Electronics
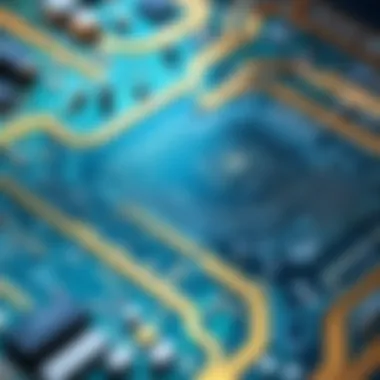
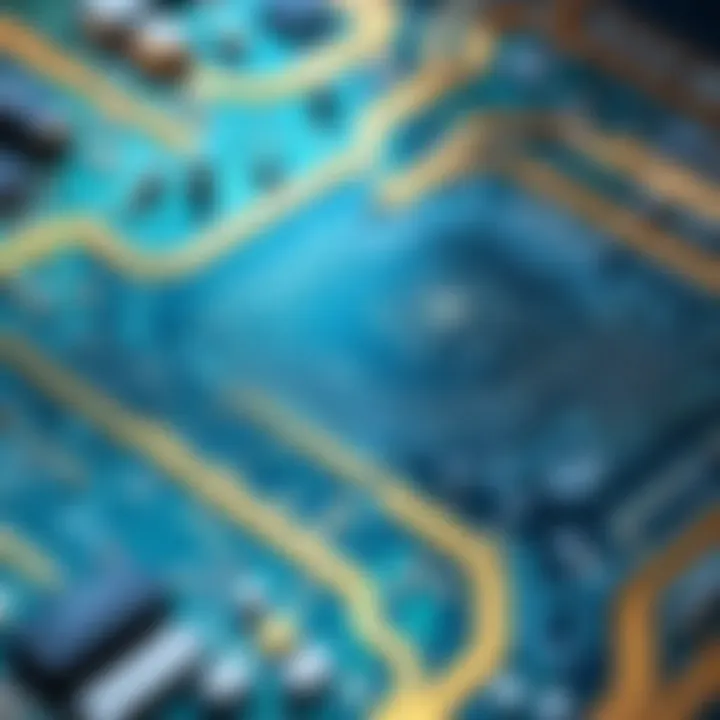
Intro
Printed circuit boards, commonly known as PCBs, are crucial elements in the electronic devices we use today. Their contribution to the functionality and efficiency of these devices cannot be understated. In this exploration, we will cover the structure and manufacturing of PCBs and their importance in various electronic applications.
A PCB serves as the backbone of an electronic circuit, providing both the physical platform for electronic components and the paths for electrical connections. This relationship between design and functionality forms the foundation for everything from consumer gadgets to sophisticated industrial systems. Understanding the mechanics behind PCBs is essential for anyone involved in electronics, as it influences the development and performance of devices dramatically.
Understanding PCB Fundamentals
What are PCBs?
PCBs are flat boards made from insulating materials that house various electrical components. They feature conductive pathways, usually made of copper, that enable the flow of electricity. The general assembly of a PCB involves a series of processes including layering, etching, and soldering.
Key Components of PCBs
A standard PCB incorporates a variety of elements:
- Conductive traces: Made of copper, these form pathways for electrical connections.
- Substrate: The base material, typically fibreglass or phenolic, supports the electronic components.
- Solder Mask: A protective layer that prevents accidental shorts and improves solderability.
- Silkscreen: Often used for labeling locations and components for assembly and troubleshooting.
The Significance of PCB Design
The complexity of PCB design scales with the requirements of the intended device. A well-designed PCB maximizes performance and minimizes interference. Techniques such as multi-layering and controlled impedance are standard practices in modern PCB designs to ensure they align with high-frequency applications.
PCB Manufacturing Processes
The manufacturing of PCBs involves numerous stages to achieve desired functionalities and specifications. Typically, these steps include:
- Design specifications: Using CAD software, engineers layout the desired track paths and placements for electronic components.
- Film footage preparation: Final printed designs are transformed into film negatives for the etching process.
- Etching: The copper layer on the board is etched away to reveal the actual conducting traces according to the design.
- Drilling: Holes are drilled for component leads.
