Crafting a Winning Inventory Control Strategy
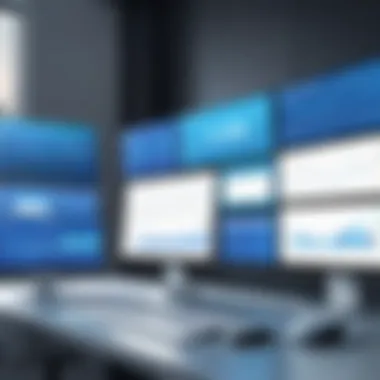
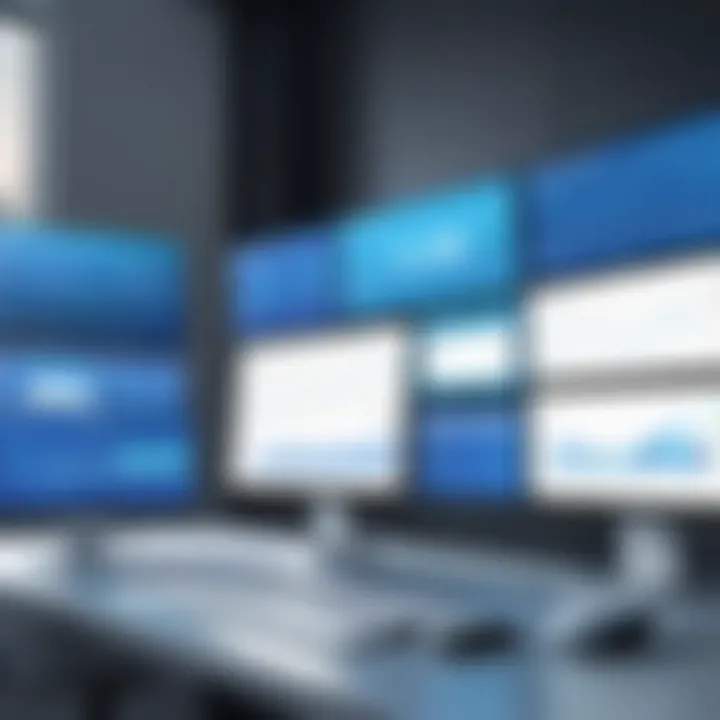
Intro
In today's fast-paced business environment, the importance of an effective inventory control plan cannot be overstated. Organizations that prioritize a structured approach to inventory management position themselves for success. Such plans streamline operations, improve customer satisfaction, and reduce operational costs. The intricate relationships between demand forecasting, inventory valuation, and technology integration play a crucial role. Understanding these connections is essential for any business aiming to maintain a competitive edge.
By utilizing the insights provided in this piece, professionals will be better equipped to enhance operational efficiency. This focus on optimization is critical for navigating the complexities of modern supply chains.
Understanding Storage, Security, or Networking Concepts
Prologue to the Basics of Storage, Security, or Networking
Organizations often overlook the foundational concepts of storage and security. For a successful inventory control plan, appreciating these basics is vital. Storage refers to how inventory is held, either physically or digitally. Security encompasses protecting data and materials from threats. Networking involves creating systems that allow for effective communication and resource management between different parts of the organization.
Key Terminology and Definitions in the Field
Familiarity with key terms benefits every aspect of inventory control. Some essential terminology includes:
- SKU (Stock Keeping Unit): A unique identifier for each distinct product.
- Lead Time: The time taken for inventory to be replenished after an order is placed.
- ABC Analysis: A method for categorizing inventory based on significance and value.
These terms lay the groundwork for deeper discussions about inventory practices.
Overview of Important Concepts and Technologies
Understanding modern technologies is crucial. Technologies such as RFID (Radio Frequency Identification) streamline tracking inventory. Warehouse Management Systems (WMS) allow for better organization and reporting. Cloud solutions facilitate real-time data access across locations. Leveraging these technologies enhances both efficiency and accuracy.
Best Practices and Tips for Storage, Security, or Networking
Tips for Optimizing Storage Solutions
To effectively manage inventory, one must focus on optimizing storage solutions. Here are several strategies:
- Conduct regular audits to assess inventory levels.
- Implement a just-in-time inventory model to reduce excess stock.
- Use technology to analyze turnover rates.
Security Best Practices and Measures
Safeguarding inventory also requires practical measures. Consider the following best practices:
- Employ access controls to limit inventory access to authorized personnel.
- Utilize surveillance cameras in storage areas.
- Regularly back up data to avoid losses from breaches.