- Solder Mask Application: This layer protects copper from oxidation and undesired connections.
- Component Assembly: Electronic leads are inserted, followed by soldering through various methods like wave or reflow soldering.
Each step of the manufacturing process substantially affects the final product's reliability and performance.
Current Trends in PCB Technology
The PCB industry observes rapid advancements propelled by changing consumer needs and increasing device complexity. Trends include:
- Flex and Rigid-Flex PCBs: Demands for compact and lightweight designs have introduced circuit boards that bend, optimizing space within devices.
- Higher Layer Counts: Devices are asserting more complex functionalities, leading to an increase in multi-layer boards.
- Sustainable Materials: There is a significant shift towards eco-friendly materials to align with global sustainability goals.
Future of PCB Design
Innovation remains key in PCB design and manufacturing. Next-generation PCBs are set to be integrated with technologies such as IoT and wearable devices, emphasizing miniaturization, durability, and efficiency.
Understanding Printed Circuit Boards
Understanding printed circuit boards (PCBs) is crucial to grasping how electronic devices operate. At the intersection of power and connectivity, PCBs are fundamental to almost all electronic applications. Their design and functionality impact device performance, reliability, and manufacturing costs. This section elucidates what PCBs are, highlighting their key purposes and types, which serve different needs in the electronics field.
Definition and Purpose
Printed circuit boards are used to support the mechanical and electrical components of electronic devices. The primary purpose of a PCB is to establish an electrical connection through conductive tracks connecting various components. This supports various functions—ranging from simple signal transmission to complex computational tasks. With the increasing trend towards miniaturization and efficiency in electronics, understanding the original intentions behind PCBs provides clarity on modern applications.
Types of PCBs
Diverse applications require specialized printed circuit boards to meet specific needs. Here, we explore three primary types of PCBs, underscoring their characteristics, benefits, and how they align with different functionalities.
Single-Sided PCBs
Single-sided PCBs feature all conductive elements on one side of the board, which makes them simple and cost-effective. Their primary use is in low-density applications such as simple machinery or wearing products. The key characteristic of single-sided PCBs is the easy fabrication process, making them a beneficial choice for rapid production and efficient manufacturing cycles.
However, a unique feature of single-sided PCBs is their weight limitation. Due to confined routing, they often restrict equipment miniaturization. As the technology evolves, their limitations become apparent, influencing contemporary electronic design advancements. Their simplicity works well for applications with minimal complexity but may fall short in higher-demand environments.
Double-Sided PCBs
Double-sided PCBs bring layers to the game, comprising components and routing on both sides. This type enhances the routing capacity compared to single-sided boards. As a popular option, double-sided PCBs find uses in various gadgets like personal computers and calculators. The elevated capability stems from its dual-surface design, accommodating more complex interlinking circuits.
Nevertheless, the defining trade-off is in the increased manufacturing costs and design complexity. Ensuring accuracy in component alignment presents added challenges and solutions in the creation process. Their potential to handle higher component counts and complexity validates a strong appeal towards their adoption in numerous electronic layouts.
Multilayer PCBs
Multilayer PCBs turn engineering sophistication to its maximum with three or more layers of circuit paths sandwiched together. This construction means increased design density and higher capacity for functionality. Consequently, multilayer PCBs are favorable for advanced applications, including telecommunications or high-performance computing systems. The vital characteristic of these boards is their capacity to fit extensive functionality within a compact area.
A unique feature of multilayer PCBs involves the enhanced performance, which often brings thermal management challenges. This complexity can translate into higher production costs but also promises significant power efficiency gains—a worthwhile benefit for high-stakes applications. Considering their capabilities reveals why multilayer PCBs dominate particular market sectors driven by intensive technical requirements.