Networking Strategies for Improved Performance
Effective networking can significantly boost inventory management. Some strategies include:
- Use cloud computing for scalable resource management.
- Establish robust communication channels across departments.
- Regularly update systems to enhance performance and security.
Industry Trends and Updates
Latest Trends in Storage Technologies
Storage technology is rapidly evolving. Trends such as automation in warehouses and heightened use of IoT devices are becoming standard. These advancements create smarter inventory management systems that respond faster to changing demand.
Cybersecurity Threats and Solutions
With technology integration comes new challenges. Cybersecurity threats, including ransomware, require proactive measures. Implementing comprehensive security frameworks and training staff on awareness can mitigate risks significantly.
Networking Innovations and Developments
Networking continues to evolve dramatically. The rise of 5G technology presents an opportunity for faster, more efficient data transfer, which is essential for inventory systems that rely on real-time data.
Case Studies and Success Stories
Real-life Examples of Successful Storage Implementations
Businesses that adopt best practices in storage often see considerable improvements. For instance, a retail chain that invested in a state-of-the-art WMS reported a 30% reduction in stock discrepancies.
Cybersecurity Incidents and Lessons Learned
Understanding past incidents can help prevent future problems. For example, a breach faced by a logistics company revealed vulnerabilities in their data handling processes. The aftermath prompted a complete overhaul of their data security measures.
Networking Case Studies Showcasing Effect Strategies
A case study involving a major distributor highlighted the effectiveness of real-time tracking systems integrated with their inventory control. The results demonstrated improved accuracy and efficiency, leading to greater customer satisfaction.
Reviews and Comparison of Tools and Products
In-depth Reviews of Storage Software and Hardware
When setting up an inventory control system, it is crucial to evaluate various software options. Systems such as Oracle NetSuite and Fishbowl provide comprehensive solutions tailored for different business sizes.
Comparison of Cybersecurity Tools and Solutions
Comparing cybersecurity tools can reveal which solutions best fit an organization's needs. Products like Norton and McAfee offer various features for different levels of protection.
Evaluation of Networking Equipment and Services
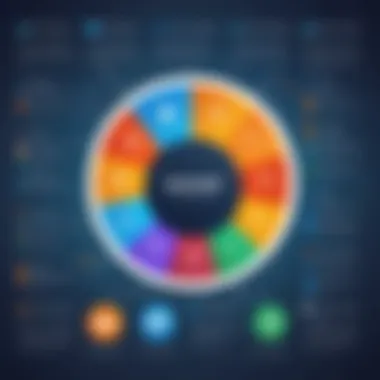
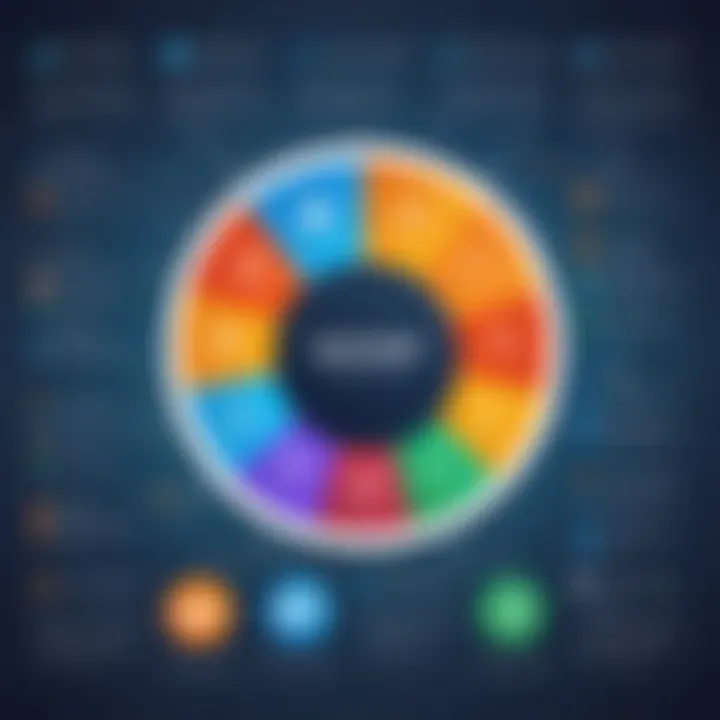
Choosing the right networking equipment is vital as well. Evaluating brands such as Cisco and Ubiquiti based on performance and cost can enhance system effectiveness.
By considering these various aspects, businesses can develop a more effective inventory control plan that not only meets their current needs but also allows for future growth.