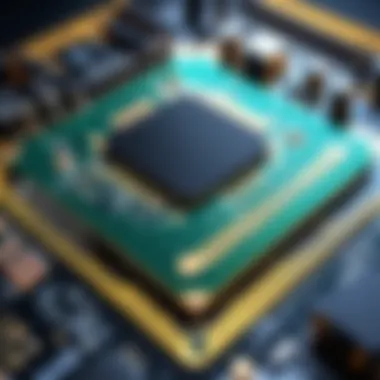
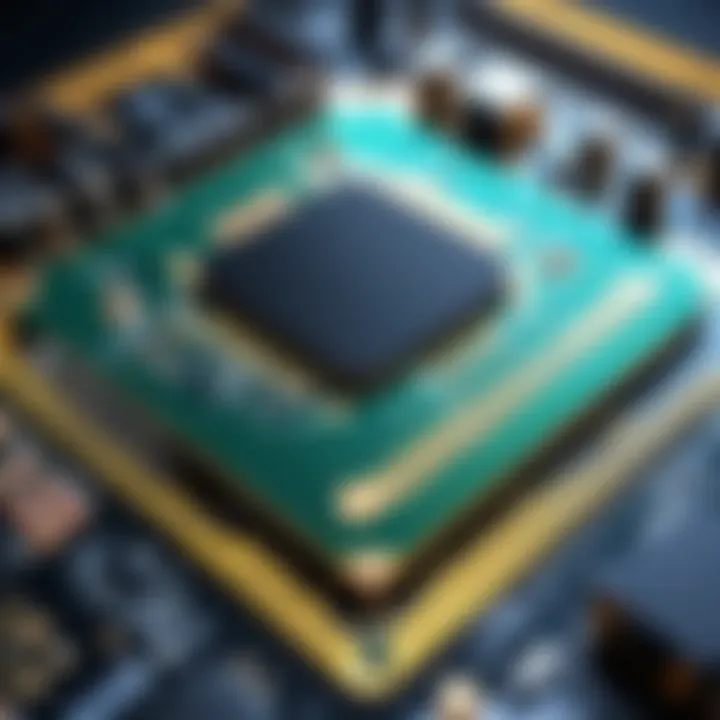
With the varying characteristics converged around these PCBs, we understand their impact within electronic sectors while highlighting different designs serve fundamentally unique aspects of efficiency and complexity in modern electronics.
PCB Design Principles
PCB design principles are critical in ensuring the functionality and reliability of electronic devices. A well-designed PCB can optimize the electrical pathways, minimize interference, and streamline the assembly process. This section will explore the core elements of PCB design, focusing on schematic design, layout and routing, and design for manufacturing. Understanding these principles empowers engineers to create effective, high-quality PCBs that meet the rigorous demands of modern electronics.
Schematic Design
Schematic design serves as the foundation of the PCB layout process. It provides a clear representation of the electrical circuits, showing how components are interconnected. This phase requires careful planning to ensure that all elements will function correctly once manufactured. Effective schematic design minimizes errors and facilitates a smoother transition to the layout phase.
By organizing the circuit efficiently, engineers can reduce the complexity of PCBs, allowing better integration of components. Adequate documentation during schematic creation is paramount, offering a reference point for future modifications or troubleshooting. Moreover, robust schematic practices can also simplify communication among team members.
Layout and Routing
Component Placement
Component placement is crucial in PCB layout. The arrangement directly influences the board's performance, signal integrity, and manufacturability. A strategic placement minimizes the distance between high-frequency components, reducing potential signal loss and crosstalk. Furthermore, grouping related components can simplify debugging and repair efforts.
Key considerations in component placement include:
- Proximity - Keep components that work together close to one another to facilitate better connections.
- Access - Ensure that parts requiring maintenance are easily reachable.
- Thermal Management - Arrange heat-sensitive components in a way that they can dissipate heat effectively.
Optimal component placement translates into improved performance and lower assembly costs, enhancing overall PCB efficiency.
Trace Management
Trace management focuses on designing the paths that connect circuits on the PCB. Attention to trace width, length, and routing ensures proper signal flow and minimizes resistance. Factors like electromagnetic interference and the overall impedance also demand consideration during the design phase.
Key aspects of trace management include:
- Width and Thickness - Selecting the right width can prevent overheating and ensure sufficient current carrying capacity.
- Clearance - Sufficient spacing between traces helps reduce crosstalk and maintain signal integrity.
- Routing Techniques - Methods such as via-in-pad or controlled impedance routing can greatly enhance signal fidelity.
Effective trace management is a cornerstone of PCB design — it ultimately determines the board's reliability and functionality.