Understanding Inventory Control
Understanding inventory control is fundamental for any business looking to fine-tune its supply chain and improve overall operational efficiency. Having a robust inventory control system not only helps in tracking the products and materials but also plays a vital role in managing costs and ensuring that the right amount of stock is available at the right time. This topic covers essential knowledge for professionals in various fields, be it logistics, supply chain management, or finance.
Definition and Importance
Inventory control refers to the processes and strategies employed by businesses to manage their stock. This encompasses the management of raw materials, work-in-progress, and finished goods. It is critical for several reasons. Firstly, effective inventory control minimizes carrying costs. By reducing excess stock, businesses can free up capital and improve cash flow. Secondly, it enables companies to meet customer demands more reliably. When inventory is managed properly, companies can reduce stock-outs and ensure a consistent supply of products, thereby increasing customer satisfaction.
Moreover, accurate inventory control aids in decision-making. With reliable data on stock levels, businesses can forecast needs better, prepare for demand spikes, and avoid unnecessary order delays. In essence, understanding these processes culminates in optimizing operational efficiency, which is crucial for competitiveness in today’s market.
Role of Inventory in Supply Chain
The role of inventory in the supply chain cannot be understated. It serves as a buffer between production and consumption, ensuring smooth operations. Efficient inventory management supports various functions within the supply chain, ranging from procurement and manufacturing to distribution and sales.
Here are some significant functions of inventory in the supply chain:
- Buffer Stock: It helps to manage uncertainties in supply and demand, acting as a cushion during unexpected spikes in customer orders.
- Cycle Stock: This is the inventory that businesses sell to customers based on expected orders. Proper management ensures that this stock rotates adequately, reducing obsolescence.
- Safety Stock: This is an additional quantity of inventory kept on hand to minimize the risk of stock-outs.
Effective inventory control enhances coordination across the supply chain. When businesses can track inventory levels accurately, they can collaborate more efficiently with suppliers and logistic partners. This leads to improved lead times and reduced operational risks. A thorough understanding of these roles enables businesses to align their inventory management strategies with broader supply chain goals.
Components of Inventory Control
Understanding the components of inventory control is crucial for any organization aiming to maintain efficiency and competitiveness. These components not only simplify the management of stock but also help in reducing costs and increasing customer satisfaction. An effective inventory control system consists of various elements that work in harmony to ensure optimal inventory levels. Consideration for each component is necessary for developing a comprehensive inventory plan.
Types of Inventory
Various types of inventory exist, which form the basis of inventory management processes in different sectors. Here, we will explore the three main types: raw materials, work-in-progress, and finished goods.
Raw Materials
Raw materials refer to the basic materials used to produce goods. It is essential to have sufficient raw materials to ensure continuous production. Companies that manage raw material inventory effectively can minimize delays in manufacturing. A key characteristic of raw materials is that they can be sourced from multiple suppliers, providing flexibility in purchasing. However, holding excessive raw materials can lead to increased carrying costs and potential obsolescence.
Work-in-progress
Work-in-progress (WIP) involves items that are in the production process but not yet completed. This type of inventory is significant because it indicates the flow of production. Companies benefit from managing WIP effectively, as it helps in maintaining steady production schedules. A unique feature of WIP is that it can tie up both time and financial resources. Balancing WIP inventory is crucial to avoid overproduction and resource wastage.
Finished Goods
Finished goods are products that have completed the manufacturing process and are ready for sale. This inventory type is pivotal in meeting customer demand and fulfilling orders promptly. The key characteristic of finished goods is their immediate availability for distribution. However, having too many finished goods may lead to higher carrying costs and possible markdowns if products become obsolete. Effective management of finished goods is essential for maintaining a lean operation and meeting market demands.
Inventory Management Techniques
Implementing the correct inventory management techniques is vital for optimizing stock levels and increasing efficiency. Some widely recognized techniques include Just-in-Time, ABC Analysis, and Economic Order Quantity.
Just-in-Time
Just-in-Time (JIT) is a strategy aimed at reducing waste by receiving goods only as they are needed in the production process. This method helps minimize inventory costs and encourages a streamlined production process. JIT is beneficial as it enhances efficiency and reduces holding costs. However, it can be risky since relying too heavily on timely deliveries may lead to production delays if suppliers fail to deliver.
ABC Analysis
ABC Analysis categorizes inventory into three classes based on their importance. Class A items require the most attention, as they account for a high percentage of the inventory value. Class B items are of moderate importance, while Class C items are the least significant in terms of value. This technique is popular because it enables companies to prioritize resources effectively. However, it may overlook the importance of C items if not managed properly.