Design for Manufacturing
Design for manufacturing (DFM) encompasses strategies to make production cost-effective and efficient. It involves optimizing the layout for manufacturing processes, aiding in easier assembly and high yield rates. When PCBs are designed with attention to manufacturability, the risk of defects can be significantly reduced.
Some fundamental principles of DFM include:
- Standardization of component footprints widens options for sourcing.
- Minimizing layers simplifies the assembly, resulting in lower costs.
- Detailed documentation helps fabricators understand requirements and reduce errors.
Adopting DFM practices positions manufacturers to better compete in the increasingly challenging electronics market. Ensuring that PCBs fit seamlessly into production lines can shorten time-to-market and align with evolving consumer demands.
Fabrication Processes of PCBs
The fabrication processes of printed circuit boards (PCBs) are critical to ensuring their reliability and functionality. These processes look at how the components are integrated and how to achieve strict specifications. Understanding this topic is essential, as it defines the quality of the PCBs and, by extension, the electronic devices they are used in.
Material Selection
Types of Substrates
Substrates are the foundational materials on which the circuitry of a PCB is built. They provide the base for electrical components. There are several types such as FR-4, Teflon, and Rogers materials. Among these, FR-4 is often the most popular choice. It is made from woven fiberglass cloth with an epoxy resin binder, offering significant electrical insulation.
The key characteristic of FR-4 is its excellent thermal stability and mechanical strength. This makes it suitable for various applications ranging from consumer electronics to industrial machinery. One of the unique features of FR-4 is its balanced performance across various frequencies. The advantages of using FR-4 include lower cost and good dielectric properties, while its main disadvantge is housing moisture vapor permeability, which can affect overall performance if not controlled.
Conductive Materials
Conductive materials, usually copper, are integral in PCBs as they create the pathways for current flow between components. Copper is widely used due to its excellent conductivity. Its major characteristic is low resistance, allowing for effective signal transmission.
This makes copper a preferred choice for PCBs, especially in high-performance applications. However, other materials like silver and gold can be used for specific parts to enhance conductivity. The unique feature of copper is its relative cost-effectiveness and high availability. The advantage of using copper lies in its better performance and durability, while one potential disadvantage is the development of a patina or corrosion over time which can affect performance and reliability.
Manufacturing Techniques
Etching
Etching is a vital process in PCB production. It removes unwanted copper to create the desired circuits on the substrate. This step relies on chemical reactions to eliminate sections of material, forming intricate patterns required for electronic function. The advantage of etching is its ability to create high precision circuit layouts, crucial for dense circuit boards where space is limited.
Nevertheless, etching presents the concern of chemical waste disposal, which must be managed effectively to maintain environmental standards.
Plating
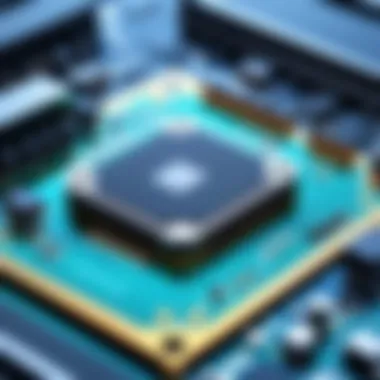
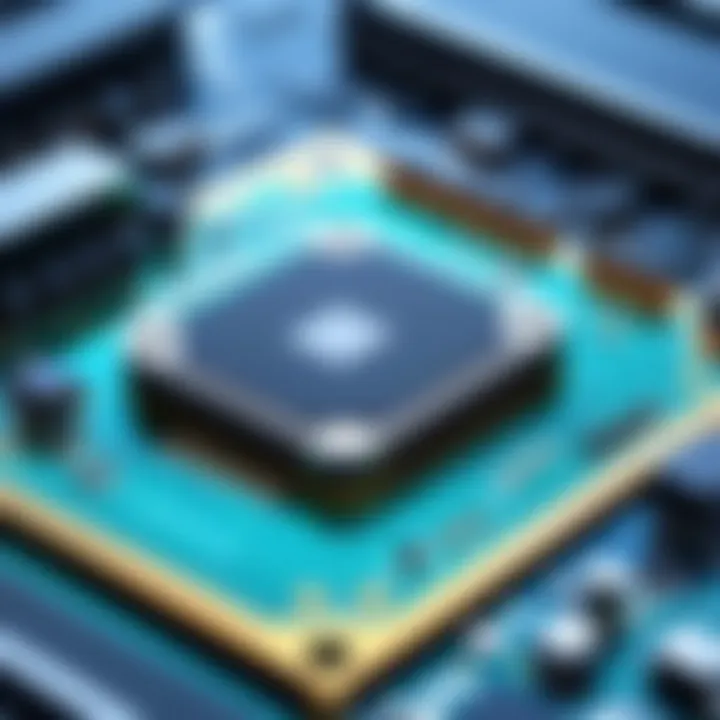
Plating involves depositing metal onto the PCB to enhance the conductivity and protect the copper traces from oxidation. This method adds a layer of metallic coating to establish a stronger connection for components. One critical benefit of plating increases the lifespan of the connections made on the PCB, by offering protection against wear and corrosion.