Economic Order Quantity
Economic Order Quantity (EOQ) is a method used to determine the optimal order quantity that minimizes total inventory costs, including ordering and holding expenses. This technique helps companies find the sweet spot between ordering too often and not ordering enough. EOQ is beneficial for maintaining cash flow and balancing order quantities. One disadvantage is that it relies heavily on accurate demand forecasting, which can be challenging in volatile markets.
The choice of inventory types and management techniques has a direct impact on an organization’s operational efficiency and cost management.
In summary, understanding the components of inventory control and effectively implementing strategies allows businesses to navigate the complexities of supply chain management successfully. As we continue through this article, we will explore how to establish objectives and employ demand forecasting methods to further enhance inventory control.
Establishing Inventory Control Objectives
Setting inventory control objectives is an essential step in crafting a coherent inventory management strategy. This process aligns the operational goals of the inventory system with the broader vision of the business. Clearly defined objectives guide decision-making and help ensure that resources are utilized efficiently. These goals inform every aspect of the inventory management process, from procurement to product delivery. By establishing a focused direction, companies enhance their agility in responding to market demands.
Defining Goals and KPIs
To create effective inventory control objectives, businesses must define clear goals and associated key performance indicators (KPIs). Goals typically focus on reducing costs, improving service levels, and minimizing excess inventory. KPIs are metrics that measure progress toward those goals. Commonly used KPIs in inventory management include:
- Inventory Turnover Ratio: This ratio indicates how often inventory is sold and replaced over a period. A higher turnover rate suggests effective stock management.
- Stock-out Rates: This metric tracks the frequency of running out of stock. Lower stock-out rates mean better customer satisfaction.
- Carrying Costs: This reflects the total cost of holding inventory, including storage, insurance, and depreciation.
Establishing these quantitative measures enables businesses to make informed decisions. Regularly evaluating KPIs helps in adjusting strategies to meet evolving needs.
Aligning with Business Strategy
Inventory control objectives must align closely with the overarching business strategy. This alignment ensures that inventory management supports broader company goals, such as market expansion or product innovation. To achieve this, a thorough understanding of the business model is vital. Here are some considerations:
- Customer Demand: Inventory levels should correspond to predicted customer demand. Fluctuations can arise from market trends, competition, or economic changes.
- Operational Capacity: Understanding production capabilities also helps in setting realistic inventory goals. A mismatch can lead to either excessive inventory or stock shortages.
- Cost Management: Aligning inventory goals with budgetary constraints ensures optimal resource allocation, reducing waste and maximizing profit margins.
Incorporating these factors into the objective-setting process creates a dynamic framework that adapts to changes in business conditions. This adaptability is essential for long-term success in a competitive market.
"The goals set for inventory control should resonate with the values and aspirations of the entire organization, fostering a culture of efficiency and responsiveness."
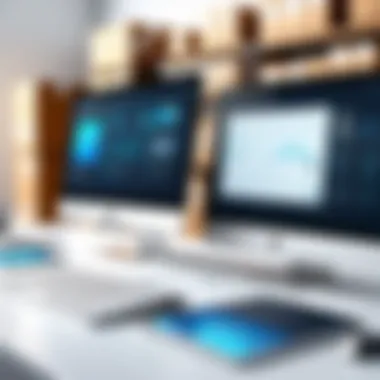
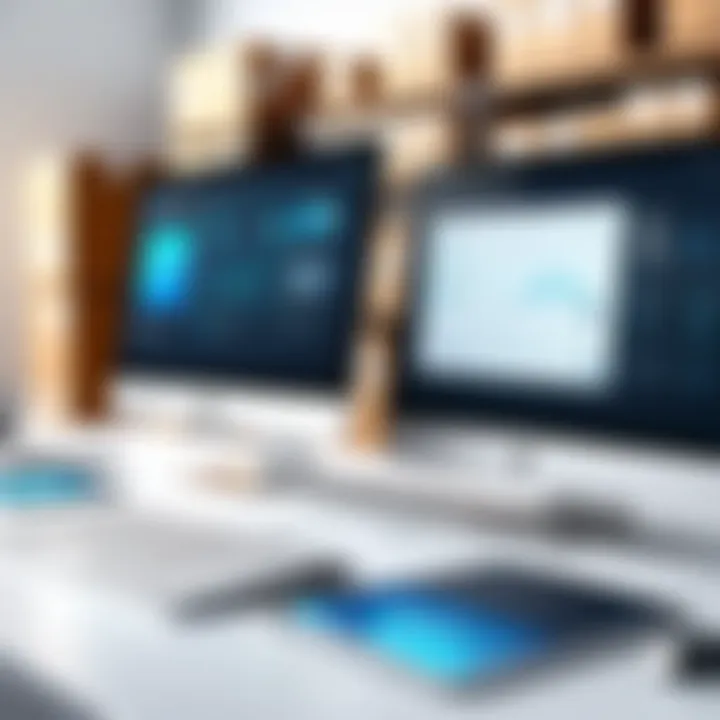
Regular reviews of inventory objectives against actual performance provide an opportunity for continuous improvement. As market conditions change, so too should the objectives, ensuring that the inventory strategy remains relevant and effective.
Demand Forecasting Methods
Qualitative Techniques
Qualitative techniques focus on subjective judgment and are especially useful when historical data is limited or when the product is relatively new. These methods rely on insights gathered from team experiences, customer feedback, and expert opinions. Here are some examples of qualitative techniques:
- Market Research: Involves surveys and interviews to gather data on customer preferences and buying behaviors.
- Expert Judgment: Consultation with industry experts to draw insights based on their experience and trends.
- Focus Groups: Engaging a group of selected individuals to discuss and predict future buying patterns based on current market conditions.
While these techniques can be effective in providing valuable context, they can be less reliable in terms of precision. Bias affects the outcome, and thus, companies should combine qualitative insights with quantitative methods for better accuracy.
Quantitative Techniques
Quantitative techniques utilize statistical and mathematical models to forecast demand. These methods often rely heavily on historical sales data and market analysis. They provide a more objective forecast compared to qualitative approaches. Here are some common quantitative techniques:
- Time Series Analysis: This method identifies patterns in historical data and uses these patterns to predict future demand.
- Causal Models: These models consider various factors that could influence demand, such as economic indicators and seasonal changes.
- Regression Analysis: A statistical method to evaluate the relationship between independent variables and demand to predict future values.
Quantitative methods can offer higher reliability and accuracy, especially when historical data is robust. However, they may not account for unexpected market shifts or changes in consumer behavior.
"Combining qualitative and quantitative methods provides a comprehensive view that can enhance demand forecasting accuracy."
Technology in Inventory Management
The role of technology in inventory management cannot be overstated. In a complex and dynamic business environment, efficient management of inventory becomes crucial. Technology provides businesses the tools necessary to streamline processes, reduce costs, and improve accuracy. A strategic deployment of technological solutions can enhance visibility and efficiency across the entire supply chain.
Inventory Management Software
Inventory management software stands as a pillar in modern inventory control systems. This software enables businesses to track their stock levels, orders, sales, and deliveries. With this tool, companies can minimize instances of stock-outs and overstock situations, both of which can have costly implications.
The main benefits of inventory management software include:
- Real-time tracking: Users can monitor stock levels instantly, allowing for timely procurement decisions.
- Data analytics: Advanced software provides insights through analytics, helping to forecast demand accurately based on historical data.
- Integration capabilities: Many inventory management solutions can integrate with other systems like accounting and customer relationship management (CRM) software.
- User-friendly interfaces: Modern systems offer intuitive layouts that simplify stock management tasks.
Implementing appropriate software requires careful consideration of some aspects. Businesses must evaluate their specific needs. They should consider factors like ease of use, integration capability, and scalability. \n
Automation and Robotics
Automation and robotics have emerged as driving forces in inventory management. By employing automated solutions, businesses can enhance their operational efficiency significantly. Automation minimizes human errors and streamlines repetitive tasks.
Some technologies now include:
- Automated storage and retrieval systems (AS/RS): These systems help businesses store and retrieve goods automatically, enhancing picking speed and accuracy.
- Robotic process automation (RPA): RPA can be utilized to automate mundane tasks such as data entry and report generation, freeing up staff to focus on more critical tasks.
- Drone inventory management: Drones can significantly reduce the time needed for inventory audits in large warehouses.
Despite these advantages, certain factors must be evaluated when considering automation. Implementing robotics can require substantial upfront investment, which may not always yield immediate returns. Moreover, changes in workforce dynamics and necessary training must be addressed to ensure a successful transition.
Technology is not just an option; it is a necessity in today's inventory management landscape.
Overall, the integration of technology into inventory management is essential for businesses that aim to maintain a competitive edge. With effective software and cutting-edge automation, companies can navigate the complexities of inventory control with greater agility and precision.
Inventory Valuation Methods
Inventory valuation methods are paramount for businesses as they influence financial reporting, taxes, and overall product costing. An effective inventory valuation approach not only ensures accurate asset representation on balance sheets but also aids in assessing profit margins. Understanding which method to employ can also impact working capital, liquidity ratios, and decision-making processes within the organization.