However, this technique sometimes requires additional processes that can increase production times and costs. It is invaluable in applications where durability is essential.
Drilling
Drilling is necessary for creating holes for through-hole components and vias. This process forms the interconnections between different layers of multilayer boards. The key characteristic is precision; lasers or mechanical drills can create exact holes that fit the design specifications.
Drilling technology continuously evolves, focusing on accuracy and speed, making it proficient and less labor-intensive over time. While drilling offers many benefits like time efficiency and the possibility of high-density via placement, sufficient care must be taken to prevent mechanical damage or incorrect drill sizing.
In summary, the fabrication processes of PCBs shape the quality, functionality, and applications of the final products in the electronics world. Understanding materials and manufacturing techniques is vital for quality assurance and performance consistency.
Testing and Quality Assurance
In the realm of electronics, especially concerning printed circuit boards (PCBs), rigorous Testing and Quality Assurance (QA) processes are indispensable. The role of these processes cannot be overstated as they directly impact the reliability and functionality of electronic devices. A robust system of testing ensures that imperfections are identified and mitigated before PCBs enter production lines or are implemented in final assemblies.
Testing and Quality Assurance focus mainly on validating both the design and the manufacturing of PCBs to surmount challenges like defect rates and workplace tolerances. The residual benefit of quality assurance goes beyond defect detection; it strives to eradicate the causes of defects and improve the overall productivity of PCB fabrication.
The implications of inadequate testing can be severe, potentially leading to failures in final electronic devices, which could undermine customer trust and incur substantial financial losses.
Effective testing is an investment in reliability that Electronics manufacturers cannot afford to ignore.
Moreover, the nature of electronic devices today demands high precision. With rapidly escalating component densities and customer expectations for miniaturization without sacrificing performance, the precise functioning of each PCB becomes critical. Failure to ensure that PCBs comply with these specifications can yield significant setbacks not just at the production stage but also during deployment.
Functional Testing
Functional testing serves as the cornerstone of PCB evaluation. It encompasses a variety of practices intended to verify that every designed feature of a PCB operates as intended. This includes testing for power operations, signal integrity, and heat generation, among other criteria.
Methods regularly incorporated in functional testing involve:
- In-Circuit Testing (ICT): Circuit functionality is tested while the PCB is in a circuit.
- Automated Optical Inspection (AOI): Visual assessments performed with machinery to identify defective components or problems in solder joints.
- Functional Board Testing: Examining the board’s performance through simulated load and real-world conditions to assess its behavior within a system.
Each functional test is pivotal for confirming system efficiency, reliability, and guaranteeing that it meets pre-specified standards. An efficient capture of discrepancies will not only enhance performance but also aid manufacturers in reducing costs over time.
Visual Inspection
Visual inspection remains a fundamental part of quality assurance for PCBs, often regarded as the first line of defense against quality issues. This method, although relatively straightforward, is vital for spotting visible defects which may not immediately impair functionality. Common inspections consider factors such as:
- Proper placement of components.
- Solder joint quality.
- Any physical damage or contamination.
The effectiveness of visual inspections can be further bolstered through proper training for personnel involved and the advent of modern technologies, including AI-enhanced visual capabilities.