Different methodologies yield varying outcomes in terms of cost of goods sold and ending inventory valuation. Therefore, the selection of an appropriate valuation strategy is crucial in aligning with business objectives and financial goals. Additionally, it can have significant implications for cash flow management and financial strategy, particularly in industries with fluctuating market demands.
In this section, we will explore three prominent inventory valuation methods—FIFO, LIFO, and Weighted Average Cost. Each method presents distinct characteristics and benefits, making them suitable for varied business scenarios.
FIFO and LIFO
FIFO stands for "First In, First Out." This method assumes that the oldest inventory items are sold first. In times of inflation, this results in lower cost of goods sold, thereby increasing profits and tax liabilities. It can also better align with the flow of goods in many retail environments where older goods are more likely sold first.
LIFO, on the other hand, means "Last In, First Out." Under this method, the most recently acquired inventory is considered sold first. This can be advantageous during inflationary periods because it usually leads to higher costs of goods sold and lower taxable income. It's essential to consider the nature of your inventory and market conditions when choosing between FIFO and LIFO, as each has its advantages and disadvantages, particularly in terms of tax implications and cash flow.
"The choice between FIFO and LIFO comes down to understanding market dynamics, tax strategy, and cash flow requirements."
Weighted Average Cost
Weighted Average Cost (WAC) takes a different approach by averaging out the costs of all inventory items available during a specific period. This method calculates a uniform cost per unit, which can smooth out price fluctuations. It works well for companies that have inventory that is not easily identifiable, such as bulk commodities. The WAC can simplify bookkeeping, making it a preferred choice for many businesses, particularly those managing large volumes of similar items.
Implementing the Inventory Control Plan
Implementing the inventory control plan is a critical step in streamlining operations and maximizing efficiency in business logistics. The importance of this phase lies not only in the operational aspect but also in setting the foundation for long-term success. A well-executed plan leads to reduced costs, improved service levels, and enhanced visibility into inventory status. Understanding how to implement this approach effectively ensures that your organization can adapt to changes and forecast needs accurately.
A variety of elements must be considered during the implementation phase. First, businesses need to assess their existing inventory systems. This means evaluating current processes, identifying gaps, and determining how new inventory strategies can fill those gaps. It's about understanding your unique operational challenges and creating a tailored plan that addresses them directly.
Second, beneficial elements of an inventory control plan often include segmentation of inventory types and understanding how each segment requires different management strategies. By segmenting, businesses can prioritize resources effectively and facilitate targeted monitoring.
Finally, it’s crucial to communicate the purpose and advantages of the inventory control plan to all levels of staff. Making sure that everyone involved understands their roles will enhance buy-in and support for the plan.
Preparing for Implementation
Preparation is essential before rolling out any inventory control plan. One key strategy is to clearly outline the objectives and key performance indicators (KPIs) relevant to your organization. Defining objectives helps ensure that all stakeholders understand expected outcomes and can work toward achieving them. Additionally, it is best practice to create a timeline for implementation, breaking down tasks into manageable phases.
Inventory audits should also be conducted prior to implementation. This process involves reviewing current inventory levels and their conditions. By gaining a thorough understanding of existing inventories, you can identify inconsistencies, losses, or outdated items that need addressing before the new system is put in place.
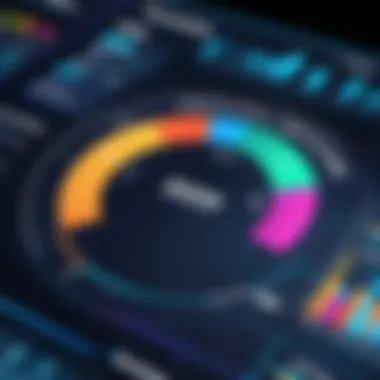
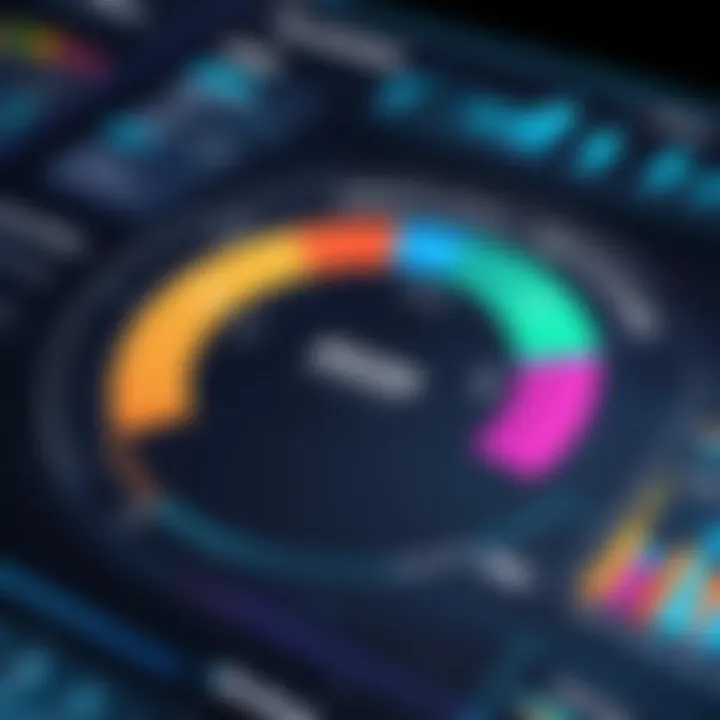
- Conduct Inventory Audits: Assess current inventories for accuracy.