While a powerful given method may improve defect detection significantly, oversight training should occur regularly to counteract inherent biases and guarantee an objective evaluation of a PCB throughout its production cycle. Integrating visual inspections with other testing strategies can yield a far greater level of assurance in PCB quality and performance.
Visually, clean, precise, and well-constructed circuit boards lead to not only better functionality but also improve longevity and user satisfaction in electronics. As such, both functional testing and visual inspection are foundational elements for PCs that play a vital role in the integrity of electronic devices today.
Applications of PCBs
The role of printed circuit boards (PCBs) in modern electronics is multifaceted. They are not just fundamental components; they are essential in determining the functionality and efficiency of various devices. Understanding where and how PCBs are used reveals their significant impact across multiple sectors. Their applications extend beyond basic connectivity to facilitating complex functionalities in consumer products and essential systems in industry and healthcare sectors.
Consumer Electronics
Consumer electronics represent the most prevalent use of PCBs. From smartphones to televisions, the need for compactness and reliability drives constant innovation in PCB design. In this sector, multi-layer PCBs are especially favored. They allow for dense component placement while providing necessary electrical paths. This densification responds to both consumer demand for slimmer devices and the industry push for multitasking capabilities.
Within consumer electronics, the soldering process plays an important role. Components need to be securely attached to withstand regular use, enhancing durability. Moreover, the trend of smart connectivity means these PCBs need to support communication technologies like Wi-Fi and Bluetooth. Thus, design for manufacturing principles become critical to ensuring that each component can be reliably produced at scale.
Industrial Control Systems
In the realm of industrial control systems, the significance of PCBs is even more pronounced. Industries rely on a variety of control systems to manage processes, where the control board is at the heart of operations. Industrial-grade PCBs need to endure harsh environments, often featuring conformal coatings that protect against moisture, thermal shock, and chemicals. This durability is key for continuous availability of machinery used in manufacturing and processing plants.
Additionally, safety standards are highly emphasized in this sector. Quality assurance processes must include rigorous testing, which ensures each PCB can consistently perform its designated tasks under variable conditions. The advancement of IoT in industrial settings has introduced further complexities that these boards must handle, and therefore high-frequency PCBs are gaining more traction in applications demanding precision and fast response times.
Medical Devices
The use of PCBs in medical devices showcases their role in life-critical applications. Devices such as heart monitors, imaging systems, and infusion pumps integrate PCBs designed with exceptional reliability and adherence to stringent regulations. In healthcare technology, the stakes are incredibly high, making diligence a requirement in PCB design and manufacturing.
Here, lightweight and compact PCBs enable portability without sacrificing functionality. Biocompatible materials are also increasingly important, ensuring devices are safe for contact with the human body. Embedded systems in medical devices often need to parse and transmit data in real-time, putting a premium on high-frequency and smart PCB design. Continuous advancements help healthcare professionals access vital information swiftly, enhancing the overall quality of patient care.
Emerging Trends in PCB Technology
The field of printed circuit boards (PCBs) is undergoing significant transformation. As electronics grow increasingly complex, the designs and components of PCBs must evolve as well. Understanding these emerging trends is paramount for those involved in electronics, from manufacturers to designers and IT professionals.