- Define Objectives and KPIs: Clearly state what success will look like.
- Establish a Timeline: Break down the implementation into phases.
Ultimately, a well-prepared implementation process can simplify transitions and ensure that the new inventory control plan is adopted seamlessly.
Training Staff
Staff training is a crucial aspect of effective inventory control plan implementation. Successful adoption of any system relies heavily on the users' understanding and competence. Training should be comprehensive and tailored to various roles within the organization. Employees need to know not just how to use new tools or software, but also why these changes benefit the larger objectives of the company.
Training sessions can take on various forms such as workshops, hands-on demonstrations, or online tutorials. It is recommended to combine different learning modes to cater to diverse learning preferences among staff.
- Hands-on Workshops: Allow employees to engage directly with the systems.
- Online Tutorials: Provide flexibility for self-paced learning.
- Regular Updates: Offer refresher courses to keep skills sharp.
Highlighting the relevance of the inventory control system during training increases engagement. Staff should grasp how accurate inventory management can impact their roles directly, such as how it influences order fulfillment rates or stock levels.
"Effective training enhances staff capabilities and ensures that new systems are utilized to their full potential."
Monitoring and Adjusting the Plan
Monitoring and adjusting the inventory control plan is a pivotal step in ensuring its effectiveness. Once the initial strategies are set, ongoing evaluation becomes necessary to adapt to ever-changing market conditions and internal operations. An organization must not only track its inventory levels but also evaluate the performance of its strategies. This allows for informed decisions that can help optimize operations and improve overall business performance.
Regular assessments can lead to lessons learned, identifying successful techniques and areas requiring enhancement. Ultimately, this process strengthens the business's responsiveness and agility in supply chain management.
Performance Metrics
Stock-outs
Stock-outs represent a critical performance metric in inventory management. When items are unavailable for sale, the impact on customer satisfaction can be significant. Chronic stock-outs can lead to lost sales opportunities, damaged customer relationships, and a decline in market share. Therefore, tracking this metric enables organizations to gauge potential weaknesses in supply chain execution.
A key characteristic of stock-outs is their direct correlation with demand forecasting. Organizations can use historical data and market analysis to anticipate demand, reducing the likelihood of running out of essential products. However, stock-outs also present a disadvantage: if not properly managed, they can lead to increased operational costs, such as expedited shipping or emergency order placements.
Carrying costs
Carrying costs denote the total cost of holding inventory over a specific time period. This includes storage fees, insurance, spoilage, and any financing costs related to unsold goods. For companies, it is essential to manage these costs effectively to maintain profitability. High carrying costs can erode profit margins, making this metric a priority in the inventory control plan.
The primary characteristic of carrying costs is their variability based on inventory levels and types. Conversely, a high level of inventory can lead to larger carrying costs, while low levels can risk stock-outs. Balancing this trade-off is essential for effective inventory management.
Order fulfillment rates
Order fulfillment rates measure how effectively an organization meets customer orders within the promised time frame. High fulfillment rates are indicative of a well-structured inventory process, leading to repeat customers and increased revenue. Poor fulfillment rates, however, can have the opposite effect, leading to customer dissatisfaction.
This metric's unique feature lies in its ability to influence other critical areas of the business, such as sales projections and customer service. While high fulfillment rates contribute positively to brand reputation, maintaining them can often require significant resource allocation. Balancing fulfillment efficiency with cost considerations is another challenge organizations face.