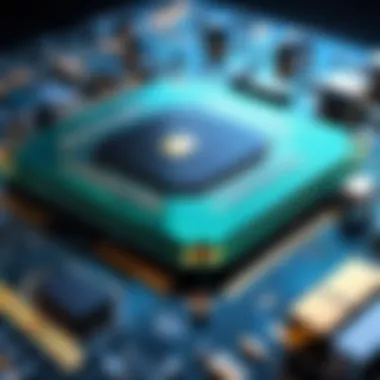
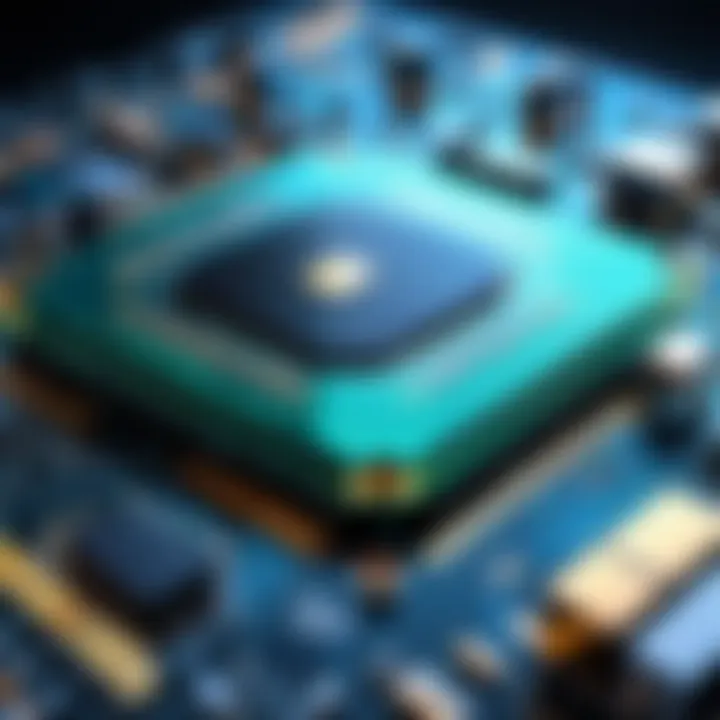
Flexible and Rigid-Flex PCBs
Flexible PCBs can bend, twist, and flex, enabling designers to create more compact and lightweight devices. They often implement in modern smartphones and wearable technology. Rigid-flex PCBs combine elements of both rigid and flexible PCBs, giving benefits like space-saving designs and the potential for reduced assembly costs. Such designs enhance reliability. This approach underlines the need for effective space utilization in designing new products.
Benefits of Flexible and Rigid-Flex PCBs
- Lightweight and Thin Designs: The lighter weight enhances portability, a crucial factor in user preferences today.
- Space Saving: Compact designs allow for smaller devices that still pack powerful capabilities.
- Improved Durability: These PCBs often withstand harsher conditions, which is essential for many applications.
High-Frequency PCBs
High-frequency PCBs are essential for advanced communication systems and RF applications. Many areas rely on this technology, including 5G networks and satellite communication. High-frequency outright improves performance by minimizing signal loss and interference. It is necessary for circuits that handle rapid data processing. As applications requiring higher frequencies increase, the relevance of these specialized PCBs rises accordingly.
Considerations for High-Frequency PCBs
- Impacts on Signal Integrity: Designers must address unique challenges related to maintaining signal quality at high frequencies.
- Material Choices: Selecting appropriate materials becomes critical. Low-loss substrates reduce signal loss effectively.
Smart PCBs
Smart PCBs integrate technology such as sensors and connectivity protocols directly into the PCB design. This incorporation supports functionalities in the Internet of Things (IoT) projects. Notably, smart PCBs can improve the interactivity of products. They can collect data and facilitate device communication. As demand for smart devices increases, adapting and integrating this concept will be indispensable.
Benefits of Smart PCBs
- Data Collection: Embedded sensors gather real-time data, enhancing the functionality of the device.
- Connectivity: Smart PCBs enable different devices to communicate easily, fostering interconnected systems.
- Enhanced Efficiency: They optimize power consumption and monitoring, contributing to overall system efficiency.
Challenges in PCB Production
Printed circuit board (PCB) manufacturing is a complex process that presents several challenges. These obstacles can impact production quality, efficiency, and cost, making it vital for manufacturers to navigate them effectively. Addressing these challenges not only ensures high reliability but also enhances the overall performance of electronic devices. This section elucidates the main hurdles faced in PCB production, particularly in the areas of component density, thermal management, and cost efficiency.
Component Density
As electronics continue to evolve, the demand for higher-performance devices has surged. One notable challenge is the increasing component density on PCBs. High component density allows manufacturers to make more compact electronics but comes with inherent difficulties. Space-efficient design raises the complexity of circuitry, limiting the available area for traces and pads. Visibility shrinks, complicating assembly and increasing the risk of errors in placement. Additionally, more components may lead to heightened signal integrity issues which require diligent consideration of routing design.
Advanced software can assist in layout optimization, permitting designers to manage space while fulfilling functional requirements effectively. Understanding how to balance component selection and PCB layout is critical for meeting modern specifications without compromising performance.
Thermal Management
Another significant challenge emerging in PCB production is thermal management. As devices become more powerful, they generate additional heat, necessitating improved methods for heat dissipation. Critical components such as microprocessors and voltage regulators produce substantial heat during operation, risking damage to solder joints and sensitive components.
To mitigate these risks, designers must incorporate effective thermal management strategies early in the design phase. This may include the use of thermal vias, copper pour areas, and heat sinks. Elements such as ventilation and heat dissipation pathways must be architected considering the final product's physical arrangement. Diligent thermal analysis is paramount to preserve the PCB's reliability and extend its operational lifespan.
Cost Efficiency
Achieving cost efficiency in PCB production can be a daunting task. Various factors affect the economics of manufacturing, including material selection, tooling, labor costs and production volume. Higher quality materials might be initially more expensive, yet compromised materials may lead to a surge in prototypes, repair work, and other unplanned expenses in the long term. Efficiency in components sourced likewise must be cohesive to prevent bottlenecks within production cycles.
Optimizing yield rates during production is a tactical pillar for boosting cost efficiency. Automated quality checks, precise assembly processes, and batch-level production adjustments can contribute significantly to improved operational fluidity. Even minor advancements in organizational adaptability can yield substantial financial savings over time.
Ensuring a healthy balance among component density, thermal management, and cost efficiency is integral to the quality of PCBs in electronic applications.
In summary, addressing the challenges in PCB production is vital to achieving effective outcomes and satisfying manufacturer and consumer needs. Focused strategies related to dense component layouts, sophisticated thermal handling, and judicious resource management play crucial roles in shaping the future of PCB manufacturing.
The Future of PCBs
The future of printed circuit boards (PCBs) is shaped primarily by advancements in materials and integration with modern technologies such as the Internet of Things (IoT). These two aspects not only dictate how PCBs can enhance performance but also determine their adaptability to evolving electronic demands. Considering factors like small form factors, lower weight, and energy efficiency becomes crucial in their development.
Innovations in Materials
Innovations in materials are driving the future of PCBs significantly. The traditional glass-reinforced epoxy laminates that are prevalent today challenge current design limitations. Emerging materials like Polyimide film are lighter and capable of enduring higher temperatures. These materials support the development of smaller, more efficient components with appropriate mechanical and thermal properties. These are essential for future-grade applications.
The focal point of material innovation revolves around:
- Flexible Substrates: Allow PCBs to bend and conform to specific shapes, suited for wearables and mobile devices.
- High-Frequency Materials: Needed for applications in telecommunication and RF systems, improving signal integrity and resistance to heat.
- Biodegradable Materials: Stimulating sustainability in PCB production can minimize environmental impact. It's a response to increasing awareness regarding waste management.
By emphasizing these new materials, manufacturers hope to produce a PCB that can not only endure challenging operational conditions but also fit seamlessly within increasingly compact devices.
Integration with IoT
Integration with IoT is a game changer for PCBs, as it brings smartness into electronic devices. With PCBs being the backbone, their combination with IoT features enables devices to capture, process, and exchange data ranging from simple sensors to advanced communication modules.
The importance of IoT integration lies in:
- Enhanced Connectivity: Facilitates real-time data sharing and monitoring, unlocking the potential of smart homes and industrial Internet.
- Improved Functionality: PCBs equipped with IoT sensors enable smart functionality, such as automated home systems that can adapt based on user behavior.
- Data Processing Efficiency: IoT processes must cater to large volumes of data with limited resources—this requires robust PCB designs that can manage power consumption effectively.
Furthermore, as connectivity trends evolve, developers face pressures toward delivering designs that account for rapid changes in technology. Integration with IoT represents both an advantage and a challenge in terms of specifying versatile solutions that can adapt over time. As devices get smarter, the fundamental role of a PCB in supporting these advancements cannot be underestimated.
Innovations in PCB materials and their integration into IoT create endless possibilities for the future of electronics.
The ongoing juxtaposition of integrating innovative materials and embracing IoT forms the backbone of future PCB developments. Individually, these threads showcase vast potential; combined, they may fundamentally shift electronics toward previously unattainable frontiers.