Continuous Improvement Strategies
Continuous improvement strategies refer to initiatives aimed at enhancing the efficiency and effectiveness of the inventory control plan. By adopting methodologies such as Six Sigma or Lean Manufacturing, businesses can identify inefficiencies and implement systematic changes.
Regular reviews of inventory processes should include employee feedback, data analytics, and performance outcomes. This iterative approach not only bolsters the inventory system but also fosters a culture of accountability and motivation among employees.
Challenges in Inventory Control
Inventory control is a critical aspect of supply chain management, but it is not without its challenges. Understanding these challenges is essential for businesses aiming to optimize their inventory management processes. Effective inventory control ensures that products are available when needed, minimizing excess stock and reducing costs. However, even with a well-designed plan, external and internal factors can disrupt this balance.
Supply Chain Disruptions
Supply chain disruptions can arise from various sources, making them a significant challenge in inventory control. Natural disasters, political instability, and pandemics can significantly impact the flow of goods. For instance, the COVID-19 pandemic introduced unexpected delays in shipping, manufacturing halts, and difficulties in sourcing raw materials.
When disruptions occur, businesses often face stock outs or excess inventory. Stock outs can lead to lost sales and customer dissatisfaction, while surplus inventory escalates carrying costs. To manage such disruptions effectively, companies must develop contingency plans that include multiple sourcing options and flexible logistics strategies. This proactive approach can minimize the fallout from unexpected events and maintain the continuity of operations.
Inventory Obsolescence
Another pressing issue in inventory control is inventory obsolescence. This occurs when products become outdated or unsellable due to changes in consumer preferences, advancements in technology, or new regulatory requirements. In industries like electronics or fashion, products may have a short lifespan and, if not managed properly, can result in significant financial losses.
To combat this, businesses should regularly assess their inventory and implement effective forecasting methods to anticipate market trends. Techniques such as Just-in-Time inventory can help minimize excess stock and reduce the risk of obsolescence. Additionally, maintaining strong communication channels with suppliers can ensure that businesses adapt quickly to market changes.
"An effective inventory control plan not only reduces costs but also aligns closely with business strategy, thereby adding significant value to the organization."
In summary, recognizing and addressing the challenges of supply chain disruptions and inventory obsolescence is crucial for maintaining an effective inventory control plan. This awareness allows businesses to create more resilient systems that can adapt to changing conditions, ultimately achieving long-term operational efficiency.
Future Trends in Inventory Management
The realm of inventory management is experiencing significant shifts due to evolving market dynamics and technological advancements. Understanding these future trends is crucial for businesses keen on optimizing their inventory control plans. Professionals in the field must stay informed, as adapting to these trends can yield enhanced operational efficiency and cost savings. Focused attention on sustainability and the integration of advanced technologies will distinguish successful organizations from their competitors.
Sustainability Initiatives
Sustainability has become a paramount narrative in business operations, significantly impacting inventory management. Companies are now recognizing that environmentally responsible practices are not merely beneficial for the planet, but are also advantageous for long-term profitability. Adopting sustainable inventory practices can reduce waste, lower energy consumption, and contribute to a positive corporate image.
Implementing sustainability initiatives involves:
- Reducing excess stock to minimize waste
- Opting for eco-friendly packaging material
- Partnering with suppliers who prioritize sustainable practices
- Implementing efficient logistics systems to lower carbon footprints
The benefits can be substantial.
- Improved brand loyalty among environmentally-conscious consumers
- Potential cost reductions through minimized waste
- Alignment with regulatory standards, thus avoiding penalties
"Incorporating sustainability into inventory management is not just a trend; it's a necessity for future survival in the marketplace."
A businesses that embraces these practices often finds innovative ways to streamline operations while catering to the growing demand for sustainability.
Integration of AI and Machine Learning
Artificial Intelligence and Machine Learning are set to revolutionize inventory management by providing data-driven insights that allow organizations to make informed decisions rapidly. These technologies analyze vast amounts of data to uncover patterns and trends, enabling predictive analytics that optimize inventory levels, reduce costs, and forecast demand more accurately.
Key advantages of integrating AI and Machine Learning into inventory control include:
- Enhanced demand forecasting, leading to reduced stockouts and overstock situations
- Automated reordering processes based on real-time sales data
- Improved inventory visibility through accurate tracking and monitoring
- Sophisticated analytics tools that provide actionable insights
While the implementation of such technologies may require substantial initial investment, the long-term benefits can surpass these costs. Companies can achieve more precise inventory control, aligning stock levels closely with consumer behavior and market trends. The outcome can lead to significant reductions in holding costs and increased overall efficiency.